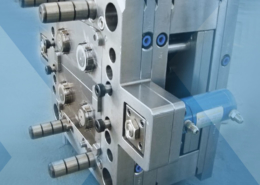
The New Lightweights: Injection Molded 'Hybrid' Composites Spur Auto
Author:gly Date: 2024-09-30
The world's largest low-pressure injection molding machine, designed and constructed by Infiltrator Systems at the company's Winchester, KY, manufacturing facility, took five months to engineer and nine months to build. However, today the machine is producing the Infiltrator IM 1530 Septic Tank product line being molded in a mold designed and built by Franchino Mold and Engineering of Lansing, MI. The mold installed in the press weighs 420,000 lbs. and molds a 15-foot long, 245-lb. polypropylene tank half, which the company claims is the world's largest molded part.
Coppes told PlasticsToday that the company's success with its 1000-gallon septic tanks led the market to demand tanks in a 1500-gallon size. Infiltrator is the world's largest septic products company. Molding a tank this large required a 6,000-ton low-pressure injection molding machine. "We brought in a lot of resources to help us redesign and engineer a press to make it suitable for our needs," Coppes explained. Infiltrator molds its own product and parts requirements in-house, and also has a number of regular injection molding presses to mold its other products.
Plasteurope.com is a business information platform for the European plastics industry. It is part of KI Kunststoff Information and PIE Plastics Information Europe, one of the leading content providers for the European plastics industry. We offer daily updated business news and reports, in-depth market analysis, polymer prices and other services for the international plastics industry, including a suppliers guide, career opportunities, a trade name directory and videos.
Phillips noted that the biggest challenge was the logistics involved in delivering the mold. After the mold was built, it was disassembled and placed on a fleet of 15 trucks for shipping from Lansing, MI, to Winchester, KY. A team of moldmakers was then sent to Kentucky to re-assemble the mold on Infiltrator's plant floor.
What's happening across the country is that the cost of expanding sewer plants has risen and a lot of the federal grant money for these infrastructure projects has dried up," Coppes explained. "That means more people and communities are looking at septic systems rather than sewer systems."
Bryan Coppes, VP of engineering at Infiltrator Systems, said, "Rounding out the successful IM-Tank product line was a high priority for Infiltrator. Franchino is our largest tooling vendor and with their experience with our other large-part molds it made them the right choice for this project."
Coppes added that the ability to mold septic tanks of this size "opens up a lot of doors" for the company in this marketplace. He noted that there is more demand for polymer septic tanks as replacements for concrete tanks because of the greater strength of the polymer tanks as well as the ease of installation and the fact that no large equipment is required.
Franchino employs 85 people currently, but that will change as the company's expansion plans evolve. Phillips noted that the company recently purchased another 62,000-sf facility behind a current plant and the two buildings will be connected. "We're going through the building modifications now and moving equipment in, which will include a 50-ton crane to accommodate the larger sizes of the molds we build," he said.
Until she retired in September 2021, Clare Goldsberry reported on the plastics industry for more than 30 years. In addition to the 10,000+ articles she has written, by her own estimation, she is the author of several books, including The Business of Injection Molding: How to succeed as a custom molder and Purchasing Injection Molds: A buyers guide. Goldsberry is a member of the Plastics Pioneers Association. She reflected on her long career in "Time to Say Good-Bye."
The world's largest low-pressure injection molding machine, designed and constructed by Infiltrator Systems at the company's Winchester, KY, manufacturing facility, took five months to engineer and nine months to build. However, today the machine is producing the Infiltrator IM 1530 Septic Tank product line being molded in a mold designed and built by Franchino Mold and Engineering of Lansing, MI. The mold installed in the press weighs 420,000 lbs. and molds a 15-foot long, 245-lb. polypropylene tank half, which the company claims is the world's largest molded part.
A project of this magnitude certainly is a partnership, and Phillips commented that Infiltrator is a great partner with which to work. "They are such an innovative company and willing to take risks. We love to have them as a partner," he added. "They've taught us a lot over the years, and through our input we've helped them find solutions as well. They like to challenge us and we enjoy meeting those challenges that result in success."
Infiltrator Systems, a Graham Partners portfolio company, employs approximately 280 people at its facility. Through its subsidiary, Champion Polymer Recycling, Infiltrator is a leading purchaser of "green materials" including post-consumer and post-industrial recycled plastics used in the manufacture of Infiltrator products.
The mold is built with aluminum core and cavity, housed in a steel mold base in what is known as a "hybrid mold" and took more than 10,000 man-hours to build. The cavity work was done using multiple Tarus 5-axis mills with table sizes of 114" x 120." It also contains the largest hot runner manifold system in operation in the world, explained Todd Phillips, VP of Franchino, which specializes the design engineering and manufacturing of very large molds to produce products that challenge the limits of injection molding. "This is the largest mold we've made to date," Phillips told PlasticsToday.
© 2001-2024 Plasteurope.com | Imprint | Privacy | Cookie settings Plasteurope.com is a business information platform for the European plastics industry. It is part of KI Kunststoff Information and PIE Plastics Information Europe, one of the leading content providers for the European plastics industry. We offer daily updated business news and reports, in-depth market analysis, polymer prices and other services for the international plastics industry, including a suppliers guide, career opportunities, a trade name directory and videos. News | Polymer Prices | Material Databases | Plastics Exchange | Suppliers Guide | Jobs | Register | Advertising PIE – Plastics Information Europe | KI – Kunststoff Information | KunststoffWeb | Plastics Material Exchange | Polyglobe | K-Profi
Each shot is a mirror image of itself with a cutout in the top for tank access. "Other than that the tanks are symmetrically the same," said Coppes. One half has gaskets and the halves are sealed together. The parts handling and finishing stations utilize what Infiltrator believes is the largest six-axis robot in the world.
Franchino has many years (16-18) of experience with building aluminum and hybrid aluminum and steel tooling for very large parts. Phillips said that some of those molds the company built have one to two million shots on them, a testament to the longevity of aluminum tooling in many large-part molding applications.
Franchino previously created what is now the world's second largest mold, Infiltrator System's IM-1060 tank in a mold to produce a part weighing 160 lbs.
GETTING A QUOTE WITH LK-MOULD IS FREE AND SIMPLE.
FIND MORE OF OUR SERVICES:
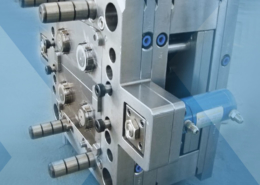
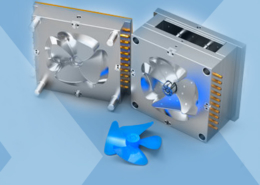
Plastic Molding

Rapid Prototyping
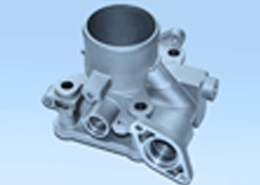
Pressure Die Casting
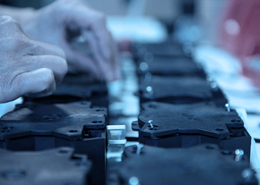
Parts Assembly
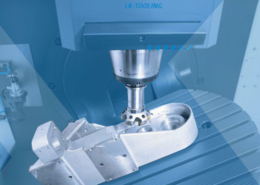