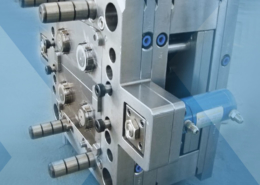
Plastics Processors Who Hire ‘Second-Chance’ Workers Do Well by Doing Good - atl
Author:gly Date: 2024-09-30
RapidDirect, a leading rapid prototyping company in China, is seeking to bridge the gap between physical and digital production systems for rapid prototyping and on-demand manufacturing with its instant quote platform.
“We understand that there is currently a big gap in the rapid manufacturing space in terms of quotes,” said Leon Huang, CEO of RapidDirect. “The need to shorten the product development cycle and reduce investment risks while saving costs continues to increase by the day. The rapid prototyping industry is also marked by a cumbersome quotation process. Prototyping customers find it difficult to get price quotes of multiple manufacturers in a short period for price comparison.
Essentially, RapidDirect’s instant quote platform removes the outdated and tedious back-and-forth file exchange process and long-winded email chains, and replaces these processes with a faster, simplified ordering experience. As a result, manufacturing lead times are significantly shortened and overall customer experience is improved.
The data-driven platform shortens the preparation stage of the prototyping process from days to less than a minute, allowing designers and manufacturers alike to upload their designs and choose from a range of suitable manufacturing options. From this, customers can instantly receive real-time information regarding price, materials, and finish options, enabling them to order various parts more quickly and freeing up engineers for other manufacturing projects.
RapidDirect’s rapid prototyping and on-demand manufacturing capabilities span CNC machining, 3D printing, injection molding, sheet metal fabrication and much more. The firm has two factories located in Shenzhen which cover more than 3,000 square meters and house state-of-the-art manufacturing equipment.
Gerard Henn, Avenue’s general manager, said: “All medical programmes are lengthy as it can take two to three years to obtain approvals from the authorities, so there are many months of testing before a component or mould is ready to be scaled up to mass production.”
Plastic moulding continues to be used for many medical applications, including manufacturing implantable medical device components, test tubes, beakers, casings and housings for laboratory and medical equipment, drug delivery components and surgical equipment. With demand for medical devices at an all-time high across hospitals and laboratories thanks to COVID-19, this has had a positive impact on market growth.
Establishing an Irish office is also part of a post-Brexit insulation strategy that will moderate any potential concerns Irish moulders may have about dealing with a UK machinery supplier. A permanent in-country service and support base will facilitate timely spare parts sourcing and trading in euros without incurring hefty exchange fees. We firmly believe that Ireland’s talent base and this supportive infrastructure will continue to make Ireland very attractive to inward investment, especially in medical and biotechology R&D.
This creates some complications in relation to the CE marking process on medical devices as the UKCA (UK Conformity Assessed) mark will replace the longstanding CE mark for goods, including medical devices, sold within England, Wales and Scotland. As there’s no hard border in Ireland, the CE mark still applies there.
The global medical injection moulding market size was valued at $1.38 billion in 2019 and is expected to grow at a compound annual growth rate (CAGR) of 8.2% between 2020 and 2027. Much of this is being driven by advances in the home healthcare sector and an ageing population, which WHO predicts will double by 2050.
The company provides rapid prototyping services for clients in a whole host of industries, ranging from aerospace and automotive to medical and consumer goods. The firm is also ISO 9001:2015 certified for its management system, which ensures its products and services meet both regulatory requirements and those of its customers. To complement this, RapidDirect’s team of 10 quality inspection personnel, 10 technical engineers, and 15 sales engineers, are on hand to assist manufacturers with their orders.
Darren Herron, UK national sales manager at Sumitomo Demag, analyses the injection moulding market and what is driving new developments for medical applications.
Additionally, users no longer need to log into multiple tracking systems in order to place or monitor their orders, as they can do this all within the instant quote platform.
The company ensures the quality of the parts it manufactures through the installation of a range of professional inspection equipment, including coordinate measuring machines, projectors, and height gauges. RapidDirect also boasts a strong supplier and manufacturing network to provide its customers with competitive prices and fast delivery, and offers 24/7 technical engineering support.
In fact, RapidDirect claims that manufacturers could save up to 30 percent of their budget by using the instant quote platform, and increase their efficiency by up to a third.
Sumitomo (SHI) Demag recently supplied a 75 tonne IntElect all-electric injection moulding machine to Avenue, a Nolato Company, in Sligo, Ireland. The investment supports the growth in the company’s healthcare division, providing dedicated capacity to mould precision parts during the product development phase. With demand for its medical device injection moulding and tool-building services increasing, Avenue recently installed a new 100 sqm ISO Class 8 cleanroom area.
Based on artificial intelligence (AI) algorithms, the platform analyzes the design data of uploaded CAD files and then automatically generates a quote from which customers can place orders. The instant quoting engine allows manufacturers to receive quotes at any time of day, and gain immediate access to all of RapidDirect’s prototype machining services.
Hayley is a Technology Journalist for 3DPI and has a background in B2B publications spanning manufacturing, tools and cycling. Writing news and features, she holds a keen interest in emerging technologies which are impacting the world we live in.
To enhance patient safety, there’s a drive towards using new and more innovative regulated materials with a better flow and high impact strength to mould components. The EU Medical Device regulations came into force 26 May 2021, following a one-year extension due to the pandemic. In Vitro Diagnostic medical device regulations (known as IVDR) become effective 26 May 2022. In the UK, the market is currently regulated by the UK Medicines and Healthcare products Regulatory Agency (MHRA).
RapidDirect launched its instant quote platform in June this year, pitched as one of the first-ever platforms to offer instant quotes for multiple prototyping services. Customers can select from four major manufacturing services – 3D printing, CNC machining, sheet metal fabrication, and injection molding – to bring their prototype designs to fruition.
New customers to RapidDirect’s instant quote platform are currently able to receive 15 percent off their first orders until 20th October 2021, using the coupon code RD3DIND. Customers can get an instant quote here.
Using RapidDirect’s instant quoting system, users are able to download, manage, and edit multiple quotes in one place, and are provided with lead times and bulk prices upfront. Customers can also compare the prices of different materials and technologies in order to make faster and more informed design decisions.
The machine’s small footprint is down to the use of its own motors and drives. The model also has wide tie bar spacing and high clamp force for its size, allowing the use of larger moulds than would normally be accommodated by a 75-tonne machine.
RapidDirect’s rapid prototyping and on-demand manufacturing capabilities are competing with the likes of global manufacturing marketplace Xometry and online manufacturing platform Hubs, which was recently acquired by on-demand digital manufacturing provider Protolabs. Like these companies, RapidDirect is seeking to democratize and streamline the on-demand manufacturing process for its customers by providing a one-stop-shop for their rapid prototyping and mass production needs.
The IntElect machine met Avenue’s brief for a small footprint machine for carrying out test runs during the development phase of projects.
Besides, the platform integrates automated DfM feedback into each rapid prototyping workflow, allowing users to easily make adjustments to their order at any point during the process. The automated DfM analysis feature helps to ensure better production design, faster turnaround time, and, ultimately, higher quality products.
Advanced batch tracking, contact-free inspection using cameras, and highly automated assembly are among the latest developments to meet the medical device market’s precision and quality control requirements. Traceability is not just about mandatory information and supply chain tracking. Real-time traceability is about being able to call up data and verify the exact settings used on the injection moulding machine when that individual plastic part was made, making connectivity to a Management Executive System (MES) vital.
With a large proportion of Sumitomo (SHI) Demag’s Irish customers in the medical market in Ireland, we last year opened a service and support office in Limerick, Ireland. This was to support its installed base of predominantly all-electric machines, providing on-the-ground preventative and reactive machine maintenance and troubleshooting support.
Subscribe to the 3D Printing Industry newsletter for the latest news in additive manufacturing. You can also stay connected by following us on Twitter and liking us on Facebook.
Essentially, RapidDirect’s instant quote platform allows customers complete access to a wide range of prototyping and on-demand manufacturing services, and shortens the preparation stage from days to within a minute. Furthermore, the platform enables customers to download, manage, and edit their quotes in a single place, while shortening turnaround times, boosting efficiency, and saving costs.
For example, when parts are being produced on multi-cavity tools, like pipettes, robots are programmed to remove and place the components into cavity-assigned racks. This means that if an issue with cavity 1 arises, the rack containing all corresponding cavity 1 parts can be isolated and the rack recalled, with all the production information stored in the MES.
The company is looking to solve the current pain points of rapid prototyping, such as efficiency, pricing, lead times, and a lack of transparency in the manufacturing process, with RapidDirect’s instant quote platform, you can experience a user-friendly interface, design for manufacturing (DfM) analysis, and efficient order management.
Through the platform, customers are kept up to date with the progress of their order by automated email notifications at each stage of production, right up to delivery. The all-in-one order management feature provides users with real-time order tracking at their fingertips, while delivering transparency throughout the manufacturing process.
GETTING A QUOTE WITH LK-MOULD IS FREE AND SIMPLE.
FIND MORE OF OUR SERVICES:
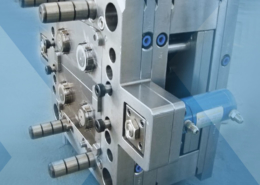
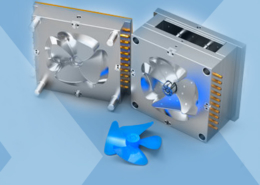
Plastic Molding

Rapid Prototyping
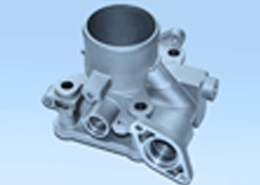
Pressure Die Casting
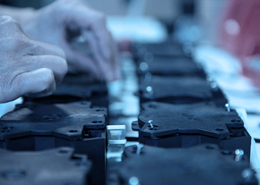
Parts Assembly
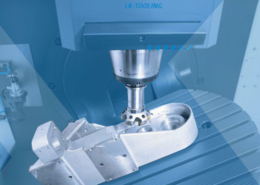