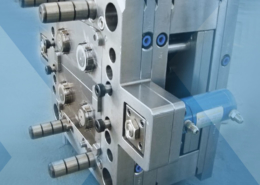
Milling Dies And Injection Moulding Some Acrylic Lenses - injection moulding alu
Author:gly Date: 2024-09-30
The question is – which technology should you choose? As a WayKen spokesperson states, “it is very difficult to get a standard answer to the cost comparison between 3D printing and CNC machining.” Instead, technology should be selected based on application.
CNC machined parts at WayKen on the other hand can be used to make functional prototypes which are suitable for engineering evaluation and testing. In contrast to the SLA and SLS services offered, CNC machining requires specially trained engineers to pre-program the processing parameters and toolpaths, then machine according to the programs. Manufacturing costs are therefore quoted taking the extra labor into account. CNC’s advantage is for machining parts with special requirements such as dimensional tolerances and surface qualities.
The process will be assisted by a pair of robots — an Engel viper 20 will remove the two-component parts and place them in trays, and an e pic robot will stack the trays in boxes, then discharge them via an integrated tray server.
Established in Hong Kong and located in Shenzhen, WayKen is a contender for China’s most experienced prototype manufacturer. The WayKen Prototype shop operates across two sites, one for plastic and one for metal. In total, the facilities span 20,000 square feet, employing over 60 dedicated personnel. WayKen’s specialist prototyping services include 3D printing (particularly SLA and SLS), CNC milling and rapid tooling technology.As a service bureau operating within high value automotive, medical, and aerospace industries, WayKen Rapid’s expertise is in selecting the right technology for the specific application, and delivering results at a cost competitive with the west.
Approximations of the general parameters of each process are detailed on WayKen.com in the company’s Technology Selection Guide, and a supporting Materials Selection Guide.
The Engel e-motion 160 combi M will make its debut at the K show in Düsseldorf, Germany, in October. Featuring just 160 tons of clamping force and a horizontal indexing table, the combi M boasts two injection units — one fitted on the stationary platen, the second on the moving platen. Two molds can operate in parallel thanks to the indexing table dividing the mold closing area in the center.
The rapid production time of 3D printing means it is finding increased uses throughout the medical industry. WayKen SLA & SLS 3D printing for medicine can be used to make hand held appliances, concept models, and new devices in low volume, e.g. diagnostic equipment, surgical instruments, electronic apparatus and ultrasonic systems. These devices are valuable for surgical planning, simulation and also to map dental correction procedures.
SLS and SLA 3D printing are useful for fast response solutions. With digital operational tools like slicer software, the process does not require as much specialized training as CNC machining. With little labour involved, the manufacturing cost of 3D printing is priced based on the amount of materials. As larger parts cost more 3D printing is advantageous for small volumes and lightweight parts. Realtively simple structures, wth less demand for surface quality and precision parts, also benefit the most from WayKen’s 3D printing services. The technology is ideal for protoyping small medical devices, industrial tooling, and outer covering of electrical tools.
WayKen specializes in an ability to machine a range of plastics (opaque and optically clear) and aluminum. In the CNC process, a toolhead gradually subtracts material from a solid block. As such, molecular stability of the base material remains constant producing a part with unparalleled tensile strength.
As far as resolution is concerned, the accuracy of CNC machining at WayKen is typically higher than 3D printing, between 0.02mm and 0.05mm – 0.10mm depending on geometry. Turnaround time for 3D printing is typically faster at just 2-5 days versus 3 – 8 days for CNC. This does however come at a tradeoff with the volume of products than can be produced. A typical SLA/SLS run can create 1 – 10 parts, whereas CNC has a range of 1 – 50.
“Traditional” processes at WayKen cover CNC plastic/metal parts machining, vacuum injection molding and rapid injection molding. In the case of CNC machining, a solid block of raw material can be used.
The Engel e-motion 160 combi M will be molding medical diagnostic components under cleanroom conditions at the event in October.
The primary SLA material used by WayKen is an ABS-like photopolymer, suitable for use in the lost-wax method of casting favoured in jewelry making and dental industries. SLS uses powdered Nylon feedstock, which acts like a support material throughout 3D printing, cutting down post-processing times. Parts made using SLS also benefit from the potential of nesting meaning that more designs can be 3D printed within the same build.
iQ process observer, which monitors the entire process. This AI platform analyzes hundreds of parameters simultaneously, displaying deviations and corrective measures.
Luckily, the company’s quoting system quickly responds to enquiries within 24 hours by our allowing “On-time delivery — every time, no exceptions.” Request a quote from WayKen Rapid online now at WayKen.com.
iQ flow control, which ensures constant temperature control ratios by controlling temperature differences in the individual cooling circuits based on a set value.
In some cases, it may even be beneficial to combine both additive and subtractive manufacturing process to complete an end goal. As an example, SLA and SLS could be used as a preliminary stage before moving the CNC machining.
One ideal application for the combi M is the molding of sample vessels for medical diagnostics under cleanroom conditions. These two-component parts will be demonstrated during the K at stand C58 in hall 15. First, primary parts with cylindrical cavities are injected using black-dyed polycarbonate. The cylinders are then sealed with transparent polycarbonate in a second molding step enabled by the indexing table rotating 180 degrees.
iQ weight control, which detects fluctuations in the injection volume and material viscosity and automatically compensates for them within validated limits in the same cycle.
Geoff Giordano is a tech journalist with more than 30 years’ experience in all facets of publishing. He has reported extensively on the gamut of plastics manufacturing technologies and issues, including 3D printing materials and methods; injection, blow, micro and rotomolding; additives, colorants and nanomodifiers; blown and cast films; packaging; thermoforming; tooling; ancillary equipment; and the circular economy. Contact him at [email protected].
A new all-electric injection molding machine and accompanying AI-driven work cell from Engel reduces footprint on the production floor as well as energy consumption, while also doubling output.
In automotive, WayKen applies a plethora of CNC prototyping and rapid tooling methods to the production of spare parts. The services are useful to car manufacturers running limited trials of a car/motorcycle, and allow volume customization. WayKen automotive rapid prototyping is delivered as a complete service, guiding customers through proof of concept design reviews and mechanical component engineering tests, to show car projects and exterior/interior prototypes.
CNC operation is determined by computer aided design (CAD) or computer aided manufacturing (CAM) data translated into Gcode – as used by 3D printers. The precision tool path in a CNC system creates an excellent surface finish, and parts can be sanded and finished on the same machine.
3D printing services at WayKen are primarily laser-powered, offering a high level of speed and accuracy. WayKen stereolithography (SLA) is a UV based curing process, and selective laser sintering (SLS) uses a carbon dioxide laser.
The competitive price point for all services, according to the company’s website, is “normally 30%-50% less than the US/European prices, due to lower labor costs. Moreover allowing a quick project start compares to other rapid prototype companies.”
One of the main advantages of this process is material availability as virtually any material can be CNC machined. For this reason, and its use in industry since the 1940s, CNC machining remains the most common means of prototyping to date
The combi M takes up approximately 20% less space because of its horizontal indexing table. A comparable 32-cavity mold with a vertical rotary table would require a machine with at least 280 tons of clamping force, the company noted.
GETTING A QUOTE WITH LK-MOULD IS FREE AND SIMPLE.
FIND MORE OF OUR SERVICES:
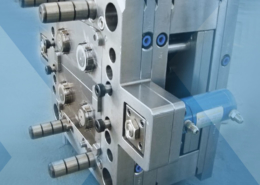
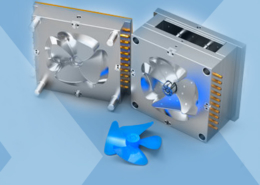
Plastic Molding

Rapid Prototyping
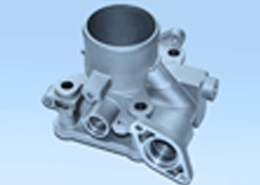
Pressure Die Casting
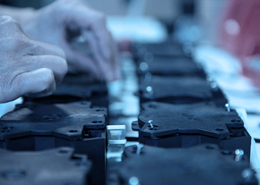
Parts Assembly
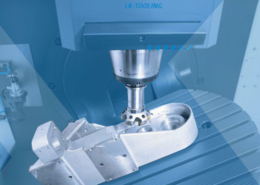