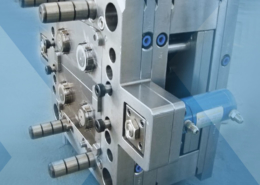
New "injection moulded" technology could revolutionise vinyl manufacturing - pvc
Author:gly Date: 2024-09-30
Nexus also developed the ServoMix X20 LSR dosing system, which ensures air-free dosing, even in very small quantities, of the liquid silicone rubber. Networking via OPC UA and MES authentig by TIG ensures full process data monitoring and complete traceability down to the individual cavity level.
Polypropylene is used in a variety of applications, including plastic packaging, machinery and equipment parts, and fibers and textiles. Extrusion, injection, and stretch are the various technologies used in blowmolding plastics for packaging, consumables, electronics, automotive and transport, building and construction, medical, and other applications.
Success stories at the seminar included the biodegradability of proprietary bioplastic material; biopolymer solutions for sustainable agriculture; and a method for measuring biodegradation in compost, fresh and waste waters, soil, and marine environments.
For the packaging sector, AIMPLAS presented results of projects that included biodegradable barrier packaging made from food waste, plastic film derived from coffee waste, active packaging that extends the shelf life of cheese and is made from cheese-industry waste, and cartridges for 3D food printing.
Because of the tie-bar-less design, multi-cavity molds may be used on smaller injection molding machines than is customary, providing cost savings without affecting productivity per unit of area, according to Engel.
Nexus designed the 64-cavity mould with a demolding device to enable the end-of-arm tooling to easily grip parts. To ensure precise fill control, the cold runners in the mold are equipped with electric needle shut-off systems. Nexus’ Timeshot technology controls the fill quantity as a function of injection time. Each cavity can be controlled individually, even in molds with up to 128 cavities.
Engel’s iQ weight control smart assistance system continuously analyzes the injection profile and readjusts quality-relevant process parameters in the same cycle whenever deviations occur.
Incorporating tie-bar-less servo-hydraulic clamping and electric injection units, the e-victory model machine on display supports low-flash, rework-free processing of low-viscosity materials. The moving platen precisely follows the mold as the clamp force builds up, resulting in optimal platen parallelism, said Engel. Patented force dividers ensure that the clamping force is distributed evenly over the entire platen face. Even in large multi-cavity molds, the same clamping force is applied to cavities near the outer edge of the platen as those near the centre.
The easix articulated robot requires little headroom and connects the injection molding machine with camera-based quality control and the discharge station. Additional process units can be added retroactively, integrated upstream or downstream of the injection molding process.
For instance, in 2020, Comar, a US manufacturer and designer of innovative plastic solutions, announced locating a custom facility in Rancho Cucamonga, CA. The 230,000-square-foot facility is Current Good Manufacturing Practice regulation (cGMP)-compliant, ISO 13485-certified, and FDA-registered, with dedicated injection blowmolding, injection-stretch blowmolding, and injection-molding cells.
Production of the 7-mm-diameter blades is fully automated in a 64-cavity mold with an Engel easix articulated robot and integrated vision control system.
Companies are investing in research and development to produce new industrial plastics to keep up with market competitiveness and meet evolving end-user demands.
This marks the first time that Engel is demonstrating a networked injection molding machine and LSR dosing unit via OPC UA in line with the Euromap 82.3 standard at a trade show.
The global blow-molded plastics market grew from $89.39 billion in 2022 to $92.93 billion in 2023 at a compound annual growth rate (CAGR) of 4.0%. The blow-molded plastics market is expected to grow to $108.75 billion in 2027 at a CAGR of 4.0%, according to a report published in February by Reportlinker. The market consists of sales coveringcompound blowmolding and compression blowmolding.
In October 2021, Recycler EFS-plastics Inc., a Canada post-consumer plastics recycler with a focus on processing bales of low-value plastics, acquired Exi-Plast Custom Moulding for an undisclosed amount. Through this acquisition, EFS can directly manufacture finished products with high levels of post-consumer recycled plastic for its customers. Exi-Plast Custom Moulding is a Canadian company that provides custom plastic molding services, particularly in blow-molded solutions for designers, manufacturers, and distributors.
At stand C58 in hall 15 an e-victory injection molding machine with smart digital assistance supported by Nexus’ mold and plasticizing technology will produce LSR blade valves measuring 7-mm in diameter. Production is fully automated in a 64-cavity mold with an Engel easix articulated robot and integrated vision control system.
Blade valves are used in a range of applications, from automotive to medical technology, and in all cases the injection molding process must meet strict consistency parameters. At K 2022, Engel and partner company Nexus Elastomer Systems will demo a fully automated production cell molding liquid silicone rubber (LSR) blade valves that achieves consistent quality in a cost-effective manner.
The new facility offers a full-service mold prototyping lab as well as a specialized mold sample and development machine, allowing customers to quickly move from concept through design, prototype, and full production.
Asia-Pacific was the largest region in the blow-molded plastics market in 2021 and is expected to remain the largest through the forecast period.
The process data of the dosing unit are available during production in the CC300 control system of the injection molding machine and can be used for even more precise process monitoring and continuous optimization. The dosing parameters are stored in the mold's part data record, making them immediately available at the machine control when the mold is set up again.
Major types of blow-molded plastics are polypropylene, acrylonitrile butadiene styrene (ABS), polyethylene, polystyrene, polyvinyl chloride PVC, PET, and others. Polypropylene (also known as propane or propylene) is a tough, rigid, crystalline thermoplastic derived from the monomer propane or propylene.
Producing hollow plastic products from thermoplastic materials is a quick manufacturing solution and offers versatile products with broad industrial appeal. Markets include food suppliers, medical and pharmaceutical companies, and others.
GETTING A QUOTE WITH LK-MOULD IS FREE AND SIMPLE.
FIND MORE OF OUR SERVICES:
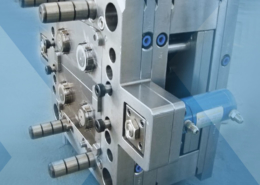
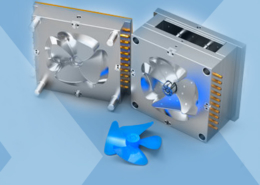
Plastic Molding

Rapid Prototyping
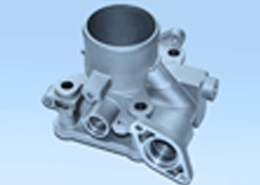
Pressure Die Casting
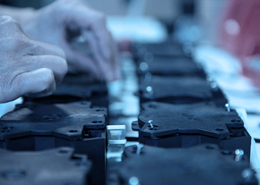
Parts Assembly
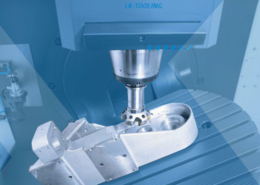