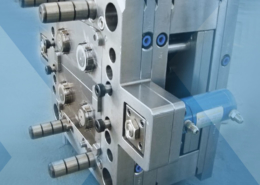
New PE Resins Reduce Roto-Molding Cycle Times and Costs - polyethylene molding
Author:gly Date: 2024-09-30
With this expansion, Kreate adds 500,000 square feet of manufacturing and distribution space, 30 injection molding machines ranging from 500 to 3,000 tons, and 160 skilled associates. This move is projected to add more than $150 million in annual revenue, said Kreate.
Sprint technology uses additive manufacturing to produce a mold that is injected with the KryonMAX compound in the same manner as a metal tool. These rapid, cost-effective prototypes allow for rapid design iterations while testing under operating conditions.
MCAM continues to innovate in materials science, and it now offers materials with tensile strengths that exceed 60,000 psi (414 MPa), as shown in the video. In addition to improved processability, KyronMAX compounds exhibit mechanical properties that surpass conventional glass- and carbon-fiber-filled thermoplastic systems at similar fiber loadings. This allows for a reduction in filler loading, thereby increasing material strain and allowing the molded part to yield rather than fracture. These compounds are now being used to replace aluminum and steel in structural applications.
Metal replacement has become a strategic element in most major OEM strategies for lightweighting and sustainability. KyronMAX technology has raised the bar for performance of injection moldable plastics and provides customers the opportunity to replace metal parts with plastic, said MCAM. KyronMAX parts that replace metal components on vehicles contribute to lower overall weight, which translates into a reduction of fuel consumption and CO2 emissions. Part cost can also be significantly reduced through the consolidation of several metal components into a single thermoplastic part by eliminating secondary operations during assembly.
The Informa Markets Engineering network of B2B media sites includes Design News, Battery Technology, Medical Device & Diagnostic Industry (MD+DI), Packaging Digest, PlasticsToday, and Powder & Bulk Solids.
A quarter-turn latch found in the galley of a commercial aircraft illustrates how even a small weight reduction can have a large impact. Typically made from machined aluminum, this latch is molded using KyronMAX S-6230, a carbon-fiber-reinforced PEI compound. Switching to the thermoplastic provided a 45% weight reduction while still meeting mechanical and flammability requirements. MCAM’s exclusive Sprint technology — a platform for rapid injection molding of functional parts — was used to rapidly prototype components prior to full production.
When it was introduced in 2014, the KryonMAX family of high-strength injection moldable thermoplastic compounds was designed to bridge the gap between traditional thermoplastics and carbon-fiber composites. “KyronMAX combines the best of both worlds by allowing engineers to injection mold high strength, carbon-fiber-reinforced thermoplastics in minutes with strengths that are comparable to metal,” said Dave Wilkinson, Technology Director for Mesa, AZ–based MCAM. “Combining specialized short carbon fiber and proprietary sizing technology produces molded parts that have significantly higher mechanical performance than was previously possible using long-fiber technology (LFT).”
“KyronMAX compounds can significantly change the way engineers approach part design, manufacturing, and assembly,” said Wilkinson. “The combination of KyronMAX’s performance with MCAM’s proprietary high-pressure molding technology is now able to produce the highest strength structural components made from injection molded thermoplastics.”
A key part of Kreate's expansion strategy across the United States, the addition of the Texas operation enhances Kreate's manufacturing capabilities and strengthens its logistics network, enabling faster delivery of innovative products nationwide.
Kreate, a design engineering company based in Findlay, OH, has acquired a supplier of plastic injection molded components for the automotive industry located in Georgetown, TX.
In January of this year, Mitsubishi Chemical Advanced Materials (MCAM) expanded its KyronMAX product line beyond performance-grade polymers, such as PEEK and PEI, by adding engineering polymers, including polycarbonate, nylon, polyphthalamide (PPA), and even polypropylene. These new compounds unlock a wider range of applications in the automotive and mobility, recreational, electronics, and medical industries.
KyronMAX can be compounded into any polymer. If an application requires the cost and property balance of nylon 6/6, for example, MCAM can formulate a nylon 6/6 KyronMAX compound that is stronger than anything currently available on the market. This technology ultimately offers customers the flexibility of selecting any polymer they want and combining it with KyronMAX fiber to create the strongest moldable compound in that category.
The Georgetown facility, known for its advanced manufacturing processes and commitment to excellence, aligns with Kreate's mission to deliver products like outdoor furniture, deck and dock systems, raised garden beds, utility sinks, wheelbarrows, and other everyday products to its retail partners.
This expansion is a step toward delivering our products within a day's transit anywhere in the United States,” said Nickolas Reinhart, founder and owner of Kreate. “We aim to build on Georgetown's foundation while introducing new product innovation, customer diversification, and sustainable manufacturing practices."
Until she retired in September 2021, Clare Goldsberry reported on the plastics industry for more than 30 years. In addition to the 10,000+ articles she has written, by her own estimation, she is the author of several books, including The Business of Injection Molding: How to succeed as a custom molder and Purchasing Injection Molds: A buyers guide. Goldsberry is a member of the Plastics Pioneers Association. She reflected on her long career in "Time to Say Good-Bye."
Kreate uses 3D-printing technology and sustainable manufacturing practices to set industry standards for sustainability, quality, efficiency, and cost-effectiveness, said the news release.
The compounds from Mitsubishi Chemical Advanced Materials are being used to replace aluminum and steel in structural applications.
GETTING A QUOTE WITH LK-MOULD IS FREE AND SIMPLE.
FIND MORE OF OUR SERVICES:
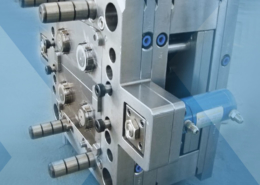
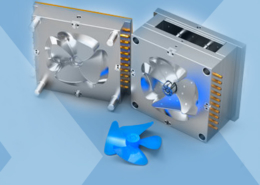
Plastic Molding

Rapid Prototyping
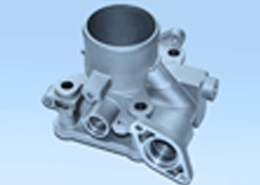
Pressure Die Casting
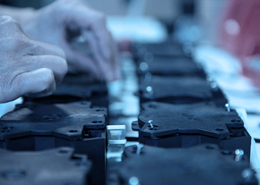
Parts Assembly
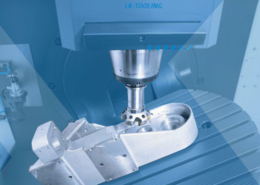