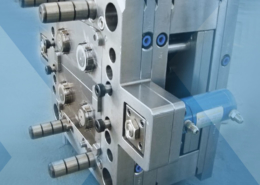
Understanding Injection Moulding Mould Cost: A Comprehensive Analysis
Author:gly Date: 2024-06-08
Injection moulding mould cost is a critical aspect of the manufacturing process that significantly impacts production efficiency, product quality, and overall profitability. In this article, we explore the various factors influencing injection moulding mould cost, providing insights into its importance, components, cost drivers, cost-saving strategies, and the impact of technological advancements. By delving into these aspects, readers will gain a comprehensive understanding of the complexities surrounding injection moulding mould cost and the strategies to optimize cost-effectiveness while maintaining high standards of quality.
Introduction: Unveiling the Importance of Injection Moulding Mould Cost
Injection moulding serves as a cornerstone of modern manufacturing, allowing for the mass production of intricate plastic components with unparalleled efficiency and precision. At the heart of this process lies the mould, which plays a pivotal role in shaping molten plastic into desired forms. The cost associated with injection moulding moulds encompasses various expenses, including design, materials, machining, and maintenance. Understanding the factors influencing mould cost is essential for manufacturers striving to optimize their production processes and maximize returns on investment.
Components of Injection Moulding Mould Cost
The cost of injection moulding moulds comprises several components, each contributing to the overall expense and complexity of the moulding process.
Design and Engineering Costs
The design and engineering phase involves conceptualizing the mould design, creating 3D models, and conducting feasibility studies. Skilled designers and engineers play a crucial role in developing mould designs that meet functional requirements while minimizing material usage and manufacturing complexity.
Material Costs
The selection of mould materials impacts both the performance and cost of injection moulds. High-quality materials, such as tool steel or aluminum, offer superior durability and heat resistance but come at a higher price point. Manufacturers must balance material costs with the desired lifespan and performance characteristics of the mould.
Machining and Tooling Costs
Machining and tooling expenses encompass the fabrication of mould components using CNC machining, EDM (Electrical Discharge Machining), or other manufacturing processes. The complexity of the mould design, precision requirements, and the choice of materials influence machining costs and lead times.
Maintenance and Repair Costs
Regular maintenance and timely repairs are essential for prolonging the lifespan of injection moulds and ensuring consistent product quality. Budgeting for ongoing maintenance costs, including cleaning, lubrication, and component replacement, is crucial for minimizing downtime and maximizing operational efficiency.
Factors Influencing Injection Moulding Mould Cost
Several factors contribute to the variability of injection moulding mould cost, making it essential for manufacturers to consider these factors when planning their production processes.
Complexity of Mould Design
The complexity of the mould design, including the number of cavities, part geometry, and surface finish requirements, directly impacts the cost of mould fabrication. Intricate designs with complex features may require specialized tooling and machining processes, resulting in higher costs.
Production Volume and Lead Time
The anticipated production volume and lead time requirements influence mould cost considerations. High-volume production typically warrants the use of durable, high-performance mould materials and advanced machining techniques to meet demand while minimizing per-unit costs.
Quality and Performance Requirements
The desired quality standards and performance requirements of moulded parts influence the selection of mould materials, machining processes, and maintenance protocols. Investing in high-quality moulds upfront can yield long-term cost savings by minimizing defects, reducing downtime, and enhancing product consistency.
Cost-Saving Strategies and Technological Advancements
Advancements in technology and innovative strategies offer opportunities for manufacturers to optimize injection moulding mould cost and enhance operational efficiency.
Utilization of Advanced Materials and Technologies
The adoption of advanced materials, such as high-performance tool steels and engineered plastics, enables manufacturers to achieve superior mould performance and longevity. Additionally, advancements in machining technologies, such as additive manufacturing and high-speed milling, contribute to cost savings and lead time reduction.
Design Optimization and Simulation Tools
Utilizing design optimization and simulation tools allows manufacturers to iteratively refine mould designs, identify potential issues, and optimize performance parameters before fabrication. By simulating various scenarios and analyzing virtual prototypes, manufacturers can minimize design iterations, reduce material waste, and mitigate costly errors during production.
Strategic Supplier Partnerships
Establishing strategic partnerships with reputable mould suppliers and service providers can lead to cost savings through volume discounts, streamlined communication, and access to specialized expertise. Collaborating with suppliers early in the design phase enables manufacturers to leverage their insights and recommendations for cost-effective mould solutions.
Conclusion: Maximizing Value and Efficiency
In conclusion, injection moulding mould cost is a multifaceted aspect of manufacturing that requires careful consideration and strategic planning. By understanding the components, factors, and cost-saving strategies associated with injection moulding moulds, manufacturers can optimize their production processes, enhance product quality, and maximize returns on investment. As technology continues to evolve and market demands evolve, embracing innovation and adopting best practices in mould design, material selection, and production techniques will be paramount for maintaining competitiveness and sustainability in the dynamic landscape of injection moulding manufacturing.
GETTING A QUOTE WITH LK-MOULD IS FREE AND SIMPLE.
FIND MORE OF OUR SERVICES:
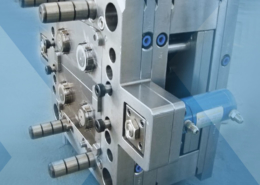
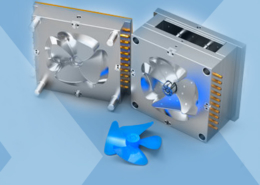
Plastic Molding

Rapid Prototyping
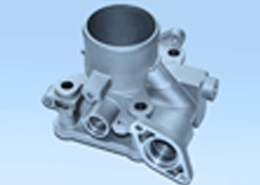
Pressure Die Casting
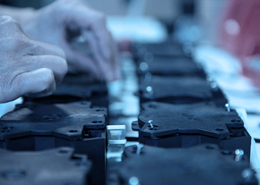
Parts Assembly
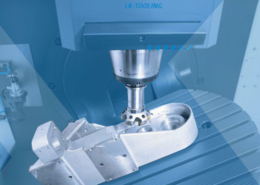