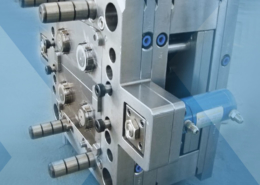
Sanyo Seisakusho: Pioneering excellence in mold design and manufacturing - plast
Author:gly Date: 2024-09-30
The system works by allowing customers to choose which Pantone number they require or provide a sample part that can be scanned and colour matched, when a part design is ready. A material is then selected from the 13 available resin combinations, and PolyOne’s Pinpoint system is able to create a liquid formula that is dispensed and mixed before moving to the injection moulding press. The material is then fed through the doser and injection moulded. This results in customers receiving their custom colours much faster than traditional methods e.g. days compared to weeks.
"Implant manufacturers were missing a PEEK material that fuses with bone cells and, thus, accelerates healing," said Marc Knebel, Head of the Medical Systems Market Segment at Evonik. "We are closing this gap in the market with VESTAKEEP Fusion and offering an alternative to titanium, stainless steel, or cobalt-chromium implants."
“With development cycles shrinking to meet the market demand for increased customisation, this is yet another tool to help our customers accelerate product launches and streamline supply chains.”
A collaboration between Evonik and Swiss plastics processor Samaplast results in an alternative to titanium, stainless steel, and cobalt-chromium implants.
Evonik is also developing a 3D-printable VESTAKEEP Fusion filament that can be processed via additive manufacturing using fused filament fabrication technology.
Matthews continued: “All of these new capabilities are things that our customers have wanted for a while, so we’re excited to finally be able to offer it to them while still delivering finished parts at industry leading speeds.”
Joel Matthews, global product manager at Protolabs said: “These new colour matching capabilities are a huge leap for the manufacturing industry, one stacked with benefits for our customers who are developing highly tailored products.
In order to further its position as a single source supplier from prototyping to production Protolabs has added new injection moulding capabilities. Therefore, along with custom colour matching it has launched multiple secondary processes and finishing options to support the full manufacturing process. These processes include things such as pad printing and laser engraving, threaded inserts, mould texturing for mould-tech finishes, and part assembly.
The device PolyOne Pinpoint Express Colour and Dosing System features 3M precision dispensing and dosing technologies, allowing Protolabs to develop custom colours on site. As a result this reduces the time it takes to mould short-run plastic parts in precise colours.
With VESTAKEEP Fusion, Evonik is introducing a new product line of next-generation PEEK-based implant materials that accelerate bone fusion and convalescence. In vitro studies document a more than 30% increase in cell attachment and cell proliferation, according to Evonik. In preclinical tests, histological examination reveals a dense network of newly formed osteoblasts at the bone-implant interface. Bone histo-morphometry shows an approximately twofold increase in bone apposition. Moreover, pull-out tests demonstrate a more than twofold increase in implant fixation, said the company.
Initially offered in granule form and as semi-finished products, VESTAKEEP Fusion can be milled, compression molded, extruded, and injection molded, said Evonik. The compound was optimized for injection molding in close cooperation with Samaplast AG.
Andy Homyk, senior engineer at medtech firm HemoSonics added: “Speed and flexibility, being able to deploy different manufacturing options, and a commitment to customer service are the main reasons we use Protolabs.”
"We tested VESTAKEEP Fusion on injection molding machines in the cleanroom and found that it was very easy to process," said Samaplast CEO Stefan Okle in a prepared statement. "Thanks to the excellent exchange with Evonik, we were able to produce a prototype within 10 days." Previously, tool development alone had taken eight to 10 weeks. With rapid prototyping, this process can be shortened considerably.
Until now, it has been virtually impossible to manufacture implants from polymer compounds with bioactive particles by injection molding, because a thin polymer layer usually forms on the surface, preventing the implant from growing in, explained Evonik in a press release. VESTAKEEP Fusion's specially configured microparticles and their homogeneous distribution, however, allow the formation of functional biphasic calcium phosphate (BCP) additives on the surface of injection-molded components. The additives allow bone cells to adhere to the implant more quickly and promote osteo-integration between the bone and implant.
German chemicals company Evonik and Swiss plastics processor Samaplast have collaborated in the development of an osteo-conductive PEEK-based material compatible with injection molding. Spinal implant prototypes have been molded to illustrate the processing properties of the new high-performance polymer, VESTAKEEP Fusion.
To demonstrate the medical potential of the technology, Evonik and Samaplast have produced prototypes of intervertebral implants, known as cages or spacers, which are used to fill the disc space in the spine following its removal due to disc degeneration. "We have produced a cage that contains all the details, such as serrations, threads, and apertures, that are relevant for spinal implants," explained Okle.
Thanks to the design freedom afforded by injection molding, VESTAKEEP Fusion–based cages can be tailored to patient-specific anatomies and different surgical techniques. The cage models show the design diversity in the interlocks and in the cavities for ossification. In addition, the design facilitates instrument guidance during surgery and enables minimally invasive, patient-friendly surgical techniques.
GETTING A QUOTE WITH LK-MOULD IS FREE AND SIMPLE.
FIND MORE OF OUR SERVICES:
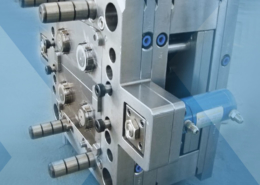
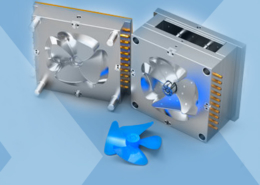
Plastic Molding

Rapid Prototyping
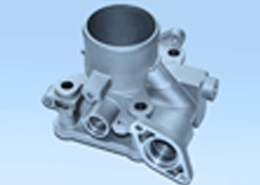
Pressure Die Casting
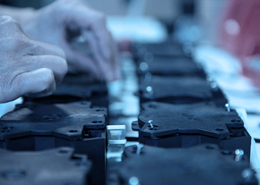
Parts Assembly
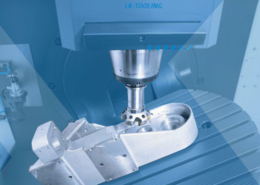