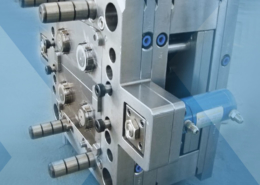
The New Lightweights: Injection Molded 'Hybrid' Composites Spur Auto
Author:gly Date: 2024-09-30
Additionally, the inclusion of Digital Direct Screw Transfer (DST) Control enhanced production flexibility by enabling precise calibration of clamping force, optimising processes, and ensuring consistent product quality.
Founded in 1959, SPAL Automotive has grown from being a manufacturer of plastic components to a pivotal player in the automotive sector, producing axial and centrifugal electric fans for various vehicles. However, the company realised that it needed to adapt its production processes to evolving market demands.
Transitioning to fully electric presses presents significant challenges for automotive manufacturers. Firstly, the initial investment costs can be substantial, encompassing the purchase and installation of more expensive electric presses along with necessary upgrades to the facility's electrical infrastructure. Moreover, specialised training and expertise are essential for operating and maintaining these presses, requiring investment in staff development or recruitment.
TM Robotics, in partnership with Shibaura Machine, formerly known as Toshiba Machine until 1st April 2020, offers a comprehensive range of industrial robots ideally suited for high-precision assembly, machine loading/unloading and material-handling applications that can be dust proof, clean room, or IP65/67. The company's extensive product line starts with a Cartesian solution available in thousands of combinations from single actuators to four-axis solutions; six-axis solutions that can include precise vision-control; and a complete range of SCARAs from low cost to the industry-leading SCARA with 1200-mm reach that can carry up to 20 kgs. TM Robotics sells and services robots throughout Europe, the Middle East, India, Russia, and Africa, as well as North, Central, and South America, from headquarters in Hertfordshire, England and Elk Grove Village, IL, USA. For more information, visit www.tmrobotics.com or follow us on Twitter, LinkedIn and YouTube.
To overcome these hurdles, SPAL turned to its strategic partnership with EPF, exclusive distributor and service partner of Shibaura Machine. The collaboration began when SPAL decided to focus on full-electric injection moulding machines. Shibaura Machine, already had the capabilities to supply injection moulding machines of a high tonnage range.
“EPF was able to supply Shibaura Machine — formerly Toshiba Machine — injection moulding machines with a tonnage range of 50 to 1,800 tones, which refers to the range of force or pressure these presses can exert during the moulding process,” added Carvani. With this range, SPAL can perform a variety of moulding tasks, from smaller components requiring less force to larger parts needing higher tonnage.”
These performance tests reaffirmed the value proposition of Shibaura Machine's injection moulding machines, providing SPAL with confidence in their ability to deliver both operational excellence and energy efficiency.
Furthermore, the integration with the Internet of Things (IoT) allowed for remote monitoring and diagnostics, empowering SPAL to proactively identify and address potential issues, thereby reducing the risk of unplanned downtime and ensuring continuous production.
With Shibaura Machine's injection moulding machines at the core of its production processes, SPAL achieved significant gains in productivity, efficiency and energy savings. By addressing challenges such as technology adaptation, production capacity enhancement, efficiency improvement and quality assurance, the collaboration enabled SPAL to position itself as a leader in the industry.
The shift from hydraulic to all-electric presses would mean not only updating production processes, but also revamping infrastructure to seamlessly accommodate the new technology. To support with these challenges, SPAL turned to its longstanding partner EPF, a partner for Shibaura Machine injection moulding equipment.
SPAL’s collaboration with EPF facilitated an expansion of its production department, equipped with 21 fully electric injection moulding machines ranging from 50 to 1800 tons, with a capability to reach 2500 tons. This expansion enabled SPAL to meet market demands effectively and cater to a broader range of products.
However, despite these challenges, transitioning to electric presses offers long-term benefits, such as reduced operating costs and improved sustainability. Overcoming these obstacles demands strategic planning, collaboration with suppliers, and diligent implementation to realise the advantages of electric press technology in automotive manufacturing.
Most mold manufacturers do not use material flow analysis software as a part of the mold design process as a general rule. Yet, because the mold is such a critical part of the success or failure of the entire molding process, all available tools should be used. That’s the opinion of Rick Carobus, president of EPS Flotek, a mold and material flow simulation service company and reseller of MoldEx 3D analysis software.
To learn more about how Shibaura Machine's all-electric injection moulding machines support sustainable manufacturing, visit TM Robotics’ website.
Most mold manufacturers do not use material flow analysis software as a part of the mold design process as a general rule. Yet, because the mold is such a critical part of the success or failure of the entire molding process, all available tools should be used. That’s the opinion of Rick Carobus, president of EPS Flotek, a mold and material flow simulation service company and reseller of MoldEx 3D analysis software.“This has always been seen as a luxury item by many moldmakers,” Carobus told PlasticsToday at NPE2012. “While they understand that it will save money in the long run, they know it’s not necessary to build or run a mold. Some OEMs will spend money to do an engineering change on the back end, however they won’t spend money to make it right on the front end.”
Manufacturers must also ensure that the performance and efficiency of electric presses meet production requirements, which may involve testing and optimisation. Integrating electric presses into existing manufacturing systems poses complexities, including compatibility issues and software adjustments. Additionally, sourcing components and adhering to regulatory standards present further hurdles, while the transition period itself can disrupt operations.
Moreover, the machines boasted faster injection speeds, resulting in reduced cycle times, thereby increasing overall productivity and throughput for SPAL's manufacturing operations. The user-friendly interface simplified operation, enhancing ease of use for SPAL's production personnel and facilitating seamless integration into existing workflows to minimise downtime and maximise efficiency.
The adoption of electric presses not only enhanced production capacity but also streamlined logistics within SPAL's production department. Efficient material handling, improved workflow management, and reduced downtime contributed to overall productivity gains.
Automotive manufacturer SPAL needed to upgrade its production line to meet changing market demands — including faster cycle times and reduced energy consumption. This meant upgrading from hydraulic to electric injection moulding machines, which presented several challenges. SPAL turned to EPF, the distributor of Shibaura Machine injection moulding equipment in Italy, for a solution. The results? Significant gains in productivity, efficiency and energy savings with the new, all-electric machines.
Performance tests conducted by Shibaura Machine ensure the energy efficiency of all-electric injection moulding machines. For example, the Shibaura Machine EC650SX-61B IMM, boasting a clamping force of 650 tons, showcased a notable 51 percent reduction in energy consumption compared to hydraulic servo alternatives. Similarly, the EC1800SX-155B model demonstrated superior cycle time and an impressive 30 percent overall energy efficiency gain compared to rival machines.
Until she retired in September 2021, Clare Goldsberry reported on the plastics industry for more than 30 years. In addition to the 10,000+ articles she has written, by her own estimation, she is the author of several books, including The Business of Injection Molding: How to succeed as a custom molder and Purchasing Injection Molds: A buyers guide. Goldsberry is a member of the Plastics Pioneers Association. She reflected on her long career in "Time to Say Good-Bye."
“SPAL decided to focus firmly on electric presses, which was an ideal solution,” explains Moreno Carvani, managing director, EPF plastic. “The benefits include very low energy consumption, high yields in the moulding process, and high reliability.”
"Embracing all-electric injection moulding machines brings more than just efficiency gains, it opens the door to more diverse manufacturing,” said Nigel Smith, CEO at TM Robotics, distribution partner of Shibaura Machine. “By providing flexible production capabilities, reduced energy consumption and enhanced performance, Shibaura Machine's machines empower manufacturers to explore new markets, and cater to varied product demands.”
Automotive manufacturer SPAL needed to upgrade its production line to meet changing market demands — including faster cycle times and reduced energy consumption.
In particular, SPAL sought to evolve — and also expand — its production line in Correggio, Italy, to achieve faster cycle times, reduce energy consumption and streamline logistics. A crucial step towards this would be upgrading its hydraulic injection moulding systems to all-electric. This would invite several challenges, including the potential of significant capital investment retrofitting complexities and retraining of personnel.
The machines offer faster injection speeds and improved cycle times, contributing to enhanced productivity and cost-effectiveness. Furthermore, their user-friendly interface and integration with the Internet of Things (IoT) simplify operations and support preventive maintenance strategies, ensuring optimal performance and longevity.
Generally the process starts with the part designer and from there, in succession, goes to the tool designer, the tool builder, the molder, and finally the parts get to the OEM, Carobus explained. “When the part is delivered and is failing in the field someone wants a simulation analysis. We don’t want to get involved at that point. We want to work with the part designer or the tool designer at the front end of the project because as you move up the ladder, the mold gets more expensive to fix. But, we seem to get involved at the back end about equally with the front end involvement.” OEMs requiring process flow in initial bidThat said, Carobus acknowledges that business has picked up considerably as some markets, such as the automotive industry, require process flow analysis and design validation prior to the mold build. “More advanced industries like the automotive will automatically include mold and material flow analysis in their design,” he noted. “Big companies tend to have this capability in-house, but some will depend on the mold maker to perform an analysis on the part design prior to cutting steel.”Often material suppliers will run a quick analysis to support the use of their material. “Does it really help the OEM or solve any problems?,” asked Carobus. “They might miss things. It’s not just running an analysis but knowing what you’re looking for—looking for real molding conditions and doing it right is what counts. Many companies own the software but don’t optimize the part design or tool design. They spend money then complain they didn’t get the information they needed. But are they using the tool correctly? Even with the stuff that’s easy to use can give you bad results.” Some OEMs depend upon the tool builder to run the analysis. Industrial Molds Group purchased the MoldEx 3D software from ESP Flotek several years ago, however due to a change in personnel, they lost some of the talent that knew how to use it. A few months ago, they re-evaluated the software and decided that it was a good tool, and that they weren’t using it the way it was meant to be used to provide benefits to both their customers and the company. They called in EPS Flotek and had the latest versions of MoldEx 3D installed and provided training to the engineering department. “Now we use MoldEx 3D to check the mold fill on every job before we cut steel,” said Kerry Smith, Industrial Molds’ Engineering Manager. “Filling the mold properly is the first consideration in the mold design and causes the most angst for our customers or their molders. The simulation allows us to look at the gate, the hot runner system and the venting. We look at hot spots and determine how to implement better cooling. It also has the ability to do warp analysis.”“The analysis tool should be used interactively – not behind the scenes in the closet,” commented Carobus. “The part designer, the tool designer, the moldbuilder, the molder and the customer should all work collaboratively. We want to build a tool as efficiently as possible, so we can tell you what happens if you reduce your cycle time by 2 seconds. The customer wants a tool that produces the best quality part, and it helps the moldmaker get them just that.” Old habits die hardOften it’s the life-long moldmaker who resists this type of software because they’ve been building molds for 40 years and think the software doesn’t know more than they do. “It’s not about the software knowing more but that the plastic process has so many variables that one little change in a rib, a gate location, a material can make a huge difference in the part quality, the cycle time savings and in profitability for their customer,” Carobus commented.Smith pointed out that some of the reluctance of smaller shops is the cost involved in purchasing a seat of mold-filling simulation software, which he acknowledges is not cheap. “They say ‘I can’t buy it because the customer won’t pay for it,’” he said. “But what does that mean? What is the cost of not running a mold-filling analysis? The customer will pay for it. He’ll pay for it with a bad tool that runs slower cycles or bad parts. The tool shop will pay for it by reworking a tool—often on their own dime—that doesn’t run right.”For smaller mold manufacturers that don’t have the resources for in-house simulation software or an analyst on staff, there are companies such as EPS Flotek that can perform a full range of engineering services for them using MoldEx 3D simulation software. EPS Flotek offers that service for them on a per-project basis for about $2500 to $3500.Moldex3D can predict the condition of the plastic parts during the molding process to help moldmakers understand how best to design the mold for optimum processability. The advantage to the mold designer and the moldbuilder is that simulation is a value added service. “The moldmaker can tell his customer, ‘We’re making sure you get the best tool and best part up front. We’ll fix anything that’s wrong after the mold is built but we don’t want to have to do that.’”Industrial Molds has realized the mutual benefits gained by both parties, noted Smith. “Performing the mold-fill simulation analysis saves us from doing an extra round of venting or reworking vents and runners,” he said. “On the customer side, they can see proof positive why their original idea for the design of the part, and the type of mold they thought they wanted, might not be the most optimum production mold for the part. Performing the mold fill analysis with the tool maker is the best path.”“In one instance, the customer wanted to use a three-plate mold. The part was captured by slides on all four sides so the runner system was very large. Early on in the design stage we did a quick runner system design to run a mold analysis. The analysis showed us there would be a tremendous amount of scrap, and the cycle time would be extended because of the distances the runners had to flow. We changed the basic mold configuration based on that problem, showed the customer why we needed to change the design, and got approval to change the mold design.”“We got the answer just a few days into the mold design rather than after we’d cut steel,” said Smith. “It was so meaningful for the customer to actually see the problems that would result from the three-plate mold design. It’s one thing to say to a customer ‘I think this is going to be a problem,’ but when you can show them the actual simulation that reveals the problem, that’s the real evidence—not speculation. And we did that in just a few days’ time rather than well into the design cycle.”“By not using mold analysis software, companies are losing out on unrealized profit and unrealized cost savings in design a mold that doesn’t perform optimally. Address the issues up front and everything becomes more efficient,” said Carobus. “It’s like an insurance policy. You don’t notice just how much you’ve saved until something goes wrong.”
GETTING A QUOTE WITH LK-MOULD IS FREE AND SIMPLE.
FIND MORE OF OUR SERVICES:
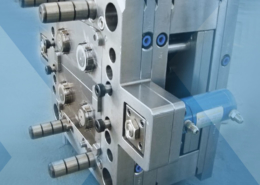
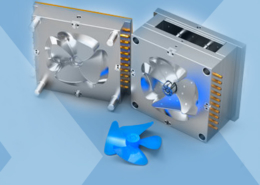
Plastic Molding

Rapid Prototyping
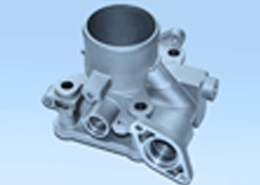
Pressure Die Casting
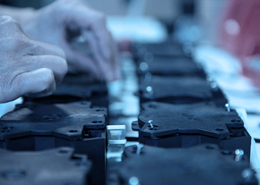
Parts Assembly
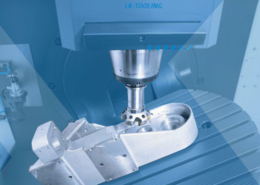