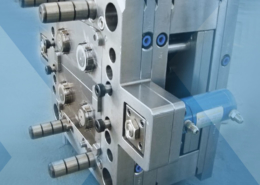
Medical Micro Molding at Scale Featured at IME South - liquid plastic for molds
Author:gly Date: 2024-09-30
Editor in chief of PlasticsToday since 2015, Norbert Sparrow has more than 30 years of editorial experience in business-to-business media. He studied journalism at the Centre Universitaire d'Etudes du Journalisme in Strasbourg, France, where he earned a master's degree.
Lakeshore is helping many companies onshore molds or rebuild molds from a previous supplier that are difficult to remove. For these transitions, Lakeshore helps customers confirm mold and tooling compatibility with its facility, match material and color, review quality control requirements, and plan logistics.
Coming soon are specialized molds designed to produce custom plastic caps in various sizes and textures at a lower initial cost.
Starting as a mold fabrication company in 2019, Lakeshore provides turnkey services from engineering through to assembly.
“The benefit to customers of our turnkey experience is risk mitigation,” Pontius said. “From CAD modeling to in-house fabrication and repair to prototyping and mass production, the development cycle is under one roof. If a mold has an issue, rather than having it taken out of the machine and shipped away for repair, we can diagnose the problem and repair it in a matter of hours, minimizing downtime and maximizing production schedules,” said Pontius.
20/20 Custom Molded Plastics first detailed plans to set up shop at the vacant facility in Bluffton in 2017, reported Inside Indiana Business. The company committed to investing $27 million in that plant and adding 155 jobs. Just over a year later, 20/20 said it would invest $41 million to add 240,000 square feet to the facility and add more than 200 new jobs.
The WARN notification indicated that the laid-off employees would receive COBRA benefits. The nonunion workers did not receive any separation benefits and were not eligible for Bumping Rights, the notification added.
Automation is critical to Lakeshore’s business. Removing high-end jewelry cases from a mold, for example, requires careful handling to maintain aesthetics, a task that is best performed by a robot. Molding polished parts of clear Tritan copolyester, which degrades quickly with any variation in cycle time, also requires automation. “The ARI top-entry robot is faster and more consistent at removing the part from the mold and prevents damage that could be introduced if a machine operator so much as bumps the mold when removing the part,” said Lakeshore CEO Kyle Pontius.
In a sign of robust injection molding demand, Utah’s Lakeshore Plastics expanded capacity of its Orem manufacturing facility by about 50% to 12,000 square feet.
As recently as April 2021, 20/20 Custom Molded Plastics issued a press release announcing that it would bring “more than 100 new jobs to its two locations.” At the same time, the company said it would relocate 375- and 500-ton presses from Holiday City to Bluffton. The Indiana location was also slated to receive three new structural foam presses, the company said at the time, “over the next 18 months.”
Geoff Giordano is a tech journalist with more than 30 years’ experience in all facets of publishing. He has reported extensively on the gamut of plastics manufacturing technologies and issues, including 3D printing materials and methods; injection, blow, micro and rotomolding; additives, colorants and nanomodifiers; blown and cast films; packaging; thermoforming; tooling; ancillary equipment; and the circular economy. Contact him at [email protected].
20/20 Custom Molded Plastics LLC announced that it is laying off 93 workers at its Bluffton, IN, facility. The company, which has its headquarters in Holiday City, OH, notified the state of Indiana of the layoffs via a letter in accordance with the Worker Adjustment and Retraining Notification Act (WARN). The letter was undated but local media outlets reported that it was sent late last week.
Lakeshore produces about four million caps annually and is adding equipment for cap lining. The company owns five injection molding machines (IMMs) from Absolute Haitian, ranging from 100 to 427 tons. Three of those IMMs are paired with top-entry robots from Absolute Robot. Lakeshore’s new manufacturing space can accommodate three more IMMs.
For mold fabrication, the company added a CNC lathe and three electrical discharge machines (wire, sinker, and hole popper) to complement its CNC milling machine.
In the letter, the company said 27 workers were laid off on Oct. 21, and a further 66 were let go on Nov. 4. No reason was given, but 20/20 Custom Molded Plastics said in the letter that the “impact” of the action “is expected to be temporary.”
“In the coming months, we're making available specialized molds to easily swap logos and textures on numerous cap sizes to produce a custom closure at a much lower initial cost,” Pontius said.
GETTING A QUOTE WITH LK-MOULD IS FREE AND SIMPLE.
FIND MORE OF OUR SERVICES:
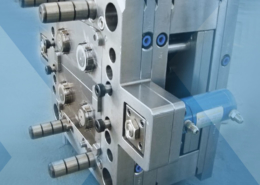
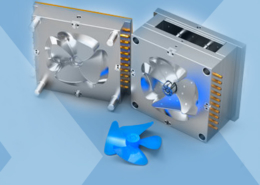
Plastic Molding

Rapid Prototyping
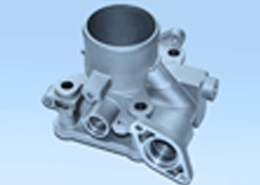
Pressure Die Casting
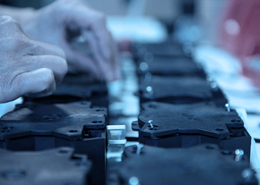
Parts Assembly
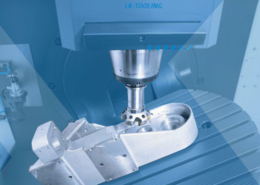