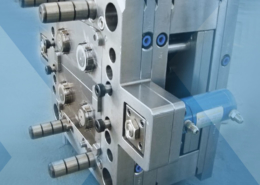
Advancements in Medical Device Plastic Molding: Pioneering Healthcare Innovation
Author:gly Date: 2024-06-08
Introduction:
Medical device plastic molding stands at the forefront of healthcare innovation, playing a pivotal role in the production of critical components for a wide range of medical applications. From intricate surgical instruments to implantable devices, plastic molding technologies have revolutionized the landscape of modern medicine, enabling the development of safer, more reliable, and cost-effective healthcare solutions. In this article, we delve into the intricate world of medical device plastic molding, exploring its significance, methodologies, and transformative impact on patient care.
1. Precision Engineering for Life-Saving Devices
The realm of medical device plastic molding demands unparalleled precision and reliability to ensure the safety and efficacy of healthcare interventions. With advancements in tooling design, injection molding techniques, and material science, manufacturers can produce complex components with micron-level accuracy and consistency. From microfluidic channels for diagnostic devices to intricate housing for implantable sensors, precision engineering lies at the heart of medical device molding, enabling the realization of cutting-edge healthcare technologies.
Furthermore, the integration of computer-aided design (CAD) and simulation tools facilitates virtual prototyping and design validation, minimizing time-to-market and mitigating potential risks associated with product development. By leveraging these advanced technologies, manufacturers can iterate on design concepts rapidly and optimize production processes to meet the stringent regulatory standards governing the medical device industry.
2. Material Selection and Biocompatibility
The choice of materials in medical device plastic molding is of paramount importance, given the critical role they play in ensuring patient safety and device performance. Biocompatibility, chemical resistance, and sterilization compatibility are among the key considerations driving material selection for medical applications. Thermoplastics such as polyethylene, polycarbonate, and ABS offer excellent mechanical properties, biocompatibility, and sterilizability, making them ideal candidates for a wide range of medical devices.
Moreover, the advent of advanced biomaterials and bioresorbable polymers has expanded the horizons of medical device design, enabling the development of implantable devices that degrade over time within the body. These materials, derived from natural sources or synthesized in the laboratory, offer unprecedented opportunities for tissue regeneration, drug delivery, and minimally invasive surgery, ushering in a new era of personalized medicine.
3. Regulatory Compliance and Quality Assurance
The medical device industry is subject to stringent regulatory oversight to ensure the safety, efficacy, and quality of healthcare products. Medical device plastic molding manufacturers must adhere to a myriad of regulatory standards and guidelines, including ISO 13485, FDA 21 CFR Part 820, and CE Marking requirements. Compliance with these regulations necessitates robust quality management systems, traceability protocols, and validation processes throughout the product lifecycle.
Furthermore, quality assurance measures such as process validation, risk management, and statistical process control (SPC) are integral to ensuring consistent product quality and performance. By implementing rigorous testing protocols and inspection procedures, manufacturers can detect and mitigate potential defects early in the production process, minimizing the risk of product recalls and adverse events.
4. Driving Innovation in Minimally Invasive Surgery
The rise of minimally invasive surgery (MIS) has transformed the landscape of surgical interventions, offering patients faster recovery times, reduced post-operative pain, and improved cosmetic outcomes. Medical device plastic molding plays a crucial role in enabling MIS procedures by facilitating the development of sophisticated instrumentation and surgical implants. From laparoscopic graspers and trocars to endoscopic cameras and stents, plastic-molded components are integral to the success of minimally invasive techniques.
Moreover, advancements in material science and manufacturing technologies have fueled the development of bioresorbable scaffolds and drug-eluting implants, further enhancing the efficacy and safety of MIS procedures. By harnessing the power of medical device plastic molding, healthcare professionals can deliver superior patient care and drive innovation in surgical interventions.
Conclusion:
In conclusion, medical device plastic molding stands as a cornerstone of healthcare innovation, driving advancements in precision engineering, material science, and regulatory compliance. By leveraging cutting-edge technologies and embracing a culture of continuous improvement, manufacturers can pioneer the development of life-saving medical devices that transform patient care. As we look towards the future, the potential for further innovation in medical device plastic molding remains limitless, promising a world where healthcare technologies empower clinicians and improve patient outcomes.
GETTING A QUOTE WITH LK-MOULD IS FREE AND SIMPLE.
FIND MORE OF OUR SERVICES:
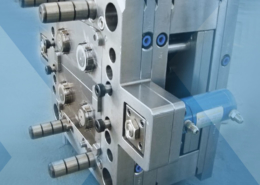
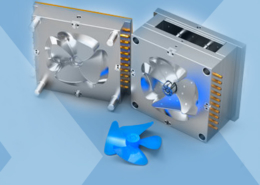
Plastic Molding

Rapid Prototyping
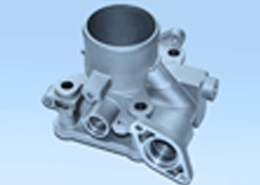
Pressure Die Casting
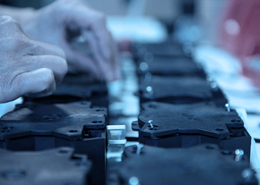
Parts Assembly
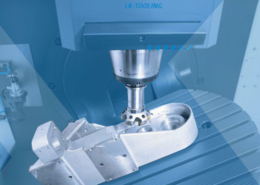