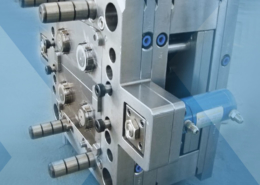
TMW: The go-to manufacturer of injection molds for automobile parts - automotive
Author:gly Date: 2024-09-30
In the FiberForm process, a fully consolidated fiber-reinforced thermoplastic sheet, called organosheet, is inserted into the forming tool and overmolded with a thermoplastic.
Monroe Capital LLC provided financing for the acquisition. Winston & Strawn LLP provided legal representation to Core and Fathom in the transaction.
Chicago-based private-equity firm Core Industrial Partners announced today the acquisition of Summit Tooling Inc. and Summit Plastics Inc. by its portfolio company Fathom. The precision tooling and injection molding supplier is the fourth add-on acquisition to the Fathom platform since Core made its initial investment in 2018.
KraussMaffei “has not only set up a machine with multiple capabilities, but has also been actively helping us on-site with process development,” said Dr. Waruna Seneviratne, director NIAR Atlas. “Our students also gain a tremendous amount of hands-on experience and get to interact with the supply chain for several new capabilities we introduced in recent years. Our goal is to transfer the efficient processes such as FiberForm from automotive production to aviation.”
Designed with the same oval geometry as the metal plugs, the thermoplastic replacements featured ribs added to increase stiffness that could withstand cabin pressure. In this case, the 16-ply organosheet was made of LM-PAEK reinforced with AS4 carbon fibers; the overmolded ribs were made of 30% chopped-fiber-filled PEEK. The final plugs were produced on a GXW 450-2000/1400 injection molding machine with a swivel platen.
Next, the NIAR team is working toward further weight reduction, making the thermoplastic plugs 40% lighter than the metal parts. And, NIAR is performing further tests to certify the plugs for series production — informed by KraussMaffei’s experience in high-production automotive applications.
The project is the subject of a technical paper, “Ultra-High-Rate Manufacturing of Thermoplastic Window Plug Using Hybrid Overmolding,” which won first place in the outstanding technical paper awards at the SAMPE 2024 advanced materials and process engineering conference and exhibition.
A project to convert passenger jets to cargo planes during the Covid pandemic, using thermoplastic window plugs instead of metal, will be on display at KraussMaffei’s booth at NPE2024 in Orlando, FL, from May 6 to 10.
The two-year partnership between KraussMaffei and the National Institute for Aviation Research (NIAR) at Wichita State University used KraussMaffei’s FiberForm technology to produce a 20% lighter alternative to the previous 590-gram metal plugs.
“Summit’s focus on customers during the design, prototyping, and low-volume production stages of a product’s life cycle perfectly aligns with Fathom’s unique customer-value proposition,” Fathom CEO Ryan Martin said in a prepared statement. “We’re excited to work with the Summit team to explore opportunities to even better serve its customers through Fathom’s comprehensive digital manufacturing platform while also providing Fathom’s existing customer base expanded domestic quick-turn precision tooling and molding capabilities,” added Martin.
At NPE, the injection molding machine maker will display thermoplastic window plugs for cargo planes developed in partnership with the National Institute for Aviation Research.
Using this process, 40 window plugs can be produced in an hour, thanks to the shorter cycle time of fast injection molding vs. metal machining. And, the thermoplastics used in the FiberForm process allow for the welding of components, in addition to demonstrating high impact strength, resistance to high temperatures and chemicals, and flame retardance.
Core Industrial Partners’ portfolio company Fathom acquired the precision tooling and injection molding supplier serving customers in the packaging and medical markets.
Dan Martin, President of Summit, commented: “Since my wife, Michelle, and I founded Summit 25 years ago, we’ve been committed to providing outstanding quality and customer service to build the business into a leader in the design, engineering, and construction of molds and molded components. We’ve now reached an inflection point in our growth trajectory, and we believe Fathom is the perfect fit in terms of both culture and customer-value proposition to help take Summit to the next level.”
Geoff Giordano is a tech journalist with more than 30 years’ experience in all facets of publishing. He has reported extensively on the gamut of plastics manufacturing technologies and issues, including 3D printing materials and methods; injection, blow, micro and rotomolding; additives, colorants and nanomodifiers; blown and cast films; packaging; thermoforming; tooling; ancillary equipment; and the circular economy. Contact him at [email protected].
“Summit’s leading customer base includes some of the largest and most recognizable players in the medical and packaging spaces,” said Matthew Puglisi, Partner of Core. “This acquisition significantly enhances Fathom’s domestic injection molding and tooling capabilities, and we’ll continue to actively pursue acquisitions, similar to Summit, that simultaneously broaden our customer base, enhance our service offering, and deepen our presence in attractive, recession-resistant end markets.”
Founded in 1996, Summit provides plastic injection mold design, precision mold making, and close-tolerance injection molding with a specialty in small to medium prototype injection molds. Summit primarily serves long-tenured customers in the medical and packaging end markets with its fleet of more than 30 machines, said Core's announcement.
In-house metalworking capabilities include engineering design, sheet metal shearing, punching and bending, roll forming, hardware integration, welding, grinding, polishing, painting, and assembly. Summit’s thermoplastics engineering expertise allows the company to process multi-shot and bi-injected tooling and perform insert overmolding. Pad printing, hot stamping, ultrasonic welding, and assembly are also offered by the company, which operates a 26,000-square-foot facility northwest of Chicago in McHenry, IL.
GETTING A QUOTE WITH LK-MOULD IS FREE AND SIMPLE.
FIND MORE OF OUR SERVICES:
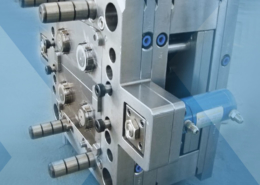
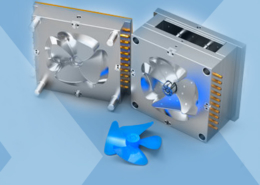
Plastic Molding

Rapid Prototyping
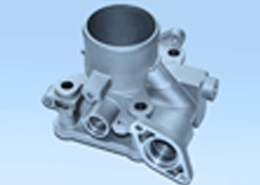
Pressure Die Casting
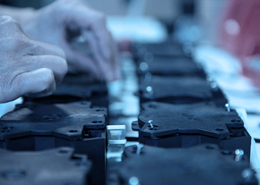
Parts Assembly
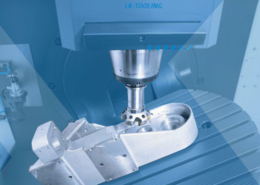