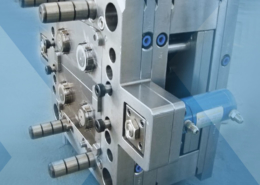
Exploring Plastic Molding: Revolutionizing Manufacturing Processes
Author:gly Date: 2024-06-08
Plastic molding, a cornerstone of modern manufacturing, encapsulates the fusion of technology, innovation, and precision engineering. From intricate components of consumer electronics to robust automotive parts, plastic molding permeates every facet of our lives. In this comprehensive exploration, we delve into the intricacies of plastic molding, unraveling its methodologies, applications, and future prospects.
Understanding Plastic Molding
Plastic molding, an indispensable technique, involves shaping molten plastic into desired forms through various processes. The journey of plastic molding begins with the meticulous design of molds, which serve as the blueprint for the final product. These molds, crafted with utmost precision, dictate the intricacies of the molded parts.
The Injection Molding Process
Injection molding stands as the epitome of precision engineering in plastic molding. This process entails injecting molten plastic into a meticulously crafted mold under high pressure. The molten plastic fills every nook and cranny of the mold, ensuring the replication of intricate details with unparalleled accuracy.
Precision and Efficiency
The hallmark of injection molding lies in its ability to produce large quantities of identical parts with minimal variance. The automated nature of the process, coupled with advanced control systems, guarantees consistency and efficiency, making it the preferred choice for mass production.
Applications Across Industries
The versatility of plastic molding transcends industry boundaries, catering to diverse needs across various sectors.
Automotive Sector
In the automotive sector, plastic molding revolutionized the manufacturing of components, ranging from interior trims to intricate engine parts. The lightweight yet durable nature of plastic molded components enhances fuel efficiency without compromising on safety or performance.
Advancements in Material Science
The advent of advanced materials, such as reinforced plastics and thermoplastic composites, further amplifies the potential of plastic molding in the automotive sector. These materials offer superior strength-to-weight ratios and thermal stability, enabling the production of components capable of withstanding extreme conditions.
Environmental Considerations
Despite its unparalleled utility, plastic molding grapples with environmental concerns, primarily revolving around plastic waste and sustainability.
Recycling Initiatives
Efforts to mitigate the environmental impact of plastic molding encompass initiatives aimed at promoting recycling and embracing sustainable materials. The integration of recycled plastics into the molding process not only reduces waste but also minimizes the reliance on virgin materials, thereby conserving natural resources.
Bioplastics: A Sustainable Alternative
The emergence of bioplastics, derived from renewable sources such as corn starch and sugarcane, presents a promising avenue for sustainable plastic molding. Bioplastics offer comparable performance to conventional plastics while mitigating the ecological footprint associated with traditional petroleum-based polymers.
Technological Advancements
The relentless march of technology continues to redefine the landscape of plastic molding, ushering in an era of unprecedented possibilities.
Additive Manufacturing: A Paradigm Shift
Additive manufacturing, colloquially known as 3D printing, disrupts traditional paradigms of plastic molding by enabling the fabrication of complex geometries with unparalleled precision. This revolutionary approach transcends the constraints of traditional molding processes, empowering designers to unleash their creativity without compromising on manufacturability.
Customization at Scale
The inherent flexibility of additive manufacturing facilitates on-demand production of customized parts, catering to individual preferences and niche markets. This democratization of manufacturing heralds a new era of personalized products, fundamentally altering the dynamics of consumer engagement and market dynamics.
Conclusion
In conclusion, plastic molding stands as a testament to human ingenuity, transforming raw materials into intricate creations that shape our daily lives. From its humble beginnings to its present-day prominence, plastic molding continues to evolve, driven by innovation and technological advancement. As we navigate the complexities of a rapidly changing world, embracing sustainable practices and harnessing the potential of emerging technologies will be paramount in shaping the future of plastic molding.
Through collaborative efforts and unwavering dedication, we can propel plastic molding towards a sustainable and prosperous future, where efficiency converges with environmental stewardship, and innovation knows no bounds. As stewards of this transformative technology, let us embark on a journey of exploration and discovery, unlocking new frontiers and forging a path towards a brighter tomorrow.
GETTING A QUOTE WITH LK-MOULD IS FREE AND SIMPLE.
FIND MORE OF OUR SERVICES:
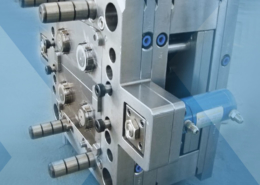
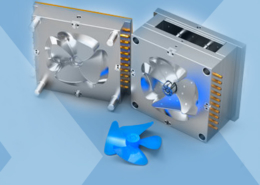
Plastic Molding

Rapid Prototyping
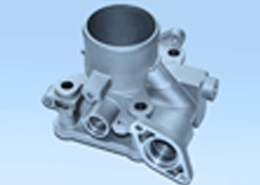
Pressure Die Casting
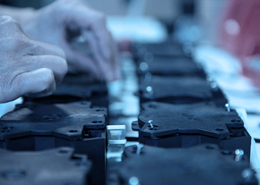
Parts Assembly
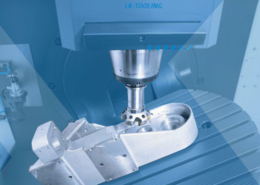