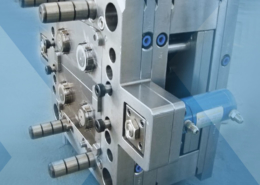
The Best DIY Injection Molding Machines of 2023 - low volume plastic injection m
Author:gly Date: 2024-09-30
By integrating TEI into General Motors, the automotive giant told Reuters it was ‘bolstering its portfolio of innovations and secure access to unique casting technology.’ TEI has reportedly been working with Tesla since 2017, with the casting company then agreeing a three-year contract with Voxeljet for the purchase of 3D printed sand moulds and cores in February 2018. While working with Tesla, TEI is believed to have supported the development of Tesla’s Model Y, Model 3, Cybertruck and heavy-duty Semi truck by prototyping large moulds.
Professor Giovanni Lucchetta of the University of Padua, founder of Smart Mold, a university spin off that developed and patented GAPP, explained the technology at the Sirmax stand. Italy-based Sirmax has a 50% stake in Smart Mold.
General Motors has acquired casting manufacturer Tooling & Equipment International (TEI), a long-term user of Voxeljet’s binder jetting technology and supplier to Tesla.
With its expanded sand 3D printing capacity, TEI has been able to print hundreds of cores for several vehicle sets in one night. It is this capability that initially attracted General Motors to partner with the company and subsequently acquire it. It is understood that TEI will remain its own business with General Motors operating as its parent company.
International news agency Reuters broke the news last week and has reported that the acquisition is a key element in General Motors’ strategy to ‘make up ground on Tesla’. Tesla is said to have leaned on TEI, as well as three other suppliers, to facilitate its Gigacasting processes for the casting of large car structures in one piece.
Experimental tests cited by Lucchetta reportedly showed that GAPP can increase weld line strength by 240% in polypropylene reinforced with 35% short-glass fibers, almost reaching the nominal strength of the compound.
Weld lines, also called knit lines, are a common problem encountered by injection molders. Beyond aesthetic issues, weld lines can also lead to functional failure. During a press conference at K 2022 in Düsseldorf, Germany, compounder Sirmax Group introduced Gas-Assisted Push-Pull (GAPP) technology, which, it claims, can prevent weld lines in injection molded plastic parts.
Gas-Assisted Push-Pull technology enables dynamic packing of weld lines using a single injection unit and miniaturized injectors.
“Others have tried unsuccessfully to eliminate the criticality of weld lines in structural parts,” said Lucchetta in a prepared statement. Dynamic packing during the initial phase of the “holding” process allows for improved matrix interdiffusion at the interface and reorientation of the fibers in the direction of flow. However, according to Smart Mold, this typically requires two independent injection molding units. By contrast, GAPP allows for the dynamic packing of weld lines using a single injection unit and miniaturized gas injectors. Moreover, the small size of the gas injectors makes the technology compatible with existing molds, according to the company. “I am convinced that the strength of GAPP technology lies in the ability to implement it in existing molds with noninvasive and inexpensive modifications,” stressed Lucchetta.
Weld lines typically appear in a part when an obstruction of some kind separates the melt flow and prevents it from "knitting" together. Weld lines are among the most critical structural defects in parts made by the injection molding of fiber-reinforced thermoplastics, explained Sirmax in a press release. In a weld line, reinforcement fibers adopt an orthogonal orientation with respect to the filling direction, which results in a significant reduction in the strength and rigidity of the molded part. During the presentation at the K, Lucchetta explained how GAPP promotes the interpenetration of weld line flow fronts by changing the shape of the interface, promoting inter-diffusion between flow fronts, and realigning reinforcing fibers.
Come 2021, TEI was using two VX4000 sand 3D printing systems from Voxeljet and soon would earn itself a reputation as one of the largest users of sand 3D printing in the United States. Earlier this year, it was revealed the company had purchased a third VX4000 machine – expanding its additive manufacturing capacity to up to 2.5 litres per year – and was working with General Motors, producing cast cores for the series production of large-format, weight-saving structural components for the electric Cadillac CELESTIQ vehicle.
GAPP technology can solve weld line strength issues in all parts made of fiber-reinforced thermoplastics that require high mechanical performance, said Smart Mold. Applications include supports, brackets, cooling fans, pulleys, and other structural parts.
Editor in chief of PlasticsToday since 2015, Norbert Sparrow has more than 30 years of editorial experience in business-to-business media. He studied journalism at the Centre Universitaire d'Etudes du Journalisme in Strasbourg, France, where he earned a master's degree.
The technology can play a key role in advancing the use of recycled plastic in glass-fiber-reinforced compounds, he added.
GETTING A QUOTE WITH LK-MOULD IS FREE AND SIMPLE.
FIND MORE OF OUR SERVICES:
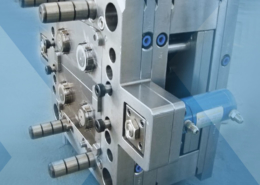
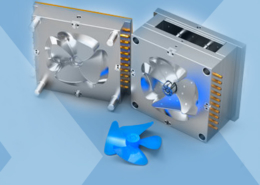
Plastic Molding

Rapid Prototyping
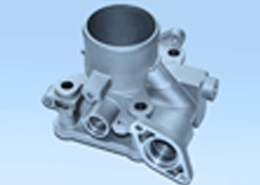
Pressure Die Casting
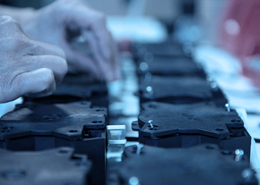
Parts Assembly
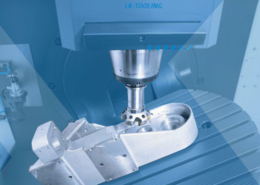