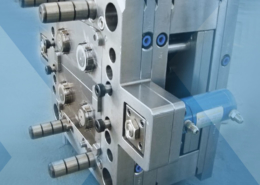
Plastic injection molding dies using hybrid additively manufactured 420/CX
Author:gly Date: 2024-09-30
“For decades, glass has often been the second choice when it comes to materials in manufacturing processes because its formation is too complicated, energy-intensive and unsuitable for producing high-resolution structures,” explains Rapp. “Polymers, on the other hand, have allowed all of this, but their physical, optical, chemical and thermal properties are inferior to glass. As a result, we have combined polymer and glass processing to quickly and cost-effectively replace both mass-produced products and complex polymer components with glass.”
When used in conjunction with 3D printed molds, the composite material enables the high-throughput production of complex glass components with previously impossible geometries. The team, led by Prof. Dr. Bastian Rapp from the university’s Laboratory of Process Technology, expects potential applications in everything from optical devices to solar technology and lab-on-a-chip medical devices.
Kotz adds, “We have also been able to show that micro-optical glass coatings can increase the efficiency of solar cells. This technology can now be used to produce cost-effective high-tech coatings with high thermal stability. There are a number of commercial opportunities for it.”
Dr. Frederik Kotz, group leader at the Laboratory of Process Technology and Chief Scientific Officer at Glassomer, states, “We see great potential, especially for small high-tech glass components with complicated geometries. In addition to transparency, the very low coefficient of expansion of the glass also makes the technology interesting. Sensors and optics work reliably at any temperature if the key components are made of glass.”
Further details of the study can be found in the paper titled ’High-throughput injection molding of transparent fused silica glass’. It is co-authored by Bastian Rapp, Frederik Kotz, Markus Mader et al.
For millennia, glass has been the go-to material for aesthetic, see-through parts. Today, the material is used in everything from bottles and windows to high-tech telecommunication devices. The shaping of glass components is predominantly based on processes such as melting, grinding, etching, and kiln casting – all of which are slow, energy-intensive, and severely limited in terms of geometric freedom.
Today, HWF uses additive manufacturing and is able to create the same structure by applying layers 250µm thick at a rate of 5000 mm³ per hour. The job can therefore be finished in just 24 hours at a laser output of only 400 watts. Time-consuming finishing by EDM or milling is significantly reduced.
Injection molding, on the other hand, is the leading technology in the polymer industry. It is both rapid and cost-effective, making it well suited to series production with a wide variety of part types. According to the Freiburg team, transparent glass has not been compatible with high-speed injection molding technology until now.
The company’s comprehensive portfolio of products is the outcome of unceasing efforts to build on and apply many years of practical experience in the fields of laser welding and cladding.
Development and manufacture of laser equipment in Germany for companies that include Siemens, Bosch, Geberit, Freudenberg, and General Electric.
Since founding O.R. Lasertechnologie GmbH in September 1997, Yhushua Resnik and Uri Resnik have steadfastly pursued the goal of developing new applications for lasers in materials processing and innovative laser technologies for a wide range of customers in the metal- and plastics-processing industries.
In the past, structures like this were built up layer by layer with wire-fed laser cladding to avoid the risks of cracks, deformation, and altered metallurgical properties. The welder took between 60 and 80 hours to complete the task.
When injected into a 3D printed mold, the material is initially a milky-white color, but can be converted into pure quartz glass via a heat treatment process. This can be done using far less energy than conventional glass melting, and the formed glass parts have a high surface quality so the need for further polishing is eliminated altogether.
The result is a crack-free, high-quality structure that is optimally fused with the base material and has a hardness of 45-65 HRC. Time-consuming preheating of the mold insert is no longer needed. The base material is affected much less than before, thus greatly reducing the risk of cracks and material undercut that conventional repair methods often cause. The mold insert is ready for reuse after just a short time.
Since the start of the 21st century, laser cladding has become established as a highly effective process for modifying and repairing injection molds and dies.
First a CAD file defining the addition is loaded into the ORLAS SUITE, a powerful CAD/CAM software solution from OR LASER. There it is sliced into layers and the optimal strategy determined. Then the coordinate system is calibrated with three characteristic reference points, and the laser parameters are transmitted to the system. All of the preparations take an average of about an hour to complete. The manufacturing process then takes place fully automatically.
Solutions for the automotive and aerospace, mechanical engineering, electrical, medical, plastics, and tool- and mold making industries
A team of researchers from the University of Freiburg, together with materials startup Glassomer, have developed a new polymer-based silica glass material compatible with injection molding technology.
The powder nozzle is available as an add-on for existing laser cladding systems that are AM 2.0-capable and can therefore be programmed with the CAD/CAM software of the ORLAS SUITE. “We are convinced that this technology will deliver considerable competitive advantages, especially for small and midsized companies,” says Markus Wolf, the head of R&D at OR LASER. “Our innovative powder nozzle lets a conventional system be upgraded in minutes, turning it into a powerful, cost-effective additive manufacturing tool.”
Material costs are also reduced, since the DMD process produces geometries that very closely approximate the final contours. Only a tiny amount of follow-up machining is then required.
To make the current work possible, the research team had to solve existing problems relating to material porosity and particle abrasion. In a bid to make the technology more environmentally-friendly, Rapp’s team also used water as a base material.
Elsewhere, at Lawrence Livermore National Laboratory (LLNL), researchers have previously used multi-material 3D printing, namely direct ink writing (DIW), to fabricate highly customized gradient refractive index (GRIN) glass optics. The technique allows for a number of optical functions to be programmed directly into flat glass components – functions that would otherwise require curved lenses.
Subscribe to the 3D Printing Industry newsletter for the latest news in additive manufacturing. You can also stay connected by following us on Twitter and liking us on Facebook.Looking for a career in additive manufacturing? Visit 3D Printing Jobs for a selection of roles in the industry.Featured image shows glass gears injection molded using the new Glassomer material. Photo via Glassomer.
The newly developed material is a special composite granulate designed in-house by the researchers, and it is moldable at a low temperature of just 130°C. There is also a liquid resin version of the material that is compatible with SLA-based 3D printing.
The combination of 3D printing and glass tends to be an eyebrow-raising topic, but there are a number of research institutions looking to advance the field. Scientists from the King Abdullah University of Science and Technology (KAUST) recently developed a new method of 3D printing photonic crystal fibers – a special type of optical fiber. The team constructed a purpose-built SLA-based 3D printer for the project, one that enabled the scientists to customize their optical fibers with previously impossible internal geometries.
In DMD, a powder nozzle coaxially feeds metal powder into the laser beam onto an existing surface. The process can be completely automated and even works with laser systems with an average output of only 300 watts. It can be used on three-dimensional surfaces and lends itself to a wide range of uses: enhancing surfaces, modifying shapes, and restoring damaged forming, punching, and injection molding tools and dies to a like-new condition.
Markus Fischer, the managing director of HWF, is enthusiastic: “Laser cladding is here to stay in tool and mold making. DMD has made us more productive by letting us take a different approach when molds change. We have firmly integrated it into our process and CAD/CAM landscape.”
Now a new additive manufacturing method is taking it to the next level: DMD with a coaxial powder nozzle. In contrast to conventional laser cladding, which usually requires a welder to feed filler wire almost entirely by hand, the new approach is fully automated and highly precise. This enormously boosts productivity. Especially for small and midsized companies, it affordably enhances existing equipment.
Kubi Sertoglu holds a degree in Mechanical Engineering, combining an affinity for writing with a technical background to deliver the latest news and reviews in additive manufacturing.
The laser system is also flexibly controllable while the object is being formed, which permits on-the-fly adjustment of the process parameters to meet changing requirements. For example, the laser intensity can be varied: beginning with fast build-up with a relatively high output and powder feed rate and then reducing both toward the end of the process to create surfaces that closely approach the final contours and thus minimize the required finishing work.
The enormous benefits of this additive manufacturing process have also won over the midsized company of HWF, a tool and mold making company in Eppertshausen, near Frankfurt, Germany. One of the challenges that HWF faces is that of building up a structure measuring 300 x 20 x 20 mm (i.e. with a volume of 120,000 mm³) on a typical mold material (AISI H11, one of the internationally most-used hot-working steels and extremely wear-resistant).
Direct metal deposition (DMD) can be up to 250-330% faster than manual laser cladding. New Additive Manufacturing 2.0 (AM 2.0)-capable laser welding systems can now be equipped with a recently developed powder nozzle from O.R. Lasertechnologie GmbH that permits fully automatic layerwise buildup. This solution holds enormous potential for tool and mold making applications at small and midsized companies.
GETTING A QUOTE WITH LK-MOULD IS FREE AND SIMPLE.
FIND MORE OF OUR SERVICES:
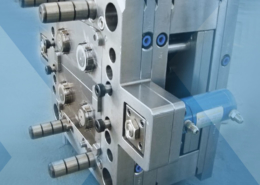
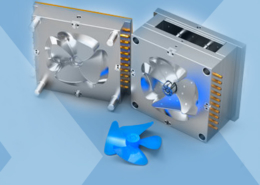
Plastic Molding

Rapid Prototyping
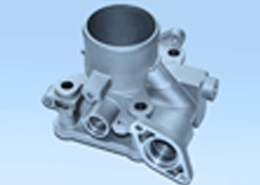
Pressure Die Casting
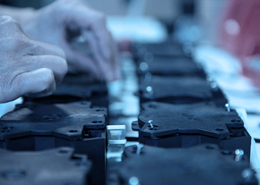
Parts Assembly
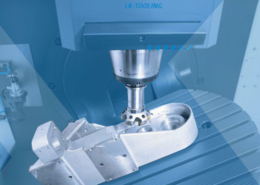