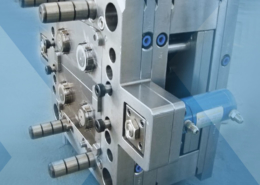
Thermal properties and mechanical behavior of hot pressed PEEK/graphite
Author:gly Date: 2024-09-30
Joh. Fuchs & Sohn – FUSO – was established in 1947 in Waidhofen on the river Ybbs in Lower Austria. In 1964, it started off into plastic injection moulding by producing the orange-coloured lids for Ovomaltine cans.
From the left: Martin Stammhammer, Int. sales manager Robots, WITTMANN Technology, Maximilian Högn, CEO of FUSO, Klaus Großtesner, CSO of FUSO, Andreas Högn, majority shareholder and advisor, FUSO, Roland Pechtl, area sales manager WITTMANN BATTENFELD
The company makes a point of supplying technical plastic parts and assemblies to a solid, mixed industrial customer base. The various sectors served by FUSO include the automotive and railway industries, as well as consumer goods, electronics, medical technology, building construction, telecommunication, mechanical engineering and renewable energy generation.
Requirements from the customer base concerning quality standards and attributes of the parts in terms of tolerances, outward appearance and materials used are constantly becoming more and more stringent. FUSO scores with purchasers by its extensive technical know-how and many years of experience in making high-quality parts and assemblies. This wealth of expertise enables the company to offer top-quality solutions which are both sustainable and cost-efficient. FUSO also stands out on the market by its high supply availability and reliability towards its customers.
The cooperation between FUSO and WITTMANN BATTENFELD has already been in existence for four decades. The machines most recently supplied by WITTMANN BATTENFELD are exclusively models from the SmartPower series. The machines from the SmartPower series are hydraulic machines equipped with fast-responding servo motors and powerful constant displacement pumps. This technology, combined with the KERS (Kinetic Energy Recovery System) to recover the deceleration energy within the machine, which is included as standard, provides the SmartPower’s high level of energy efficiency. Further characteristics of the SmartPower are its small footprint and its pivotable injection unit, which ensures easy access to the barrel for quick and comfortable barrel change.
To make all these parts, a number of injection moulding machines ranging from 450 to 5,200 kN in clamping force are in operation, 17 of which have come from WITTMANN BATTENFELD. Moreover, FUSO is also a long-standing customer of the WITTMANN Group for automation equipment, using more than 40 handling devices with load capacities from 5 to 30 kg, including No. 7 robots as well as latest No. 9 series models with R9 control systems.
All SmartPower machines except one are designed as Insider cells, which means that they come with a WITTMANN robot and a conveyor belt integrated in the production cell. This variant offers a number of advantages, ranging from an enormous amount of space saved compared to systems with conventional automation solutions, all the way to cost advantages from the fact that all hazardous areas are already secured and certified ex works. Moreover, the robot cycle time can be minimised due to shorter travel distances and direct parts depositing on the conveyor belt.
In addition to a good price-performance ratio, FUSO requires from injection moulding machines above all stability, as well as easy access for servicing and cleaning, a smooth, easy-to-clean surface, user-friendliness in operation and a high standard of repeatability. Other factors gaining increasingly in significance are the machines’ energy efficiency, their networkability with robots and auxiliaries and availability of assistance systems.
The family-owned company managed by its CEO Maximilian Högn and its CSO Klaus Großtesner makes highly sophisticated plastic parts from a great variety of materials, including high-temperature plastics, for many different sectors of industry, with about 80 workers on a production floor of just under 3,000 m².
Korea’s LG Chem has started supplying carbon nanotube (CNT)–filled engineering plastic compounds to Japan’s Mitsubishi Motors for the front fenders of its RVR, Delica D:5, and Outlander models. The injection-molded fenders can be powder-coated thanks to the electrical conductivity of the CNT-filled polyphenylene ether (mPPE) and polyamide (PA66) alloy, dubbed Lucon TX5007.
Last, but not least, the quality of the after-sales service including the possibility of using an online service also play an important part in the purchasing decision according to Klaus Großtesner. In the acquisition of robots, easy programmability is a top priority in addition to all other criteria which are also applicable to the machines.
In general, using plastics in place of steel/aluminum contributes to automotive lightweighting. When a plastic fender is used, the weight of the vehicle is reduced by about 4 kg, which also improves fuel efficiency.
With the rising demands from customers on the parts and assemblies produced, FUSO’s own demands on the injection moulding equipment used are also increasing. The company’s machinery is state-of-the-art, with a high level of automation on its production floor. All systems are fitted with matching robots to ensure careful parts handling.
3D prints for rapid prototyping are also possible. Injection moulding tools and automation systems are planned, designed and manufactured in-house at the company’s own mould-making shop. For ecological purposes, the company has made a special point of installing tool-friendly cooling water systems. Further evidence of FUSO’s commitment to protecting the environment are waste heat utilisation and a photovoltaic system.
The front fender is located on the side of the vehicle and not only acts as a key factor in the exterior design but also protects wheels from road debris. Consequently, it must be mechanically robust while having an exterior quality that maintains design integrity with the rest of the car body.
Stephen has been with PlasticsToday and its preceding publications Modern Plastics and Injection Molding since 1992, throughout this time based in the Asia Pacific region, including stints in Japan, Australia, and his current location Singapore. His current beat focuses on automotive. Stephen is an avid folding bicycle rider, often taking his bike on overseas business trips, and is a proud dachshund owner.
The machines delivered in 2023 also come already equipped with the new B8X control system and the HiQ Flow assistance system. The B8X control system includes several control components developed in-house. These allow a higher internal clock frequency with shorter response times to sensor signals and consequently a higher standard of parts reproducibility, with user-friendliness and familiar visualisation remaining unchanged.
Lucon TX5007 reportedly has excellent electrical conductivity and mechanical properties. In addition, its outstanding heat resistance makes it suitable for the electrostatic in-line painting process used by automakers that operates at temperatures of 200°C and higher. At the same time, the alloy delivers dimensional stability thanks to its low coefficient of linear thermal expansion (CLTE).
The items produced range from micro parts weighing just 0.03 g right up to large parts weighing 2 kg. In addition to manufacturing complex plastic parts by 1- or 2-component injection moulding, the company offers insert moulding for functional parts, mounting of complete assemblies, as well as gluing and welding, plus decoration by 4-colour pad printing and laser printing, and 3D scanning for reverse engineering.
In addition to Lucon TX5007, LG Chem offers a broad portfolio of compounds that can be used for large automotive exterior parts that undergo the powder coating process. These grades can be customized to meet automotive suppliers’ diverse parts requirements for fenders, bumper panels, hoods, tailgates, fuel doors, and side mirrors.
LG Chem is using CNT, a filler that delivers excellent conductivity even at low loadings, in its engineering plastics to support the diverse requirements of customers. Since this material can cover a wider range of electrical conductivity compared with other carbon fillers such as carbon black and carbon fiber, it is considered an optimal solution for powder coating. LG Chem is currently expanding its capacity for CNT, with a fourth plant expected to come on stream in 2024, which will ensure reliable supply of high-quality products for powder coating, according to the company.
“The Insider cells based on the servo-hydraulic SmartPower and WITTMANN linear robots meet our requirements in every respect”, Maximilian Högn confirms. “The equipment is space-saving, highly energy-efficient, easily accessible and easy to operate.”
The HiQ Flow assistance system is an injection regulation function by which viscosity fluctuations in the material used can be compensated. This function enables automatic process automation and compensates even minimal fluctuations in the material quality. FUSO is so completely satisfied with this system that all of the company’s other machines have been retrofitted with it, too, wherever technically feasible and economically advisable.
GETTING A QUOTE WITH LK-MOULD IS FREE AND SIMPLE.
FIND MORE OF OUR SERVICES:
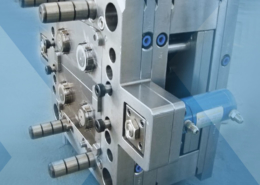
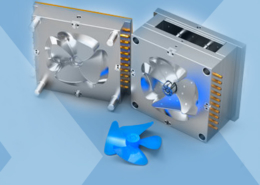
Plastic Molding

Rapid Prototyping
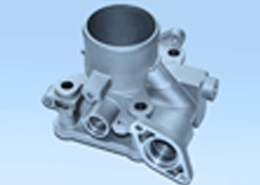
Pressure Die Casting
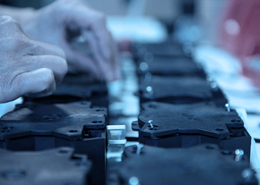
Parts Assembly
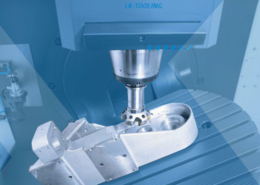