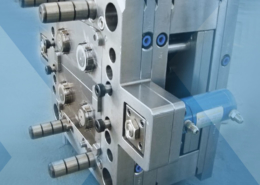
The Best DIY Injection Molding Machines of 2023 - large part injection molding
Author:gly Date: 2024-09-30
DeviceTalks is a conversation among medical technology leaders. It's events, podcasts, webinars and one-on-one exchanges of ideas & insights.
Our experienced team uses the newest equipment and automation, including brands such as Arburg, Toshiba, GF, Hexagon and Makino. Being transparent when producing parts is what makes us stand out. Not only will we set up the production in accordance with all your needs but we can also help to improve process quality and reduce cycle times. In-house medical tooling VEM’s in-house medical molds have helped us develop medical parts for molding and assembly for years. Our fully owned mold manufacturer consistently gives us complete control over molds and materials, allowing for optimal quality control. Optimisation, rigorous quality testing, and a professional approach to solving problems have always been our key approaches. Our molds are used worldwide by large medical companies, including Danaher Corporation, Cepheid, Foamtec Medical and Freudenberg Medical. Cleanroom molding and assembly VEM can offer services in design assistance, prototyping, production mold making, injection molding in a white room or cleanroom, component sourcing, assembly, testing and packaging. Both inside and outside our cleanroom, we have room and equipment for various sizes of injection machines. Our cleanroom is built in a modular way, which allows us to be flexible and increase size as quickly as possible according to customers’ needs. Three of our global locations include high-tech tool shops, which enable us to quickly develop molds from prototype to production, as well as perform maintenance and repairs. Manufacturing transfer Thinking about moving production out of China? Facing rising costs and import/export issues with medical device production in China, VEM helps clients with an expedited manufacturing transfer of plastic injection molding and assembly projects from China to Thailand with their supply chains intact. VEM has been manufacturing in Thailand for 13 years and medical device manufacturing project transfers are among our most popular services and can be set up and running within just a few weeks. For more information, read our case study under the ‘White Papers’ tab on this page. Medical plastics and device manufacturing in Thailand Manufacturing in Southeast Asia offers a lower price point, more flexibility, and a faster time to market than domestic manufacturing can provide. For more than 13 years, VEM has operated its wholly-owned manufacturing operation in Rayong, Thailand. The largest port in Thailand, Laem Chabang Port, is just a 30-minute drive from our facility and many large medical device and healthcare manufacturers are located nearby. There is an undeniable reason behind the growth of the medical device manufacturing industry in Thailand. The location is strategically attractive due to a skilled and educated workforce, a welcoming and open economy with a stable government, quality infrastructure, lower cost of labour and reduced import taxes, and ease of import/export of raw materials and components. About VEM Medical VEM currently has five manufacturing facilities across Asia, Europe and Central America. Our facility in Thailand is ISO 13485:2016 certified and specialises in medical device production and assembly. Our tool shop in Shenzhen, China, manufactures molds for our medical device clients worldwide.
VEM Medical is a full-service contract manufacturing organisation for medical plastics, devices and components. We partner with medical device companies across three continents to provide plastic injection molding, in-house tooling, prototyping, assembly, testing and more. A highly experienced team, best-in-class equipment and rigorous quality control help us deliver solutions for challenging medical tooling and molding applications. For more than 20 years, VEM has focused on customer satisfaction as our highest priority. Our clients range from small innovative companies to large multinational original equipment manufacturers (OEMs). Our production facility is certified according to ISO 9001 and ISO 13485, with a Class 100,000 (ISO 8) cleanroom. VEM Medical can produce small and precise molded parts for medical devices. Our medical assembly line is inspected by a stringent quality control team. A static 2K mixer for medical applications. VEM Medical can produce injection-molded parts for medical sub-assembly. Each of our manufactured devices must pass a testing procedure specified by the customer. Medical inserts can be molded in our clean room. We produce parts through complex medical tooling. Our team sub-assembles a tube connection for a breathing device. Many different parts can be moulded in our Class 100,000 cleanroom. Medical plastics and device manufacturing VEM is an integrated partner from design assistance and design for manufacturing to finished device production and assembly. Our fully owned tool shops, cleanroom production, assembly and sub-assembly capabilities provide rich opportunities to partner with us, no matter which stage your product is in. Our experienced team uses the newest equipment and automation, including brands such as Arburg, Toshiba, GF, Hexagon and Makino. Being transparent when producing parts is what makes us stand out. Not only will we set up the production in accordance with all your needs but we can also help to improve process quality and reduce cycle times. In-house medical tooling VEM’s in-house medical molds have helped us develop medical parts for molding and assembly for years. Our fully owned mold manufacturer consistently gives us complete control over molds and materials, allowing for optimal quality control. Optimisation, rigorous quality testing, and a professional approach to solving problems have always been our key approaches. Our molds are used worldwide by large medical companies, including Danaher Corporation, Cepheid, Foamtec Medical and Freudenberg Medical. Cleanroom molding and assembly VEM can offer services in design assistance, prototyping, production mold making, injection molding in a white room or cleanroom, component sourcing, assembly, testing and packaging. Both inside and outside our cleanroom, we have room and equipment for various sizes of injection machines. Our cleanroom is built in a modular way, which allows us to be flexible and increase size as quickly as possible according to customers’ needs. Three of our global locations include high-tech tool shops, which enable us to quickly develop molds from prototype to production, as well as perform maintenance and repairs. Manufacturing transfer Thinking about moving production out of China? Facing rising costs and import/export issues with medical device production in China, VEM helps clients with an expedited manufacturing transfer of plastic injection molding and assembly projects from China to Thailand with their supply chains intact. VEM has been manufacturing in Thailand for 13 years and medical device manufacturing project transfers are among our most popular services and can be set up and running within just a few weeks. For more information, read our case study under the ‘White Papers’ tab on this page. Medical plastics and device manufacturing in Thailand Manufacturing in Southeast Asia offers a lower price point, more flexibility, and a faster time to market than domestic manufacturing can provide. For more than 13 years, VEM has operated its wholly-owned manufacturing operation in Rayong, Thailand. The largest port in Thailand, Laem Chabang Port, is just a 30-minute drive from our facility and many large medical device and healthcare manufacturers are located nearby. There is an undeniable reason behind the growth of the medical device manufacturing industry in Thailand. The location is strategically attractive due to a skilled and educated workforce, a welcoming and open economy with a stable government, quality infrastructure, lower cost of labour and reduced import taxes, and ease of import/export of raw materials and components. About VEM Medical VEM currently has five manufacturing facilities across Asia, Europe and Central America. Our facility in Thailand is ISO 13485:2016 certified and specialises in medical device production and assembly. Our tool shop in Shenzhen, China, manufactures molds for our medical device clients worldwide.
Being transparent when producing parts is what makes us stand out. Not only will we set up the production in accordance with all your needs but we can also help to improve process quality and reduce cycle times. In-house medical tooling VEM’s in-house medical molds have helped us develop medical parts for molding and assembly for years. Our fully owned mold manufacturer consistently gives us complete control over molds and materials, allowing for optimal quality control. Optimisation, rigorous quality testing, and a professional approach to solving problems have always been our key approaches. Our molds are used worldwide by large medical companies, including Danaher Corporation, Cepheid, Foamtec Medical and Freudenberg Medical. Cleanroom molding and assembly VEM can offer services in design assistance, prototyping, production mold making, injection molding in a white room or cleanroom, component sourcing, assembly, testing and packaging. Both inside and outside our cleanroom, we have room and equipment for various sizes of injection machines. Our cleanroom is built in a modular way, which allows us to be flexible and increase size as quickly as possible according to customers’ needs. Three of our global locations include high-tech tool shops, which enable us to quickly develop molds from prototype to production, as well as perform maintenance and repairs. Manufacturing transfer Thinking about moving production out of China? Facing rising costs and import/export issues with medical device production in China, VEM helps clients with an expedited manufacturing transfer of plastic injection molding and assembly projects from China to Thailand with their supply chains intact. VEM has been manufacturing in Thailand for 13 years and medical device manufacturing project transfers are among our most popular services and can be set up and running within just a few weeks. For more information, read our case study under the ‘White Papers’ tab on this page. Medical plastics and device manufacturing in Thailand Manufacturing in Southeast Asia offers a lower price point, more flexibility, and a faster time to market than domestic manufacturing can provide. For more than 13 years, VEM has operated its wholly-owned manufacturing operation in Rayong, Thailand. The largest port in Thailand, Laem Chabang Port, is just a 30-minute drive from our facility and many large medical device and healthcare manufacturers are located nearby. There is an undeniable reason behind the growth of the medical device manufacturing industry in Thailand. The location is strategically attractive due to a skilled and educated workforce, a welcoming and open economy with a stable government, quality infrastructure, lower cost of labour and reduced import taxes, and ease of import/export of raw materials and components. About VEM Medical VEM currently has five manufacturing facilities across Asia, Europe and Central America. Our facility in Thailand is ISO 13485:2016 certified and specialises in medical device production and assembly. Our tool shop in Shenzhen, China, manufactures molds for our medical device clients worldwide.
Runyan concludes, “The exacting tolerances inherent in micro-optic applications, necessitate that OEMs collaborate with seasoned experts like Accumold from the outset to achieve precise, timely, and cost-effective manufacturing outcomes. We invite all Photonics West attendees to join us at booth 1566, where we’re excited to showcase our successes in micro molding and discuss how our expertise can elevate your micro-optics projects. Engage with our expert team and let’s explore how our partnership can illuminate the path to your product’s success.”
For more information, read our case study under the ‘White Papers’ tab on this page. Medical plastics and device manufacturing in Thailand Manufacturing in Southeast Asia offers a lower price point, more flexibility, and a faster time to market than domestic manufacturing can provide. For more than 13 years, VEM has operated its wholly-owned manufacturing operation in Rayong, Thailand. The largest port in Thailand, Laem Chabang Port, is just a 30-minute drive from our facility and many large medical device and healthcare manufacturers are located nearby. There is an undeniable reason behind the growth of the medical device manufacturing industry in Thailand. The location is strategically attractive due to a skilled and educated workforce, a welcoming and open economy with a stable government, quality infrastructure, lower cost of labour and reduced import taxes, and ease of import/export of raw materials and components. About VEM Medical VEM currently has five manufacturing facilities across Asia, Europe and Central America. Our facility in Thailand is ISO 13485:2016 certified and specialises in medical device production and assembly. Our tool shop in Shenzhen, China, manufactures molds for our medical device clients worldwide.
VEM has been manufacturing in Thailand for 13 years and medical device manufacturing project transfers are among our most popular services and can be set up and running within just a few weeks. For more information, read our case study under the ‘White Papers’ tab on this page. Medical plastics and device manufacturing in Thailand Manufacturing in Southeast Asia offers a lower price point, more flexibility, and a faster time to market than domestic manufacturing can provide. For more than 13 years, VEM has operated its wholly-owned manufacturing operation in Rayong, Thailand. The largest port in Thailand, Laem Chabang Port, is just a 30-minute drive from our facility and many large medical device and healthcare manufacturers are located nearby. There is an undeniable reason behind the growth of the medical device manufacturing industry in Thailand. The location is strategically attractive due to a skilled and educated workforce, a welcoming and open economy with a stable government, quality infrastructure, lower cost of labour and reduced import taxes, and ease of import/export of raw materials and components. About VEM Medical VEM currently has five manufacturing facilities across Asia, Europe and Central America. Our facility in Thailand is ISO 13485:2016 certified and specialises in medical device production and assembly. Our tool shop in Shenzhen, China, manufactures molds for our medical device clients worldwide.
On booth 1566 at Photonics West, Accumold will be showcasing its expertise as the world’s leading high-tech manufacturer of precision micro molded plastic components with part geometries from 5cm to less than 1mm in size. The company’s 30-plus years at the forefront of micro molding innovation ensures that it leads with expertise in insert molding, clean room molding, and 2-shot molding across materials like PEEK, Ultem, LCP, and a wide range of engineered thermoplastics.
Copyright © 2024 WTWH Media, LLC. All Rights Reserved. The material on this site may not be reproduced, distributed, transmitted, cached or otherwise used, except with the prior written permission of WTWH Media LLC. Site Map | Privacy Policy | RSS
VEM Europe, part of VEM Group, a global tooling and molding provider to the medical device and consumer goods industry, will exhibit at the upcoming trade fair Interplas, September 28-30. It is the UK’s leading plastics industry event, an exciting showcase for technologies, manufacturing processes and services essential to the plastics sector. VEM will be exhibiting at booth C69.
A highly experienced team, best-in-class equipment and rigorous quality control help us deliver solutions for challenging medical tooling and molding applications. For more than 20 years, VEM has focused on customer satisfaction as our highest priority. Our clients range from small innovative companies to large multinational original equipment manufacturers (OEMs). Our production facility is certified according to ISO 9001 and ISO 13485, with a Class 100,000 (ISO 8) cleanroom. VEM Medical can produce small and precise molded parts for medical devices. Our medical assembly line is inspected by a stringent quality control team. A static 2K mixer for medical applications. VEM Medical can produce injection-molded parts for medical sub-assembly. Each of our manufactured devices must pass a testing procedure specified by the customer. Medical inserts can be molded in our clean room. We produce parts through complex medical tooling. Our team sub-assembles a tube connection for a breathing device. Many different parts can be moulded in our Class 100,000 cleanroom. Medical plastics and device manufacturing VEM is an integrated partner from design assistance and design for manufacturing to finished device production and assembly. Our fully owned tool shops, cleanroom production, assembly and sub-assembly capabilities provide rich opportunities to partner with us, no matter which stage your product is in. Our experienced team uses the newest equipment and automation, including brands such as Arburg, Toshiba, GF, Hexagon and Makino. Being transparent when producing parts is what makes us stand out. Not only will we set up the production in accordance with all your needs but we can also help to improve process quality and reduce cycle times. In-house medical tooling VEM’s in-house medical molds have helped us develop medical parts for molding and assembly for years. Our fully owned mold manufacturer consistently gives us complete control over molds and materials, allowing for optimal quality control. Optimisation, rigorous quality testing, and a professional approach to solving problems have always been our key approaches. Our molds are used worldwide by large medical companies, including Danaher Corporation, Cepheid, Foamtec Medical and Freudenberg Medical. Cleanroom molding and assembly VEM can offer services in design assistance, prototyping, production mold making, injection molding in a white room or cleanroom, component sourcing, assembly, testing and packaging. Both inside and outside our cleanroom, we have room and equipment for various sizes of injection machines. Our cleanroom is built in a modular way, which allows us to be flexible and increase size as quickly as possible according to customers’ needs. Three of our global locations include high-tech tool shops, which enable us to quickly develop molds from prototype to production, as well as perform maintenance and repairs. Manufacturing transfer Thinking about moving production out of China? Facing rising costs and import/export issues with medical device production in China, VEM helps clients with an expedited manufacturing transfer of plastic injection molding and assembly projects from China to Thailand with their supply chains intact. VEM has been manufacturing in Thailand for 13 years and medical device manufacturing project transfers are among our most popular services and can be set up and running within just a few weeks. For more information, read our case study under the ‘White Papers’ tab on this page. Medical plastics and device manufacturing in Thailand Manufacturing in Southeast Asia offers a lower price point, more flexibility, and a faster time to market than domestic manufacturing can provide. For more than 13 years, VEM has operated its wholly-owned manufacturing operation in Rayong, Thailand. The largest port in Thailand, Laem Chabang Port, is just a 30-minute drive from our facility and many large medical device and healthcare manufacturers are located nearby. There is an undeniable reason behind the growth of the medical device manufacturing industry in Thailand. The location is strategically attractive due to a skilled and educated workforce, a welcoming and open economy with a stable government, quality infrastructure, lower cost of labour and reduced import taxes, and ease of import/export of raw materials and components. About VEM Medical VEM currently has five manufacturing facilities across Asia, Europe and Central America. Our facility in Thailand is ISO 13485:2016 certified and specialises in medical device production and assembly. Our tool shop in Shenzhen, China, manufactures molds for our medical device clients worldwide.
VEM’s in-house medical molds have helped us develop medical parts for molding and assembly for years. Our fully owned mold manufacturer consistently gives us complete control over molds and materials, allowing for optimal quality control. Optimisation, rigorous quality testing, and a professional approach to solving problems have always been our key approaches. Our molds are used worldwide by large medical companies, including Danaher Corporation, Cepheid, Foamtec Medical and Freudenberg Medical. Cleanroom molding and assembly VEM can offer services in design assistance, prototyping, production mold making, injection molding in a white room or cleanroom, component sourcing, assembly, testing and packaging. Both inside and outside our cleanroom, we have room and equipment for various sizes of injection machines. Our cleanroom is built in a modular way, which allows us to be flexible and increase size as quickly as possible according to customers’ needs. Three of our global locations include high-tech tool shops, which enable us to quickly develop molds from prototype to production, as well as perform maintenance and repairs. Manufacturing transfer Thinking about moving production out of China? Facing rising costs and import/export issues with medical device production in China, VEM helps clients with an expedited manufacturing transfer of plastic injection molding and assembly projects from China to Thailand with their supply chains intact. VEM has been manufacturing in Thailand for 13 years and medical device manufacturing project transfers are among our most popular services and can be set up and running within just a few weeks. For more information, read our case study under the ‘White Papers’ tab on this page. Medical plastics and device manufacturing in Thailand Manufacturing in Southeast Asia offers a lower price point, more flexibility, and a faster time to market than domestic manufacturing can provide. For more than 13 years, VEM has operated its wholly-owned manufacturing operation in Rayong, Thailand. The largest port in Thailand, Laem Chabang Port, is just a 30-minute drive from our facility and many large medical device and healthcare manufacturers are located nearby. There is an undeniable reason behind the growth of the medical device manufacturing industry in Thailand. The location is strategically attractive due to a skilled and educated workforce, a welcoming and open economy with a stable government, quality infrastructure, lower cost of labour and reduced import taxes, and ease of import/export of raw materials and components. About VEM Medical VEM currently has five manufacturing facilities across Asia, Europe and Central America. Our facility in Thailand is ISO 13485:2016 certified and specialises in medical device production and assembly. Our tool shop in Shenzhen, China, manufactures molds for our medical device clients worldwide.
Paul Runyan, VP Sales & Marketing at Accumold, says. “The critical importance is to integrate seasoned micro-optic suppliers like Accumold into the design phase as early as possible. It’s our partnership approach, versus a mere vendor relationship, that enables the fusion of specialized micro manufacturing and micro-optic expertise into your projects for solutions that are both efficient and economical. We are able to produce micro-optic marvels such as 250-micron fiber optic lenses, parallel arrays, demux devices, and diffractive lenses, enhanced by our experience in molding attenuated resins and applying coatings like IR, AR, and reflective layers onto plastic substrates. The complex demands of crafting micro-sized optical couplers, embedding lenses into housings, replicating lens profiles to a quarter wave accuracy, and achieving lens surface finishes within 50 angstroms are why we have dedicated tooling specialists to ensure your light transmission projects are flawlessly executed.”
Subscribe to Medical Design & Outsourcing. Bookmark, share and interact with the leading medical design engineering magazine today.
Three of our global locations include high-tech tool shops, which enable us to quickly develop molds from prototype to production, as well as perform maintenance and repairs. Manufacturing transfer Thinking about moving production out of China? Facing rising costs and import/export issues with medical device production in China, VEM helps clients with an expedited manufacturing transfer of plastic injection molding and assembly projects from China to Thailand with their supply chains intact. VEM has been manufacturing in Thailand for 13 years and medical device manufacturing project transfers are among our most popular services and can be set up and running within just a few weeks. For more information, read our case study under the ‘White Papers’ tab on this page. Medical plastics and device manufacturing in Thailand Manufacturing in Southeast Asia offers a lower price point, more flexibility, and a faster time to market than domestic manufacturing can provide. For more than 13 years, VEM has operated its wholly-owned manufacturing operation in Rayong, Thailand. The largest port in Thailand, Laem Chabang Port, is just a 30-minute drive from our facility and many large medical device and healthcare manufacturers are located nearby. There is an undeniable reason behind the growth of the medical device manufacturing industry in Thailand. The location is strategically attractive due to a skilled and educated workforce, a welcoming and open economy with a stable government, quality infrastructure, lower cost of labour and reduced import taxes, and ease of import/export of raw materials and components. About VEM Medical VEM currently has five manufacturing facilities across Asia, Europe and Central America. Our facility in Thailand is ISO 13485:2016 certified and specialises in medical device production and assembly. Our tool shop in Shenzhen, China, manufactures molds for our medical device clients worldwide.
Beyond tooling intricacies, the meticulous nature of the molding process, precise metrology, and automated post-molding assembly are essential to maintaining the integrity of micro-optics from conception to final assembly. Partnering with Accumold means engaging with a leader in the field, a company whose three-decade legacy in micro molding brings unparalleled experience and the capability to scale production to meet any demand. This reassurance of stability and efficiency translates into cost-effective solutions for Accumold’s customers.
VEM Group, a global tooling and molding provider to the medical device and consumer goods industry, will exhibit at the upcoming trade fair Design & Manufacturing West, also known as MD&M West. This event is the leading U.S. tradeshow and conference for the medical device manufacturing industry which takes place August 10-12 in Anaheim, California. VEM will be exhibiting in Hall D, booth 3327.
Accumold’s history in the micro optics marketplace spans decades, and the company has proudly partnered with leading SMEs and major international corporations to craft ground-breaking products that push the boundaries of innovation. In the photonics sector where supreme precision is not just desired but required, Accumold has cemented its role as the micro molding authority for OEMs seeking to create components that are not only complex and diminutive but also precise, timely, and cost-effective.
VEM Medical is a full-service contract manufacturing organisation for medical plastics, devices and components. We partner with medical device companies across three continents to provide plastic injection molding, in-house tooling, prototyping, assembly, testing and more. A highly experienced team, best-in-class equipment and rigorous quality control help us deliver solutions for challenging medical tooling and molding applications. For more than 20 years, VEM has focused on customer satisfaction as our highest priority. Our clients range from small innovative companies to large multinational original equipment manufacturers (OEMs). Our production facility is certified according to ISO 9001 and ISO 13485, with a Class 100,000 (ISO 8) cleanroom. VEM Medical can produce small and precise molded parts for medical devices. Our medical assembly line is inspected by a stringent quality control team. A static 2K mixer for medical applications. VEM Medical can produce injection-molded parts for medical sub-assembly. Each of our manufactured devices must pass a testing procedure specified by the customer. Medical inserts can be molded in our clean room. We produce parts through complex medical tooling. Our team sub-assembles a tube connection for a breathing device. Many different parts can be moulded in our Class 100,000 cleanroom. Medical plastics and device manufacturing VEM is an integrated partner from design assistance and design for manufacturing to finished device production and assembly. Our fully owned tool shops, cleanroom production, assembly and sub-assembly capabilities provide rich opportunities to partner with us, no matter which stage your product is in. Our experienced team uses the newest equipment and automation, including brands such as Arburg, Toshiba, GF, Hexagon and Makino. Being transparent when producing parts is what makes us stand out. Not only will we set up the production in accordance with all your needs but we can also help to improve process quality and reduce cycle times. In-house medical tooling VEM’s in-house medical molds have helped us develop medical parts for molding and assembly for years. Our fully owned mold manufacturer consistently gives us complete control over molds and materials, allowing for optimal quality control. Optimisation, rigorous quality testing, and a professional approach to solving problems have always been our key approaches. Our molds are used worldwide by large medical companies, including Danaher Corporation, Cepheid, Foamtec Medical and Freudenberg Medical. Cleanroom molding and assembly VEM can offer services in design assistance, prototyping, production mold making, injection molding in a white room or cleanroom, component sourcing, assembly, testing and packaging. Both inside and outside our cleanroom, we have room and equipment for various sizes of injection machines. Our cleanroom is built in a modular way, which allows us to be flexible and increase size as quickly as possible according to customers’ needs. Three of our global locations include high-tech tool shops, which enable us to quickly develop molds from prototype to production, as well as perform maintenance and repairs. Manufacturing transfer Thinking about moving production out of China? Facing rising costs and import/export issues with medical device production in China, VEM helps clients with an expedited manufacturing transfer of plastic injection molding and assembly projects from China to Thailand with their supply chains intact. VEM has been manufacturing in Thailand for 13 years and medical device manufacturing project transfers are among our most popular services and can be set up and running within just a few weeks. For more information, read our case study under the ‘White Papers’ tab on this page. Medical plastics and device manufacturing in Thailand Manufacturing in Southeast Asia offers a lower price point, more flexibility, and a faster time to market than domestic manufacturing can provide. For more than 13 years, VEM has operated its wholly-owned manufacturing operation in Rayong, Thailand. The largest port in Thailand, Laem Chabang Port, is just a 30-minute drive from our facility and many large medical device and healthcare manufacturers are located nearby. There is an undeniable reason behind the growth of the medical device manufacturing industry in Thailand. The location is strategically attractive due to a skilled and educated workforce, a welcoming and open economy with a stable government, quality infrastructure, lower cost of labour and reduced import taxes, and ease of import/export of raw materials and components. About VEM Medical VEM currently has five manufacturing facilities across Asia, Europe and Central America. Our facility in Thailand is ISO 13485:2016 certified and specialises in medical device production and assembly. Our tool shop in Shenzhen, China, manufactures molds for our medical device clients worldwide.
VEM can offer services in design assistance, prototyping, production mold making, injection molding in a white room or cleanroom, component sourcing, assembly, testing and packaging. Both inside and outside our cleanroom, we have room and equipment for various sizes of injection machines. Our cleanroom is built in a modular way, which allows us to be flexible and increase size as quickly as possible according to customers’ needs. Three of our global locations include high-tech tool shops, which enable us to quickly develop molds from prototype to production, as well as perform maintenance and repairs. Manufacturing transfer Thinking about moving production out of China? Facing rising costs and import/export issues with medical device production in China, VEM helps clients with an expedited manufacturing transfer of plastic injection molding and assembly projects from China to Thailand with their supply chains intact. VEM has been manufacturing in Thailand for 13 years and medical device manufacturing project transfers are among our most popular services and can be set up and running within just a few weeks. For more information, read our case study under the ‘White Papers’ tab on this page. Medical plastics and device manufacturing in Thailand Manufacturing in Southeast Asia offers a lower price point, more flexibility, and a faster time to market than domestic manufacturing can provide. For more than 13 years, VEM has operated its wholly-owned manufacturing operation in Rayong, Thailand. The largest port in Thailand, Laem Chabang Port, is just a 30-minute drive from our facility and many large medical device and healthcare manufacturers are located nearby. There is an undeniable reason behind the growth of the medical device manufacturing industry in Thailand. The location is strategically attractive due to a skilled and educated workforce, a welcoming and open economy with a stable government, quality infrastructure, lower cost of labour and reduced import taxes, and ease of import/export of raw materials and components. About VEM Medical VEM currently has five manufacturing facilities across Asia, Europe and Central America. Our facility in Thailand is ISO 13485:2016 certified and specialises in medical device production and assembly. Our tool shop in Shenzhen, China, manufactures molds for our medical device clients worldwide.
VEM Medical provides plastic injection molding, in-house tooling, prototyping, assembly, testing and more for medical devices, plastics and components.
Both inside and outside our cleanroom, we have room and equipment for various sizes of injection machines. Our cleanroom is built in a modular way, which allows us to be flexible and increase size as quickly as possible according to customers’ needs. Three of our global locations include high-tech tool shops, which enable us to quickly develop molds from prototype to production, as well as perform maintenance and repairs. Manufacturing transfer Thinking about moving production out of China? Facing rising costs and import/export issues with medical device production in China, VEM helps clients with an expedited manufacturing transfer of plastic injection molding and assembly projects from China to Thailand with their supply chains intact. VEM has been manufacturing in Thailand for 13 years and medical device manufacturing project transfers are among our most popular services and can be set up and running within just a few weeks. For more information, read our case study under the ‘White Papers’ tab on this page. Medical plastics and device manufacturing in Thailand Manufacturing in Southeast Asia offers a lower price point, more flexibility, and a faster time to market than domestic manufacturing can provide. For more than 13 years, VEM has operated its wholly-owned manufacturing operation in Rayong, Thailand. The largest port in Thailand, Laem Chabang Port, is just a 30-minute drive from our facility and many large medical device and healthcare manufacturers are located nearby. There is an undeniable reason behind the growth of the medical device manufacturing industry in Thailand. The location is strategically attractive due to a skilled and educated workforce, a welcoming and open economy with a stable government, quality infrastructure, lower cost of labour and reduced import taxes, and ease of import/export of raw materials and components. About VEM Medical VEM currently has five manufacturing facilities across Asia, Europe and Central America. Our facility in Thailand is ISO 13485:2016 certified and specialises in medical device production and assembly. Our tool shop in Shenzhen, China, manufactures molds for our medical device clients worldwide.
Thinking about moving production out of China? Facing rising costs and import/export issues with medical device production in China, VEM helps clients with an expedited manufacturing transfer of plastic injection molding and assembly projects from China to Thailand with their supply chains intact. VEM has been manufacturing in Thailand for 13 years and medical device manufacturing project transfers are among our most popular services and can be set up and running within just a few weeks. For more information, read our case study under the ‘White Papers’ tab on this page. Medical plastics and device manufacturing in Thailand Manufacturing in Southeast Asia offers a lower price point, more flexibility, and a faster time to market than domestic manufacturing can provide. For more than 13 years, VEM has operated its wholly-owned manufacturing operation in Rayong, Thailand. The largest port in Thailand, Laem Chabang Port, is just a 30-minute drive from our facility and many large medical device and healthcare manufacturers are located nearby. There is an undeniable reason behind the growth of the medical device manufacturing industry in Thailand. The location is strategically attractive due to a skilled and educated workforce, a welcoming and open economy with a stable government, quality infrastructure, lower cost of labour and reduced import taxes, and ease of import/export of raw materials and components. About VEM Medical VEM currently has five manufacturing facilities across Asia, Europe and Central America. Our facility in Thailand is ISO 13485:2016 certified and specialises in medical device production and assembly. Our tool shop in Shenzhen, China, manufactures molds for our medical device clients worldwide.
VEM is an integrated partner from design assistance and design for manufacturing to finished device production and assembly. Our fully owned tool shops, cleanroom production, assembly and sub-assembly capabilities provide rich opportunities to partner with us, no matter which stage your product is in. Our experienced team uses the newest equipment and automation, including brands such as Arburg, Toshiba, GF, Hexagon and Makino. Being transparent when producing parts is what makes us stand out. Not only will we set up the production in accordance with all your needs but we can also help to improve process quality and reduce cycle times. In-house medical tooling VEM’s in-house medical molds have helped us develop medical parts for molding and assembly for years. Our fully owned mold manufacturer consistently gives us complete control over molds and materials, allowing for optimal quality control. Optimisation, rigorous quality testing, and a professional approach to solving problems have always been our key approaches. Our molds are used worldwide by large medical companies, including Danaher Corporation, Cepheid, Foamtec Medical and Freudenberg Medical. Cleanroom molding and assembly VEM can offer services in design assistance, prototyping, production mold making, injection molding in a white room or cleanroom, component sourcing, assembly, testing and packaging. Both inside and outside our cleanroom, we have room and equipment for various sizes of injection machines. Our cleanroom is built in a modular way, which allows us to be flexible and increase size as quickly as possible according to customers’ needs. Three of our global locations include high-tech tool shops, which enable us to quickly develop molds from prototype to production, as well as perform maintenance and repairs. Manufacturing transfer Thinking about moving production out of China? Facing rising costs and import/export issues with medical device production in China, VEM helps clients with an expedited manufacturing transfer of plastic injection molding and assembly projects from China to Thailand with their supply chains intact. VEM has been manufacturing in Thailand for 13 years and medical device manufacturing project transfers are among our most popular services and can be set up and running within just a few weeks. For more information, read our case study under the ‘White Papers’ tab on this page. Medical plastics and device manufacturing in Thailand Manufacturing in Southeast Asia offers a lower price point, more flexibility, and a faster time to market than domestic manufacturing can provide. For more than 13 years, VEM has operated its wholly-owned manufacturing operation in Rayong, Thailand. The largest port in Thailand, Laem Chabang Port, is just a 30-minute drive from our facility and many large medical device and healthcare manufacturers are located nearby. There is an undeniable reason behind the growth of the medical device manufacturing industry in Thailand. The location is strategically attractive due to a skilled and educated workforce, a welcoming and open economy with a stable government, quality infrastructure, lower cost of labour and reduced import taxes, and ease of import/export of raw materials and components. About VEM Medical VEM currently has five manufacturing facilities across Asia, Europe and Central America. Our facility in Thailand is ISO 13485:2016 certified and specialises in medical device production and assembly. Our tool shop in Shenzhen, China, manufactures molds for our medical device clients worldwide.
The Medical Device Business Journal. MassDevice is the leading medical device news business journal telling the stories of the devices that save lives.
Optimisation, rigorous quality testing, and a professional approach to solving problems have always been our key approaches. Our molds are used worldwide by large medical companies, including Danaher Corporation, Cepheid, Foamtec Medical and Freudenberg Medical. Cleanroom molding and assembly VEM can offer services in design assistance, prototyping, production mold making, injection molding in a white room or cleanroom, component sourcing, assembly, testing and packaging. Both inside and outside our cleanroom, we have room and equipment for various sizes of injection machines. Our cleanroom is built in a modular way, which allows us to be flexible and increase size as quickly as possible according to customers’ needs. Three of our global locations include high-tech tool shops, which enable us to quickly develop molds from prototype to production, as well as perform maintenance and repairs. Manufacturing transfer Thinking about moving production out of China? Facing rising costs and import/export issues with medical device production in China, VEM helps clients with an expedited manufacturing transfer of plastic injection molding and assembly projects from China to Thailand with their supply chains intact. VEM has been manufacturing in Thailand for 13 years and medical device manufacturing project transfers are among our most popular services and can be set up and running within just a few weeks. For more information, read our case study under the ‘White Papers’ tab on this page. Medical plastics and device manufacturing in Thailand Manufacturing in Southeast Asia offers a lower price point, more flexibility, and a faster time to market than domestic manufacturing can provide. For more than 13 years, VEM has operated its wholly-owned manufacturing operation in Rayong, Thailand. The largest port in Thailand, Laem Chabang Port, is just a 30-minute drive from our facility and many large medical device and healthcare manufacturers are located nearby. There is an undeniable reason behind the growth of the medical device manufacturing industry in Thailand. The location is strategically attractive due to a skilled and educated workforce, a welcoming and open economy with a stable government, quality infrastructure, lower cost of labour and reduced import taxes, and ease of import/export of raw materials and components. About VEM Medical VEM currently has five manufacturing facilities across Asia, Europe and Central America. Our facility in Thailand is ISO 13485:2016 certified and specialises in medical device production and assembly. Our tool shop in Shenzhen, China, manufactures molds for our medical device clients worldwide.
The opinions expressed in this news release are the author’s only and do not necessarily reflect those of Medical Design & Outsourcing or its employees.
VEM currently has five manufacturing facilities across Asia, Europe and Central America. Our facility in Thailand is ISO 13485:2016 certified and specialises in medical device production and assembly. Our tool shop in Shenzhen, China, manufactures molds for our medical device clients worldwide.
There is an undeniable reason behind the growth of the medical device manufacturing industry in Thailand. The location is strategically attractive due to a skilled and educated workforce, a welcoming and open economy with a stable government, quality infrastructure, lower cost of labour and reduced import taxes, and ease of import/export of raw materials and components. About VEM Medical VEM currently has five manufacturing facilities across Asia, Europe and Central America. Our facility in Thailand is ISO 13485:2016 certified and specialises in medical device production and assembly. Our tool shop in Shenzhen, China, manufactures molds for our medical device clients worldwide.
VEM Group, a global tooling and molding provider to the medical device and consumer goods industry, has been selected by Manufacturing Outlook magazine a Top 10 Injection Molding Service Companies 2021.
VEM Group, a global tooling and molding provider to the medical device, automotive, and consumer goods industry, has expanded operations into Eastern Europe. The wholly owned manufacturing plant is located in Plovdiv, Bulgaria, which is the cultural capital and second largest city in Bulgaria.
For more than 20 years, VEM has focused on customer satisfaction as our highest priority. Our clients range from small innovative companies to large multinational original equipment manufacturers (OEMs). Our production facility is certified according to ISO 9001 and ISO 13485, with a Class 100,000 (ISO 8) cleanroom. VEM Medical can produce small and precise molded parts for medical devices. Our medical assembly line is inspected by a stringent quality control team. A static 2K mixer for medical applications. VEM Medical can produce injection-molded parts for medical sub-assembly. Each of our manufactured devices must pass a testing procedure specified by the customer. Medical inserts can be molded in our clean room. We produce parts through complex medical tooling. Our team sub-assembles a tube connection for a breathing device. Many different parts can be moulded in our Class 100,000 cleanroom. Medical plastics and device manufacturing VEM is an integrated partner from design assistance and design for manufacturing to finished device production and assembly. Our fully owned tool shops, cleanroom production, assembly and sub-assembly capabilities provide rich opportunities to partner with us, no matter which stage your product is in. Our experienced team uses the newest equipment and automation, including brands such as Arburg, Toshiba, GF, Hexagon and Makino. Being transparent when producing parts is what makes us stand out. Not only will we set up the production in accordance with all your needs but we can also help to improve process quality and reduce cycle times. In-house medical tooling VEM’s in-house medical molds have helped us develop medical parts for molding and assembly for years. Our fully owned mold manufacturer consistently gives us complete control over molds and materials, allowing for optimal quality control. Optimisation, rigorous quality testing, and a professional approach to solving problems have always been our key approaches. Our molds are used worldwide by large medical companies, including Danaher Corporation, Cepheid, Foamtec Medical and Freudenberg Medical. Cleanroom molding and assembly VEM can offer services in design assistance, prototyping, production mold making, injection molding in a white room or cleanroom, component sourcing, assembly, testing and packaging. Both inside and outside our cleanroom, we have room and equipment for various sizes of injection machines. Our cleanroom is built in a modular way, which allows us to be flexible and increase size as quickly as possible according to customers’ needs. Three of our global locations include high-tech tool shops, which enable us to quickly develop molds from prototype to production, as well as perform maintenance and repairs. Manufacturing transfer Thinking about moving production out of China? Facing rising costs and import/export issues with medical device production in China, VEM helps clients with an expedited manufacturing transfer of plastic injection molding and assembly projects from China to Thailand with their supply chains intact. VEM has been manufacturing in Thailand for 13 years and medical device manufacturing project transfers are among our most popular services and can be set up and running within just a few weeks. For more information, read our case study under the ‘White Papers’ tab on this page. Medical plastics and device manufacturing in Thailand Manufacturing in Southeast Asia offers a lower price point, more flexibility, and a faster time to market than domestic manufacturing can provide. For more than 13 years, VEM has operated its wholly-owned manufacturing operation in Rayong, Thailand. The largest port in Thailand, Laem Chabang Port, is just a 30-minute drive from our facility and many large medical device and healthcare manufacturers are located nearby. There is an undeniable reason behind the growth of the medical device manufacturing industry in Thailand. The location is strategically attractive due to a skilled and educated workforce, a welcoming and open economy with a stable government, quality infrastructure, lower cost of labour and reduced import taxes, and ease of import/export of raw materials and components. About VEM Medical VEM currently has five manufacturing facilities across Asia, Europe and Central America. Our facility in Thailand is ISO 13485:2016 certified and specialises in medical device production and assembly. Our tool shop in Shenzhen, China, manufactures molds for our medical device clients worldwide.
Manufacturing in Southeast Asia offers a lower price point, more flexibility, and a faster time to market than domestic manufacturing can provide. For more than 13 years, VEM has operated its wholly-owned manufacturing operation in Rayong, Thailand. The largest port in Thailand, Laem Chabang Port, is just a 30-minute drive from our facility and many large medical device and healthcare manufacturers are located nearby. There is an undeniable reason behind the growth of the medical device manufacturing industry in Thailand. The location is strategically attractive due to a skilled and educated workforce, a welcoming and open economy with a stable government, quality infrastructure, lower cost of labour and reduced import taxes, and ease of import/export of raw materials and components. About VEM Medical VEM currently has five manufacturing facilities across Asia, Europe and Central America. Our facility in Thailand is ISO 13485:2016 certified and specialises in medical device production and assembly. Our tool shop in Shenzhen, China, manufactures molds for our medical device clients worldwide.
Facing rising costs and import/export issues with medical device production in China, VEM Medical helps clients with an expedited manufacturing transfer of plastic injection molding and assembly projects from China, where costs continue to rise, to Thailand with supply chains intact.
GETTING A QUOTE WITH LK-MOULD IS FREE AND SIMPLE.
FIND MORE OF OUR SERVICES:
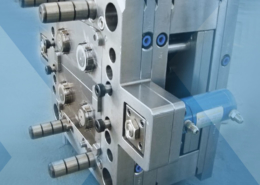
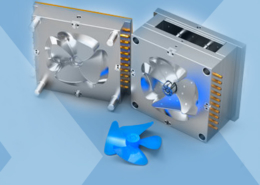
Plastic Molding

Rapid Prototyping
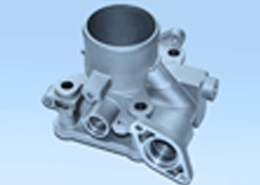
Pressure Die Casting
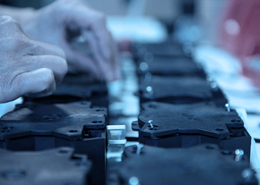
Parts Assembly
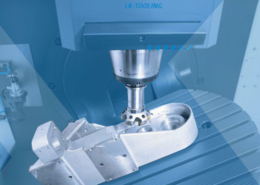