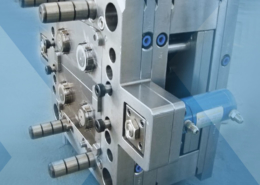
The Best Metal 3D Printers in 2024 - top 100 injection molding companies
Author:gly Date: 2024-09-30
“You also have the possibility of functionalization with thermoplastic pultrusion,” Wilhelm says. “With thermoset profiles, you don’t have the ability to thermoform or overmold them with a strong material connection. With thermoplastics, you can just heat up a profile, place it in an injection molding die or a compression molding die, and co-mold or overmold it with shorter fiber-reinforced polymers.” Providing this local reinforcement for the composite part reduces the need for the time-consuming and expensive process of cutting, placing and consolidating layers of reinforcing tapes.
Elli notes that the company has found Scientific Molding to be an important tool for analyzing and remedying problems with incoming molds. “We’ve developed a process for diagnosing tools that allows us to talk to our customers in a factual way about what’s going on with transfer tooling. That’s one reason why we’re a vendor of choice for transfers. We can get that tool up, running, and making the best parts it’s capable of producing as fast, or faster, than anyone else, while also backing it up with ‘process-pedigree’ documentation to produce consistent parts going forward.”
As for hiring… at last count, Empire Precision has added a project manager, a tooling engineer/quoter, a scheduler, maintenance personnel, machine operators, and materials specialists since posting its online help-wanted ad.
Virtually all of the company’s manufacturing auxiliaries—from suppliers such as Novatec, Advantage Engineering, and Rapid Granulator—are backed-up with spares. Both power systems and heat exchangers are used with redundant pumps. Elli says the in-house team that laid out the shop floor made sure to reserve space for a preventive-maintenance staging area and for equipment cleaning.
This month’s resin pricing report includes PT’s quarterly check-in on select engineering resins, including nylon 6 and 66.
Another advantage of GFRTP rebar is the ability to create surface deformations on it with secondary processes, according to Roberto Lopez-Anido, a University of Maine professor and member of the thermoplastic rebar research team at its Advanced Structures & Composites Center (ASCC). Adding ribbing or twisted fibers to the rebar’s surface, for example, could create texture that would help improve the bond between rebar and concrete.
This Knowledge Center provides an overview of the considerations needed to understand the purchase, operation, and maintenance of a process cooling system.
With mechanical recycling via shredding of the profiles and the use of injection molding, the team found that a part made with recycled materials achieved nearly the same properties as one made with virgin materials. The properties of the part did depend on the amount of recycled material included in it. The team is currently studying the properties of nylon 6 that is removed from a part using chemical recycling.
Introduced by Zeiger and Spark Industries at the PTXPO, the nozzle is designed for maximum heat transfer and uniformity with a continuous taper for self cleaning.
ERP software from IQMS, run through a wireless router, monitors every machine to help manage production. Process monitoring is accomplished through a data-acquisition system supplied by RJG Inc. (rjginc.com).
Across all process types, sustainability was a big theme at NPE2024. But there was plenty to see in automation and artificial intelligence as well.
Operating three shifts, 24/7, the company employs 55 and runs 40 molding machines, mostly from Arburg and Sumitomo. It operates an ISO Class 7 clean room, and its secondary operations include light assembly, pad printing, machining, ultrasonic welding, and part functionality testing.
“Once we establish the process that we’re going to use in production, it’s a frozen process, and that’s what we run. We don’t ‘process at will’ anymore. Everything drives back to the pedigree of that very specific process.”
After successfully introducing a combined conference for moldmakers and injection molders in 2022, Plastics Technology and MoldMaking Technology are once again joining forces for a tooling/molding two-for-one.
In this collection of articles, two of the industry’s foremost authorities on screw design — Jim Frankand and Mark Spalding — offer their sage advice on screw design...what works, what doesn’t, and what to look for when things start going wrong.
Successfully starting or restarting an injection molding machine is less about ticking boxes on a rote checklist and more about individually assessing each processing scenario and its unique variables.
While prices moved up for three of the five commodity resins, there was potential for a flat trajectory for the rest of the third quarter.
The researchers used polyethylene terephthalate-glycol (PETG), an amorphous copolymer of PET and E-glass fibers for this process. “The advantages of PETG being amorphous is that it is not sensitive to cooling, so we do not have problems with crystallization. But we need to deal with the viscosity of the material, and being amorphous, it doesn’t have a well-defined melt temperature. That requires some calibration of the process,” says Lopez-Anido.
Next, the material travels into the cooled die where, depending on the type of polymer used, water or air cools the pultruded profile below the glass transition temperature in a controlled manner. The profile is then cut to the desired length.
Thousands of people visit our Supplier Guide every day to source equipment and materials. Get in front of them with a free company profile.
Across the show, sustainability ruled in new materials technology, from polyolefins and engineering resins to biobased materials.
Empire runs parts in filled and unfilled engineering resins—everything from acetal, PPO alloy, and TPE to PPA, PEI, PPS, PEEK, and LCP. Mold temperatures of 500 to 800 F are routine. Empire uses a little less that 40,000 lb/month of materials to manufacture and ship 7 million to 10 million parts a year. Average annual sales are approximately $8 million.
A U.S. custom injection molder that’s hiring? You couldn’t miss the on-line “help wanted” notices this summer when visiting empireprecision.com, the website belonging to molder and moldmaker Empire Precision in Rochester, N.Y. And when visiting the company in person, you’ll quickly learn what company officials believe to be a key reason for their company’s growth: From the top to the shop, Empire Precision has fully embraced the principles of “Scientific Molding.” What’s more, the company has developed and implemented a proprietary business system for putting those principles into practice.
Multiple speakers at Molding 2023 will address the ways simulation can impact material substitution decisions, process profitability and simplification of mold design.
Elli believes there’s much more involved in Scientific Molding than simply using process-monitoring sensors: “I think that Scientific Molding has nothing to do with sensors. But if you develop a process along its principles, and then you put sensors on it, you can assess how you’re doing. It kind of ‘opens up’ the mold and lets you see what’s going on inside before waiting for it to actually open up and knock out a part.
Core Technology Molding turned to Mold-Masters E-Multi auxiliary injection unit to help it win a job and dramatically change its process.
Second quarter started with price hikes in PE and the four volume engineering resins, but relatively stable pricing was largely expected by the quarter’s end.
In a time where sustainability is no longer just a buzzword, the food and beverage packaging industry is required to be at the forefront of this innovation. By adopting circular packaging processes and solutions, producers can meet regulatory requirements while also satisfying consumer demand and enhancing brand reputation. Join Husky to learn more about the broader implications of the circular economy — as well as how leading brands are leveraging this opportunity to reduce costs, increase design flexibility and boost product differentiation. Agenda: The cost and operational benefits of embracing circularity Key materials in circular packaging — including rPET and emerging bioplastics How to design a circular food and beverage package Strategies for selecting sustainable closures to future-proof packaging solutions Optimization and streamlining of production processes for enhanced efficiency How Husky Technologies can enable your sustainable success
While the major correction in PP prices was finally underway, generally stable pricing was anticipated for the other four commodity resins.
ASCC’s non-reactive pultrusion process begins with towpregs or pre-impregnated fibers that are fed into a guidance system. The material is then heated to the desired consolidation temperature of the thermoplastic polymer. The heating source makes the process efficient and reduces the time the material remains in the consolidating die that shapes it into the desired profile or sheet.
Empire Precision has an active Six Sigma program in place. In addition to Trudeau’s black belt, Gary Oliver, senior process engineer; Steve Steinmetz, production manager; and Chris Judd, quality director are Green Belts.
Recyclability of the thermoplastic profiles was part of the researchers’ work. “We did a study to find out which recycling route and formulation would lead to good mechanical properties compared to virgin materials,” says Wilhelm.
Empire uses Autodesk’s Moldflow software (moldflow.com), of which Toolroom Manager Scott McLaren says, “It won’t tell us everything, but it helps us run molds in our equipment using Scientific Molding. It helps us to optimize tool design and predict potential problems and risks during the design phase.”
ASCC researchers designed and built a new continuous forming machine (CFM) that made it possible to produce rebar through a non-reactive thermoplastic pultrusion process. The CFM may be the key to overcoming the scalability and production issues that have been a problem with some other thermoplastic pultrusion processes.
Take a deep dive into all of the various aspects of part quoting to ensure you’ve got all the bases—as in costs—covered before preparing your customer’s quote for services.
Exhibitors and presenters at the plastics show emphasized 3D printing as a complement and aid to more traditional production processes.
Join Engel in exploring the future of battery molding technology. Discover advancements in thermoplastic composites for battery housings, innovative automation solutions and the latest in large-tonnage equipment designed for e-mobility — all with a focus on cost-efficient solutions. Agenda: Learn about cutting-edge thermoplastic composites for durable, sustainable and cost-efficient battery housings Explore advanced automation concepts for efficient and scalable production See the latest large-tonnage equipment and technology innovations for e-mobility solutions
Join KraussMaffei for an insightful webinar designed for industry professionals, engineers and anyone interested in the manufacturing processes of PVC pipes. This session will provide a comprehensive understanding of the technology behind the production of high-quality PVC pipes: from raw material preparation to final product testing. Agenda: Introduction to PVC extrusion: overview of the basic principles of PVC pipe extrusion — including the process of melting and shaping PVC resin into pipe forms Equipment and machinery: detailed explanation of the key equipment involved — such as extruders, dies and cooling systems — and their roles in the extrusion process Process parameters: insight into the critical process parameters like temperature, pressure and cooling rates that influence the quality and consistency of the final PVC pipes Energy efficiency: examination of ways to save material and energy use when extruding PVC pipe products
In May 2023, at the North American Pultrusion Conference hosted by ACMA in collaboration with the European Pultrusion Technology Association, researchers shared the results of thermoplastic pultrusion projects and opportunities they present in the composites marketplace.
Cavity-pressure monitoring describes precisely what’s taking place inside the mold, providing a transparent view of the conditions under which a part is created and ensuring conformance with GMP and ISO 13485 in medical injection molding.
Empire also designs and manufactures molds. Employing eight toolmakers, it provides everything from prototype mold manufacturing and engineering changes to complete builds—both for its own use and for captive molding customers.
FRP rebar made with thermoset matrices offers many advantages in concrete bridge and highway construction, including its strength, light weight and corrosion resistance. But it has some disadvantages. Unlike steel rebar, it can’t be bent into different shapes at the construction site and is not easily recycled.
Your source for composite reinforcements and technical supportVectorply combines highly engineered composite reinforcements with industry-leading engineering and technical support to give customers a clear path to achieve their production goals.
Pultrusion offers many advantages for companies that want to produce consistent, high-strength and dimensionally accurate parts through a highly automated system. Thermoset matrices have been the material of choice for years, but researchers now hope to expand the use of thermoplastics in pultrusion as well.
The Plastics Industry Association (PLASTICS) has released final figures for NPE2024: The Plastics Show (May 6-10; Orlando) that officially make it the largest ever NPE in several key metrics.
With advocacy, communication and sustainability as three main pillars, Seaholm leads a trade association to NPE that ‘is more active today than we have ever been.’
The team faced some challenges in developing this process. Since caprolactam – the monomer of nylon 6 – can be negatively affected by moisture, they used special matrix formulations and handling methods to avoid those problems. They also dealt with limited availability of the special sizing required to get a good adhesion of the thermoplastic matrix to the fiber.
Plastics Technology covers technical and business Information for Plastics Processors in Injection Molding, Extrusion, Blow Molding, Plastic Additives, Compounding, Plastic Materials, and Resin Pricing. About Us
Join this webinar to explore the transformative benefits of retrofitting your existing injection molding machines (IMMs). Engel will guide you through upgrading your equipment to enhance monitoring, control and adaptability — all while integrating digital technologies. You'll learn about the latest trends in IMM retrofitting (including Euromap interfaces and plasticizing retrofits) and discover how to future-proof your machines for a competitive edge. With insights from industry experts, it'll walk you through the decision-making process, ensuring you make informed choices that drive your business forward. Agenda: Maximize the value of your current IMMs through strategic retrofitting Learn how to integrate digital technologies to enhance monitoring and control Explore the benefits of Euromap interfaces and plasticizing retrofits Understand how retrofitting can help meet new product demands and improve adaptability Discover how Engel can support your retrofitting needs, from free consultations to execution
On Empire’s manufacturing floor, under 23-ft-high ceilings, materials are pneumatically conveyed above the center spacing between three rows of machines, which prevents any possibility of materials and molded parts competing for floorspace. The shop floor is currently lit by sodium halite lighting, but Empire will convert to energy-efficient compact fluorescent lighting later this year.
The American Composites Manufacturers Association (ACMA) is the world's largest trade group representing over 3,000 companies in the composites industry in North America alone. ACMA is recognized as the premier provider of composites industry educational resources through its CAMX show, conferences, and Certified Composites Technician (CCT®) program. It serves its members and the industry by providing strong, proactive leadership in growing the composites market and technical, legislative and regulatory affairs.
“We decided that what we really needed was to create a process,” he explains. “We didn’t create a new way to process plastics. We built a business system. We take all of the important data when we develop a process, fine-tune it, and we put it into a software package that we wrote and store in a captive online database. It’s a procedure that’s been in place now for more than five years.
Medical-component specialist LightningCath has carved a niche meeting the needs of small to medium-sized entrepreneurs with complex catheter designs … quickly.
Discover how artifical intelligence is revolutionizing plastics processing. Hear from industry experts on the future impact of AI on your operations and envision a fully interconnected plant.
With a capital investment of approximately $4 million, Elli expects Empire’s current sales volume of $8 million to rocket to $20 million in less than four years through the use of procedures the company has developed under the influence of Scientific Molding.
In this collection of content, we provide expert advice on welding from some of the leading authorities in the field, with tips on such matters as controls, as well as insights on how to solve common problems in welding.
Say “manufacturing automation” and thoughts immediately go to the shop floor and specialized production equipment, robotics and material handling systems. But there is another realm of possible automation — the front office.
Resin drying is a crucial, but often-misunderstood area. This collection includes details on why and what you need to dry, how to specify a dryer, and best practices.
Additive technology creates air pockets in film during orientation, cutting down on the amount of resin needed while boosting opacity, mechanical properties and recyclability.
Composites Manufacturing is the official publication of the American Composites Manufacturers Association. Published bimonthly, it offers practical assessments of the current state of the composites industry as well as thoughtful explorations of the opportunities and challenges ahead. It includes timely coverage of core market segments, materials, processes and technical education plus topics such as sustainability, plant safety, operational efficiency and research advances. Subscribe to Composites Manufacturing Magazine.
Sustainability continues to dominate new additives technology, but upping performance is also evident. Most of the new additives have been targeted to commodity resins and particularly polyolefins.
Scientific Molding, promulgated by Plastics Technology columnist, John Bozzelli—the founder of Injection Molding Solutions (a.k.a. Scientific Molding), Midland, Mich. (scientificmolding.com)—is a procedure for optimizing the molding process by managing material viscosity through the control of material temperature and pressure, injection velocity, and mold temperature. Neal P. Elli, president of Empire Precision, says his company’s adoption and adaptation of these principles began about eight years ago after attending a Scientific Molding seminar.
In this three-part collection, veteran molder and moldmaker Jim Fattori brings to bear his 40+ years of on-the-job experience and provides molders his “from the trenches” perspective on on the why, where and how of venting injection molds. Take the trial-and-error out of the molding venting process.
American Composites Manufacturers Association 2000 N. 15th Street, Ste. 250, Arlington, VA 22201 Ph | 703.525.0511 Fx | 703.525.0743 | www.acmanet.org
The researchers compared the properties of thermoplastic profiles made with nylon 6 and Elium® resin from Arkema with thermoset profiles made with epoxy and vinyl ester.
Mixed in among thought leaders from leading suppliers to injection molders and mold makers at the 2023 Molding and MoldMaking conferences will be molders and toolmakers themselves.
In this collection, which is part one of a series representing some of John’s finest work, we present you with five articles that we think you will refer to time and again as you look to solve problems, cut cycle times and improve the quality of the parts you mold.
“Scientific Molding takes the fear out of molding engineering materials,” states Mark Trudeau, a Six Sigma Master Black Belt, and the company’s director of operations. “Without theory, you run completely on experience, which is fine, but I don’t believe it allows you to control technology.”
Empire needs a “scientific” approach for its kind of molding. At its 42,500-ft², facility, it specializes in precision, intricately detailed, small and micro parts—some weighing less than 0.1 g—for medical, electrical/electronic, industrial, and consumer products. The firm is also proficient in MuCell microcellular molding (trexel.com) and multicomponent, two-shot parts. Empire is ISO 9001 and 13485 registered, UL46D recognized, and TS 16949 compliant.
While the melting process does not provide perfect mixing, this study shows that mixing is indeed initiated during melting.
Adds McLaren: “Our designs may take a little bit longer, since we use Scientific Molding principles for process prediction and Moldflow to assess mold designs, but these procedures help us get the process ‘scripted’ before we start to build the tool. An easier way to manufacture a mold might make it harder to mold a good part.”
“The big benefits of this process are the extremely low viscosity of the monomer and the adjustability of the reactivity by changing the amount of activator and catalyst, so you can make the resin’s polymerization quite fast,” says Wilhelm. This results in a composite with a very high fiber volume content and better adherence between the fibers and the matrix.
The aim of this presentation is to guide you through the factors and the numbers that will help you determine if a robot is a smart investment for your application. Agenda: Why are you considering automation? What problems are you trying to solve? How and why automation can help Crunch the numbers and determine the ROI
The equipment for producing pultruded thermoplastic and thermoset profiles is similar, however the thermoplastic process also requires a pre-heating and drying unit and a metering and mixing machine.
“We have already started with the first customers on the process to series production, and I hope we can realize the first automotive part – which has in-situ pultruded profiles – by the end of this year,” Wilhelm adds. He hopes this proof of concept case leads to the scaling up of mass production for hundreds of thousands of parts per year.
One other thing you’ll notice on the shop floor is a digital display screen at every molding station. Each press can be monitored by Empire’s proprietary “Fill Analysis Software,” which presents a visual, shot-to-shot verification that key process parameters are run in compliance with setpoints generated by the company’s Scientific Molding design of experiments (DOE).
Recycling of composite parts is also important today, especially in Europe, where manufacturers must increasingly be able to prove the recyclability of their materials to OEMs. Components produced using reactive in situ thermoplastic pultrusion are easy to recycle.
When, how, what and why to automate — leading robotics suppliers and forward-thinking moldmakers will share their insights on automating manufacturing at collocated event.
Ultradent's entry of its Umbrella cheek retractor took home the awards for Technical Sophistication and Achievement in Economics and Efficiency at PTXPO.
To produce these thermoplastic pultrusions, Wilhelm’s team used a reactive process in which impregnation of the pre-heated fibers and polymerization of the matrix takes place in a heated die block.
There are several reasons for increased interest in thermoplastic pultrusion, Wilhelm says. When pultrusion was introduced in the 1950s, composites with high fiber fills could only be impregnated with low viscosity thermoset resin systems, such as vinyl esters, polyesters and epoxies. New materials have opened the possibility of using reactive thermoplastic resins like nylon 6 or PMMA (polymethyl methacrylate), which are in the same price range as thermoset resins.
Neal P. Elli (r.), president of Empire Precision, literally stands behind his company’s thorough application of Scientific Molding principles. At this unusual cell, whose small throughput couldn’t be handled by conventional dryers, he stands behind a screen displaying the cell’s performance with the company’s own Fill Analysis Software. At left is Gary Oliver, senior process engineer.
Wilhem says their research has shown that a good business case can be made for industrial use of thermoplastic profiles. They are currently working on research projects in construction (rebar), transportation (battery enclosures) and the wind industry (spar caps).
Plastics Technology’s Tech Days is back! Every Tuesday in October, a series of five online presentations will be given by industry supplier around the following topics: Injection Molding — New Technologies, Efficiencies Film Extrusion — New Technologies, Efficiencies Upstream/Downstream Operations Injection Molding — Sustainability Extrusion — Compounding Coming out of NPE2024, PT identified a variety of topics, technologies and trends that are driving and shaping the evolution of plastic products manufacturing — from recycling/recyclability and energy optimization to AI-based process control and automation implementation. PT Tech Days is designed to provide a robust, curated, accessible platform through which plastics professionals can explore these trends, have direct access to subject-matter experts and develop strategies for applying solutions in their operations.
“I must have one of the smallest screw/barrel sizes in the business on all my presses,” he adds. “For instance, on an 80-tonner, I’ll usually have an 3-oz barrel. We use the smallest shot size that we can get in order to apply more melt pressure and to ensure that we’re not pressure-limited.”
“That’s a tangible event that we can go back to when we develop a process. It also helps us when, for whatever reason, customers change materials. And it shows us how to evaluate tools that come in, regardless of who built them and where they came from.”
How do you create processes that allow 40 molding machines to control material viscosity and consistently fill your molds, even for challenging micro parts? Empire Precision’s answer is Scientific Molding.
Join Wittmann for an engaging webinar on the transformative impact of manufacturing execution systems (MES) in the plastic injection molding industry. Discover how MES enhances production efficiency, quality control and real-time monitoring while also reducing downtime. It will explore the integration of MES with existing systems, emphasizing compliance and traceability for automotive and medical sectors. Learn about the latest advancements in IoT and AI technologies and how they drive innovation and continuous improvement in MES. Agenda: Overview of MES benefits What is MES? Definition, role and brief history Historical perspective and evolution Longevity and analytics Connectivity: importance, standards and integration Advantages of MES: efficiency, real-time data, traceability and cost savings Emerging technologies: IoT and AI in MES
Mold maintenance is critical, and with this collection of content we’ve bundled some of the very best advice we’ve published on repairing, maintaining, evaluating and even hanging molds on injection molding machines.
Pultruded thermoplastic (GFRTP) rebar could be the solution. After their initial fabrication, these reinforcement bars could be sent to the jobsite where they could be reheated and formed into hooks, stirrups or other special configurations a concrete pour requires.
Empire Precision has about 450 active molds and makes three to five mold changes per shift. Most of its tools are built in S-70 or H-13 steel, though it usually uses stainless steel for medical projects. Empire has also built aluminum tools from day one, which are now growing in popularity among injection molders because of their superior heat transfer and faster machining. Empire has run a million cycles off on one of its aluminum molds. On occasion it also has built aluminum/steel “hybrid” tooling.
“In my mind, it’s all about how you build a mold, and how you build a process that allows the molding machine to control material viscosity, so you’ll fill the tool consistently shot after shot.”
The team used digitized sensors during their research to collect data about the interaction of materials in various processes and to look at properties and special material behavior that could never be seen before. Wilhelm says this digitization process has drawn the interest of industry, which needs this type of data to provide information about the CO2 produced and the energy used during manufacturing. Manufacturers could also use the collected data to improve the quality of their products and the efficiency of their processes.
What it can’t build in-house it outsources from established local moldmakers and specialized regional and offshore partners. Additionally, Empire builds hot-runner tooling, incorporating systems primarily from PolyShot, Mold-Masters, and Heitec. It can make mold bases and pins, but it mostly focuses on core and cavity work.
Learn about sustainable scrap reprocessing—this resource offers a deep dive into everything from granulator types and options, to service tips, videos and technical articles.
technotrans says climate protection, energy efficiency and customization will be key discussion topics at PTXPO as it displays its protemp flow 6 ultrasonic eco and the teco cs 90t 9.1 TCUs.
Empire Precision’s Scientific Molding-based software package, developed in-house, helps the company “freeze” optimum process parameters—such as optimum flow rate for filling a mold—and repeatably reproduce them.
While prices moved up for three of the five commodity resins, there was potential for a flat trajectory for the rest of the third quarter.
Vectorply combines highly engineered composite reinforcements with industry-leading engineering and technical support to give customers a clear path to achieve their production goals.
Driven by brand owner demands and new worldwide legislation, the entire supply chain is working toward the shift to circularity, with some evidence the circular economy has already begun.
Formnext Chicago is an industrial additive manufacturing expo taking place April 8-10, 2025 at McCormick Place in Chicago, Illinois. Formnext Chicago is the second in a series of Formnext events in the U.S. being produced by Mesago Messe Frankfurt, AMT – The Association For Manufacturing Technology, and Gardner Business Media (our publisher).
Its highly automated moldmaking capabilities include wire and sinker CNC EDM, high-speed CNC milling, grinding, and polishing. An eye-catcher is its Makino E33, a late-model high-speed mill. It’s serviced by a 3R Robotic system. A late-model EDM sinker nearby runs unattended.
Gifted with extraordinary technical know how and an authoritative yet plain English writing style, in this collection of articles Fattori offers his insights on a variety of molding-related topics that are bound to make your days on the production floor go a little bit better.
At the Fraunhofer Institute for Chemical Technology ICT in Germany, Michael Wilhelm and his co-researchers have developed a processing method for a reactive thermoplastic matrix system for pultrusion using nylon 6 (polycaprolactam). Their research focused on the robust processing and functionalization of the pultruded parts and ecological and economic aspects of the thermoplastic pultrusion process.
Processors with sustainability goals or mandates have a number of ways to reach their goals. Biopolymers are among them.
ACMA offers a number of events throughout the year to facilitate critical information exchanges and professional connections.
August 29-30 in Minneapolis all things injection molding and moldmaking will be happening at the Hyatt Regency — check out who’s speaking on what topics today.
Mike Sepe has authored more than 25 ANTEC papers and more than 250 articles illustrating the importance of this interdisciplanary approach. In this collection, we present some of his best work during the years he has been contributing for Plastics Technology Magazine.
Despite price increase nominations going into second quarter, it appeared there was potential for generally flat pricing with the exception of a major downward correction for PP.
“We saw that the pultrusions based on reactive thermoplastics were definitely comparable to thermosets and in some cases had slightly higher properties,” says Wilhelm. “But the properties are always dependent on the use case, so it’s important to look at the use case and decide if a thermoplastic or a thermoset is more suitable to use. We don’t want to replace all thermoset profiles, but whenever the benefits of thermoplastics can be used why not use them?”
Study shows the plastic compounding process is being used to boost electrical properties and UV resistance while custom compounding is increasingly being used to achieve high-performance in plastic-based goods.
GETTING A QUOTE WITH LK-MOULD IS FREE AND SIMPLE.
FIND MORE OF OUR SERVICES:
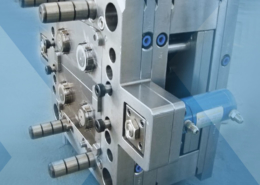
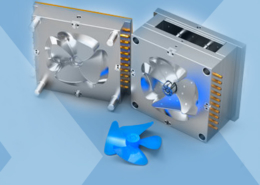
Plastic Molding

Rapid Prototyping
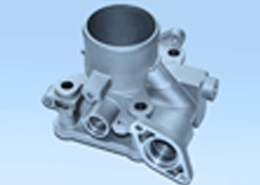
Pressure Die Casting
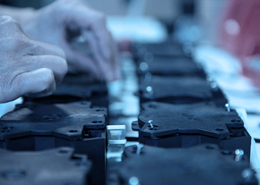
Parts Assembly
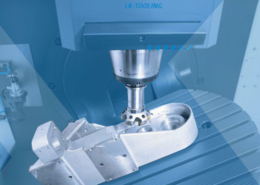