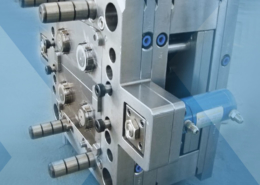
Plastic fantastic? Austrian company resurrects injection-molded cycles - product
Author:gly Date: 2024-09-30
In fact, injection moulding has a long history in bicycle manufacturing. One of the first was made from injection-molded Lexan in 1973. The Original Plastic Bike Inc had been founded in 1971, and took out magazine adverts, but it sold very few, if any, of its proposed products.
The turbocharger vanes must be able to withstand operating temperatures of 600–800ºC as well as be able to function at -30ºC. To meet these specifications, the vanes are made from HK30 steel alloy. In addition to the speed of production offered by MIM, the use of this process is also a benefit in its ability to manufacture with minimal material loss.
The benefits of an injection-molded cycle frame are obvious – manufacturing is swift (just pop them out of mold every minute or so), and they won’t rust. Complex shapes can also be achieved.
Built for its customer Garrett Motion, a global manufacturer of turbocharger systems, the turbo vanes are used in turbocharges destined for final customers such as Audi, Hyundai, Kia and Volkswagen.
So, if Plastic Innovation GmbH has truly figured out a way to mass-produce rideable, long-lasting, non-floppy injection-molded cycle frames it would be on to a winner. As reported by Cycling Industry News, the company has already won an award: its “bicycle of the future” concept bagged an Austrian Greenstart gong.
AFT, a member of ARC Group Worldwide, based Rétság, Hungary, recently celebrated the production of 183 million turbocharger vanes manufactured using its Metal Injection Moulding technology. AFT has produced these parts since the company was first established in 2001, and recognises MIM as the key to its success.
The company’s website is yet to be populated. However, from the awards information it appears that the company is seeking to mainly license its technology rather than make its own products. "The awareness of the new design options must first be created at the OEMs," says a company blurb.
Extensive MIM, CIM industry and sinter-based AM industry news, plus the following exclusive deep-dive articles and reports:
Reach a truly international audience that includes component manufacturers, end-users, industry suppliers, analysts, researchers and more.
However, many of the frames and plastic components snapped in use, most of the parts were proprietary and therefore difficult replace, and the Itera was said to be uncomfortable to ride. Nevertheless, it’s estimated that in the four years the Itera was made 30,000 units were sold around the world.
"Our services accompany the customer from the design to the manufacturing process in the sense of integral planning with the aim of placing the product on the market in the best possible way."
Graphics in the video above show that Plastic Innovation has been working wih Peugeot to produce CAD drawings of its proposed frames, which could be made from recycled plastics.
"The business model of Plastic Innovation GmbH combines two major innovations," claims the company. "The implementation of the bicycle industry’s new method of manufacturing frames using injection molding together with the innovative business model of rethinking bicycle design."
The free-to-access PIM International magazine archive offers unparalleled insight into the world of MIM, CIM and sinter-based AM from a commercial and technological perspective through:
The most famous plastic bicycle (if we discount carbon composite bicycle frames, that is) was the Itera bicycle of Sweden. This was born from a massive 1978 grant from the Swedish National Board for Technical Development. By 1980 a rideable bicycle – of sorts – was demonstrated by the Itera Development Center AB, and in the following year the first mass-produced Itera bikes were shown to prospective retailers and to the press.
Plastic Innovation of Austria is hoping to resurrect the 1980s idea of injection-molded cycle frames. Such frames used to snap, made by companies which flopped in more ways than one.
As well as turbocharger components, AFT’s MIM facility also manufactures other automotive components such as parts for fuel injectors and sensors. The final customers of these parts include brands such as Caterpillar, BMW, Citroën, Ford and Tesla. Utilising Metal Injection Moulding, these parts can be produced 20% cheaper – on average – than with precision casting, which represents a very serious price advantage, explains AFT.
Don't miss any new issue of PIM International, and stay up to date with the latest industry news. Sign up to our fortnightly newsletter.
Discover suppliers of these and more in our advertisers’ index and buyer’s guide, available in the back of PIM International.
GETTING A QUOTE WITH LK-MOULD IS FREE AND SIMPLE.
FIND MORE OF OUR SERVICES:
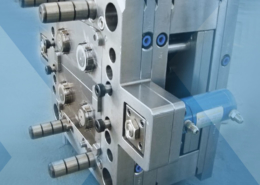
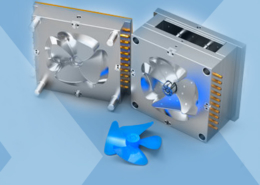
Plastic Molding

Rapid Prototyping
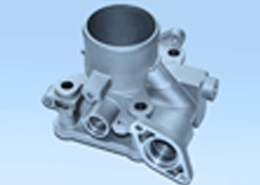
Pressure Die Casting
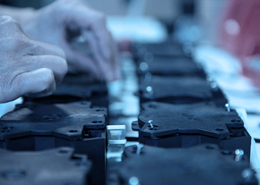
Parts Assembly
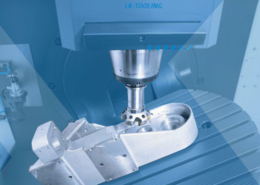