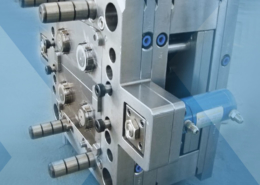
Simulating Two-Shot Molding: How Does the First Shot Affect Overall Part
Author:gly Date: 2024-09-30
Imprint Cookie-Manager About Media Subscription cancellation Privacy General Terms and Conditions Help AI-Guidelines
The breakthrough is gaining traction. Stirn informs us that tests and trials are already lined up in North and South America with more to follow.
If we think about new production designs, then our strategic partner, Synventive Moulding Solutions, is an innovative producer and developer of hot runners, always involved at an early stage in order to develop process-oriented, reliable and functionally efficient hot runner systems. Synventive knows our structures and the importance of safe production sequences in our manufacturing process. We use Synventive Plug'n'Play hot runner systems, which we have delivered pre-assembled, interlaced and wired. Not only do we appreciate Synventive's functional and process-oriented hot runner technology, but we also appreciate the fast response times and the company's service, should there be a technical query or an unscheduled maintenance task.”
We only have a partial reserve stock for a maximum of two days. In order to be able to safely run this idea, you need suppliers who are absolutely reliable strategic partners, who know exactly in which structures and in which process sequences thinking and manufacturing takes place. Hot-runner technology is of crucial and decisive importance in our process sequences. This is because for modules with over one million units per year and corresponding guarantees for injection-moulding tools made to our customers, quality and a long life-cycle for the components must be of prime importance.
Sybridge’s Matt Little and Milacron’s Andy Stirn pause at NPE2024 with the innovative pail and the injection molding system in the background. RICK LINGLE
Milacron and partners perfect the injection molding of a precise layer of recycled content — mechanical or advanced processes — to sustainably boost the eco-footprint of 5-gal plastic pails.
The plastic industry seeks sustainability opportunities throughout the breadth of the market from automotive to medical to packaging. It’s in the latter market where the depth of that commitment was exemplified in the plastic pail category at NPE2024 where Milacron exhibited an M-Series Model 1070 injection molding system capable of adding a core layer of recycled content.
In so doing, EKT was able to make the customer's previously developed design in co-operation with the long-term business partner, Richter Werkzeugbau GmbH, and the machine manufacturer's components, a reality. The SOP took place in June 2017 after around two years of development time.
The development supports legislation that sets single-use plastic targets and recycled content goals for brand owners, which stateside is most notably forthcoming CA SB 54.
Volker Scheffels explains the process stages as follows: “We want to keep the flow of materials, storage and administration as low as possible to guarantee the best economic viability. We produce modules in the machine's cycle and finalise them on the machine itself, place them in the shipping crate and load them onto the truck. These are the shortest possible processing routes. That does mean, however, if we have any disruptions as part of the production process, we will immediately have bottle-necks, since we no longer deliver from stock.
The at-show encapsulated post-consumer recycle (PCR) layer was 46%, according to Stirn, “but we go up to 50% with complete control of where the recycle layer is located, whether inner, middle, or outer layer.”
So as to avoid shrinkage in the cooling phase during the conversion process, EKT has developed a technical solution for the entire injection moulding process on a single 2K injection moulding machine. When constructing the tool, a solution was subsequently sought, which would allow the soft component to be simultaneously injection-moulded on both sides of the pre-prepared hard component. EKT has solved this task together with its partners in terms of manufacturing technology by furnishing the H-component with bypass channels during its construction, which allowed both the front and rear side of the hard component to be injection-moulded with the soft component. The cycle times remain extremely short as the feature component is completed directly on the machine itself before going straight to shipping for the customer.
The inner and outer layers are made of high-density polyethylene. The advanced recycling material demonstrated on May 6 was provided by LyondellBasell. Shell Polymers provides the virgin HDPE.
SyBridge’s Matt Little, business development manager, life sciences and consumer, sees plastic handles replacing metal to simplify and maximize plastic pail recyclability.
Participating in the demonstration this year were a collaboration of NPE partner companies Beck Automation, KW Plastics, LyondellBasell, MCC Verstraete, Mold Masters, Shell Polymers, and SyBridge Technologies.
The encapsulating concept was introduced at NPE2015 for a single-cavity model, but the 2024 difference is that there is a higher output “double-cavity processing with precise control of the layer,” explains Andy Stirn, general manager advanced systems. “And that is now applicable for chemically recycled content along with mechanically recycled content.”
This portal is a brand of Vogel Communications Group. You will find our complete range of products and services on www.vogel.com
EKT has been able to solve a particularly difficult task with its partners. This task was preceded by a thought of rationalisation at Miele. The essence of the thought was to make a single functional component out of several individual components from the air duct in the rear wall of a tumble dryer, consisting of a hard component and soft component on both sides in the form of sealing rings, which were to replace earlier retrofitted sealing designs.
The cycle times should be kept extremely short during the 2-K injection-moulding process. For economic reasons, on the one hand, and to guarantee the high-quality requirements for the component in terms of accuracy of dimensions and process-stable reproducibility, on the other. The initial solution design envisaged producing the functional component on two separate injection-moulding machines. The produced H-component would be removed from the tool as part of the injection-moulding process and inserted into the second tool of a second injection-moulding machine, in which the component could then be extrusion-coated from both sides with the soft component.
The front and rear side of the air duct component with hard and soft Miele washer-drier component. (Source: Synventive)
Sustainably speaking, other pails pale in comparison. But that’s not the ultimate solution because there’s more pail sustainability ahead.
Rick Lingle is Senior Technical Editor, Packaging Digest and PlasticsToday. He’s been a packaging media journalist since 1985 specializing in food, beverage and plastic markets. He has a chemistry degree from Clarke College and has worked in food industry R&D for Standard Brands/Nabisco and the R.T. French Co. Reach him at [email protected] or 630-481-1426.
GETTING A QUOTE WITH LK-MOULD IS FREE AND SIMPLE.
FIND MORE OF OUR SERVICES:
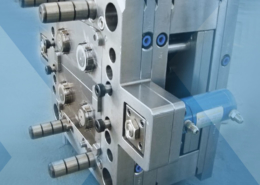
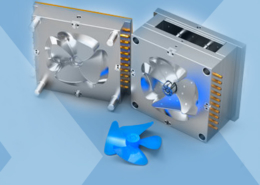
Plastic Molding

Rapid Prototyping
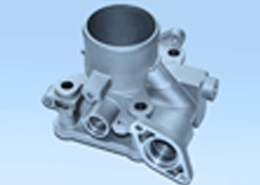
Pressure Die Casting
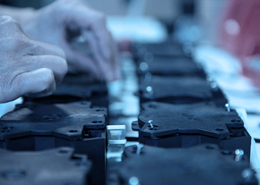
Parts Assembly
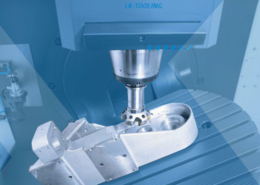