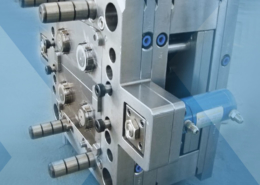
Multi-Material Printing Enables Low Cost Silicone Prototypes - prototype plastic
Author:gly Date: 2024-09-30
Geoff Giordano is a tech journalist with more than 30 years’ experience in all facets of publishing. He has reported extensively on the gamut of plastics manufacturing technologies and issues, including 3D printing materials and methods; injection, blow, micro and rotomolding; additives, colorants and nanomodifiers; blown and cast films; packaging; thermoforming; tooling; ancillary equipment; and the circular economy. Contact him at [email protected].
Added Christopher Navratil, CTO of Alltrista's parent company: "We were determined to be the first manufacturer to run a system with 128 cavities in under two seconds. In Netstal, z-moulds, and Intravis, we have found the best system partners for this project. Each company is a leader in its field, and the combination is unbeatable. With our 128-cavity systems, we produce more efficiently than ever before, can deliver at any time, and inspire our customers. This has given us an enormous competitive advantage."
Injection-molded silicone parts were produced within two days, allowing early verification of key design and performance aspects.
Certified to ISO 13485, Denmark-based SPT Vilecon describes itself as a fully integrated provider of development and manufacturing services to the medical device industry. It offers in-house tool making and injection molding along with other manufacturing services to companies in northern Europe.
Robust and valid prototyping and verification are key to minimizing cost, time, and risk factors in developing medical devices, said SPI Vilecon. FIM is a new toolbox for medical device companies seeking to accelerate their innovation and obtain early verification of part performance and moldability, added the company.
SPT implemented Nexa3D’s Freeform Injection Molding (FIM) technology to help customers shorten time-to-market on complex medical devices in demanding medical-grade materials and to expand on the range of materials that can be quickly and reliably used in prototyping and early device test manufacturing.
The patented FIM process uses high-speed Nexa3D printers and xMOLD resin to print injection molding tools that are compatible with thousands of off-the-shelf injection molding materials, including reinforced high-performance feedstocks. The process reduces design, iteration, and validation cycles using end-product materials to a matter of hours rather than weeks.
Design input collected from the first tests was integrated in a second iteration that took only a couple of hours to complete. By contrast, conventional metal tooling would have taken more than six weeks to design and procure, and the adjustments needed for the second iteration would have taken an in-house tool-shop a week to complete.
A supplier of development and manufacturing services to medical device OEMs used Freeform Injection Molding from Nexa3D to accelerate time-to-market and slash prototyping costs for a complex silicone-based IV device. SPT Vilecon explained the process in a recent press release.
Based on input collected from the first two iterations, the design of the silicone part was approved and manufacturing of a metal tool was initiated with full confidence of part moldability and performance. The in-house tool shop built the final metal tooling in four weeks without iterations.
Editor in chief of PlasticsToday since 2015, Norbert Sparrow has more than 30 years of editorial experience in business-to-business media. He studied journalism at the Centre Universitaire d'Etudes du Journalisme in Strasbourg, France, where he earned a master's degree.
In the NPE demonstration, finished caps will travel through an Intravis vision-inspection system. The system executes 360-degree inspection of the closures to an accuracy of hundredths of a millimeter using nine high-resolution cameras.
Netstal’s CAP-Line 4500 is identical to two production systems being used by Alltrista, a contract manufacturer based in Greer, SC. The line features an all-electric clamping unit with 4,500 kN of force and a dry cycle time of 1.4 seconds. An optimized barrier screw allows for a smaller injection unit with higher plasticizing performance and better homogenization, Netstal expained.
The 3D-printed molds for the first and second iterations cost less than €2,000 combined. And the technology enabled a two-day design cycle, which is more than 90% faster than conventional metal tooling.
SPT Vilecon said it has begun expanding the range of injection mold prototyping with silicone, metal, and ceramic materials to provide medical device manufacturers with an even wider selection of product development and verification services.
Overall, Netstal’s CAP-Line also fits in a smaller overall space — 538 square feet — and uses about 12% less electricity than competing machines running 96-cavity molds, Kogler said.
Medical device manufacturers are tasked with developing elaborate test protocols to ensure that the product in development is safe and meets essential requirements. If these tests are conducted late in the development process, the more onerous and risky they become. SPT Vilecon often works with silicone, a material that is extensively used in medical applications because of its chemical resistance, mechanical performance, and biocompatibility. However, silicone parts are notoriously difficult to prototype and test, since most grades need to be injection molded to achieve their full performance potential, said the company. FIM enabled SPT Vilecon to offer an alternative to a customer developing an intravenous (IV) silicone product — the use of 3D-printed tooling to perform early design and material verification at a fraction of the cost of conventional methods.
Freeform Injection Molding technology from Nexa3D compresses design, iteration, and validation cycle times into a matter of hours rather than weeks.
A 128-cavity mold will produce 26-mm water closures in a cycle time of 1.9 seconds in a live experience at Netstal’s booth at NPE 2024.
"With the new CAP-Line concept, we are aligning our portfolio even more closely with our customers' applications,” he noted. “Closure manufacturers benefit from a customized system, while pre-configuration can speed up the consultation and quotation process so that delivery times for the machine are as short as possible."
"Alltrista is the first in the world to produce with 128 cavities and a cycle time of 1.9 seconds,” said Horst Kogler, head of Netstsal’s caps and closures business unit. “They produce more than 3.1 billion closures with two lines [annually]. More output per square meter of production area is currently not possible."
The mold, produced by Austria’s z-moulds, is as small and light as a 96-cavity mold and fits into the injection molding machine with a smaller column distance. Cycle time is reduced by the smaller design, which also requires moving less mass. Alltrista has cut the weight of its enclosures by 25%; with 3.1 billion closures produced annually, that means more than 2 million pounds less resin used – about the weight of 160 African Bush elephants, the company said.
GETTING A QUOTE WITH LK-MOULD IS FREE AND SIMPLE.
FIND MORE OF OUR SERVICES:
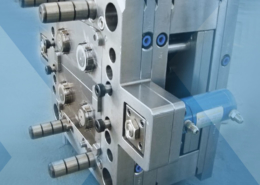
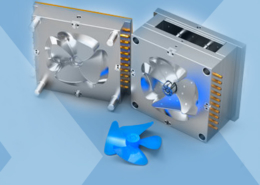
Plastic Molding

Rapid Prototyping
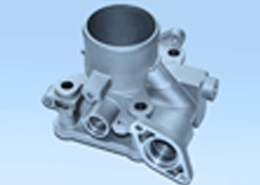
Pressure Die Casting
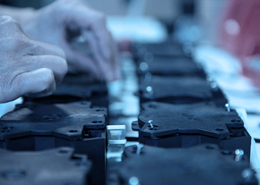
Parts Assembly
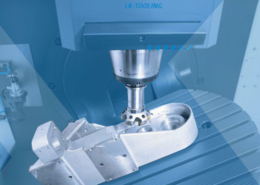