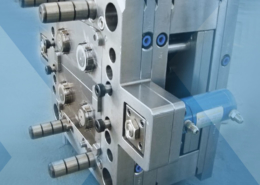
Medical Device Plastic Injection Molding: Revolutionizing Healthcare
Author:gly Date: 2024-06-08
Plastic injection molding has revolutionized the manufacturing processes in various industries, particularly in the healthcare sector. With the rise of medical device plastic injection molding, the landscape of healthcare delivery has been significantly transformed. This article delves into the intricacies of medical device plastic injection molding, exploring its importance, applications, challenges, and future prospects.
The Importance of Medical Device Plastic Injection Molding
Medical device plastic injection molding plays a pivotal role in modern healthcare by enabling the mass production of intricate medical devices with high precision and efficiency. Its significance lies in its ability to produce complex geometries, intricate designs, and tight tolerances, which are crucial for medical devices' functionality and performance.
Precision and Consistency
One of the key advantages of plastic injection molding in medical device manufacturing is its unmatched precision and consistency. This process allows for the production of components with minimal variation, ensuring uniformity across large production runs. The ability to maintain tight tolerances is essential for medical devices' reliability and performance.
Cost-effectiveness
In addition to precision, medical device plastic injection molding offers cost-effectiveness, making it an attractive option for manufacturers. By streamlining the production process and minimizing material waste, injection molding helps reduce manufacturing costs, ultimately leading to more affordable medical devices for patients and healthcare providers.
Material Versatility
Another advantage of plastic injection molding is its versatility in materials selection. Manufacturers can choose from a wide range of medical-grade polymers with different properties, such as biocompatibility, sterilization resistance, and chemical resistance. This flexibility allows for the production of medical devices tailored to specific applications and performance requirements.
Applications in Healthcare
The applications of medical device plastic injection molding are diverse and encompass various healthcare sectors, including:
Implantable Devices
Plastic injection molding is widely used in the manufacturing of implantable medical devices such as orthopedic implants, cardiovascular implants, and dental prosthetics. These devices require biocompatible materials and intricate designs, which can be efficiently produced using injection molding techniques.
Disposable Medical Supplies
Disposable medical supplies, such as syringes, IV catheters, and surgical instruments, are commonly produced using plastic injection molding. The high-volume production capabilities of injection molding make it ideal for manufacturing these disposable items, which are essential for infection control and patient safety in healthcare settings.
Diagnostic Equipment
Medical diagnostic equipment, including components for imaging devices, laboratory instruments, and diagnostic test kits, often rely on plastic injection molding for the production of housing, enclosures, and other critical components. The ability to achieve tight tolerances and complex geometries is crucial for the performance and accuracy of diagnostic equipment.
Challenges and Considerations
While medical device plastic injection molding offers numerous benefits, it also presents certain challenges and considerations that manufacturers must address:
Regulatory Compliance
Manufacturers must adhere to stringent regulatory requirements, such as FDA regulations in the United States and CE marking in the European Union, to ensure the safety and efficacy of medical devices produced through injection molding. Compliance with these regulations adds complexity to the manufacturing process and requires meticulous documentation and quality assurance procedures.
Material Selection and Biocompatibility
Selecting the appropriate materials for medical device injection molding is critical to ensure biocompatibility, sterilization compatibility, and long-term performance. Manufacturers must carefully evaluate the properties of medical-grade polymers and conduct thorough testing to verify their suitability for specific applications.
Design Complexity and Tooling
The design of medical devices for injection molding requires careful consideration of part geometry, mold design, and tooling considerations. Complex designs may necessitate the use of advanced molding techniques, such as multi-cavity molds or overmolding, which can increase production costs and lead times.
Future Directions and Innovations
Looking ahead, advancements in materials science, manufacturing technologies, and design optimization are poised to drive further innovation in medical device plastic injection molding. Some potential future directions include:
Advanced Materials Development
The development of new medical-grade polymers with enhanced properties, such as improved biocompatibility, antimicrobial properties, and biodegradability, holds promise for expanding the applications of injection molding in healthcare.
Additive Manufacturing Integration
The integration of additive manufacturing technologies, such as 3D printing, with traditional injection molding processes could enable the production of customized medical devices with complex geometries and patient-specific designs.
Automation and Industry 4.0
Automation and digitalization technologies, encompassing robotics, artificial intelligence, and data analytics, are transforming the landscape of injection molding manufacturing. Implementing Industry 4.0 principles can enhance production efficiency, quality control, and supply chain management in medical device manufacturing.
Conclusion
In conclusion, medical device plastic injection molding is a cornerstone of modern healthcare manufacturing, offering precision, cost-effectiveness, and material versatility. Its applications span across implantable devices, disposable medical supplies, and diagnostic equipment, driving innovation and improving patient outcomes. Despite challenges such as regulatory compliance and design complexity, ongoing advancements in materials science and manufacturing technologies promise to further elevate the capabilities of medical device injection molding, shaping the future of healthcare delivery.
GETTING A QUOTE WITH LK-MOULD IS FREE AND SIMPLE.
FIND MORE OF OUR SERVICES:
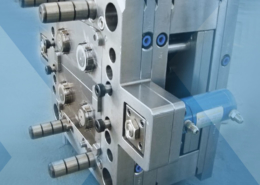
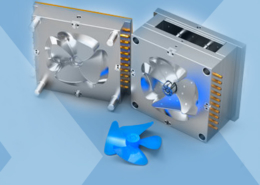
Plastic Molding

Rapid Prototyping
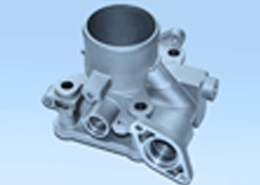
Pressure Die Casting
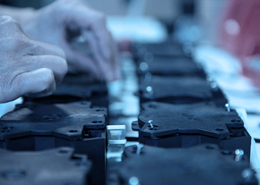
Parts Assembly
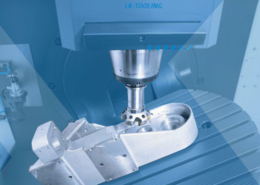