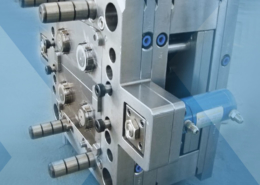
Mueller/Tecnoplast invests in WITTMANN injection moulding machines - plastic mou
Author:gly Date: 2024-09-30
Barbara Honer is a painter and fiber artist from Pelican Rapids, who's intrigued by plastic. She makes polished jewelry and signs, and is experimenting with free form bowls. She’s found plastic to be a challenging medium to work with as she blends colors and different types of plastic waste.
The Otter Tail County waste educator, Walters, said the pandemic was a challenging time to start a public workspace, but she and a handful of local artists spent the past few months working out the bugs in the process and she's now scheduling training classes for people who want to use the makerspace.
“You put it in the hopper, in the injector and you don't really know how it's going to come out,” she said. “So it's always exciting to see what the end product looks like. And sometimes I don't know exactly what I'm going to do with it until it comes out. And sometimes it tells me what to do with it.”
"Anybody can do it. I mean, if you can use a hot glue gun, you can use a plastics lab," said Zachmann, a Fergus Falls metal sculptor. "And we have, so far I think, the most complete one in the entire Midwest, and it's here in my own little town!"
Thanks to the design freedom afforded by injection molding, VESTAKEEP Fusion–based cages can be tailored to patient-specific anatomies and different surgical techniques. The cage models show the design diversity in the interlocks and in the cavities for ossification. In addition, the design facilitates instrument guidance during surgery and enables minimally invasive, patient-friendly surgical techniques.
When breaking news happens, MPR News provides the context you need. Help us meet the significant demands of these newsgathering efforts.
"Things like pharmacy pill bottles that are that clear orange color, and it's transparent and has that golden hue, all my friends are saving all their medication bottles for me now, so that way I can bring them here and shred them and turn them into things."
Zachmann used his metal working skills to build an oven that can hold larger molds so people can make flower pots or stepping stones.
"We tested VESTAKEEP Fusion on injection molding machines in the cleanroom and found that it was very easy to process," said Samaplast CEO Stefan Okle in a prepared statement. "Thanks to the excellent exchange with Evonik, we were able to produce a prototype within 10 days." Previously, tool development alone had taken eight to 10 weeks. With rapid prototyping, this process can be shortened considerably.
"What I'm looking for is a movement that can be contagious, where other people in the community can see what we're doing and think ‘well I can do that, too. I can make my own paving stones for my garden and I can recycle my own plastic waste into something,’” said Honer.
The $13,000 cost was funded by Otter Tail, Pope and Douglas counties, the West Central Initiative and Springboard for the Arts.
Experimenting with melted plastic and molds has changed how Zachmann recycles, and what he saves from the recycling bin.
Much of the plastic dumped in recycling containers in Otter Tail County, Minn., is shipped away to be turned into plastic lumber.
"I am practicing to make a Napoleon in pink. It's a good color on him," said Zachmann, prying apart the mold to show off the pink general.
But in a small room tucked in the corner of the recycling facility, Carl Zachmann is making something entirely different. He holds a small mold for making tin soldiers while a machine pumps it full of pink gooey plastic.
"Because it is a little unique and it's the first one of its kind in Minnesota for sure, it might draw people from all over the state and possibly even from surrounding states,” said Otter Tail County waste educator Cedar Walters. “And so we're hoping that it becomes a kind of a regional community and people can come visit and see what it's all about."
"Implant manufacturers were missing a PEEK material that fuses with bone cells and, thus, accelerates healing," said Marc Knebel, Head of the Medical Systems Market Segment at Evonik. "We are closing this gap in the market with VESTAKEEP Fusion and offering an alternative to titanium, stainless steel, or cobalt-chromium implants."
"There's lots of things people could do that would be very marketable,” she said. “So this is showing people what's possible, showing them the model, giving them those resources, and hopefully some people will jump off with it from there."
To demonstrate the medical potential of the technology, Evonik and Samaplast have produced prototypes of intervertebral implants, known as cages or spacers, which are used to fill the disc space in the spine following its removal due to disc degeneration. "We have produced a cage that contains all the details, such as serrations, threads, and apertures, that are relevant for spinal implants," explained Okle.
Evonik is also developing a 3D-printable VESTAKEEP Fusion filament that can be processed via additive manufacturing using fused filament fabrication technology.
Until now, it has been virtually impossible to manufacture implants from polymer compounds with bioactive particles by injection molding, because a thin polymer layer usually forms on the surface, preventing the implant from growing in, explained Evonik in a press release. VESTAKEEP Fusion's specially configured microparticles and their homogeneous distribution, however, allow the formation of functional biphasic calcium phosphate (BCP) additives on the surface of injection-molded components. The additives allow bone cells to adhere to the implant more quickly and promote osteo-integration between the bone and implant.
The small amount of plastic used in this space won’t make a dent in plastic recycled in Otter Tail County. Most will still be shipped away to be reused, but this small room in the corner the recycling center might just spark some creative new uses for plastic waste.
A collaboration between Evonik and Swiss plastics processor Samaplast results in an alternative to titanium, stainless steel, and cobalt-chromium implants.
There is a steep learning curve, said Walters, and they've developed techniques through trial and error. Some plastics melt better than others. Some create a smooth surface while others are textured. Recycled plastic totes in bright colors are a favorite, and plastic bags create a marbled effect when mixed with other plastic.
With VESTAKEEP Fusion, Evonik is introducing a new product line of next-generation PEEK-based implant materials that accelerate bone fusion and convalescence. In vitro studies document a more than 30% increase in cell attachment and cell proliferation, according to Evonik. In preclinical tests, histological examination reveals a dense network of newly formed osteoblasts at the bone-implant interface. Bone histo-morphometry shows an approximately twofold increase in bone apposition. Moreover, pull-out tests demonstrate a more than twofold increase in implant fixation, said the company.
"It does change how you view your waste,” said Walters. “That's really the power of this project — getting people to notice what is happening with their waste. It changes your perspective and you start to think, 'Oh, what could that be?' instead of just viewing it as disposable."
Walters has more molds on order, and said people can buy or build their own molds. She's excited to see artists and entrepreneurs use the plastics lab as an idea generator.
The Lakes Area Mix Workspace is a small-scale version of a large plastic reuse operation. The open source machines were purchased from a company in the Netherlands called Precious Plastics.
Initially offered in granule form and as semi-finished products, VESTAKEEP Fusion can be milled, compression molded, extruded, and injection molded, said Evonik. The compound was optimized for injection molding in close cooperation with Samaplast AG.
German chemicals company Evonik and Swiss plastics processor Samaplast have collaborated in the development of an osteo-conductive PEEK-based material compatible with injection molding. Spinal implant prototypes have been molded to illustrate the processing properties of the new high-performance polymer, VESTAKEEP Fusion.
There's a shredder to chop the plastic into small pieces, and machines to heat it to about 400 degrees, so it can be formed by molds or shaped freehand as the melted plastic flows from an extrusion machine like hot toothpaste from a tube.
GETTING A QUOTE WITH LK-MOULD IS FREE AND SIMPLE.
FIND MORE OF OUR SERVICES:
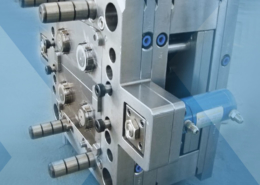
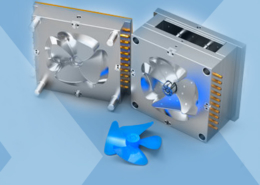
Plastic Molding

Rapid Prototyping
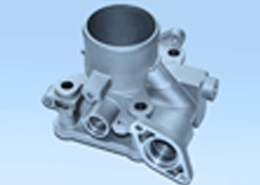
Pressure Die Casting
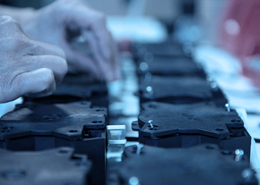
Parts Assembly
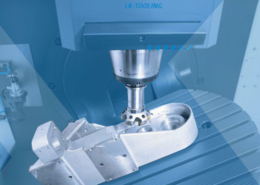