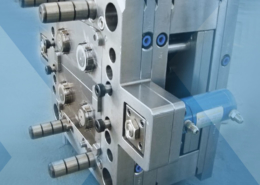
Thermoforming — The Surprising Vitality of a Mature Plastics Processing
Author:gly Date: 2024-09-30
Stephen has been with PlasticsToday and its preceding publications Modern Plastics and Injection Molding since 1992, throughout this time based in the Asia Pacific region, including stints in Japan, Australia, and his current location Singapore. His current beat focuses on automotive. Stephen is an avid folding bicycle rider, often taking his bike on overseas business trips, and is a proud dachshund owner.
Sabic said that the medical-grade PBT resin has passed stringent injection molding trials, where it demonstrated high flow even in complex designs, as well as mold release properties with lower shrinkage variation compared with competitive engineering plastics.
A new high-performance, medical-grade polybutylene terephthalate (PBT) resin from Sabic is suitable for molding precision components for insulin delivery pens, insulin pumps, auto-injectors, and continuous glucose monitors. The Valox HX325HP resin combines processability with chemical resistance and validated biocompatibility, said Sabic in the announcement.
Global diabetes cases are expected to soar from 529 million to 1.3 billion by 2050, according to Sabic. This will result in manufacturers that supply the medical and pharmaceutical markets to invest in easy-to-use, consistent, and accurate devices that put diabetes treatment in patients’ hands, said Roble Amanda, director of Advanced Consumer Solutions at Sabic. “This trend requires materials capable of providing high levels of safety, reliability, and durability without compromising productivity or precision in high-volume applications. We are pleased to introduce our new Valox HX325HP grade as a thermoplastic polyester solution that is engineered to exceed the high expectations and strict specifications of manufacturers in these demanding industry segments,” said Amanda.
The Informa Markets Engineering network of B2B media sites includes Design News, Battery Technology, Medical Device & Diagnostic Industry (MD+DI), Packaging Digest, PlasticsToday, and Powder & Bulk Solids.
Valox HX325HP has been successfully tested to international biocompatibility standards. Preliminary assessments according to ISO 10993 or USP Class VI are available upon request. In addition, the grade is subject to Sabic’s Healthcare Policy, providing reliable formulation lock and change control management in line with FDA and EU guidelines for medical-grade plastics. The resin also serves as a formaldehyde-free alternative to polyoxymethylene (POM) materials.
Mr. Herter added: “This new development is the result of our close partnership with leading OEMs. Together, we identified the need to address this issue and we were able to develop tailor-made solutions. This approach is fully in line with our strategy to focus on specialty added-value materials.”
Typical critical automotive interior parts affected include door handles, seating parts, cup holders, and air vents. The newly developed grades may also be suited for other segments such as E&E, white goods, or consumer goods.
According to Fabian Herter, Industry Manager Automotive at Elix Polymers, with these new grades, significant cost savings are possible: “Until now, in many instances, fabrics or grease had to be added afterwards to reduce squeak and rattle. However, this involves additional costs and manual labor – and therefore is not ideal. Now, thanks to these new Elix grades, we are able to offer a more competitive solution when compared to other resins that are currently available.”
The resin features chemical resistance, mitigating environmental stress cracking, and is compatible with ethylene oxide (EtO), gamma, and steam sterilization.
Elix Polymers (Tarragona, Spain) has developed a range of specialty grades of acrylonitrile-styrene-butadiene (ABS) and polycarbonate (PC)/ABS to reduce the squeak that is generated when plastic parts come into contact with other plastic parts, leather, PVC foil, or other products. These undesirable noises can negatively affect the driver’s comfort and the car’s quality impression.
The new grades use Elix Polymers base polymers: standard ABS, high-heat ABS, ABS/PC or PC/ABS – and because their key properties remain the same, this does not affect existing OEM approvals of Elix grades. Furthermore, as the shrinkage of the materials stays the same, current molds can be used without further need for modifications.
The new grades underwent stick-slip tests at several premium automotive OEMs according to the VDA230-206 standard using testing machines from Ziegler Instruments, with very positive test results: a 10-point scale is used where 10 is the highest risk level. The new Elix grades managed toscore 1 – the lowest risk level. Tests were conducted with different forces (10 N, 40 N) and speeds (1 mm/s and 4 mm/s) at several temperatures.
GETTING A QUOTE WITH LK-MOULD IS FREE AND SIMPLE.
FIND MORE OF OUR SERVICES:
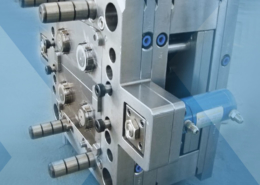
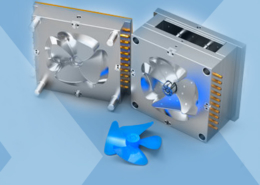
Plastic Molding

Rapid Prototyping
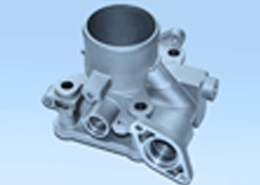
Pressure Die Casting
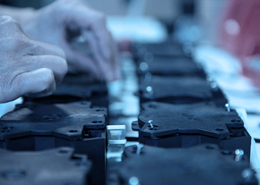
Parts Assembly
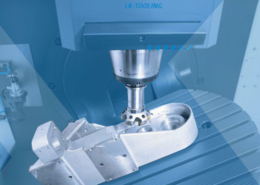