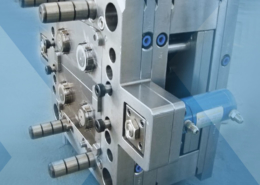
Plastic Molding for Wire 1 2: Revolutionizing Wire Management
Author:gly Date: 2024-06-08
Wire management is an integral aspect of various industries, from electronics to automotive. Ensuring the proper organization and protection of wires is crucial for maintaining functionality and safety. In recent years, plastic molding has emerged as a game-changer in wire management, offering versatility, durability, and cost-effectiveness. This article delves into the innovative realm of plastic molding for wire management, exploring its applications, benefits, and future prospects.
1. Evolution of Wire Management
Wire management has evolved significantly over the years, from simple bundling techniques to sophisticated molding solutions. Traditional methods often involved the use of zip ties, clips, and adhesive tapes, which provided basic organization but lacked durability and aesthetics. With the advent of plastic molding technologies, wire management has undergone a paradigm shift, allowing for precise customization and seamless integration into various applications.
Plastic molding enables the creation of intricate wire harnesses and enclosures that conform to specific shapes and sizes. This level of precision not only enhances the aesthetic appeal but also optimizes space utilization and facilitates efficient wire routing. Moreover, molded plastic components offer superior protection against environmental factors such as moisture, heat, and vibration, ensuring long-term reliability in diverse operating conditions.
2. Applications in Various Industries
The versatility of plastic molding for wire management has spurred its adoption across a wide range of industries. In the automotive sector, molded wire harnesses play a crucial role in connecting electrical components and systems, contributing to vehicle performance and safety. The seamless integration of wires within molded enclosures minimizes the risk of abrasion, short circuits, and electrical interference, thereby enhancing reliability and longevity.
In the electronics industry, plastic molding enables the creation of compact and lightweight wire assemblies for consumer electronics, telecommunications, and computing devices. Miniaturization is a key trend driving innovation in this sector, and molded wire solutions offer the perfect combination of space-saving design and robust functionality. From smartphones to IoT devices, plastic molding for wire management caters to the evolving needs of modern technology.
3. Advantages of Plastic Molding
Plastic molding offers numerous advantages over traditional wire management methods, making it the preferred choice for many manufacturers. Firstly, molded plastic components are highly customizable, allowing for complex geometries and integrated features such as strain relief and mounting points. This versatility streamlines the assembly process and reduces labor costs, contributing to overall efficiency and productivity.
Furthermore, plastic molding enables the use of various materials with specific properties tailored to the application requirements. From thermoplastics to elastomers, manufacturers can select the most suitable materials for durability, flexibility, and thermal performance. Additionally, molded wire harnesses are inherently resistant to corrosion, chemicals, and UV radiation, ensuring reliable operation in harsh environments.
4. Future Directions and Challenges
Looking ahead, the future of plastic molding for wire management holds immense potential for innovation and advancement. As industries continue to embrace digitalization and automation, there is a growing demand for smart and interconnected systems that rely on seamless wire integration. Plastic molding technologies are poised to meet these evolving needs by enabling the creation of intelligent wire harnesses with embedded sensors, connectors, and communication interfaces.
However, despite its many benefits, plastic molding for wire management also presents certain challenges, such as material selection, design complexity, and sustainability concerns. Addressing these challenges requires collaboration across the supply chain, from material suppliers to equipment manufacturers and end-users. By leveraging advanced materials, design tools, and manufacturing processes, stakeholders can overcome these obstacles and unlock new opportunities for innovation.
Conclusion
In conclusion, plastic molding has revolutionized wire management by offering unparalleled versatility, durability, and customization options. From automotive to electronics, molded wire solutions have become indispensable for ensuring efficient wire routing, protection, and integration. As industries continue to evolve and embrace digital transformation, plastic molding technologies will play a pivotal role in enabling the next generation of smart and interconnected systems. By embracing innovation and collaboration, stakeholders can harness the full potential of plastic molding for wire management and drive future advancements in the field.
GETTING A QUOTE WITH LK-MOULD IS FREE AND SIMPLE.
FIND MORE OF OUR SERVICES:
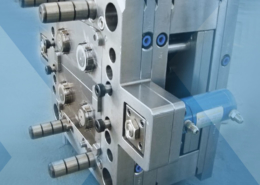
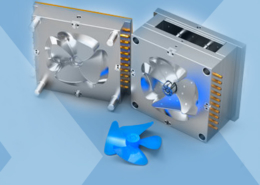
Plastic Molding

Rapid Prototyping
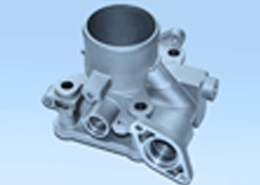
Pressure Die Casting
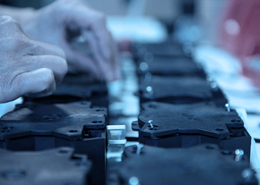
Parts Assembly
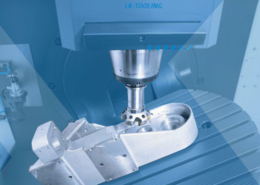