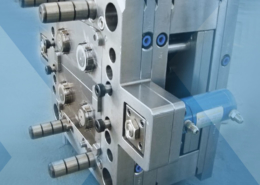
Sanyo Seisakusho: Pioneering excellence in mold design and manufacturing - plast
Author:gly Date: 2024-09-30
We are always moving, but not just because there is a business there. Besides looking at new tools, one of our targets is also to put forth an effort in following up on all the tools that we have sent in the last 20 years. Tools have a lifespan of 10 to 15 years, so we do everything we can to be responsible, and we get paid for that. There is a time limit for our voluntary services, then we move on. We do what we need to do to keep our name and remain where we are.
This month’s resin pricing report includes PT’s quarterly check-in on select engineering resins, including nylon 6 and 66.
Plastics Technology covers technical and business Information for Plastics Processors in Injection Molding, Extrusion, Blow Molding, Plastic Additives, Compounding, Plastic Materials, and Resin Pricing. About Us
When I was in junior high, I moved to the US, and I did not speak a single word of English. I started from scratch. Although I was like a baby learning English, I managed to be able to speak in English. Though I am not perfect, I successfully attended school, made a lot of friends, worked and enjoyed my stay in the US. When my family decided for me to join a company in the US and not come back to Japan, I started my career there. Back then, we only had around 20 people working in the mold division of our company in the US. As I walked into the shop, I had to do literally everything, even cleaning. Nevertheless, that was a great experience for me because, in a short period, everyone was quickly teaching me everything. I was able to give support to our company's tool shop, and I was able to run machines and make data on my own as it had a smaller capacity. The younger people who come into our company here in Japan are usually assigned to a specific area and gain expertise in machining, finishing or designing. They will not get generalized training, which we consider a big problem. Given how I grew up and my experience, I know the shop, what the tools are and what the future is supposed to be. I strive to share that with our people all the time.
Thousands of people visit our Supplier Guide every day to source equipment and materials. Get in front of them with a free company profile.
Plastics Technology’s Tech Days is back! Every Tuesday in October, a series of five online presentations will be given by industry supplier around the following topics: Injection Molding — New Technologies, Efficiencies Film Extrusion — New Technologies, Efficiencies Upstream/Downstream Operations Injection Molding — Sustainability Extrusion — Compounding Coming out of NPE2024, PT identified a variety of topics, technologies and trends that are driving and shaping the evolution of plastic products manufacturing — from recycling/recyclability and energy optimization to AI-based process control and automation implementation. PT Tech Days is designed to provide a robust, curated, accessible platform through which plastics professionals can explore these trends, have direct access to subject-matter experts and develop strategies for applying solutions in their operations.
This Knowledge Center provides an overview of the considerations needed to understand the purchase, operation, and maintenance of a process cooling system.
We have to keep our core business going. We always have a QCD problem or cost issues globally. However, my philosophy is that business will come as long as we keep our healthy relationships with our customers harmonious, and not be too selfish. I might be too Japanese in saying that. We have bad and good times, as well as times with busy and less workload.
NPE2024: Absolute Haitian says Generation 5 of the servo-hydraulic Haitian and electric Zhafir machines lines emphasize efficiency, performance and intelligence.
An integral supplier in the effort to fast-track COVID-19 vaccine deployment, Retractable Technologies turned to Arburg and its PressurePilot technology to help deliver more than 500 million syringes during the pandemic.
I was lucky to get an early look at many of the past half-century’s exciting developments in plastics. Here’s a selection.
How do you envision your international development, and what kind of tools or partnerships are you looking to create to become globalized?
Take a deep dive into all of the various aspects of part quoting to ensure you’ve got all the bases—as in costs—covered before preparing your customer’s quote for services.
TMW is a specialist producer of plastic-injection molds for automobile parts such as instrument panels and bumpers. Founded in 1949, the Japanese company supplies a host of major vehicle manufacturers both at home and abroad.
NPE2024: Chen Hsong has three injection molding machines in its booth, including 2-platen, hybrid and a next-generation line with improved platen and toggle design.
Join this webinar to explore the transformative benefits of retrofitting your existing injection molding machines (IMMs). Engel will guide you through upgrading your equipment to enhance monitoring, control and adaptability — all while integrating digital technologies. You'll learn about the latest trends in IMM retrofitting (including Euromap interfaces and plasticizing retrofits) and discover how to future-proof your machines for a competitive edge. With insights from industry experts, it'll walk you through the decision-making process, ensuring you make informed choices that drive your business forward. Agenda: Maximize the value of your current IMMs through strategic retrofitting Learn how to integrate digital technologies to enhance monitoring and control Explore the benefits of Euromap interfaces and plasticizing retrofits Understand how retrofitting can help meet new product demands and improve adaptability Discover how Engel can support your retrofitting needs, from free consultations to execution
NPE2024: The injection molding machine suppliers has four machines running in its booth molding automotive, medical and consumer goods applications.
NPE2024: Arburg’s debut of the 310-ton Allrounder 720 E Golden Electric extends the tonnage range of the electric series and marks the first global press premiere outside of Germany.
In this collection of articles, two of the industry’s foremost authorities on screw design — Jim Frankand and Mark Spalding — offer their sage advice on screw design...what works, what doesn’t, and what to look for when things start going wrong.
Join KraussMaffei for an insightful webinar designed for industry professionals, engineers and anyone interested in the manufacturing processes of PVC pipes. This session will provide a comprehensive understanding of the technology behind the production of high-quality PVC pipes: from raw material preparation to final product testing. Agenda: Introduction to PVC extrusion: overview of the basic principles of PVC pipe extrusion — including the process of melting and shaping PVC resin into pipe forms Equipment and machinery: detailed explanation of the key equipment involved — such as extruders, dies and cooling systems — and their roles in the extrusion process Process parameters: insight into the critical process parameters like temperature, pressure and cooling rates that influence the quality and consistency of the final PVC pipes Energy efficiency: examination of ways to save material and energy use when extruding PVC pipe products
Any molder will tell you there’s a difference in working with electric vs. hydraulic drives. Servohydraulic is still hydraulic; a hybrid machine is something different. Imprecise use of terms causes needless confusion.
NPE2024: A slimmed-down version of Engel’s all-electric, e-mac injection molding machine is among eight displays, which also include LSR micromolding, quick mold changes and a cube mold.
Core Technology Molding turned to Mold-Masters E-Multi auxiliary injection unit to help it win a job and dramatically change its process.
For us, continuing as Yokozuna means we have to consolidate a big number of tools with the projects they are giving to toolmakers. Our capacity cannot be calculated by just our facility. We have to share our engineering method, know-how, timekeeping, and even our software with our supply chain partners for them to be able to build our tools to our standards. Keeping that supply chain is very difficult especially during years when business is slow. We tried to stay a Yokozuna by gathering a lot of business at our facility here to supply to our partners. The benefit for us is being able to stay a Yokozuna, and for them, they get more business.
technotrans says climate protection, energy efficiency and customization will be key discussion topics at PTXPO as it displays its protemp flow 6 ultrasonic eco and the teco cs 90t 9.1 TCUs.
NPE2024: Sumitomo SHI Demag’s show focus is on the application of all-electric injection molding machine technology for a variety of markets and components.
In this three-part collection, veteran molder and moldmaker Jim Fattori brings to bear his 40+ years of on-the-job experience and provides molders his “from the trenches” perspective on on the why, where and how of venting injection molds. Take the trial-and-error out of the molding venting process.
Across all process types, sustainability was a big theme at NPE2024. But there was plenty to see in automation and artificial intelligence as well.
Sustainability continues to dominate new additives technology, but upping performance is also evident. Most of the new additives have been targeted to commodity resins and particularly polyolefins.
What is your manufacturing philosophy or take on monozukuri? In your opinion, what sets your company and Japan apart from its regional manufacturing competitors?
After working for about five years in America, I came to Japan. My uncle, the former president of the company, asked me where I wanted to go and what I wanted to do. I told him that I wanted to work in the shop. I did not care, even if that meant a two to five year commitment. Most employees who are working, managing and serving as officers in the company (shop) now are those I worked with in the shop twenty years ago. They know who I am in and out, what I do and what I expect. I do not want to be Tatematsu. Here at our company, there are six Tatematsu-san (sons) working, including my father. I am the head of this company, but we have a holding company. My father has two brothers, and each of them has a son. One of my cousins just went back to the US. He is going to be 40 next year, so he is very young to be taking over the entire US operation. Despite that, I want him to take on that challenge. I also took over this company at 40. Before, you would have to be 50 or 55, maybe even close to 60, to become the president of the company. That happens in chushokigyos all the time, as there is always the difficulty of passing things down. At our company, we are trying to lower that age required to become an officer, so we now have several younger leaders and managers. Our officers are in their mid-30s to 70s, and we consider them experienced. Still, we welcome inexperienced employees who display an understanding of who we are, what we do and what our company is expecting. If they have the capability and willingness to put their time into our business, I am also willing to put them up with our upper management. A bad thing about Japanese culture is that once you go up to higher management, you never go down. That is where you get stuck. At the same time, many younger people cannot go up. Therefore, we ask them to step down, which is a mindset that I have set up in our company 10 years ago before I became president.
Most of Japan’s economy is held by monozukuri- something built. Whether small or large and global or domestic, everything starts from manufacturing and goes into the service. We understand that we have competitors in China or Korea in our tooling business. I think each company’s philosophy depends on whether they consider them competitors or partners. For our part, we think of them as our partners, and we utilize and leverage their capacity.Many in our industry would always try to compete with China and Korea or ASEAN like Vietnam, Indonesia or Thailand. On the contrary, TMW looks at them as partners in order to stay in global business.
Formnext Chicago is an industrial additive manufacturing expo taking place April 8-10, 2025 at McCormick Place in Chicago, Illinois. Formnext Chicago is the second in a series of Formnext events in the U.S. being produced by Mesago Messe Frankfurt, AMT – The Association For Manufacturing Technology, and Gardner Business Media (our publisher).
Sodick Plustech’s VR-G and MS-G2 Series both utilize the company’s proprietary V-Line technology, separating plasticizing and injection functions, and have upgraded displays, energy efficiency, response time and more.
Imagine we come back in two years for your 75th anniversary and have this interview all over again. What would you like to tell us? What are your dreams for this company, and what goals would you like to have accomplished by then?
Companies that have been able to succeed and have that kind of status for so long have accumulated expertise passed down to the next generations. However, the transfer of that technical expertise to the younger generation has become an growing problem, especially for chushokigyos. What has your experience been in that respect? What has been the main challenge of Japan’s demographic decline for your company?
Multiple speakers at Molding 2023 will address the ways simulation can impact material substitution decisions, process profitability and simplification of mold design.
Across the show, sustainability ruled in new materials technology, from polyolefins and engineering resins to biobased materials.
NPE2024: Arburg says the Allrounder 720 E injection molding machine premiere highlights the importance of the show and market.
While the melting process does not provide perfect mixing, this study shows that mixing is indeed initiated during melting.
Formerly a showroom for early-aughts-era Van Dorn hydraulics, the newest additions to Drummond Industries’ transforming fleet are all-electric Niigata injection molding machines.
Gifted with extraordinary technical know how and an authoritative yet plain English writing style, in this collection of articles Fattori offers his insights on a variety of molding-related topics that are bound to make your days on the production floor go a little bit better.
Although it is a supply chain in which there is a business between us, we call them partners, never suppliers. We make tools every day, used for applications such as instrument panels and bumpers. Considering the capacity of our headquarters plant in Inazawa, we cannot make 20 big tools in this facility each month. We are limited to seven or eight tools a month.
August 29-30 in Minneapolis all things injection molding and moldmaking will be happening at the Hyatt Regency — check out who’s speaking on what topics today.
Mike Sepe has authored more than 25 ANTEC papers and more than 250 articles illustrating the importance of this interdisciplanary approach. In this collection, we present some of his best work during the years he has been contributing for Plastics Technology Magazine.
Can you elaborate on your relationship with your overseas partners? What do they gain from you, and what do you gain from them?
We do everything we can to maximize our capacity. In that situation, the business forecast in Japan does not look very good. Even though I talk about good things and our history, no one knows what is going to happen next year. It is possible for us to go down. To prevent that, we need to keep growing. Having said that, I am not trying to grow our business. Rather, I am trying to stay in business. My idea is to keep this legendary company from my grandfather, who started it. I changed the name of the company in 2018 because I wanted to take Tatematsu out of the company's name. Tatematsu Mold Works not only has over 65 years of experience but is also trusted by our customers, and everyone knows us. It was on our 60th anniversary when I changed the name. I asked my employees, "How long is it going to take us to go over that 60 years with a new plan, a new logo and a new name?". I would like my CEOs and officers to be able to go up to be in management, and to eventually take over my position. I made the decision to have others step down. Now, they can make the decision of making me step down.
Boy will debut three new models in its Electric series of machines, which feature a redesigned and more compact drive and inverter technology.
Exhibitors and presenters at the plastics show emphasized 3D printing as a complement and aid to more traditional production processes.
In the last few years, we had a difficult time, just like everybody else globally. We most likely open our demands to our customers so that they could support us. At the end of the day, we are always supporting customers however they need us. We tell our customers exactly what is going on, even about the transfer of tools or parts. We try to be honest, and we are only trying to profit from what we make. That philosophy, which stays in our partnerships, counts in order to gain their trust.
The Korean maker of injection molding machines featured eight machines in its nearly 14,000-square-foot booth with additional presses at Yushin and Incoe’s booths, as it targets 20% market share.
In 2018, we changed our name from Tatematsu Mold Works to TMW. Tatematsu Mold Works was one of the biggest brands in the tooling business in Japan, especially in automotive. Everybody knows us, but we do not know everybody. Thanks to the valuable efforts of my grandfather - the former president and the company's former employees, we were considered one of the top and largest tool-making companies in Japan. We have that background that allows us to go anywhere in the world and be viewed as a good company to collaborate with in Japan, especially being a chushokigyo (SME). Partnerships are maybe the most important value and the core of our business.
Discover how artifical intelligence is revolutionizing plastics processing. Hear from industry experts on the future impact of AI on your operations and envision a fully interconnected plant.
Eden Manufacturing was founded on a vision of vertical integration, adding advanced injection molding capabilities to a base of precision moldmaking and more recently bringing Swiss-type machining capabilities in-house.
A bad thing about chushokigyos is that we sometimes time to preserve that legend too much. In other words, Japanese people cannot be too dry. In the business field, that is referred to as ninjo, a human connection deep within one’s heart. The upper management will try to save even the worst employee. They never fire someone, and that happens in our company. My grandfather hated to lay off employees. Throughout our 75 years of history, we have not done any layoffs in TMW, even though our business was doing badly after Lehman or 10 years before that. However, we did it in the subsidiary I managed in Malaysia. The first thing I had to do was to lay off around 20 members, which was a very tough decision for me, but it was an important learning experience. My mindset changed when I came back. Today, I am asking all my employees to input whatever they can to be in this company; otherwise, I will have to make that difficult decision. Everybody, including the banks and consultants, tells me to downsize the company due to high wage costs. However, I respond, “So what? That only means we have to make more.” Keeping our employees means allowing them to continue making a living. Whenever we are in a bad situation, I go up in front of everybody and say, “Hey, I need to cut your wage down. Help me for a year or six months.” They always agree each time I do that because they know that the company has their interests at heart.
Second quarter started with price hikes in PE and the four volume engineering resins, but relatively stable pricing was largely expected by the quarter’s end.
Join Wittmann for an engaging webinar on the transformative impact of manufacturing execution systems (MES) in the plastic injection molding industry. Discover how MES enhances production efficiency, quality control and real-time monitoring while also reducing downtime. It will explore the integration of MES with existing systems, emphasizing compliance and traceability for automotive and medical sectors. Learn about the latest advancements in IoT and AI technologies and how they drive innovation and continuous improvement in MES. Agenda: Overview of MES benefits What is MES? Definition, role and brief history Historical perspective and evolution Longevity and analytics Connectivity: importance, standards and integration Advantages of MES: efficiency, real-time data, traceability and cost savings Emerging technologies: IoT and AI in MES
The aim of this presentation is to guide you through the factors and the numbers that will help you determine if a robot is a smart investment for your application. Agenda: Why are you considering automation? What problems are you trying to solve? How and why automation can help Crunch the numbers and determine the ROI
While prices moved up for three of the five commodity resins, there was potential for a flat trajectory for the rest of the third quarter.
In a time where sustainability is no longer just a buzzword, the food and beverage packaging industry is required to be at the forefront of this innovation. By adopting circular packaging processes and solutions, producers can meet regulatory requirements while also satisfying consumer demand and enhancing brand reputation. Join Husky to learn more about the broader implications of the circular economy — as well as how leading brands are leveraging this opportunity to reduce costs, increase design flexibility and boost product differentiation. Agenda: The cost and operational benefits of embracing circularity Key materials in circular packaging — including rPET and emerging bioplastics How to design a circular food and beverage package Strategies for selecting sustainable closures to future-proof packaging solutions Optimization and streamlining of production processes for enhanced efficiency How Husky Technologies can enable your sustainable success
Mold maintenance is critical, and with this collection of content we’ve bundled some of the very best advice we’ve published on repairing, maintaining, evaluating and even hanging molds on injection molding machines.
We need the capacity of our subsidiaries in China and Korea as well as our many partners outside in order to keep our business like Yokozuna (sumo champion). There are only a few firms left that are considered Yokozuna tooling companies, which means being independent.
Say “manufacturing automation” and thoughts immediately go to the shop floor and specialized production equipment, robotics and material handling systems. But there is another realm of possible automation — the front office.
Successfully starting or restarting an injection molding machine is less about ticking boxes on a rote checklist and more about individually assessing each processing scenario and its unique variables.
In the history of your company, perhaps the biggest transformation in the automotive industry is the switch to EV and FCV. What has the impact been for you? How are you adapting to the external changes in the automotive sector?
Join Engel in exploring the future of battery molding technology. Discover advancements in thermoplastic composites for battery housings, innovative automation solutions and the latest in large-tonnage equipment designed for e-mobility — all with a focus on cost-efficient solutions. Agenda: Learn about cutting-edge thermoplastic composites for durable, sustainable and cost-efficient battery housings Explore advanced automation concepts for efficient and scalable production See the latest large-tonnage equipment and technology innovations for e-mobility solutions
While the major correction in PP prices was finally underway, generally stable pricing was anticipated for the other four commodity resins.
The Coronavirus pandemic has been incredibly disruptive, especially in terms of supply chain management and supply chain partnerships for your builders and supporters. How did you react to those disruptions?
The Plastics Industry Association (PLASTICS) has released final figures for NPE2024: The Plastics Show (May 6-10; Orlando) that officially make it the largest ever NPE in several key metrics.
After successfully introducing a combined conference for moldmakers and injection molders in 2022, Plastics Technology and MoldMaking Technology are once again joining forces for a tooling/molding two-for-one.
The Worldfolio provides business, industrial and financial news about global economies, with a focus on understanding them from within.
While prices moved up for three of the five commodity resins, there was potential for a flat trajectory for the rest of the third quarter.
Right after the Lehman shock, the economy struggled, and our industry crashed pretty badly. I am proud to say that while we were very negative for a long time, but we were able to manage and keep going. We tried to keep the cash flowing. Despite being negative, we were able to keep our business and our promise to our grandfather. He always says that all our employees are our family. Our company's philosophy states that everybody eats the same meal, and we eat the same rice from the same rice cooker. We want to keep that philosophy as our tradition. In fact, we have employed people who cook for all of us in our cafeteria every day, and we used to serve dinner too. Back when my grandfather started the business, he asked my grandmother to cook daily for everybody. She was actually running the lathe too. She had my father on her back while working, running the lathe and working in the kitchen. That was how our family started our business 74 (forty) years ago.
Introduced by Zeiger and Spark Industries at the PTXPO, the nozzle is designed for maximum heat transfer and uniformity with a continuous taper for self cleaning.
In view of the tooling business being a complicated and old-type style business that keeps lots of traditions and standards, we want to be more easygoing, fashionable and creative.. That is why having younger people in management is advantageous because they have more ideas. The older ones usually keep things ordinary, fixed and old school. I asked all the former management people to step down. To do that, I needed a trigger. I do not think some of the old-school things have changed, but we have project management, which is unusual for tooling companies in Japan. Project management is common in the US and Europe. On the contrary, it is more army-style in Japan.
No other toolmakers do some of the things we do because of our history. The only thing I ask those who want to join our company is whether they have the passion to work with us or not. Of course, they say they do on the interview. I never say, "I am going to make you into this kind of person, or I am going to groom you into being this person in our company." I always encourage them to try it. If you do not work out, then you walk out. I try to be honest with them.
In this collection, which is part one of a series representing some of John’s finest work, we present you with five articles that we think you will refer to time and again as you look to solve problems, cut cycle times and improve the quality of the parts you mold.
In order to change that, we have to physically change the way we run the tooling and processes. It took me about a year to continually discuss with the management how we can transform our styles and daily processes at our workplace. A year ago, we came up with new project management, and we also brought in a new management that runs daily. The older management keeps watch over the new management, but they are usually under it, as they are ordered to work and do whatever they need to do to provide support. We did that for a year and a half before totally switching over. Meanwhile, the wages remained the same.
In this collection of content, we provide expert advice on welding from some of the leading authorities in the field, with tips on such matters as controls, as well as insights on how to solve common problems in welding.
We do have that problem, but what helps us is our style of being an cool tool maker, which we want to be our core style. We tried to commercialize and showcase that to make our employees feel that we are doing something cool. The TMW red logo that we have been using for over 65 years was designed by my grandfather. In 2018, I designed the black logo to separate our tooling business from our venture or start-up businesses. We also pursue start-up businesses internally by taking ideas from our employees. On every occasion, I am upfront in providing any support toward that endeavor, like considering agreements. Ideally, though, we try to make our business target and end up in the tooling business. All our departments are structured to connect back to our tooling business. Our core business is the mold tooling business, which we are good at and famous for because we have been doing that for more than 60 years.
Despite price increase nominations going into second quarter, it appeared there was potential for generally flat pricing with the exception of a major downward correction for PP.
I do not send Christmas cards, but I call to say, "We apologize that we have not had a business deal in a year. This is how Japan's economy is now." We let them know, and they usually understand. They understand the good and bad times.
Processors with sustainability goals or mandates have a number of ways to reach their goals. Biopolymers are among them.
Mixed in among thought leaders from leading suppliers to injection molders and mold makers at the 2023 Molding and MoldMaking conferences will be molders and toolmakers themselves.
When, how, what and why to automate — leading robotics suppliers and forward-thinking moldmakers will share their insights on automating manufacturing at collocated event.
Resin drying is a crucial, but often-misunderstood area. This collection includes details on why and what you need to dry, how to specify a dryer, and best practices.
Learn about sustainable scrap reprocessing—this resource offers a deep dive into everything from granulator types and options, to service tips, videos and technical articles.
We have numerous internal mechanisms to make that possible. Likewise, we have the know-how as we have already experienced building big tools that have a lot of space. We know that we have many ways to make different shapes inside the tool. Small tools that require small injection machines have very limited space, and we cannot really do so much. The durability of big-sized tools is very hard, so we have many things that we can do inside. The airbag tear cut was one of the ideas that came from that.
Ultradent's entry of its Umbrella cheek retractor took home the awards for Technical Sophistication and Achievement in Economics and Efficiency at PTXPO.
Additive technology creates air pockets in film during orientation, cutting down on the amount of resin needed while boosting opacity, mechanical properties and recyclability.
Everybody says that it is a threat, and that is true for someone in our shoes. Plastic injection tooling businesses significantly deal with automotive, but we also do other things. We feel that the automotive side of the market is an opportunity because we can try more different ways of approaching injection tooling. That is why I have a hot runner system business. I have key factor components that need to be in the tooling. We try to work on injection businesses at the same time so that we can gather more information and collaborate back into tooling.
Our core business will not change so much. Whether it is EV, FCV or gasoline engines, there is always interior and exterior. It is not a motorcycle, so it needs a body. Also, it does not really matter if it is simplified or electrical. Except, the design of the many things we build here will have to change because buttons will be changed to touch panels. The air conditioning, radio or other components do not have to be separated, which makes things simpler. However, the design and shape are going to be more complicated than they used to be.
GETTING A QUOTE WITH LK-MOULD IS FREE AND SIMPLE.
FIND MORE OF OUR SERVICES:
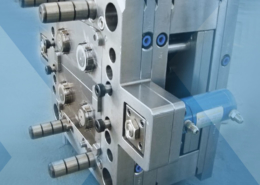
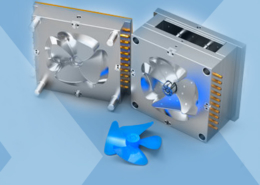
Plastic Molding

Rapid Prototyping
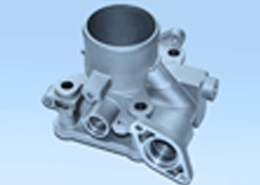
Pressure Die Casting
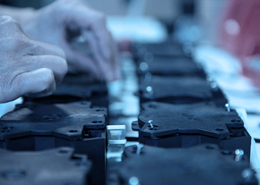
Parts Assembly
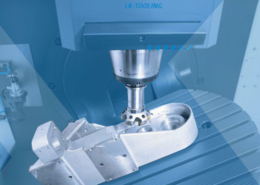