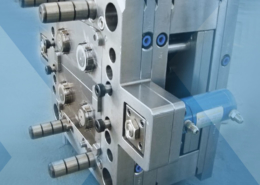
Plastics Products Makers Posting Sales, Margin Gains - injection molding company
Author:gly Date: 2024-09-30
The answer lies in considering the parts and assembly processes that IME renders unnecessary. For example, providing capacitive touch sensing by applying functional foils means that lighting and waveguides need to be produced and installed separately, whereas with IME they are integral to the component. Greater integration means that IME will require fewer parts and materials and fewer assembly processes overall. IME parts, thus, will be lighter, benefitting both electric vehicle range and sustainability.
This apparent discrepancy poses an important question: Will the capacitive human-machine interface (HMI) components of the future be produced using IME, or will the simpler, currently used manufacturing methodologies persist? This question is addressed in a recent report published by IDTechEx titled, “In-Mold Electronics 2022-2032: Technology, Market Forecasts, Players.” The market could be worth $1.5 billion by 2032, according to the report.
As a molded plastic part manufacturer, what do you think are your company's core competencies that make you the optimal choice compared to your competitors in Japan and overseas?
We do not have a presence in the overseas market at this time. We have plenty of collaboration, especially with material production companies. Our long-standing relationship and collaboration with Panasonic started because they used to use magnesium, which was expensive and hard to handle and they consulted with us to make an alternative material with the same properties. This was the component used for personal handheld digital cameras. They wanted to replace their existing material with plastic. I talked with several material production companies to address this request but it was difficult because magnesium has an electromagnetic shield property that plastic does not have. The client wanted to keep the same property and level of hardness. We mixed the plastic with carbon fiber to give the electromagnetic shield property and added hardness. This is how our new material was applied by Panasonic. This added to the complexity of the production process, however we overcame it and increased its productivity.
A molded plastic parts manufacturer first established over 100 years ago, Daimei Plastic is a leading light when it comes to sustainable innovation.
I am oriented toward the foreign market. I used to work in a foreign capital company and I used to live in a foreign country as well. When my predecessor entered the Singaporean market, I lived there for six years. However, the market of injection molding has become a commodity now. If we bring it as it currently is to foreign markets, we may not be able to be competitive when it comes to pricing. We are trying to change our business model to be competitive in the foreign market. Once we find a way to compete in the other markets, we would like to enter the overseas market with that new business model. I don't have any region in mind but it is going to be either Asia or North America.
When it comes to EVs, lightweight parts are required. The Gas Assist Injection molding technology was a proposal we made to improve the surface appearance of thick plastic surfaces with sink marks. We improved the technology to be used for lightweight automotive parts. We improve and look for new applications for existing technologies to meet customer demands.
You are celebrating your 109th year anniversary this year. If we come back six years from now and have this interview again, what goals and dreams would you like to have accomplished by then?
Because of the less stringent material requirements and lower adoption barriers relative to IME, applying functional foils to slightly curved parts to make capacitive touch switches has already reached commercialization in the automotive sector. Given that the two manufacturing methods result in parts with very similar functionalities and, hence, consumer experience, how can IME compete?
A few years ago, we received a request for the same material for industrial cameras. Again, we worked with a partner to develop that material. It does not have a surface coating but the client wanted a good appearance and the same electromagnetic shield property and level of hardness. We achieved this with the new material and our client adopted it. Every year, Panasonic requests suppliers to come up with eco-friendly proposals and they evaluate them under the ECO-VC Initiative. We got the Gold Award in 2021 for this material.
The hybrid thermoforming/injection-molding process has the potential to incorporate a wider range of functionalities, including haptics, energy harvesting, and heating, than current production methods.
Our existing business is focused on the automotive and amusement sectors and other miscellaneous fields. Moving forward, we would like to address new markets and have a third or fourth pillar for our business. To achieve that, we would like to approach and collaborate with various customers, regardless of the size of the company or the length of its history.
About 20 years ago, we started again and launched Healthy Foot Washer because we wanted to have our original brand. Having our own brand made our employees happy. We got plenty of media exposure, which motivated our employees. In addition, we developed new products for traveling goods and Kasa Hotaru, an umbrella that shines by itself. It was shown on a TV program recently. The Healthy Foot Washer was also picked up by some TV programs. Recently, we have released new brands and one of them is SOEM. For branding and designing of SOEM, we are collaborating with a company specializing in designing and branding to develop it.
Through your R&D, you made advancements and found a new application for Gas Assisted Injection molding technology. Can you give us a simple explanation of how Gas Assisted Injection molding is different or more effective in creating parts than conventional plastic injection molding?
The other thing is we are trying to utilize the data generated from monozukuri to contribute to better efficiency in production. We believe the various data which can be received from making plastic products predict potential defects.
This technology was used to improve the appearance of thick plates that have surface sink marks or dents. Resins can have different thicknesses. One part can be thinner while the other part is thicker. They get compressed when the temperature drops. The thicker parts are more compressed than the thinner part. Sink marks and dents appear during compression. This technology uses air to correct the sink mark on the surface. It is a technology that has been around for a long time but we have pioneered this kind of application.
The Japanese advantage is the ability to see something through to the end. We are good at sustainable innovation. The Japanese are very detail oriented and skillful in their work. We spare no effort in improving the tools we are using when the current tools present inconveniences. Let’s take chopsticks as an example. In Japan, one edge is thinner than the other, but Chinese chopsticks are not this way. Chopsticks originally came from China, but the Japanese made improvements to them because they found them inconvenient. This is a strength of the Japanese monozukuri. When we realize that something needs improvement, we are willing to put forth the effort to improve the process or the product. This is our competitive edge.
Technologies are important, but something more important than that is the ability to meet customer requests. We have three Top Management Policies: making the most of people’s ability, sustainable creation of technical products and a flexible management system. Our employees act according to these policies. We believe that our ability to meet the demands of our customers, which we consider our core competence, is also the result of embodying one of our policies, the sustainable creation of technological products. In 2004-2005, about 80% of Daimei's sales was from Panasonic. Today, 30-40% of our sales comes from the automotive sector, 30-40% from the amusement sector, and the rest comes from Panasonic and the others. We were the first vendors which means the most reliable supplier for Panasonic's flagship product, the TV. There were only three companies manufacturing TVs, so we had a large share in the field.
Back in 1976, we launched about several B2C products. One was puzzles and another was big block toys for children to build houses. They did not sell very well so we stopped manufacturing B2C products. It was too early to launch to the market. I think that if we launch them now, they might sell better.
We are also trying to find new business from our existing production process. We would like to find something that can be spun out of the process. An example is the repair of our molds. Although we used to just produce new molds, we have started a repair business with our skills.
TV cabinet produced in 1955 SOEM Healthy Foot Washer Gas Assist Injection Molding (interior) Previous Next
Crucially, as IME technology develops, a wider range of functionalities will be integrated. These include haptics, energy harvesting, heating, and even the control electronics (i.e., PCBs), removing the need for many separate parts and enhancing the IME value proposition. With functional foils, such extensive integration of electronics is challenging and slow, since components would need to be mounted on a 3D surface. By contrast, IME electronic components can be mounted before thermoforming via comparatively rapid conventional 2D pick-and-place systems.
We are seeing new components used for EVs that did not exist before. We make proposals for the designs of new components that need to be developed from scratch and work together with our customers to develop these.
A big part of our sales comes from the automotive and amusement sectors, and we became the first vendor in both fields. We have about a 70-year relationship with Panasonic, but less than 20 years in the automotive and amusement field. In these latter two fields, we are new players. Most companies have existing suppliers already. Despite that, we became the first vendor. This was a result of responding to customer requests. The automotive sector has very high standards for quality and we tried to meet their requests. In addition, we responded to new methods of production and technologies demanded by the customers. Furthermore, we are pursuing material development. All these contributed to making us the first vendor. Our employees like new challenges. When they receive requests, they are very willing to address and work on them which gains the trust of customers.
It is common to have a proposal-oriented approach with the clients and use technologies for advancement in the B2B market in components, household products, or cars. However, we are also curious about your B2C client, For example, your Healthy Foot Washer. What motivated you to apply your technologies and expertise in the B2C fields? Can you give us an introduction to some of your key B2C products?
The reason is that we do not know which field will grow in the future. We used to have key products for the TV cabinet and we started molding for that component in 1955 which was the first time in the world, but at the time, there was not one TV per household. Today, the market has grown and now we have more than one TV per household. Perhaps one room has one TV. Even if the market is still small, if we see a potential for future growth, we will not hesitate to enter that field.
Despite their visual similarity, backlit capacitive touch sensors can be produced with a range of different methods. One common approach, deployed in some recently launched cars, is to first produce a decorative, often curved part via high-pressure thermoforming and subsequent injection molding. A functional film comprising a printed conductive pattern of capacitive switches and interconnects is then attached to the back side. Conductive regions can be transparent — either via conductive polymer PEDOT:PSS (poly(3,4-ethylenedioxythiophene) polystyrene sulfonate) or metal mesh) — to enable backlighting with separately produced waveguides.
The Worldfolio provides business, industrial and financial news about global economies, with a focus on understanding them from within.
By contrast, the manufacturing process for IME places more challenging requirements on the materials. First, conductive ink is printed onto a plastic, commonly polycarbonate, substrate. Electrically conductive adhesives (ECAs) are then used to attach electrical components such as LEDs. The substrate with conductive traces and mounted components is then thermoformed to produce the desired curvature, followed by injection molding to produce the complete part.
Lee Kuan Yew is the founding father of Singapore. He loved Japan and often talked about the story of chopsticks. He knew of the Japanese kaizen philosophy of constantly improving products. He wanted to incorporate the kaizen culture into Singapore. The Japanese are not good at disruptive innovation but we are good at sustainable innovation. Automotive makers in Europe are familiar with the term kaizen. In our company, each engineer on the gemba can come up with an idea for kaizen. The Japanese have high-quality products because they pursue perfection in their products. This is what keeps us competitive.
HMI components that offer backlit capacitive touch sensing are increasingly utilized in multiple applications, including automotive interiors and household appliance control panels. Relative to traditional mechanical switches, the fewer parts used in backlit capacitive touch sensors make them both lighter and simpler to assemble, while the lack of discrete buttons means that they can be wiped clean.
In-mold electronics (IME) is often touted as a forthcoming revolution in how automotive touch-sensitive interfaces will be manufactured. However, while smooth capacitive touch sensors are increasingly common in many recently launched vehicles, especially on steering wheels and parts of the center console, they are not currently produced by IME. Instead, other methods, such as applying functional films to existing 3D parts, are employed.
GETTING A QUOTE WITH LK-MOULD IS FREE AND SIMPLE.
FIND MORE OF OUR SERVICES:
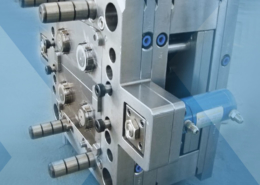
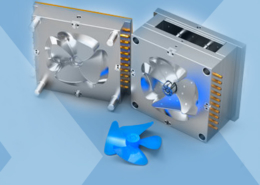
Plastic Molding

Rapid Prototyping
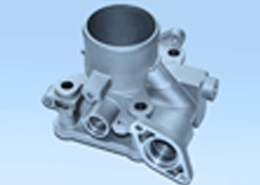
Pressure Die Casting
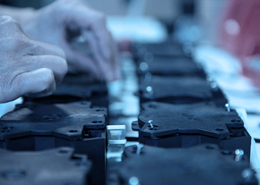
Parts Assembly
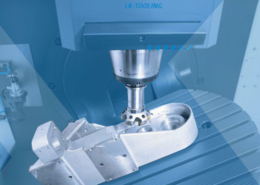