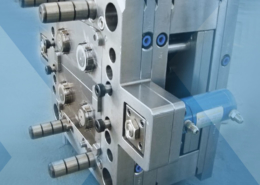
Injection moulding manufacturers play a pivotal role in the manufacturing indust
Author:gly Date: 2024-06-08
Processes
Injection moulding manufacturers employ sophisticated processes to transform raw materials into precise components. The process begins with the design of moulds, followed by material selection and preparation. Then, the material is melted and injected into the mould cavity under high pressure. After cooling and solidification, the mould opens, and the finished part is ejected. This cycle repeats continuously, ensuring efficient production with minimal waste.
The precision and repeatability of injection moulding make it ideal for mass production of intricate parts with tight tolerances. Manufacturers utilize advanced machinery and automation to optimize cycle times and maintain consistent quality throughout production runs.
Applications
Injection moulding manufacturers serve diverse industries, including automotive, electronics, medical, consumer goods, and packaging. In the automotive sector, they produce interior and exterior components, such as dashboards, bumpers, and trim panels. In electronics, they manufacture housings, connectors, and casings for devices ranging from smartphones to industrial machinery.
Moreover, injection moulding is prevalent in the medical field for producing disposable syringes, vials, and surgical instruments. In the consumer goods sector, manufacturers produce a wide range of products, including toys, kitchenware, and household appliances. Additionally, packaging companies rely on injection moulding for producing bottles, caps, and containers for food, beverages, and cosmetics.
Challenges
Despite its many advantages, injection moulding faces several challenges, including material selection, design complexity, and tooling costs. Manufacturers must carefully choose materials that meet the required performance criteria while considering factors such as durability, flexibility, and chemical resistance.
Furthermore, complex part geometries and intricate mould designs can pose challenges in terms of tooling and production feasibility. Ensuring proper cooling and venting within the mould is essential to prevent defects such as warping, sink marks, and air traps.
Moreover, tooling costs can be substantial, particularly for high-precision moulds with intricate features. Manufacturers must balance these expenses with the expected production volume and product lifespan to determine the overall cost-effectiveness of the project.
Innovations
To address these challenges and enhance efficiency, injection moulding manufacturers continually innovate in various aspects of the process. Advanced materials, such as bioplastics and composite resins, offer improved performance characteristics while reducing environmental impact.
Furthermore, advancements in mould design and simulation software enable manufacturers to optimize part geometry, reduce cycle times, and minimize material waste. Additive manufacturing techniques, such as 3D printing, are also being integrated into injection moulding processes, allowing for rapid prototyping and on-demand production of tooling components.
Additionally, automation and robotics play a significant role in streamlining production workflows and improving consistency and repeatability. From automated material handling to robotic part inspection, these technologies contribute to higher throughput and quality control in injection moulding manufacturing.
Conclusion
In summary, injection moulding manufacturers play a vital role in modern manufacturing, providing cost-effective solutions for a wide range of industries. Despite facing challenges such as material selection and tooling costs, ongoing innovations in processes, materials, and technologies continue to drive the industry forward.
As demand for precision-engineered components grows across various sectors, injection moulding manufacturers must remain agile and adaptive to meet evolving market needs. By embracing innovation, collaboration, and sustainable practices, they can continue to deliver high-quality products that shape our everyday lives.
Through ongoing research and development, injection moulding manufacturers can further enhance efficiency, reduce environmental impact, and unlock new possibilities for future applications. By staying at the forefront of technological advancements, they can continue to drive progress and innovation in the manufacturing industry.
GETTING A QUOTE WITH LK-MOULD IS FREE AND SIMPLE.
FIND MORE OF OUR SERVICES:
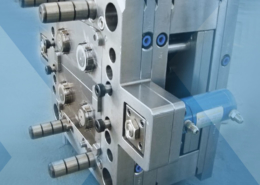
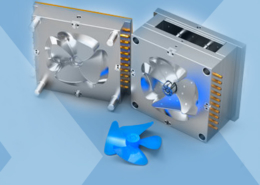
Plastic Molding

Rapid Prototyping
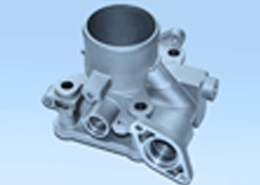
Pressure Die Casting
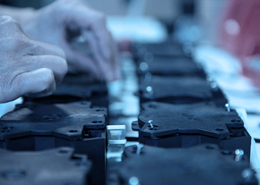
Parts Assembly
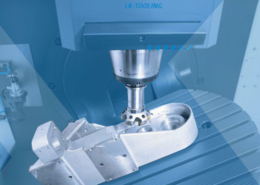