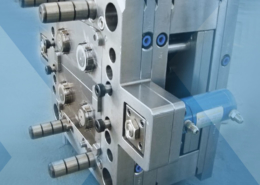
Moldex3D to preview next-gen plastic injection molding simulation software
Author:gly Date: 2024-09-30
Editor in chief of PlasticsToday since 2015, Norbert Sparrow has more than 30 years of editorial experience in business-to-business media. He studied journalism at the Centre Universitaire d'Etudes du Journalisme in Strasbourg, France, where he earned a master's degree.
In the future, it is also conceivable that process, quality, and patient data for each individual part will be 100% traceable via an RFID code.
A medical in-mold labeling (IML) application will be showcased by Arburg at NPE2024. First presented at Fakuma in 2023 as a proof of concept, the compact turnkey production cell anchored by Arburg’s electric Allrounder 520 A "Ultimate" press will produce a centrifuge tube with label on the NPE show floor.
Until now, large plastic parts have often been manufactured using various processes other than injection molding, which have significant limitations. With the availability of an injection molding machine as large as the duo 5500 combi M in a technical center, extensive possibilities for part and technology development and sampling are now available. This offering reinforces Engel's role as an enabler of new technologies, allowing customers and partners to actively pursue developments in new dimensions and expand injection molding capabilities.
The duo 5500 combi M represents the latest technology in injection molding, said Engel in the announcement. It features two movable (combined and individually operable) horizontal injection units and a combi M injection unit. It is also equipped with two six-axis Engel easix articulated robots for flexible and efficient automation.
Initially developed to mold large parts for the automotive sector, the press is now available for customer trials at the St. Valentin, Austria, technical center.
A scale on the scratch-resistant label indicates the exact fill level, which can be relevant for insulin pen and medical measuring cup applications, for example.
The company aims to use this machine to explore technologies and mold components in completely new dimensions in collaboration with its customers and partners. The extra-large mold space accommodates molds weighing up to 150 tonnes, with possible shot weights up to a massive 42 kg. The state-of-the-art machine was developed to meet the demands of the automotive industry and technical injection molding and is now available for customer trials.
The new Engel technical center facility covers all application areas for the automotive sector and technical injection molding.
Moldmaker Kebo, in-mold labeling specialist MCC Verstraete, automation developer Beck, and vision system supplier Intravis contributed to the joint IML project.
NPE2024 visitors can see the system in operation at booth W3743. The event returns to the Orange County Convention Center in Orlando, FL, on May 6 to 10.
IML is standard for packaging products, but the process is rarely used in medical manufacturing, said Arburg in its announcment. The concept is all the more compelling because both the tube and label are made of polypropylene, thus promoting sustainability and adding value for customers in the pharmaceutical and medical sectors.
Manufacturers of large, complex plastic parts and toolmakers can now test feasibility and implementation at an early project stage. This significantly shortens time to market and avoids costly subsequent errors by identifying and eliminating sources of error early on. Initial customer trials are scheduled to begin shortly.
Stephen has been with PlasticsToday and its preceding publications Modern Plastics and Injection Molding since 1992, throughout this time based in the Asia Pacific region, including stints in Japan, Australia, and his current location Singapore. His current beat focuses on automotive. Stephen is an avid folding bicycle rider, often taking his bike on overseas business trips, and a proud dachshund owner.
The electric Allrounder 520 A "Ultimate" is designed for ISO Class 7 cleanroom use and has a clamping force of 165 tons (1,500 kN). The ready-to-use 15-ml PP tubes are produced in an eight-cavity mold from Kebo at an approximate 10-second cycle time. Servo-electric drives ensure precise and reproducible mold positioning in the press, and a label adjustment head from Beck ensures that the labels are precisely aligned and applied. An integrated camera system from Intravis visually inspects the finished parts in real time. In a real application, the tubes could also be screwed together and packaged in tubular bags in the production cell, added Arburg.
For PU applications, two Cannon systems are available — one for small-volume applications and another for high-volume output. A corresponding dosing unit allows for coloring the polyurethane.
With the introduction of the duo 5500 combi M, Engel said it has reinforced its role as a leading hub for testing new technologies and collaborating closely with the industry to promote new injection molding possibilities. The machine allows for the testing and development of existing and new customer projects under real conditions and on neutral ground. This includes tool and material tests as well as the development of new manufacturing technologies.
In addition to facilitating recycling, the mono-material construction and integrated processing of the tube and label contribute to the stability of the tube, enabling a reduction in wall thickness, if needed. The process also eliminates secondary operations, such as bonding and printing. No adhesives are required and there is no waste caused by contamination with liquid color.
Engel reports that it has expanded its technical center in St. Valentin, Austria, with one of the largest injection molding machines from its standard portfolio — the duo 5500 combi M. With a clamping force of 55,000 kN and measuring 32 meters long, 13 meters wide, 6.8 meters high, and weighing 545 tonnes, it is by far the largest technical center machine in the world, according to Engel.
The IML print-to-cut distance is only around 0.08 in. (0.2 mm) for the centrifuge tube application. With a wall thickness of only 57 micrometers, the labels must be precisely positioned in the mold cavities, and equally precisely aligned and applied. A label adjustment head equalizes the manufacturing tolerance to a few hundredths, which is an important requirement for functionality and significantly reduces quality fluctuations and rejects.
All digital assistance systems from Engel are integrated into the machine control, enabling energy-efficient, sustainable production while optimizing processes.
A temperature-sensitive element can be included that monitors interruptions in the cold chain. If the temperature of the filled tube exceeds 7°C, for example, the thermo-chromic printing ink irreversibly changes in appearance.
The automotive industry increasingly uses larger plastic parts to reduce vehicle weight, improve fuel efficiency, and lower production costs. Plastics offer design flexibility, enhance corrosion resistance, and contribute to the longevity and safety of vehicles. They also allow for the integration of functional elements and reduce the number of individual parts needed. Engel’s new facility supports this trend by enabling the production of larger plastic components.
GETTING A QUOTE WITH LK-MOULD IS FREE AND SIMPLE.
FIND MORE OF OUR SERVICES:
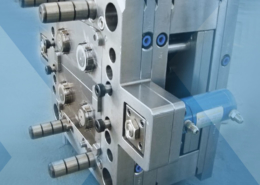
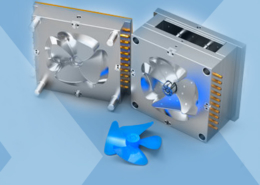
Plastic Molding

Rapid Prototyping
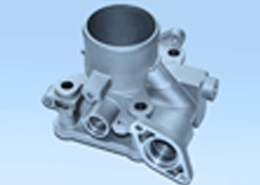
Pressure Die Casting
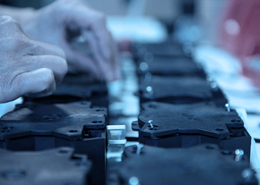
Parts Assembly
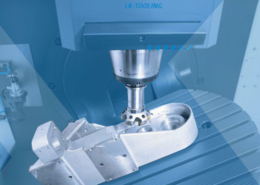