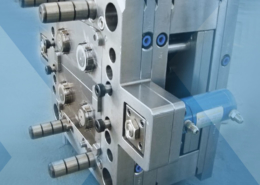
Thermoset Resins Set to Play Key Roles in Vehicle Lightweighting - nissei inject
Author:gly Date: 2024-09-30
Subscribe to the 3D Printing Industry newsletter for the latest news in additive manufacturing. You can also stay connected by following us on Twitter and liking us on Facebook.
Hot runner supplier Mastip used K 2022 to introduce the customized and valve-gated Aquilo liquid silicone rubber (LSR) cold deck.
Across all process types, sustainability was a big theme at NPE2024. But there was plenty to see in automation and artificial intelligence as well.
Additive technology creates air pockets in film during orientation, cutting down on the amount of resin needed while boosting opacity, mechanical properties and recyclability.
August 29-30 in Minneapolis all things injection molding and moldmaking will be happening at the Hyatt Regency — check out who’s speaking on what topics today.
In this three-part collection, veteran molder and moldmaker Jim Fattori brings to bear his 40+ years of on-the-job experience and provides molders his “from the trenches” perspective on on the why, where and how of venting injection molds. Take the trial-and-error out of the molding venting process.
Exhibitors and presenters at the plastics show emphasized 3D printing as a complement and aid to more traditional production processes.
In this collection of content, we provide expert advice on welding from some of the leading authorities in the field, with tips on such matters as controls, as well as insights on how to solve common problems in welding.
Discover how artifical intelligence is revolutionizing plastics processing. Hear from industry experts on the future impact of AI on your operations and envision a fully interconnected plant.
Processors with sustainability goals or mandates have a number of ways to reach their goals. Biopolymers are among them.
Micro-injection processes might have worked well under laboratory conditions, but during scale-up and high-volume production, the molders and equipment suppliers face completely new challenges. This applies above all to the dimensional accuracy of the parts. Factors that have virtually no effect on large parts are decisive for the reject rate in the case of delicate micro-parts. Deviations of a few thousandths of a millimeter or a few tenths of a milligram have a major impact on the quality of these tiny parts, and thus on their subsequent reliability in use.
“The combination of our P4K printer and Covestro e-PerFORM optimized for our printers enables fast, cost-effective production of injection molding tooling,” said Al Siblani, EnvisionTEC CEO. “Our collaboration has resulted in a new and much-needed solution.”
The companies showcased their combined DLP 3D printing offering at this week’s RAPID + TCT event in Chicago, and believe the development will accelerate the adoption of industrial 3D printing for producing molds in low volumes, and parts with detailed features, faster and more economically.
The Engel e-victory injection machine used here has an electric injection unit in combination with a servohydraulic, tiebarless clamp. Since the tiebarless clamp allows for full utilization of the mold platens right up to the edge, even large, bulky molds with a rotary table will fit on a comparatively small machine.
A new LSR micro-injection unit, developed jointly by Engel and ACH Solution (both in Austria), makes it possible to manufacture precision parts from LSR with shot weights significantly below 0.1 g. The unit consists of a plunger rather than a screw; but ACH incorporates a dynamic mixer (rather than a more typical static mixer) into the feed system to ensure a good mix of the silicone A and B components and pigment, if any. Technically, it may be considered a two-stage injection system, because there is a hold stage for the mixed liquid components, followed by an injection stage. Plunger diameter is 6 mm and maximum shot capacity is 2.26 cm3. For very tiny components, Engel recommends using this system together with its iQ weight control software.
FIG. 1 These LSR micro-parts—connecting elements in instruments for ophthalmic diagnostics—measure 1.7 mm long × 0.9 mm diam. and weigh just 0.0005 g each. They’re molded in 32 cavities.
Sei Woo Hi-Tech Polymer, Austria, a specialist in microtechnology, combines polyamide (nylon) and LSR on one injection molding machine to form a micro-part. The components are part of an air-inlet valve responsible for the massage function in vehicle seats (Fig. 3). For this purpose, the polyamide (PA) housing base bodies are first injection molded in a 16+16 cavity, rotary-plate mold on an Engel e-victory 140 combi injection molding machine. At the second indexing position, the LSR is injected, while 16 more housing base bodies are produced at the same time. Specially formulated PA and LSR form a chemical bond. However, as the contact area is very small, the finished parts are annealed at 200 C (392 F) after molding for safety reasons in order to permanently bond the thermoplastic and silicone. The parts then pass through camera-based 100% quality control.
Molding delicate LSR parts weighing 0.5 mg in 32 cavities requires high precision and repeatability in molding and careful post-mold handling. Here’s a look at the challenges of micro-molding with LSR and what makes it different from thermoplastic micro-molding.
FIG. 4 The “smart-shut” sliding-ring nonreturn valve by Engel for very low-viscosity melts or LSR and short cycle times is used to help achieve the greatest possible shot-weight consistency, which is essential in micro-parts.
Mike Sepe has authored more than 25 ANTEC papers and more than 250 articles illustrating the importance of this interdisciplanary approach. In this collection, we present some of his best work during the years he has been contributing for Plastics Technology Magazine.
Thermoplastics do not behave any differently than usual during micro-injection molding: The pellets are fed to a screw and heated barrel. The screw and temperature management ensure that the melt forms homogeneously and can be fed to the cavities shot by shot by means of a sub-runner and valve gate.
Core Technology Molding turned to Mold-Masters E-Multi auxiliary injection unit to help it win a job and dramatically change its process.
Hayley is a Technology Journalist for 3DPI and has a background in B2B publications spanning manufacturing, tools and cycling. Writing news and features, she holds a keen interest in emerging technologies which are impacting the world we live in.
Raw-material supply to the injection molding machine is another point where LSR and thermoplastic micro-injection molding differ. The two components of liquid silicone are stored in containers whose volume should not exceed 0.5 to 0.7 liters for microinjection molding. To additionally protect the material, the hose connections to the barrel also should be as short as possible and have only a narrow cross-section. When selecting the metering pumps for the molding system, Engel gives priority to working with partners whose units are OPC UA-capable in order to ensure integration into the machine control system.
This month’s resin pricing report includes PT’s quarterly check-in on select engineering resins, including nylon 6 and 66.
Given a component 1.7 mm long and 0.9 mm in diam., the part weight made of LSR is 0.0005 g (Fig. 1). If you have 32 cavities, the total shot weight (including sprue) is then 0.125 g. This is the equivalent of about 125 grains of sugar. For comparison's sake, a sugar cube contains about 20,000 to 30,000 grains.
The firm has also teased the potential of its upcoming DLP 8K Xtreme machine, which it claims is significantly faster than both Formlabs’ 3L and HP’s MJF 5200 systems. The printer is to be powered by EnvisionTEC’s Projection Array technology and will use a closed-loop printing process to fabricate parts with “desirable properties.”
Better control of LSR mixing/dosing and cold-runner valve-gate injection, as well as improved mold-design capabilities are highlighted at Molding 2019 Conference.
Sustainability continues to dominate new additives technology, but upping performance is also evident. Most of the new additives have been targeted to commodity resins and particularly polyolefins.
Micro-injection molding means working with part weights of significantly less than one gram. Right now, some manufacturers are already achieving part weights below one milligram—although it makes a big difference here whether the raw material is a thermoplastic with a low specific weight or a liquid silicone with higher density (typically 1.10 to 1.50 g/cm3). Micro-parts made of silicone are generally heavier than thermoplastic micro-parts, but they can be smaller—and more challenging—in terms of dimensions.
Introduced by Zeiger and Spark Industries at the PTXPO, the nozzle is designed for maximum heat transfer and uniformity with a continuous taper for self cleaning.
FIG. 2 The all-electric and tiebarless Engel e-motion TL injection molding machine is tailored for micro-injection molding. It is offered with a special LSR micro-injection unit jointly developed with ACH Solution and a metering pump system from the same partner.
Featured image shows a tool used for injection molding glass-filled nylon gears 3D printed on EnvisionTEC’s Perfactory P4K series printer using the e-PerFORM resin. Photo via EnvisionTEC.
As well as its 3D printing hardware and technology, EnvisionTEC also has an extensive 190-strong material portfolio. The firm has recently developed two new biocompatible resins, E-Dent 1000 and E-Denture Pro, which are currently undergoing 510k clearance.
Tests carried out by Polyvia, the French Federation of Plastics and Composites, confirmed the material-printer combination’s suitability for rapid tooling applications.
Micro-injection molding requires highest precision in all phases of the injection molding process, including consistency of shot weight. One ongoing commercial molding program involves connectors made of liquid crystalline polymer (LCP) with a shot weight of 0.484 g and an injection time of 0.018 sec. The Engel customer is achieving great results here thanks to the “smart-shut” sliding-ring nonreturn valve: The deviation per shot is a maximum of +/-0.0005 g, which is about 0.1%.
Another feature of this system is a barrel-coding option that permits replacing the ACH micro-injection unit with a standard screw plasticating unit for LSR or thermoplastic. For processing LSR on the conventional screw with an ACH metering pump, the barrel-coding software disables screw rotation so that it functions just as a plunger, and adjusts the injection pressures and volumes for the barrel diameter.
Engel offers the “smart-shut” sliding-ring nonreturn valve for very low-viscosity melts (or LSR) and short cycle times to provide support for achieving the greatest possible shot-weight consistency (Fig. 4). The non-return valve is particularly useful in applications with a very short injection stroke and very slow injection speeds. The underlying principle is that valve closing is actively initiated by the counter-rotation of the screw; this means that the nonreturn valve is already completely closed when the injection process begins.
This Knowledge Center provides an overview of the considerations needed to understand the purchase, operation, and maintenance of a process cooling system.
Some special features must also be taken into account in handling the tiny parts, the automation on the machine, and quality control. Takeoff by means of a gripper is just as unthinkable as allowing sensitive parts to simply drop off the mold.
For instance, at last year’s Formnext Connect, Covestro launched a new eco-friendly Addigy range of materials that were either partially made from recycled plastics or comprised of up to 20 percent CO2.
“The validation and proven solution with their P4K printers will help accelerate the adoption of additive manufacturing of injection mold tooling.”
For LSR components, the air flow also needs to be changed to reflect the temperatures. Due to the heat generated, the gases mainly escape upward during part removal, which is why the air must be extracted above the mold for LSR injection molding in a cleanroom. By contrast, for thermoplastics, the air extractors are usually located below the mold and the parts in the mold are additionally cooled with fresh air from above in a laminar flow.
SIGMA Engineering and Momentive Performance Materials announced a cooperation to optimize material data for silicone elastomers to make LSR molding simulation more reliable.
For the market launch of the micro-injection unit at the end of 2020, it was used to mold connecting elements for medical instruments in a valve-gated, cold-runner mold with 32 cavities. The delicate parts measure 1.7 mm long × 0.9 mm diam., with a combined part weight of just 16 mg. The unit runs on an all-electric and tiebarless Engel e-motion 50/30 TL injection molding machine and is supplied by an LSR metering pump from ACH Solution. An Engel viper 6 linear robot removes the parts and deposits them on a conveyor belt for camera-based quality control.
Having said this, silicone offers benefits in terms of takeoff and part design: The elastic components can be deformed during demolding without impacting quality. This increases design freedom for LSR micro-parts; even small undercuts are possible here. On the other hand, in the case of thermoplastic parts, a strategy for damage-free removal of the rigid, cooled parts must be carefully considered in advance.
But before we turn to the differences between LSR and thermoplastic in processing, it's worth taking a comprehensive look at the special challenges of micro-injection molding. These challenges exist independently of the raw material used, because some of the engineering challenges in micro-injection molding arise solely from the part—and part feature—dimensions and extremely low masses processed.
Plastics Technology covers technical and business Information for Plastics Processors in Injection Molding, Extrusion, Blow Molding, Plastic Additives, Compounding, Plastic Materials, and Resin Pricing. About Us
FIG. 3 The automotive industry is one of the main drivers of the micro trend. This air-intake valve for the massage function in vehicle seats measures 4 × 3 mm and combines LSR and nylon in an overmolding application. (Photo: Sei Woo)
Resin drying is a crucial, but often-misunderstood area. This collection includes details on why and what you need to dry, how to specify a dryer, and best practices.
Multiple speakers at Molding 2023 will address the ways simulation can impact material substitution decisions, process profitability and simplification of mold design.
When, how, what and why to automate — leading robotics suppliers and forward-thinking moldmakers will share their insights on automating manufacturing at collocated event.
Take a deep dive into all of the various aspects of part quoting to ensure you’ve got all the bases—as in costs—covered before preparing your customer’s quote for services.
“We tested the new e-PerFORM resin printed on the EnvisionTEC P4K printer and demonstrated that we could achieve very good results in part fidelity and in the number of shots molded in both polypropylene and glass-reinforced nylon,” explained Guy Chrétien, Process Project Manager at Polyvia. “With the cost-effectiveness and print speed of the P4K platform and with the properties of the e-PerFORM resin, this creates additional opportunities for rapid tooling.”
Through their partnership, Covestro and EnvisionTEC are seeking to provide a complete industrial manufacturing offering for 3D printing injection mold tooling, a feat that, according to them, has so far not been accomplished in terms of meeting stringent dimensional stability and minimal warpage industry requirements.
Even luxury goods such as watches increasingly contain tiny components made of thermoplastic—for example, cog wheels in watch movements or clips—and silicone for tiny seals. It is the latter material, in particular, that is gaining increasing market share because of its special properties. Due to trends toward electromobility and autonomous driving, the automotive industry will also require larger numbers of micro-parts made of liquid silicone rubber (LSR) in the future.
Successfully starting or restarting an injection molding machine is less about ticking boxes on a rote checklist and more about individually assessing each processing scenario and its unique variables.
The requirements placed on the production unit therefore initially appear to be fundamentally different, yet they can be met on a single injection molding machine. This offers the processor more flexibility and the opportunity to better utilize its machines. How does it work?
Maximum precision in the interaction of all units of the system is indispensable here. Engel recommends for this purpose all-electric and tiebarless injection molding machines from its e-motion TL series, not only for development, lab work and prototyping or for short runs, but also for high-volume production (Fig. 2). These precision machines are complemented by a new flexible micro-injection unit (see sidebar) that was developed as a dedicated solution for LSR micro-injection molding.
Static charge means that the parts stick to smooth surfaces like magnets and can then hardly be gripped even using your fingers. For this reason, micro-injection molded parts are often taken in by vacuum and blown into a small collection container. Once the parts are in the container, things that are otherwise self-evident, such as counting, measuring or weighing a single part, are no longer possible due to the minimal dimensions. Camera inspection for quality assurance therefore takes place on the way from the cavity to the collection container or even directly at the cavity before part removal. To accomplish this, the camera is located on the gripper, which docks onto a specific position on the mold, allowing the camera to assess the quality for multiple cavities. Engel partners with market leaders in automation and quality assurance and offers turnkey production units from a single source.
Through the partnership, Covestro’s DLP resin e-PerFORM has been optimized for EnvisionTEC’s Perfactory P4K series DLP 3D printer.
Mold maintenance is critical, and with this collection of content we’ve bundled some of the very best advice we’ve published on repairing, maintaining, evaluating and even hanging molds on injection molding machines.
Say “manufacturing automation” and thoughts immediately go to the shop floor and specialized production equipment, robotics and material handling systems. But there is another realm of possible automation — the front office.
Despite price increase nominations going into second quarter, it appeared there was potential for generally flat pricing with the exception of a major downward correction for PP.
Join Wittmann for an engaging webinar on the transformative impact of manufacturing execution systems (MES) in the plastic injection molding industry. Discover how MES enhances production efficiency, quality control and real-time monitoring while also reducing downtime. It will explore the integration of MES with existing systems, emphasizing compliance and traceability for automotive and medical sectors. Learn about the latest advancements in IoT and AI technologies and how they drive innovation and continuous improvement in MES. Agenda: Overview of MES benefits What is MES? Definition, role and brief history Historical perspective and evolution Longevity and analytics Connectivity: importance, standards and integration Advantages of MES: efficiency, real-time data, traceability and cost savings Emerging technologies: IoT and AI in MES
Learn about sustainable scrap reprocessing—this resource offers a deep dive into everything from granulator types and options, to service tips, videos and technical articles.
EnvisionTEC has invested heavily in biofabrication through its Bioplotter platform, which is capable of printing biocompatible parts for medical use within bone regeneration, soft tissue surgery, optimized drug release, and could potentially fabricate complete organs in the future.
The sprue channel alone illustrates how much technical know-how micro-injection molding requires. Its volume must be in a balanced ratio to the volume of the molded part(s). Several boundary conditions have to be weighed against each other and the overall process optimized. Key factors are process management, the waste and energy statistics, the material price and cycle time. All this poses the greatest challenges for the equipment manufacturer and for the manufacturer of the micro-parts.
Repeatability of the injection movement has an enormous influence on the precision and repeatability of the injection results. But high-quality micro-injection molding is not just a question of the injection unit. Clamp positioning and traverse accuracy also are essential for precise molding of a micro-part. For both LSR and thermoplastics, all-electric, servo-driven machines are therefore a sensible choice in micro-injection molding.
Over the years, the company has continued to develop new materials for the technology through various partnerships and acquisitions. In October last year, Covestro agreed to acquire nutritional science specialist Royal DSM’s Resins & Functional Materials unit for €1.6 billion, with the firm’s Somos resin range covering everything from tooling and automotive to aerospace and consumer goods. Covestro also benefitted from the unit’s FDM-suitable filaments and granules and its SLS powders.
The special features of a tiebarless machine have a positive effect in the injection molding of micro-parts. Due to their design, these machines inherently ensure great platen parallelism and uniform clamp-force distribution. In addition, the tiny parts often need to be produced in a cleanroom. A compact machine design with a large clamping surface reduces the space requirements here; and the clean machine concept without hydraulics, with encapsulated toggle levers and linear guidance, also supports the processor in complying with GMP (FDA’s Good Manufacturing Practice) specifications.
While the major correction in PP prices was finally underway, generally stable pricing was anticipated for the other four commodity resins.
In this collection of articles, two of the industry’s foremost authorities on screw design — Jim Frankand and Mark Spalding — offer their sage advice on screw design...what works, what doesn’t, and what to look for when things start going wrong.
Without us noticing, tiny plastic parts are increasingly making inroads into our lives: in cars, medical technology, mobile phones and wearables. Increasing numbers of these micro-parts are made of silicone. But what challenges does micro-injection molding pose for processors? Is liquid silicone, which is seeing increasingly widespread use, making processes more complex than they already are for thermoplastics? And where will the journey take us—how far can the limits of what is feasible be pushed?
Second quarter started with price hikes in PE and the four volume engineering resins, but relatively stable pricing was largely expected by the quarter’s end.
In this collection, which is part one of a series representing some of John’s finest work, we present you with five articles that we think you will refer to time and again as you look to solve problems, cut cycle times and improve the quality of the parts you mold.
Join KraussMaffei for an insightful webinar designed for industry professionals, engineers and anyone interested in the manufacturing processes of PVC pipes. This session will provide a comprehensive understanding of the technology behind the production of high-quality PVC pipes: from raw material preparation to final product testing. Agenda: Introduction to PVC extrusion: overview of the basic principles of PVC pipe extrusion — including the process of melting and shaping PVC resin into pipe forms Equipment and machinery: detailed explanation of the key equipment involved — such as extruders, dies and cooling systems — and their roles in the extrusion process Process parameters: insight into the critical process parameters like temperature, pressure and cooling rates that influence the quality and consistency of the final PVC pipes Energy efficiency: examination of ways to save material and energy use when extruding PVC pipe products
Since its establishment as a legally-independent company in 2015, Covestro has become a global polymer business boasting a broad portfolio of elastomers, foams, films, and composites. The firm’s Addigy, Somos, Arnite and Makrolon materials are specially engineered for 3D printing, and have been developed with sustainability in mind.
Gifted with extraordinary technical know how and an authoritative yet plain English writing style, in this collection of articles Fattori offers his insights on a variety of molding-related topics that are bound to make your days on the production floor go a little bit better.
While prices moved up for three of the five commodity resins, there was potential for a flat trajectory for the rest of the third quarter.
DLP system and materials producer EnvisionTEC has teamed up with polymer 3D printing specialist Covestro to provide new material and printer combinations for DLP tooling applications.
The LSR microparts are still very hot on demolding, which must be taken into account when designing the automation system for parts handling. Particular attention must be paid to using heat-resistant materials and measuring technology here.
The two companies are seeking to accelerate the adoption of industrial 3D printing by lowering the entry barriers for companies looking to produce molds for low volumes or parts with detailed features more quickly and economically. To do this, they have combined Covestro’s material expertise with EnvisionTEC’s 3D printer technology to create what they claim is a complete industrial manufacturing offering for 3D printing injection mold tooling.
Plastics Technology’s Tech Days is back! Every Tuesday in October, a series of five online presentations will be given by industry supplier around the following topics: Injection Molding — New Technologies, Efficiencies Film Extrusion — New Technologies, Efficiencies Upstream/Downstream Operations Injection Molding — Sustainability Extrusion — Compounding Coming out of NPE2024, PT identified a variety of topics, technologies and trends that are driving and shaping the evolution of plastic products manufacturing — from recycling/recyclability and energy optimization to AI-based process control and automation implementation. PT Tech Days is designed to provide a robust, curated, accessible platform through which plastics professionals can explore these trends, have direct access to subject-matter experts and develop strategies for applying solutions in their operations.
The trend towards miniaturization has gained considerable momentum in recent years. Many products—and with them the parts they are made of—are becoming smaller, more delicately complex and more compact. Micro-injection molding is used to produce many of these complex, delicate parts. In medical technology, examples include the increasing numbers of minimally invasive operations or new methods of analysis. Another target group for micro-molding is consumer electronics with very small electronic and optical precision components for smartphones, among other things.
After successfully introducing a combined conference for moldmakers and injection molders in 2022, Plastics Technology and MoldMaking Technology are once again joining forces for a tooling/molding two-for-one.
The Plastics Industry Association (PLASTICS) has released final figures for NPE2024: The Plastics Show (May 6-10; Orlando) that officially make it the largest ever NPE in several key metrics.
Join Engel in exploring the future of battery molding technology. Discover advancements in thermoplastic composites for battery housings, innovative automation solutions and the latest in large-tonnage equipment designed for e-mobility — all with a focus on cost-efficient solutions. Agenda: Learn about cutting-edge thermoplastic composites for durable, sustainable and cost-efficient battery housings Explore advanced automation concepts for efficient and scalable production See the latest large-tonnage equipment and technology innovations for e-mobility solutions
Elsewhere, Covestro has worked with fellow polymer 3D printing specialist Polymaker to develop waste-free 3D printable fabrics, and most recently to develop a new material partially made from recycled plastic bottles, called PC-r.
Ultradent's entry of its Umbrella cheek retractor took home the awards for Technical Sophistication and Achievement in Economics and Efficiency at PTXPO.
Formnext Chicago is an industrial additive manufacturing expo taking place April 8-10, 2025 at McCormick Place in Chicago, Illinois. Formnext Chicago is the second in a series of Formnext events in the U.S. being produced by Mesago Messe Frankfurt, AMT – The Association For Manufacturing Technology, and Gardner Business Media (our publisher).
For example, Engel uses the tiebarless version of the all-electric e-motion TL as the basis for LSR micro-molding. The machine produces tiny silicone components with a new LSR micro-injection unit. However, thanks to a quick coupling system, it can be converted into a thermoplastic injection machine in less than 30 min. And even switching over from micro-injection molding to the production of small components with a size 15 or 18 barrel in the injection unit is possible on the same machine. The material feed required in each case can be smoothly integrated into the machine control system via standardized interfaces (OPC-UA). This turns a standard machine into a highly flexible production unit for small and micro-components made of either LSR or thermoplastic.
“By working closely with our partner EnvisionTEC, we developed a material that meets critical needs voiced in the market: improved dimensional stability and minimal warpage for optimal functionality,” said Hugo da Silva, Head of Additive Manufacturing at Covestro.
Thousands of people visit our Supplier Guide every day to source equipment and materials. Get in front of them with a free company profile.
As of February this year, EnvisionTEC became a wholly-owned subsidiary of metal 3D printer manufacturer Desktop Metal in a $300 million acquisition. The company is known for its proprietary Continuous Digital Light Manufacturing (cDLM) 3D printing platform, with its Envision One cDLM printer delivering widespread applications to the dental sector, among other industries.
Mixed in among thought leaders from leading suppliers to injection molders and mold makers at the 2023 Molding and MoldMaking conferences will be molders and toolmakers themselves.
The aim of this presentation is to guide you through the factors and the numbers that will help you determine if a robot is a smart investment for your application. Agenda: Why are you considering automation? What problems are you trying to solve? How and why automation can help Crunch the numbers and determine the ROI
While the melting process does not provide perfect mixing, this study shows that mixing is indeed initiated during melting.
Join this webinar to explore the transformative benefits of retrofitting your existing injection molding machines (IMMs). Engel will guide you through upgrading your equipment to enhance monitoring, control and adaptability — all while integrating digital technologies. You'll learn about the latest trends in IMM retrofitting (including Euromap interfaces and plasticizing retrofits) and discover how to future-proof your machines for a competitive edge. With insights from industry experts, it'll walk you through the decision-making process, ensuring you make informed choices that drive your business forward. Agenda: Maximize the value of your current IMMs through strategic retrofitting Learn how to integrate digital technologies to enhance monitoring and control Explore the benefits of Euromap interfaces and plasticizing retrofits Understand how retrofitting can help meet new product demands and improve adaptability Discover how Engel can support your retrofitting needs, from free consultations to execution
technotrans says climate protection, energy efficiency and customization will be key discussion topics at PTXPO as it displays its protemp flow 6 ultrasonic eco and the teco cs 90t 9.1 TCUs.
Such small quantities as in this example—connecting elements used in instruments for ophthalmic diagnostics—now must be uniformly and repeatably distributed over all the cavities. The micro-injection unit, the sprue channel and thermal management are enormously important here in terms of quality, precision and repeatability.
Ing. Leopold Praher, Sales Manager elast/LIM/thermoset for Engel Austria in Schwertberg, has 35 years’ experience in sales and marketing worldwide in the elastomer industry. He has been with Engel since 1988, starting in spare parts and moving to area sales manager for rubber and silicone machines in 1994. He became worldwide sales director for the Elast Dept. in 2000. Contact: leopold.praher@engel.at; engelglobal.com.
To achieve this, Covestro’s patented DLP e-PerFORM material has been optimized for EnvisionTEC’s P4K series 3D printer. The e-PerFORM resin has been tested with key molding institutes to validate its performance, with results showing the material delivered high stiffness and temperature performance.
In a time where sustainability is no longer just a buzzword, the food and beverage packaging industry is required to be at the forefront of this innovation. By adopting circular packaging processes and solutions, producers can meet regulatory requirements while also satisfying consumer demand and enhancing brand reputation. Join Husky to learn more about the broader implications of the circular economy — as well as how leading brands are leveraging this opportunity to reduce costs, increase design flexibility and boost product differentiation. Agenda: The cost and operational benefits of embracing circularity Key materials in circular packaging — including rPET and emerging bioplastics How to design a circular food and beverage package Strategies for selecting sustainable closures to future-proof packaging solutions Optimization and streamlining of production processes for enhanced efficiency How Husky Technologies can enable your sustainable success
While prices moved up for three of the five commodity resins, there was potential for a flat trajectory for the rest of the third quarter.
Across the show, sustainability ruled in new materials technology, from polyolefins and engineering resins to biobased materials.
The most important differences in processing result from differences in temperature control for the two kinds of materials up to curing or vulcanization. When injection molding LSR, a two-component composite is mixed at room temperature in the barrel module. Feeding to the barrel takes place along the shortest possible paths with a small cross-section; distribution is then handled by a valve gate and sub-runner. The LSR vulcanizes in the mold at temperatures of 170 to 190 C (338 to 374 F) to form the elastic part. The mold and its temperature control must therefore be designed for high temperatures. Strict thermal separation between the barrel and mold must also be ensured to prevent the premixed liquid-phase LSR from unintentionally vulcanizing in the barrel.
GETTING A QUOTE WITH LK-MOULD IS FREE AND SIMPLE.
FIND MORE OF OUR SERVICES:
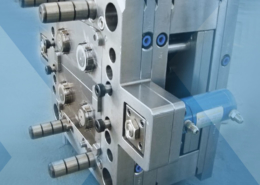
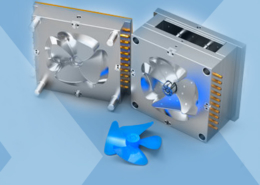
Plastic Molding

Rapid Prototyping
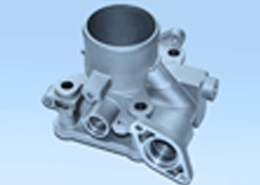
Pressure Die Casting
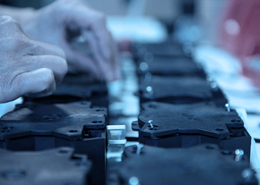
Parts Assembly
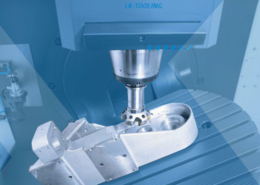