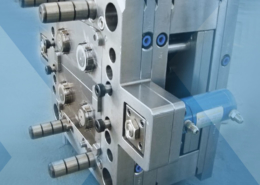
Reusable popcorn bucket with peelable in-mold labels is a hit with Chilean
Author:gly Date: 2024-09-30
Ultradent's entry of its Umbrella cheek retractor took home the awards for Technical Sophistication and Achievement in Economics and Efficiency at PTXPO.
Making deburring part of the process. Hobby knives are among the most frequently used tools at the shop, Mr. Marchand says. Whether for reasons of aesthetics or function, most parts machined at East Coast Precision require smooth surfaces. Unfortunately, conventional deburring methods like tumbling tend to be ineffective, because dangling plastic tends to “flap around” rather than break, he says. Mechanical deburring can also damage more sensitive plastics. As a result, some parts leave no other option but to spend hours whittling away manually at residual chads of material.
The shop’s staffers rely on patience, experience and a steady hand to machine geometry almost too small to see on equipment that would be just as suitable for more conventionally sized parts. Here, Richie Fernandez, machinist, indicates a drill on the shop’s Hardinge SV 200 lathe.
In any case, one reason the grinder gets so much use is that tool designs that work well in other materials don’t necessarily translate to plastics. This also leads the shop to prioritize simple geometry in its standard cutters, Mr. Marchand says. For instance, chip-breakers are a no-no because they can exacerbate the tendency of soft, stringy material to stretch and twist as it peels away from the stock. All of the shop’s milling and turning tools also tend to have a neutral rake angle. Keeping the edge as perpendicular to the material as possible helps prevent flexing the plastic too far away from the cut and encouraging longer spirals, as might happen with a negative rake, or drawing it inward and gumming up the cutting zone, as might happen with a positive rake. In a turning operation, either scenario could also result in unwanted taper and poor surface finish, Mr. Marchand says. With few exceptions (Fiberglass, for instance), the shop never buys coated tools because there’s simply no advantage, he adds, explaining that plastics aren’t hard enough on tools or machines to justify it.
FABTECH 2024 will be held October 15-17, 2024, in Orlando, Florida, at the Orange County Convention Center. FABTECH provides a convenient ‘one-stop shop’ venue where you can meet with world-class suppliers, discover innovative solutions, and find the tools to improve productivity and increase profits. There is no better opportunity to network, share knowledge and explore the latest technology, all here in one place. Future U.S. Show Dates and Locations 2025 – September 8-11 at McCormick Place in Chicago, IL 2026 – October 21-23 at Las Vegas Convention Center in Las Vegas, NV 2027 – September 13-16 at McCormick Place in Chicago, IL
True to the adjective in its name, Dynamic Group has been characterized by constant change, activity and progress over its nearly five decades as a medical molder and moldmaker.
Standards for surface finishes and profiles are not static; they change as technology changes or new processes come along that need to be considered.
During the technical presentations, Gerhard Dimmler, Engel’s senior vice president of R&D, addressed just why the company got involved in this new technology: “The processing is very close to the injection molding process—it’s a useful complement to our core technologies,” he says. Additionally, it provides the company with additional market access.
Heidenhain and Acu-Rite Solutions are offering several hands-on experiences at their booth this year, as well as internal components that reduce energy use.
Legacy Precision Molds takes us on a tour of their moldbuilding facility. They've recently implemented two automated 5-axis cells for metal and graphite machining that run lights out during nights and weekends.
In this three-part collection, veteran molder and moldmaker Jim Fattori brings to bear his 40+ years of on-the-job experience and provides molders his “from the trenches” perspective on on the why, where and how of venting injection molds. Take the trial-and-error out of the molding venting process.
Misapplication of these important CNC features will result in wasted time, wasted or duplicated effort and/or wasted material.
Achieve higher metal removal rates and enhanced predictability with ISCAR’s advanced high-feed milling tools — optimized for today’s competitive global market.
Leveraging the right tool geometry. Many of the aforementioned “cleanup cutters” are standard offerings that have undergone modifications on the shop’s Deckel S0 benchtop tool grinder. However, imparting chamfers and other geometries that help remove burrs is just one of many purposes of customizing tool geometry. For instance, a standard, 0.019-inch grooving tool might be ground to 0.011 inch to cut a narrower channel, or part of a boring bar might be ground away to avoid interference with a taper at the back of a blind hole. Of course, other geometries are far more involved, and Mr. Marchand says those provide a competitive edge.
In the late 1800s, a new technology — Swiss-type machines — emerged to serve Switzerland’s growing watchmaking industry. Today, Swiss-machined parts are ubiquitous, and there’s a good reason for that: No other machining technology can produce tiny, complex components more efficiently or at higher quality.
While prices moved up for three of the five commodity resins, there was potential for a flat trajectory for the rest of the third quarter.
Keeping clean. Finally, Mr. Marchand emphasizes that keeping coolant filtered and machines clean is imperative when working with small parts. The component on page 93, for instance, proved difficult to distinguish from chips caught by the fine-screen parts catcher on one of the Swiss-types. One step taken as a result is to make it more of a priority to routinely ensure coolant is filtered and machines are clean. That boils down to basic housekeeping. As such, it serves as evidence that even the deepest expertise goes only so far in ensuring chip control (or achieving any other goal, for that matter) without common sense and a solid grasp of fundamentals.
Effective team collaboration is a critical component of success in today’s manufacturing world. With cloud-based technologies that make it easy for team members to brainstorm and problem solve remotely from various locations, design-to-manufacturing processes can become faster and more efficient. This webinar will demonstrate how fully integrated CAM software can be utilized with 3DExperience SolidWorks in a seamless work environment to accelerate product development. Agenda: See how HCL CAMWorks can be used as an add-in for all SolidWorks applications working with the cloud-based 3DExperience platform Learn how fully integrated CAD/CAM saves significant amounts of time during the design to manufacturing process Gain a new understanding of how software can connect users worldwide to accelerate product development Watch a demonstration of team collaboration using platform tools in the CAD/CAM software environment
Core Technology Molding turned to Mold-Masters E-Multi auxiliary injection unit to help it win a job and dramatically change its process.
The shop didn’t stop there. Both Swiss-type machines are fitted with a Loc-Line magnetic manifold kit that mounts to the Y-axis structure to keep coolant hoses in the same position relative to the work as the machine runs. Meanwhile, aftermarket valves enable operators to switch off coolant nozzles individually, Mr. Marchand says, whether to better direct flow or to take advantage of the resulting pressure increase in the rest of the lines.
In this webinar, industry-leading experts will demonstrate how additive manufacturing can revolutionize your operations and answer the question: Can you afford not to? From rapid prototyping to robust fixturing and specialized custom tooling, it’ll showcase the diverse applications that can drive your business forward in a time where cost and time saving can be crucial. Discover how to reduce costs, accelerate production cycles and achieve unparalleled design freedom through the strategic integration of 3D printing technology. Phillip’s panel of seasoned professionals will share real-world examples and practical insights to help you understand the potential of additive manufacturing. Learn how to overcome production challenges, improve product quality and gain a competitive advantage. It will explore the cost-benefit analysis of 3D printing — including material and labor savings — as well as the potential for increased revenue. Join this webinar to discover why additive manufacturing is no longer a luxury, but a necessity for success. Agenda: Prototyping example: quick-change prototype Custom tooling real-world example: press brake, tube bending die CMM fixturing and workholding example: CMM fixture and soft jaw
Gifted with extraordinary technical know how and an authoritative yet plain English writing style, in this collection of articles Fattori offers his insights on a variety of molding-related topics that are bound to make your days on the production floor go a little bit better.
Ever wonder what sets Top Shops apart from the competition? Dive into their award-winning practices and explore behind-the-scenes strategies for operational excellence.
Liquidmetal is a class of zirconium alloys that feature an amorphous, non-crystalline structure, which is why they are referred to as metallic glasses. Components made from these materials are extremely hard, but at the same time very elastic, which leads to very good recovery behavior. For example, the elasticity of steel is 0.2% and is 1% for titanium, while the value for components made of Liquidmetal alloys is 2%. In addition, the materials are characterized by their low specific weight and excellent corrosion resistance. This range of characteristics predetermines the alloys for use in precision components that are subjected to high mechanical stresses.
There were plenty of highlights, such as the recently extended Engel easix robot series and enhancements to its iQ weight-control software. But the biggest showstopper during the symposium was surprisingly not a plastic application, but rather metal. For the first time, Engel demonstrated injection molding of metal alloys using technology from Liquidmetal Technologies, Rancho Santa Margarita, Calif. Engel is the exclusive machine partner of Liquidmetal.
In a time where sustainability is no longer just a buzzword, the food and beverage packaging industry is required to be at the forefront of this innovation. By adopting circular packaging processes and solutions, producers can meet regulatory requirements while also satisfying consumer demand and enhancing brand reputation. Join Husky to learn more about the broader implications of the circular economy — as well as how leading brands are leveraging this opportunity to reduce costs, increase design flexibility and boost product differentiation. Agenda: The cost and operational benefits of embracing circularity Key materials in circular packaging — including rPET and emerging bioplastics How to design a circular food and beverage package Strategies for selecting sustainable closures to future-proof packaging solutions Optimization and streamlining of production processes for enhanced efficiency How Husky Technologies can enable your sustainable success
Every three years, injection machine manufacturer Engel (U.S. office in York, Pa.) invites customers and partners to its facilities in picturesque Austria to present technology innovations for injection molders. On June 16-18, more than 3000 molders from all over the world attended the Engel Symposium 2015 at the company’s machine plant in St. Valentin and the Design Center in Linz.
When, how, what and why to automate — leading robotics suppliers and forward-thinking moldmakers will share their insights on automating manufacturing at collocated event.
The Liquidmetal alloys are available in the form of slugs cut from round rods. These blanks are automatically fed into a chamber, where the material is melted inductively under high vacuum conditions. Very rapid cooling with exclusion of oxygen leads to forming of the amorphous structure. Standard robots, such as the Engel viper series, are used to remove the finished parts. The sprue can be removed with the help of a water-jet cutting machine or mechanical shears.
Are AMRs the next big trend in job shop automation? System 3R’s IMTS booth will emphasize both its specialty EDM tooling and its automation products, including an autonomous moving robot.
Second quarter started with price hikes in PE and the four volume engineering resins, but relatively stable pricing was largely expected by the quarter’s end.
Across the show, sustainability ruled in new materials technology, from polyolefins and engineering resins to biobased materials.
However, this laborious task can often be avoided with strategic tool paths, Mr. Marchand says, noting that programmers attempt to “keep the burr in front of the cutting tool” whenever possible. Beyond that, a look at any of East Coast Precision’s part programs is likely to reveal cutting paths doubling back on one another, and he insists this isn’t wasted motion. With limited deburring options, having one tool follow another to “clean up” the material in its wake is often more cost-effective than manual trimming, and it tends to have minimal impact on overall cycle time anyway.
Attend TASC, The Automated Shop Conference, in Novi, Mich on Oct. 11, 2023 for a comprehensive look into how to use automation to transform your machine shop.
FANUC’s IMTS 2024 booth includes real-time demonstrations that show the abilities of its equipment, including robots, controllers and machine tools.
In this collection of articles, two of the industry’s foremost authorities on screw design — Jim Frankand and Mark Spalding — offer their sage advice on screw design...what works, what doesn’t, and what to look for when things start going wrong.
Like seemingly everything else going on at this Chester, Connecticut, shop, these chip control strategies are rooted in basic concepts, but they’re applied with the benefit of extensive, plastic-specific expertise. Indeed, a look at the 5,600-square-foot shop floor is enough to reveal that both kinds of knowledge are the true linchpins of East Coast Precision’s success. After all, workhorse machines like the shop’s seven FANUC RoboDrill VMCs may be fast and perfectly capable of meeting the ±0.005-inch tolerances required for most work, but they’d also be at home in any number of other machine shops. The case is the same for the 12-employee company’s Hyundai and Hardinge slant-bed lathes with live tooling attachments. Indeed, the only obvious evidence that East Coast Precision is set up specifically for small, plastic work consists of the parts themselves, the presence of two Citizen A16 Swiss-type lathes, cutting tools as small as 0.02 inch in diameter, and fine-screen parts catchers.
Join Mahr for an informative webinar to discover the latest advancements in precision measurement, designed to elevate your quality assurance processes and unlock peak productivity. It'll explore cutting-edge technologies — such as modern height gages and contour measuring systems — along with their applications, benefits and technical capabilities. Discover the power of height gages: Learn how intuitive and sophisticated height gages can revolutionize your measurement processes, enabling quick and accurate results in inspection and production areas. Explore the practical functions and ease of use that make height gages an ideal solution for manufacturers seeking high-performance and reliable measuring technology. Examine sample applications and industries where height gages excel, such as qualifying first parts, inspecting incoming parts and measuring series of parts in industries like aerospace, automotive and medical. Unlock efficient contour measurement: An introduction to the latest contour measuring technologies that enable fast, simple and comprehensive contour measurement in the production environment. Discover how these innovative solutions ensure reliable measurements, saving time and increasing efficiency while measuring a wide range of workpieces. Learn how to streamline your contour measuring process with speed and simplicity, achieving fast and precise measurements with incredible versatility. Register now and discover how to unlock peak productivity with new innovations in precision measurement. Agenda: Insights into the latest precision measurement technologies and their applications Understanding of how to improve quality assurance processes and increase productivity Knowledge of how to select the right measurement solutions for your specific needs Tips on how to optimize your measurement processes for maximum efficiency
Chip control begins with the right parameters, and programmers draw extensively on past experience when determining which feeds and speeds will result in a clean cut. Although material isn’t the only variable in this exercise, it is particularly significant for East Coast Precision because the range of plastics machined here is so broad, and each behaves differently. Generally, softer materials tend to present more problems than harder ones because chips don’t break as cleanly from the stock, Mr. Marchand says. Using higher feeds and speeds in these materials can help to, as he puts it, “create a fat chip and carve it off before it has a chance to screw anything up.”
User-friendly inspection software for CNC machining centers is shown monitoring measurements between and after machining while performing SPC based on recorded measurement values.
FANUC’s IMTS 2024 booth includes real-time demonstrations that show the abilities of its equipment, including robots, controllers and machine tools.
The Automated Shop Conference (TASC) will give shops of all sizes and production volumes key insights and practical guidance on how to implement automation.
Thousands of people visit our Supplier Guide every day to source equipment and materials. Get in front of them with a free company profile.
The L.S. Starrett Co. has been manufacturing precision measurement tools in Athol, Massachusetts, since 1880. Attention to U.S. manufacturing often focuses on reshoring manufacturing from other countries, but Starrett never left. The facility in Athol employs hundreds and produces thousands of tools that remain vital for measurement in machining and other fields.
Discover how artifical intelligence is revolutionizing plastics processing. Hear from industry experts on the future impact of AI on your operations and envision a fully interconnected plant.
Across a range of technical presentations aimed at small and mid-sized job shops, the first-ever Automated Shop Conference (TASC) offered insights into several automated technologies, implementation strategies, shopfloor training tips, and even the untapped power of automated coolant delivery.
When Puneet and Neelam Neotia moved from India to the United States several years ago, they brought with them a family background in manufacturing and CNC machining. Now the couple is working to get their startup machine shop off the ground, sourcing new customers and getting the word out about their shop in Clarksville, Indiana. The couple — proud to publicize their "Made in the USA" parts — is leveraging family connections and manufacturing capabilities back in India, but not in the way that some people assume.
Chiron Group combines the best of both worlds at IMTS 2024, featuring live demonstrations of their Micro5 and Mill 2000 machines, alongside a cutting-edge virtual showroom. This innovative approach allows visitors to explore Chiron’s full product lineup without the logistical challenges of transporting large equipment.
Working closely with customers and making careful investments has enabled this Wisconsin machine shop to tackle difficult jobs with tight deadlines as a core part of its business.
New U.S.-based event announced in 2021 finally debuts next year: focuses on complete additive manufacturing value chain. More at formnextchicago.com.
Plastics processors are finding applications for 3D printing around the plant and across the supply chain. Here are 8 examples to look for at NPE2024.
A collaboration between show organizer PLASTICS, recycler CPR and size reduction experts WEIMA and Conair recovered and recycled all production scrap at NPE2024.
Learn about sustainable scrap reprocessing—this resource offers a deep dive into everything from granulator types and options, to service tips, videos and technical articles.
When revising part designs, investigate the 3D CAD, the 2D drawing and the part’s functional requirements to determine which details should be tightened up.
Incremental mode can be more advantageous when programming sculptured surfaces or for certain hole-machining canned cycle applications.
Q-Mark has built its metrology business by providing what customers need, when they want it. This goes for its IMTS booth, too, with free drinks alongside custom technology.
NEW INJECTION MOLDING MACHINE Still, processing Liquidmetal alloys is not an easy endeavor—particularly because in the molten state it is highly reactive to oxygen. For this reason, Liquidmetal alloys must be processed quickly and under a highly controlled vacuum. With that in mind, Engel developed a new injection molding machine based on its all-electric machine series, the Engel e-motion. The company says that the difference between a Liquidmetal machine and a conventional injection press lies mainly in the injection unit. Instead of a screw, the machine relies on a piston that injects the molten metal alloy into a thermo-regulated mold.
When it comes to utilizing the spindle’s power, there is a lot of headroom at the upper limits, provided it’s in short bursts. Be mindful of your time at these loads so you don’t stall out.
Legacy Precision Molds takes us on a tour of their moldbuilding facility. They've recently implemented two automated 5-axis cells for metal and graphite machining that run lights out during nights and weekends.
Join this webinar to explore the transformative benefits of retrofitting your existing injection molding machines (IMMs). Engel will guide you through upgrading your equipment to enhance monitoring, control and adaptability — all while integrating digital technologies. You'll learn about the latest trends in IMM retrofitting (including Euromap interfaces and plasticizing retrofits) and discover how to future-proof your machines for a competitive edge. With insights from industry experts, it'll walk you through the decision-making process, ensuring you make informed choices that drive your business forward. Agenda: Maximize the value of your current IMMs through strategic retrofitting Learn how to integrate digital technologies to enhance monitoring and control Explore the benefits of Euromap interfaces and plasticizing retrofits Understand how retrofitting can help meet new product demands and improve adaptability Discover how Engel can support your retrofitting needs, from free consultations to execution
Liquidmetal has a license with Apple, Cupertino, Calif., news that generated a lot of attention for the material. While Apple has yet to incorporate Liquidmetal’s bulk amorphous alloy technology into any of its devices, it did recently extend its exclusive rights to Liquidmetal for another year, according to the U.S. Securities and Exchange Commission.
Taking full advantage of coolant. The benefits of coolant go beyond removing heat from the cutting zone. It is also an essential part of chip control. Although that’s true for any shop, East Coast Precision has taken extra steps to ensure that the coolant delivery systems on its two Swiss-type lathes play this role as effectively as possible.
FANUC’s IMTS 2024 booth includes real-time demonstrations that show the abilities of its equipment, including robots, controllers and machine tools.
Join Engel in exploring the future of battery molding technology. Discover advancements in thermoplastic composites for battery housings, innovative automation solutions and the latest in large-tonnage equipment designed for e-mobility — all with a focus on cost-efficient solutions. Agenda: Learn about cutting-edge thermoplastic composites for durable, sustainable and cost-efficient battery housings Explore advanced automation concepts for efficient and scalable production See the latest large-tonnage equipment and technology innovations for e-mobility solutions
Mitsui Seiki USA Inc. appoints Joseph Farkas as its director of sales West and Terry Ritterbush as its director of sales East.
Small parts call for small tools, such as the 0.023-inch drill used to cut a hole through the length of this Torlon 4203 component. Recently, the shop added high-pressure coolant to its A16 Swiss-types and invested in through-coolant tooling to help ensure effective chip evacuation.
A company that was once a consulting firm has become a successful micro-laser machine shop producing complex parts and features that most traditional CNC shops cannot machine.
technotrans says climate protection, energy efficiency and customization will be key discussion topics at PTXPO as it displays its protemp flow 6 ultrasonic eco and the teco cs 90t 9.1 TCUs.
Though most frequently used for diameter measurements, an air plug and platen can be readily configured to measure perpendicularity.
Teel Plastics opened new plant in record time, partnering with AEC & Aqua Poly Equipment Co. to expand production of swab sticks to fight pandemic.
Weldon Solutions is demonstrating three grinders at IMTS 2024. Though they differ in size and use case, all feature the company’s hallmark customizations.
August 29-30 in Minneapolis all things injection molding and moldmaking will be happening at the Hyatt Regency — check out who’s speaking on what topics today.
The subspindle on the shop’s Citizen A16 Swiss-type lathe approaches very close to the main spindle when picking off small parts. To ensure clearance, this toolholder has been ground narrower near the cutting edge. The insert has also been modified to ensure a clean break from the rest of the stock.
Plastics Technology’s Tech Days is back! Every Tuesday in October, a series of five online presentations will be given by industry supplier around the following topics: Injection Molding — New Technologies, Efficiencies Film Extrusion — New Technologies, Efficiencies Upstream/Downstream Operations Injection Molding — Sustainability Extrusion — Compounding Coming out of NPE2024, PT identified a variety of topics, technologies and trends that are driving and shaping the evolution of plastic products manufacturing — from recycling/recyclability and energy optimization to AI-based process control and automation implementation. PT Tech Days is designed to provide a robust, curated, accessible platform through which plastics professionals can explore these trends, have direct access to subject-matter experts and develop strategies for applying solutions in their operations.
Heidenhain and Acu-Rite Solutions are offering several hands-on experiences at their booth this year, as well as internal components that reduce energy use.
When it comes to utilizing the spindle’s power, there is a lot of headroom at the upper limits, provided it’s in short bursts. Be mindful of your time at these loads so you don’t stall out.
So far, Made in the USA has looked into system-wide effects of broken supply chains, automation, skilled workforce issues and our perception of manufacturing jobs — examining each topic through a prism of individual experiences. For this final episode for Season 1, let’s look at one more system-wide question and bring it back to personal perspectives: Is there today a new dawn, a new moment for American manufacturing?
In the late 1800s, a new technology — Swiss-type machines — emerged to serve Switzerland’s growing watchmaking industry. Today, Swiss-machined parts are ubiquitous, and there’s a good reason for that: No other machining technology can produce tiny, complex components more efficiently or at higher quality.
Despite price increase nominations going into second quarter, it appeared there was potential for generally flat pricing with the exception of a major downward correction for PP.
Ever wonder what sets Top Shops apart from the competition? Dive into their award-winning practices and explore behind-the-scenes strategies for operational excellence.
Tool-holder-spindle-machine combinations each have a unique dynamic response in the same way that each person has a unique fingerprint, which can be revealed using modal testing.
Job shops are implementing automation and digitalization into workflows to eliminate set up time and increase repeatability in production.
That’s not to say that keeping up with technology isn’t important to the shop—on the contrary. The shop prioritizes technology that enables consolidating operations in fewer setups, as evidenced by the Swiss-types, the live tooling and its most recent purchase, a Miyano BNA42S turn-mill with a main spindle and fully controllable C-axis subspindle. Nonetheless, Mr. Marchand emphasizes that knowing exactly how any given material will break apart during machining has had a far greater impact on the shop’s ability to handle geometry almost too small to see with equipment commonly used for conventionally sized parts. He also emphasizes the importance of fundamentals: specifically, a solid setup, a steady hand and a patient mind. More than anything else, East Coast Precision’s competitiveness depends on both deep knowledge and best-practice, common-sense manufacturing.
The Plastics Industry Association (PLASTICS) has released final figures for NPE2024: The Plastics Show (May 6-10; Orlando) that officially make it the largest ever NPE in several key metrics.
During its triennial symposium in Austria, the machine builder molded medical forceps parts from a novel liquid-metal alloy.
Each tool setting technique has merit, and it depends on where you are as a shop and the type of work you do, as cost and efficiency all come into play.
Part of Major Tool’s 52,000 square-foot building expansion includes the installation of this new Waldrich Coburg Taurus 30 vertical machining center.
Part of Major Tool’s 52,000 square-foot building expansion includes the installation of this new Waldrich Coburg Taurus 30 vertical machining center.
The Walter Turn toolholder features rake-face cooling to help break and control chips, and double flank-face cooling directly at the cutting edge to extend tool life.
Take a look inside James Engineering, a high-end CNC Deburring OEM that became a job shop when they decided to produce their own parts in-house.
Perhaps the most significant change of all has been the addition of high-pressure coolant. The challenges plastic presents for chip control make holes with extreme length-to-diameter ratios particularly difficult to machine. That difficulty, in turn, makes these holes a particular specialty for East Cost Precision, Mr. Marchand says. For years, the shop has been refining the use of techniques like peck drilling, in which rapidly oscillating the drill helps prevent chips stuck in the flutes from rubbing against the sidewall and scarring the material. However, with coolant pressures ranging to 2,000 psi (compared to only 40 psi before) and through-coolant cutting tools, such techniques are even more effective and might not even be required.
Though most frequently used for diameter measurements, an air plug and platen can be readily configured to measure perpendicularity.
This presentation focuses on the vital role that linear and angular encoders play in ensuring precision in machine tools. Attendees will learn about the common challenges compromising accuracy, such as thermal expansion, mechanical misalignments and vibration. Whether you're an OEM, integrator, or machine operator, this webinar will offer valuable insights into optimizing CNC performance. Agenda: Challenges to CNC machine accuracy Understanding encoder technology How encoders address accuracy challenges
JD Machine, 2024’s Top Shops Honoree in Human Resources, embodies its “Education for Life” core value with a robust apprenticeship program and significant continuous improvement efforts.
When it comes to raw shopfloor efficiency, nowhere is this combination more important than chip control, he says. The following provides a brief look at the basic concepts behind the shop’s go-to strategies for avoiding defective parts, chip “bird nests,” time-consuming deburring operations and other issues that can push back delivery dates.
Even the hardest plastics are prone to bend and stretch rather than break when subjected to force, he explains. As a result, turning and milling often create long, stringy chips that can adhere stubbornly to the rest of the stock; gum up cutting edges; and wrap around the part, the tool shank or anything else they happen to catch as they peel away. Beyond problems during machining, effective chip control is critical for preventing burrs, which can significantly increase overall manufacturing time for the shop’s tiny plastic parts.
In the latest episode of our View From My Shop series, MMS Editor-in-Chief Brent Donaldson visited the JN Shapiro Watches headquarters and production facility where Founder Joshua Shapiro—a history teacher turned watchmaker—realized his dream of "making a watch from scratch and everything in it."
In this episode of Made in the USA, several executives and senior staff at Hardinge give their first-person account of how they formulated the plan to shift the manufacturing of its milling and turning product lines from its Taiwan plant to its plant in Elmira, New York, the major challenges they encountered and the rewards that made it worth the effort.
In the latest episode of our View From My Shop series, MMS Editor-in-Chief Brent Donaldson visited the JN Shapiro Watches headquarters and production facility where Founder Joshua Shapiro—a history teacher turned watchmaker—realized his dream of "making a watch from scratch and everything in it."
Liquidmetal also has a license agreement with Swiss jewelry maker Swatch to use the material for watches. The licenses for the new method are obtained from Liquidmetal Technologies, with Engel delivering its injection molding machinery to licensed partners.
Engel developed a new all-electric injection molding machine for molding the Liquidmetal alloys. Instead of a screw, the machine has a piston (below) with which the molten metal alloy is injected into a thermo-regulated mold.
The latest episode “Made in the USA” podcast explores a company that uses collaborative robots, one of the key tools helping US machine shops and other manufacturers compete with lower cost countries by automating production.
Okuma America Corp. announces its plans to create a global service and repair facility, set to open in Charlotte, North Carolina, in 2025.
Low RPM lathes can cause tool breakage and prevent you from achieving proper SFM, but live tooling can provide an economical solution for these problems that can accelerate production.
Discovered by researchers at the California Institute of Technology, Liquidmetal controls the intellectual property rights with more than 70 U.S. patents.
Horn USA’s new booth concept is designed to enable attendees to (literally) get a better feel for its various tooling offerings.
Entrepreneur Scott Colosimo found early success in China producing parts for his Cleveland-based motorcycle company in the mid-2000s. This is the story of how IP theft issues overwhelmed the business, prompting Colosimo and his team to start over from scratch — and move production back to the United States.
With Liquidmetal, Engel is presenting an alternative to metal injection molding (MIM) and CNC machining. Unlike those other processes, the machine can produce Liquidmetal parts in 2-3 min. In addition, there is no waste accumulated in Liquidmetal processing because the sprues can be recycled. POTENTIAL APPLICATIONS During the symposium, Engel molded parts for medical forceps with Liquidmetal alloy. The company says it chose to showcase that product because it sees good potential for Liquidmetal technology in the field of medical technology. For instance, endoprostheses like hip joints or stents are also possible with Liquidmetal. Engel also foresees it being used in electronics, aerospace, military technology, and sports equipment.
Rob Guiao, Chris Hall and Bassanio Peters will demonstrate relatable situations to equip you with data to improve predictability, future-proof operations and maximize ROI. Agenda: Explore the importance of data in decision-making, especially for facility upgrades or new projects Learn how comprehensive solutions for manufacturing and construction projects can improve predictability and ROI See real demonstrations of machine integrations, facility layouts and automations to ensure proper throughput and integration
In this collection of content, we provide expert advice on welding from some of the leading authorities in the field, with tips on such matters as controls, as well as insights on how to solve common problems in welding.
Tool-holder-spindle-machine combinations each have a unique dynamic response in the same way that each person has a unique fingerprint, which can be revealed using modal testing.
Structured light scanning is used to create a digital twin of a manufactured part, but we must understand the measurement reproducibility to best use the data.
Clean, burr-free cutting is fundamental to competitiveness for a shop that specializes in micro-machining complex geometry from some of the softest materials in the industry.
After eight years at East Coast Precision Manufacturing, Chris Marchand knows a thing or two about micro-machining plastics. Having specialized solely in this work since its inception in 2006, the shop has carved a niche for itself in small, complex geometry that other manufacturers can’t or won’t quote. Asked for specifics on how the shop leverages its deep knowledge of machining everything from acetal, acrylic and polytetrafluoroethylene (PTFE) to trademarked materials like Teflon, Ultem and Torlon, Mr. Marchand repeatedly returns to one particular topic. “The more I think about it, the more I realize just how focused we are on controlling chips,” he says.
While the melting process does not provide perfect mixing, this study shows that mixing is indeed initiated during melting.
Lee Wimmer invited us to tour his second-generation family-owned machine shop in Perkasie, PA. This video explores the production processes behind precision-machined parts for both Wimmer Custom Cycle and LS Wimmer Machine Co., and shows how ingenuity and determination are still at the heart of American manufacturing. Today, both companies are now managed by Wimmer’s three sons.
This month’s resin pricing report includes PT’s quarterly check-in on select engineering resins, including nylon 6 and 66.
Additive technology creates air pockets in film during orientation, cutting down on the amount of resin needed while boosting opacity, mechanical properties and recyclability.
Coverage of single-use plastics can be both misleading and demoralizing. Here are 10 tips for changing the perception of the plastics industry at your company and in your community.
The choice between buying a new machine or refurbishing the current one will become clear after a thorough assessment of the machine.
Say “manufacturing automation” and thoughts immediately go to the shop floor and specialized production equipment, robotics and material handling systems. But there is another realm of possible automation — the front office.
Consistency is key for beryllium manufacturing, so the data visibility granted by Harmoni has swiftly become a vital, profitable tool in the shop’s arsenal.
After successfully introducing a combined conference for moldmakers and injection molders in 2022, Plastics Technology and MoldMaking Technology are once again joining forces for a tooling/molding two-for-one.
Given the prevalence of features like the slots in the sides of this Torlon 4203 part, milling and drilling capability is common to all of the shop’s turning machines.
Given that this challenge is fundamental to every job, chip control is a fundamental part of planning every manufacturing sequence. In fact, operations and tools are often dedicated specifically to that purpose. Not just any tools will do, either. The shop routinely modifies geometries on an in-house grinder to ensure material breaks away cleanly. For the same reason, all cutting tools must be exceedingly sharp. Attention to coolant delivery is also critical to ensure waste material flushes away from the cutting zone.
Did you know that the show was postponed for WWII? Or that McCormick Place was expanded in the ’70s just to accommodate IMTS? A fascinating look at the show’s history from 1927 to today.
Plastics Technology covers technical and business Information for Plastics Processors in Injection Molding, Extrusion, Blow Molding, Plastic Additives, Compounding, Plastic Materials, and Resin Pricing. About Us
Take a look inside James Engineering, a high-end CNC Deburring OEM that became a job shop when they decided to produce their own parts in-house.
From quadruped robot dogs, to an in-booth putting green where you can test out a new golf putter, to a 3D-printed car and more, attendees enjoyed cutting-edge technology and innovations all week long. Take a look to see what (or who!) you might have missed this week!
Mike Sepe has authored more than 25 ANTEC papers and more than 250 articles illustrating the importance of this interdisciplanary approach. In this collection, we present some of his best work during the years he has been contributing for Plastics Technology Magazine.
Understanding all the things that contribute to a machine’s full potential accuracy will inform what to prioritize when fine-tuning the machine.
Multiple speakers at Molding 2023 will address the ways simulation can impact material substitution decisions, process profitability and simplification of mold design.
The most obvious addition is extra delivery lines for the shop’s water-based coolant. (Water-based coolant is generally preferred to oil formulations, which tend to leave difficult-to-clean residue on plastic parts, Mr. Marchand notes.) Beyond increasing coolant volume—and thus, the likelihood of flushing out stray chips—extra lines provide more options for controlling coolant direction. Mr. Marchand says those options come in particularly handy for custom tool geometries that are prone to deflecting chips directly into the feed, another cutter in the tool magazine or any other undesirable location.
Each tool setting technique has merit, and it depends on where you are as a shop and the type of work you do, as cost and efficiency all come into play.
Weldon Solutions is demonstrating three grinders at IMTS 2024. Though they differ in size and use case, all feature the company’s hallmark customizations.
Processors with sustainability goals or mandates have a number of ways to reach their goals. Biopolymers are among them.
The MB45 series is designed to deliver the low cutting force benefits of positive inserts and the fracture resistance of negative inserts.
Job shops are implementing automation and digitalization into workflows to eliminate set up time and increase repeatability in production.
This Ultem component’s washer-like geometry makes it particularly prone to burrs. Given the central hole, a cut-off tool that isn’t sufficiently sharp could create enough pressure to break the part off the rest of the stock, thus creating a semi-circular, ribbon-like burr around the edge of the ID, before it has a chance to shear all the way through.
Women in Manufacturing is excited to announce that the 2024 SUMMIT will be a hybrid event — both an in-person and virtual experience. Both program offerings will enable you to grow through education and connections that are insightful, meaningful and actionable. Join Women in Manufacturing Oct. 6-9, 2024, in Boston or digitally for an event filled with plant tours at leading manufacturing facilities, professional development sessions, roundtable discussions on important topics, and inspiring keynotes. All while engaging and interacting with peers through social and networking events! __PRESENT __PRESENT
While prices moved up for three of the five commodity resins, there was potential for a flat trajectory for the rest of the third quarter.
Currier Plastics has added substantial capacity recently in both injection and blow molding for medical/pharmaceutical products, including several machines to occupy a new, large clean room.
At East Coast Precision, organized, tidy workstations are reflective of the calm, patient mindset required to work with small parts. Toolmaker’s microscopes like the one shown here are placed strategically on tables like this throughout the shop, along with quality policies, travelers for specific jobs and other reference information.
Are AMRs the next big trend in job shop automation? System 3R’s IMTS booth will emphasize both its specialty EDM tooling and its automation products, including an autonomous moving robot.
Modern Machine Shop is the leading publication and media brand in North America devoted to CNC machining. MMS combines unprecedented editorial access to manufacturing facilities with decades of experience to provide long-form content that is both insightful and impactful. About Us
Shown here mounted on a wire, this polytetrafluoroethylene (PTFE) part prompted the shop to increase attention to the cleanliness of its coolant. Measuring only 0.015 inch, the part is virtually indistinguishable from chips leftover from other jobs without sufficient coolant filtering.
This Knowledge Center provides an overview of the considerations needed to understand the purchase, operation, and maintenance of a process cooling system.
In this collection, which is part one of a series representing some of John’s finest work, we present you with five articles that we think you will refer to time and again as you look to solve problems, cut cycle times and improve the quality of the parts you mold.
Zoller’s open house in Ann Arbor, Michigan, provided attendees with a glimpse of the connectivity and efficiency the company’s products offer to users.
Formnext Chicago is an industrial additive manufacturing expo taking place April 8-10, 2025 at McCormick Place in Chicago, Illinois. Formnext Chicago is the second in a series of Formnext events in the U.S. being produced by Mesago Messe Frankfurt, AMT – The Association For Manufacturing Technology, and Gardner Business Media (our publisher).
Mold maintenance is critical, and with this collection of content we’ve bundled some of the very best advice we’ve published on repairing, maintaining, evaluating and even hanging molds on injection molding machines.
Keeping tools sharp. The prevalence of customized and slightly modified tool geometries isn’t the only reason why East Coast Precision’s benchtop grinder is in high demand among employees. Tool sharpness is a top priority, Mr. Marchand says, even to the point that the shop is known to sharpen brand new cutters right out of the box, before they’re ever used. To the same end, employees performing setups are often found peering through the eyepieces of 30X-magnification toolmaker’s microscopes to ensure tools are sharp before putting them in machines. Tools are also changed frequently to ensure they stay as sharp as possible. Finally, dull tools are always a chief suspect when something goes wrong with a process.
Manufacturers continue to feel the pressure to reduce costs, increase efficiencies and meet their sustainability strategies. As the industry evolves to keep pace with these priorities, there are opportunities within metalworking processes to use less resources with advanced lubricants and technical expertise. Agenda: An overview of metalworking lubrication Evolutions in metalworking lubrication Experience on the shop floor Key takeaways
Automation is no longer a luxury in manufacturing today – it’s a necessity. The Automated Shop Conference (TASC) will connect job shops with experts who offer advice and considerations for this process.
Working closely with customers and making careful investments has enabled this Wisconsin machine shop to tackle difficult jobs with tight deadlines as a core part of its business.
Liquidmetal is expensive, which could place some limits on its use. It costs about $110/kg, and the maximum shot weight is 100 g. Of that, approximately 20 g is required for the sprue, resulting in a maximum part weight of 80 g.
Looking to automate your shop floor? The Automated Shop Conference (TASC) will connect shops with experts who can advise them through this transition.
FANUC’s IMTS 2024 booth includes real-time demonstrations that show the abilities of its equipment, including robots, controllers and machine tools.
Thousands of people visit our Supplier Guide every day to source equipment and materials. Get in front of them with a free company profile.
Exhibitors and presenters at the plastics show emphasized 3D printing as a complement and aid to more traditional production processes.
AccuRounds has created synergy between culture and technology, driving a commitment to customer satisfaction and continuous improvement.
Walter USA has acquired PDQ Workholding, intending to strengthen its offering of workholding products and develop future cutting tool sales.
Across all process types, sustainability was a big theme at NPE2024. But there was plenty to see in automation and artificial intelligence as well.
Resin drying is a crucial, but often-misunderstood area. This collection includes details on why and what you need to dry, how to specify a dryer, and best practices.
Introduced by Zeiger and Spark Industries at the PTXPO, the nozzle is designed for maximum heat transfer and uniformity with a continuous taper for self cleaning.
Join Wittmann for an engaging webinar on the transformative impact of manufacturing execution systems (MES) in the plastic injection molding industry. Discover how MES enhances production efficiency, quality control and real-time monitoring while also reducing downtime. It will explore the integration of MES with existing systems, emphasizing compliance and traceability for automotive and medical sectors. Learn about the latest advancements in IoT and AI technologies and how they drive innovation and continuous improvement in MES. Agenda: Overview of MES benefits What is MES? Definition, role and brief history Historical perspective and evolution Longevity and analytics Connectivity: importance, standards and integration Advantages of MES: efficiency, real-time data, traceability and cost savings Emerging technologies: IoT and AI in MES
Successfully starting or restarting an injection molding machine is less about ticking boxes on a rote checklist and more about individually assessing each processing scenario and its unique variables.
The aim of this presentation is to guide you through the factors and the numbers that will help you determine if a robot is a smart investment for your application. Agenda: Why are you considering automation? What problems are you trying to solve? How and why automation can help Crunch the numbers and determine the ROI
Sharp tools are so important for two reasons. First, the smaller the part, the greater the potential impact of a dull tool that “pushes” material rather than shearing cleanly through it. Second, that kind of pushing is far more likely to happen in plastic than in even the softest metal. “Even in harder plastics, there might be little pits where a dull tool has torn off material as opposed to slicing it,” Mr. Marchand says. “These types of surface finishes are unacceptable for our work.”
Formnext Chicago is an industrial additive manufacturing expo taking place April 8-10, 2025 at McCormick Place in Chicago, Illinois. Formnext Chicago is the second in a series of Formnext events in the U.S. being produced by Mesago Messe Frankfurt, AMT – The Association For Manufacturing Technology, and Gardner Business Media (our publisher).
Join KraussMaffei for an insightful webinar designed for industry professionals, engineers and anyone interested in the manufacturing processes of PVC pipes. This session will provide a comprehensive understanding of the technology behind the production of high-quality PVC pipes: from raw material preparation to final product testing. Agenda: Introduction to PVC extrusion: overview of the basic principles of PVC pipe extrusion — including the process of melting and shaping PVC resin into pipe forms Equipment and machinery: detailed explanation of the key equipment involved — such as extruders, dies and cooling systems — and their roles in the extrusion process Process parameters: insight into the critical process parameters like temperature, pressure and cooling rates that influence the quality and consistency of the final PVC pipes Energy efficiency: examination of ways to save material and energy use when extruding PVC pipe products
While the major correction in PP prices was finally underway, generally stable pricing was anticipated for the other four commodity resins.
Learn more about the variety of technology and machinery Hwacheon Machinery America, Inc. is featuring at its IMTS 2024 booth.
AccuRounds has created synergy between culture and technology, driving a commitment to customer satisfaction and continuous improvement.
Lee Wimmer invited us to tour his second-generation family-owned machine shop in Perkasie, PA. This video explores the production processes behind precision-machined parts for both Wimmer Custom Cycle and LS Wimmer Machine Co., and shows how ingenuity and determination are still at the heart of American manufacturing. Today, both companies are now managed by Wimmer’s three sons.
Mixed in among thought leaders from leading suppliers to injection molders and mold makers at the 2023 Molding and MoldMaking conferences will be molders and toolmakers themselves.
Chiron Group combines the best of both worlds at IMTS 2024, featuring live demonstrations of their Micro5 and Mill 2000 machines, alongside a cutting-edge virtual showroom. This innovative approach allows visitors to explore Chiron’s full product lineup without the logistical challenges of transporting large equipment.
Sustainability continues to dominate new additives technology, but upping performance is also evident. Most of the new additives have been targeted to commodity resins and particularly polyolefins.
Take a deep dive into all of the various aspects of part quoting to ensure you’ve got all the bases—as in costs—covered before preparing your customer’s quote for services.
GETTING A QUOTE WITH LK-MOULD IS FREE AND SIMPLE.
FIND MORE OF OUR SERVICES:
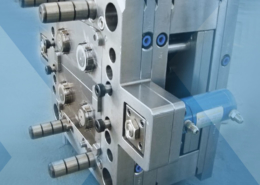
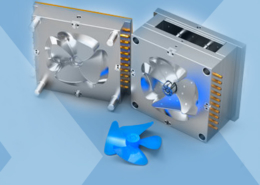
Plastic Molding

Rapid Prototyping
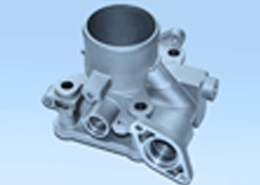
Pressure Die Casting
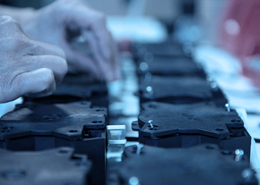
Parts Assembly
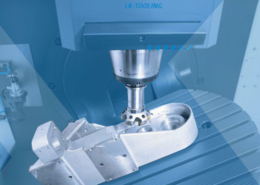