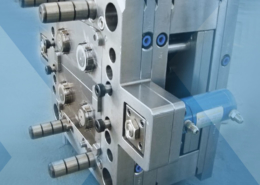
Making Cooling Time Productive With a Shuttle Mold System - one off plastic moul
Author:gly Date: 2024-09-30
In this collection, which is part one of a series representing some of John’s finest work, we present you with five articles that we think you will refer to time and again as you look to solve problems, cut cycle times and improve the quality of the parts you mold.
Across all process types, sustainability was a big theme at NPE2024. But there was plenty to see in automation and artificial intelligence as well.
3D printed nests for CMM inspection can be created using the part’s existing CAD model, similar to the process for designing a mold.
This air diverter for a youth motorbike was designed for injection molding, but bikes produced before the mold tooling was ready used 3D printed parts like this.
When, how, what and why to automate — leading robotics suppliers and forward-thinking moldmakers will share their insights on automating manufacturing at collocated event.
Quick-change tooling on a live-tooling station saves time during production my eliminating the need to touch-off tools each time they are installed.
Formnext Chicago is an industrial additive manufacturing expo taking place April 8-10, 2025 at McCormick Place in Chicago, Illinois. Formnext Chicago is the second in a series of Formnext events in the U.S. being produced by Mesago Messe Frankfurt, AMT – The Association For Manufacturing Technology, and Gardner Business Media (our publisher).
Mixed in among thought leaders from leading suppliers to injection molders and mold makers at the 2023 Molding and MoldMaking conferences will be molders and toolmakers themselves.
Successfully starting or restarting an injection molding machine is less about ticking boxes on a rote checklist and more about individually assessing each processing scenario and its unique variables.
Another early challenge was getting used to P codes, which are used to synchronize the motion of the two turrets. P codes not only ensure that the turrets don’t interfere with each other when performing separate operations, but also can signal them to perform identical operations simultaneously. For example, if a programmer wants to face a part with the upper turret and then drill the end of it with the lower turret, those operations have to be synchronized because they obviously can’t be performed at the same time. If the programmer assigns a P10 value to the upper turret and a higher P20 to the lower turret, the upper turret will continue all of its necessary motions until it encounters a higher P value in the program code. If the next P code it encounters is higher than the P code assigned to the lower turret, the upper turret will wait until lower turret is done. However, if the same P code is applied to both turrets, they will work simultaneously.
Across the show, sustainability ruled in new materials technology, from polyolefins and engineering resins to biobased materials.
Study shows the plastic compounding process is being used to boost electrical properties and UV resistance while custom compounding is increasingly being used to achieve high-performance in plastic-based goods.
Exhibitors and presenters at the plastics show emphasized 3D printing as a complement and aid to more traditional production processes.
Multiple speakers at Molding 2023 will address the ways simulation can impact material substitution decisions, process profitability and simplification of mold design.
Resin drying is a crucial, but often-misunderstood area. This collection includes details on why and what you need to dry, how to specify a dryer, and best practices.
Join this webinar to explore the transformative benefits of retrofitting your existing injection molding machines (IMMs). Engel will guide you through upgrading your equipment to enhance monitoring, control and adaptability — all while integrating digital technologies. You'll learn about the latest trends in IMM retrofitting (including Euromap interfaces and plasticizing retrofits) and discover how to future-proof your machines for a competitive edge. With insights from industry experts, it'll walk you through the decision-making process, ensuring you make informed choices that drive your business forward. Agenda: Maximize the value of your current IMMs through strategic retrofitting Learn how to integrate digital technologies to enhance monitoring and control Explore the benefits of Euromap interfaces and plasticizing retrofits Understand how retrofitting can help meet new product demands and improve adaptability Discover how Engel can support your retrofitting needs, from free consultations to execution
With that said, the company continues to work closely with Rex Luxmore, its Iscar tooling representative, who Mr. Freeman says is proactive about keeping him up to date with new tooling developments. For example, Mr. Luxmore’s recommendation of grooving tools with a new coating resulted in a 30- to 50-percent improvement in tool life. This assistance is critical, Mr. Freeman notes, largely because of the challenging materials such as M4 powder-metal tool steel that the company frequently machines. This tool steel is not only very unforgiving, but it will work-harden quickly if cut too slowly or lightly.
The photos on the following page show how camshaft cores are produced on the lathe. An operator manually slides a pre-cut bar into the main spindle, pulls the bar out a few inches to a stop, and clamps it. The lathe then turns and mills features into what will become the front face of the cam. Next, the subspindle moves into position, grabs the machined face and pulls out the bar approximately 10 inches. Grooving and lobe milling are completed on that segment of the bar. Once machining on that section is completed, the subspindle clamps onto some of the newly machined journals and pulls the bar farther out of the main spindle to enable grooving and lobe milling of the back half of the camshaft. (Performing these operations in two small sections minimizes the risk of deflection, vibration and chatter.) Finally, the subspindle consumes nearly the entire bar to enable turning and milling work on the back face of the camshaft.
The digital nature of 3D printing makes it possible to easily adjust a base product design via software to suit the specific customer or application. The technology can be applied to produce everything from custom medical devices such as splints and hearing aids to consumer products like shoe insoles and sporting equipment tailored to the buyer.
Second quarter started with price hikes in PE and the four volume engineering resins, but relatively stable pricing was largely expected by the quarter’s end.
With advocacy, communication and sustainability as three main pillars, Seaholm leads a trade association to NPE that ‘is more active today than we have ever been.’
technotrans says climate protection, energy efficiency and customization will be key discussion topics at PTXPO as it displays its protemp flow 6 ultrasonic eco and the teco cs 90t 9.1 TCUs.
After successfully introducing a combined conference for moldmakers and injection molders in 2022, Plastics Technology and MoldMaking Technology are once again joining forces for a tooling/molding two-for-one.
While the major correction in PP prices was finally underway, generally stable pricing was anticipated for the other four commodity resins.
Say “manufacturing automation” and thoughts immediately go to the shop floor and specialized production equipment, robotics and material handling systems. But there is another realm of possible automation — the front office.
Take a deep dive into all of the various aspects of part quoting to ensure you’ve got all the bases—as in costs—covered before preparing your customer’s quote for services.
Unless a camshaft has an odd number of grooves, the lathe performs turning and grooving operations using both turrets simultaneously when the bar is held between spindles. Because the upper turret is optimized to run close to the main spindle and the lower one is set up to run close to the subspindle, the company does not perform pinch turning. However, Mr. Godbold estimates that simultaneous cutting enables the lathe to remove material 30 percent faster primarily because the tool pressure is balanced. In addition, starting the grooving operations at the middle of each section of bar and moving out toward the spindles leaves more stock at either end of the bar section. This ensures rigid support to prevent chatter and also eliminates flexing at weak areas of the bar, which could possibly pinch or break a grooving tool.
3D printing still plays a valuable role for rapid prototyping, as it is often the fastest way to get a look-and-feel prototype or iterate design ideas. However, the technology has advanced to the point that, with the right material and printer, a prototype can often be used just like a production part. Brackets, electronics enclosures, ducts, components of medical devices and more have made this leap.
One advantage of standardization is that it minimizes the number of tools that must be touched-off for a new job. Typically, an operator has to install and touch-off only a few drills, reamers and taps during setup for a new job. Tool standardization also enables programmers to quickly and easily determine whether additional tooling is needed for a new project. Ultimately, standardization has enabled Comp Cams to reduce change-over times for most new jobs from an entire day to just a few hours.
While the melting process does not provide perfect mixing, this study shows that mixing is indeed initiated during melting.
Resin drying is a crucial, but often-misunderstood area. This collection includes details on why and what you need to dry, how to specify a dryer, and best practices.
A collaboration between show organizer PLASTICS, recycler CPR and size reduction experts WEIMA and Conair recovered and recycled all production scrap at NPE2024.
Cobots, pick-and-place robots and other automation can make plastics processing more productive, but in most cases these additions require specialized end-of-arm tooling (EOAT) and other fixturing. 3D printing can be applied to produce vacuum grippers and other specialized end effectors for handling parts. These devices can integrate vacuum lines, wire harnesses and other features to simplify assembly, and tend to be lighter weight than conventional options.
This month’s resin pricing report includes PT’s quarterly check-in on select engineering resins, including nylon 6 and 66.
While the melting process does not provide perfect mixing, this study shows that mixing is indeed initiated during melting.
Mike Sepe has authored more than 25 ANTEC papers and more than 250 articles illustrating the importance of this interdisciplanary approach. In this collection, we present some of his best work during the years he has been contributing for Plastics Technology Magazine.
Today, Comp Cams machines small batches of racing camshaft cores on a twin-spindle/twin-turret lathe from Okuma. (Camshaft cores are camshafts that have their primary features machined, but still require subsequent heat treating and grinding operations.) Bringing this machining capability in-house enabled the company to greatly speed turnaround of custom camshafts for professional racing applications because it no longer had to wait weeks or months to receive camshaft cores. It can now manufacture as many as 12 M4 powder-metal tool-steel camshaft cores in a single eight-hour shift.
Thousands of people visit our Supplier Guide every day to source equipment and materials. Get in front of them with a free company profile.
The aim of this presentation is to guide you through the factors and the numbers that will help you determine if a robot is a smart investment for your application. Agenda: Why are you considering automation? What problems are you trying to solve? How and why automation can help Crunch the numbers and determine the ROI
While prices moved up for three of the five commodity resins, there was potential for a flat trajectory for the rest of the third quarter.
Eliminating the need to contact each supplier for every individual quote, a new CRM for automotive supplier Axiom Group tracks past quotes as well as industry history to generate fast, reliable RFQs and more.
Across the show, sustainability ruled in new materials technology, from polyolefins and engineering resins to biobased materials.
In a time where sustainability is no longer just a buzzword, the food and beverage packaging industry is required to be at the forefront of this innovation. By adopting circular packaging processes and solutions, producers can meet regulatory requirements while also satisfying consumer demand and enhancing brand reputation. Join Husky to learn more about the broader implications of the circular economy — as well as how leading brands are leveraging this opportunity to reduce costs, increase design flexibility and boost product differentiation. Agenda: The cost and operational benefits of embracing circularity Key materials in circular packaging — including rPET and emerging bioplastics How to design a circular food and beverage package Strategies for selecting sustainable closures to future-proof packaging solutions Optimization and streamlining of production processes for enhanced efficiency How Husky Technologies can enable your sustainable success
technotrans says climate protection, energy efficiency and customization will be key discussion topics at PTXPO as it displays its protemp flow 6 ultrasonic eco and the teco cs 90t 9.1 TCUs.
Formnext Chicago is an industrial additive manufacturing expo taking place April 8-10, 2025 at McCormick Place in Chicago, Illinois. Formnext Chicago is the second in a series of Formnext events in the U.S. being produced by Mesago Messe Frankfurt, AMT – The Association For Manufacturing Technology, and Gardner Business Media (our publisher).
Coverage of single-use plastics can be both misleading and demoralizing. Here are 10 tips for changing the perception of the plastics industry at your company and in your community.
August 29-30 in Minneapolis all things injection molding and moldmaking will be happening at the Hyatt Regency — check out who’s speaking on what topics today.
This Adcole cylindrical coordinate measuring machine orients camshafts vertically for measurement results that require no need for sag correction. It takes less than a minute for an operator to enter camshaft feature specifications to measure.
Prior to the lathe’s delivery, Comp Cams sent what it thought was a very difficult camshaft core to Okuma’s facility for machine prove-out: a 70-mm-diamter NHRA Pro Stock camshaft with nine journals. Kevin Kraieski, an applications engineer for Okuma, created the initial part programs and machined the first sample parts. Mr. Kraieski set up the part program using multiple variable-style sub-routines for commonly required operations, such as grooving between lobes, milling lobe profiles, drilling and tapping bolt hole patterns, and more. This made it possible for Comp Cams to easily reprogram the complex machine for any number of camshaft designs without starting from scratch each time.
Machining simulation is performed after a program is created for a new camshaft design. After that, a dry run is performed on the lathe followed by a test part created from low-cost mild steel. Once the process is verified, production can ensue in the specified material.
Processors with sustainability goals or mandates have a number of ways to reach their goals. Biopolymers are among them.
A leading manufacturer of high-performance valve train components installed a twin spindle/twin-turret lathe to bring camshaft machining work in-house. Here, the company explains how it has become more effective using its multifunction lathe to produce small batches of custom racing camshafts.
At NPE 2024: The Plastics Show, 3D printing and additive manufacturing (AM) suppliers are highlighted in the Advanced Manufacturing Zone, while AM users will take to the stage for Wednesday’s 3D Printing Workshop. But keep an eye out for promising developments and applications across the show floor, including:
Learn about sustainable scrap reprocessing—this resource offers a deep dive into everything from granulator types and options, to service tips, videos and technical articles.
Longer 6-inch jaws on the sub-spindle enable it to clamp at least two journals of every camshaft Comp Cams manufactures.
Say “manufacturing automation” and thoughts immediately go to the shop floor and specialized production equipment, robotics and material handling systems. But there is another realm of possible automation — the front office.
Files for 3D printing are more easily stored than physical parts, leading major OEMs, military branches and government agencies to adopt the technology as a way of sourcing spare parts and items needed for system maintenance. Digital inventory parts like clamps, clips and brackets can be 3D printed as needed, saving the hassle and expense of storing extras or keeping track of tooling. Even better, digital inventory can also be distributed. By working with manufacturing partners or placing printers at different facilities, organizations can produce these parts near where they will be used.
August 29-30 in Minneapolis all things injection molding and moldmaking will be happening at the Hyatt Regency — check out who’s speaking on what topics today.
Discover how artifical intelligence is revolutionizing plastics processing. Hear from industry experts on the future impact of AI on your operations and envision a fully interconnected plant.
Improving finish in the grooves between the lobes and increasing lobe machining speed proved to be challenging during testing. However, Tim Whitmore, an OEM project manager for Iscar, work closely with Mr. Kraieski to iron out the tooling issues. By the time the machine was delivered to Comp Cams, it could complete a M4 camshaft core in 75 minutes.
Exhibitors and presenters at the plastics show emphasized 3D printing as a complement and aid to more traditional production processes.
The lower turret contains center drills used for both the front and rear camshaft faces. This turret also has live horizontal stations set up to create features such as vent holes. Two stations contain miscellaneous tools. These include a multifunction drilling/boring tool that is typically used to create counterbores, and a large indexable-insert drill that machines bores on the rear of a camshaft.
In this collection of articles, two of the industry’s foremost authorities on screw design — Jim Frankand and Mark Spalding — offer their sage advice on screw design...what works, what doesn’t, and what to look for when things start going wrong.
In a time where sustainability is no longer just a buzzword, the food and beverage packaging industry is required to be at the forefront of this innovation. By adopting circular packaging processes and solutions, producers can meet regulatory requirements while also satisfying consumer demand and enhancing brand reputation. Join Husky to learn more about the broader implications of the circular economy — as well as how leading brands are leveraging this opportunity to reduce costs, increase design flexibility and boost product differentiation. Agenda: The cost and operational benefits of embracing circularity Key materials in circular packaging — including rPET and emerging bioplastics How to design a circular food and beverage package Strategies for selecting sustainable closures to future-proof packaging solutions Optimization and streamlining of production processes for enhanced efficiency How Husky Technologies can enable your sustainable success
Scooter Brothers certainly understood that when the twin-spindle/twin-turret machine was delivered. As long as long as the company became more effective using the lathe during the first few months and was able to achieve a half-throttle-level of production within a year, Mr. Brothers was not going to be discouraged.
3D printing is a viable production choice for a variety of products, particularly where printing enables geometric complexity or other advantages. While 3D printing is capable of continuous production of tens of thousands of pieces, it is equally applicable to smaller batches of parts needed less frequently — with no minimum order quantity. Production use cases for this technology include brackets, phone cases, valves, medical implants, packaging solutions and much, much more.
Originally, the prolonged camshaft-core delivery times had the company considering adding a “conventional” cell to produce the small batches that race teams required. Such cells typically include a saw to cut barstock to length; lathes to face the front and rear of the camshaft, add centers and groove the lobe layout; mills to machine details in the front and rear camshaft faces; and additional mills to machine the lobe profiles. Most of these operations required multiple time-consuming setups, too.
Baystar's Borstar technology is helping customers deliver better, more reliable production methods to greenhouse agriculture.
Gifted with extraordinary technical know how and an authoritative yet plain English writing style, in this collection of articles Fattori offers his insights on a variety of molding-related topics that are bound to make your days on the production floor go a little bit better.
As it turned out, the “really difficult” camshaft Comp Cams sent to Okuma for testing proved easier to machine than its other camshaft models. That’s because the camshaft’s nine journals provided more clamping points for the subspindle than a typical five-journal camshaft. Consequently, the original subspindle jaws were not long enough to clamp across at least two journals on the five-journal models (this was necessary to ensure adequate support during machining). Installing lengthier 6-inch jaws enabled the subspindle to clamp across two or more journals on any type of camshaft the company manufactures. The main spindle always clamps solid barstock, so longer jaws are not necessary for that spindle.
The clear model in the center shows the conformal cooling lines inside the metal 3D printed mold on the right, used to produce the plastic part on the left.
Ultradent's entry of its Umbrella cheek retractor took home the awards for Technical Sophistication and Achievement in Economics and Efficiency at PTXPO.
Once that section is completed, the sub-spindle consumes the machined section and pulls the bar out further to repeats those operations on the back section of bar.
Join Wittmann for an engaging webinar on the transformative impact of manufacturing execution systems (MES) in the plastic injection molding industry. Discover how MES enhances production efficiency, quality control and real-time monitoring while also reducing downtime. It will explore the integration of MES with existing systems, emphasizing compliance and traceability for automotive and medical sectors. Learn about the latest advancements in IoT and AI technologies and how they drive innovation and continuous improvement in MES. Agenda: Overview of MES benefits What is MES? Definition, role and brief history Historical perspective and evolution Longevity and analytics Connectivity: importance, standards and integration Advantages of MES: efficiency, real-time data, traceability and cost savings Emerging technologies: IoT and AI in MES
Workpiece slippage inside the jaws also proved to be problematic at times because some camshaft materials are more difficult to clamp tightly than others. The solution was applying a tungsten-alloy coating from Carbonite Metal Coatings on the gripping surface of the jaws. This particular coating is applied via electrofusion, which creates a metallurgical bond that is said to be stronger than spray-on coatings. The coating has virtually eliminated linear and angular workpiece slippage from occurring during machining.
Mixed in among thought leaders from leading suppliers to injection molders and mold makers at the 2023 Molding and MoldMaking conferences will be molders and toolmakers themselves.
These smart ski goggles were developed with a 3D printed electronics enclosure. Originally meant as a prototype, the 3D printed assembly has since been used in sale units as well.
In this three-part collection, veteran molder and moldmaker Jim Fattori brings to bear his 40+ years of on-the-job experience and provides molders his “from the trenches” perspective on on the why, where and how of venting injection molds. Take the trial-and-error out of the molding venting process.
Plastics processors are finding applications for 3D printing around the plant and across the supply chain. Here are 8 examples to look for at NPE2024.
Processors with sustainability goals or mandates have a number of ways to reach their goals. Biopolymers are among them.
Core Technology Molding turned to Mold-Masters E-Multi auxiliary injection unit to help it win a job and dramatically change its process.
Despite price increase nominations going into second quarter, it appeared there was potential for generally flat pricing with the exception of a major downward correction for PP.
Lead time delays for molded parts often originate from difficulties with sourcing tooling. 3D printing makes it possible to accelerate mold development and simplify design changes down the line. If a new design is needed, 3D printing offers a faster route to a new tool and even the chance to repair or modify an existing one. While metal 3D printing methods, such as laser powder bed fusion, have historically been the most common techniques applied to mold tooling, there are new innovations to explore in terms of more accessible metal printing methods and short-run molds made from other materials such as polymer composites.
The company has also standardized on coolant, using the same Castrol Syntilo 9918 synthetic coolant for machining that it does for grinding. Mr. Godbold says the company could save money by using a lower-cost coolant, but it appreciates the consistent performance the advanced coolant offers. Comp Cams plans to install an 8,000-gallon central coolant system with a single main paper filter system to supply both the machining and grinding areas in the facility.
The camshaft portion of Comp Cams’ product line is evenly divided into three segments: high-performance/non-racing applications; hobbyist racers; and engine builders for NASCAR, NHRA and other professional race teams. The custom billet camshafts machined in the company’s Memphis facility are used by the professional race teams.
Join this webinar to explore the transformative benefits of retrofitting your existing injection molding machines (IMMs). Engel will guide you through upgrading your equipment to enhance monitoring, control and adaptability — all while integrating digital technologies. You'll learn about the latest trends in IMM retrofitting (including Euromap interfaces and plasticizing retrofits) and discover how to future-proof your machines for a competitive edge. With insights from industry experts, it'll walk you through the decision-making process, ensuring you make informed choices that drive your business forward. Agenda: Maximize the value of your current IMMs through strategic retrofitting Learn how to integrate digital technologies to enhance monitoring and control Explore the benefits of Euromap interfaces and plasticizing retrofits Understand how retrofitting can help meet new product demands and improve adaptability Discover how Engel can support your retrofitting needs, from free consultations to execution
While prices moved up for three of the five commodity resins, there was potential for a flat trajectory for the rest of the third quarter.
Plastics Technology covers technical and business Information for Plastics Processors in Injection Molding, Extrusion, Blow Molding, Plastic Additives, Compounding, Plastic Materials, and Resin Pricing. About Us
While the major correction in PP prices was finally underway, generally stable pricing was anticipated for the other four commodity resins.
Sustainability continues to dominate new additives technology, but upping performance is also evident. Most of the new additives have been targeted to commodity resins and particularly polyolefins.
Each turret on the LT-300MY has 12 tool stations. Daniel Freeman, the R&D technician for Comp Cams who commonly programs and helps run the lathe, says the company takes full advantage of those 24 total stations. Approximately two-thirds of them rarely change. In addition, tools in several stations are mirrored on both the upper and lower turrets to facilitate the simultaneous machining operations.
Learn about sustainable scrap reprocessing—this resource offers a deep dive into everything from granulator types and options, to service tips, videos and technical articles.
Join Engel in exploring the future of battery molding technology. Discover advancements in thermoplastic composites for battery housings, innovative automation solutions and the latest in large-tonnage equipment designed for e-mobility — all with a focus on cost-efficient solutions. Agenda: Learn about cutting-edge thermoplastic composites for durable, sustainable and cost-efficient battery housings Explore advanced automation concepts for efficient and scalable production See the latest large-tonnage equipment and technology innovations for e-mobility solutions
Plastics Technology covers technical and business Information for Plastics Processors in Injection Molding, Extrusion, Blow Molding, Plastic Additives, Compounding, Plastic Materials, and Resin Pricing. About Us
Mr. Godbold explains that Comp Cams’ traditional expertise was in grinding camshafts, not machining them. So when the decision was made to install the seven-axis multifunction lathe in 2008, the company relied heavily on the expertise and advice of its equipment suppliers to establish an effective machining process. Comp Cams continues to tap those resources today as it strives to minimize cycle times for camshaft cores.
In this collection of articles, two of the industry’s foremost authorities on screw design — Jim Frankand and Mark Spalding — offer their sage advice on screw design...what works, what doesn’t, and what to look for when things start going wrong.
Mold maintenance is critical, and with this collection of content we’ve bundled some of the very best advice we’ve published on repairing, maintaining, evaluating and even hanging molds on injection molding machines.
Luckily for me, “you can’t sell if you don’t tell” is the motto of Paul “Scooter” Brothers, one of Comp Cams’ owners as well as chairman of the board for the Specialty Equipment Market Association. In keeping with the spirit of that saying, company representatives weren’t shy about detailing how they’ve become better at using the advanced lathe during my visit to their Memphis, Tennessee facility.
These phone case components are 3D printed in a machine that can produce several hundred of these parts per day; scaling production to higher quantities means simply adding additional machines.
The company ultimately decided to go a different route after Mr. Godbold met with Larry Schwartz, who at that time was Okuma America’s president (he’s now the machine tool builder’s chief strategy officer). The men discussed alternate ways to manufacture camshaft cores that would minimize change-overs and simplify setups for production runs of 20 or so pieces. Mr. Schwartz’s idea was to use a twin-spindle/twin-turret lathe. Keeping a bar either clamped between the spindles and/or partially inside of them would enable complete machining of camshaft cores in one setup. Plus, the twin spindles could perform some operations simultaneously.
The upper turret has two vertically oriented end mills of different diameters that remain in their respective live stations. These are used in conjunction with the machine’s Y-axis movement to perform lobe milling. The narrower 0.75-inch end mill has one less insert than the 1-inch end mill, so the feed rate has to be reduced when that tool is used. Tools in the upper turret’s five horizontal live stations often don’t change either. These perform drilling, tapping, reaming and other operations on the front face of a camshaft.
The lathe then turns and mills features into the front face of the camshaft. Next, the sub-spindle pulls the bar out for grooving...
Attendees will benefit from a program focused on practical applications of 3D technologies related to plastics processing. This event will conclude with a 3D Printing Industry Reception sponsored by Additive Manufacturing Media.
Plastics processors are finding applications for 3D printing around the plant and across the supply chain. Here are 8 examples to look for at NPE2024.
Join KraussMaffei for an insightful webinar designed for industry professionals, engineers and anyone interested in the manufacturing processes of PVC pipes. This session will provide a comprehensive understanding of the technology behind the production of high-quality PVC pipes: from raw material preparation to final product testing. Agenda: Introduction to PVC extrusion: overview of the basic principles of PVC pipe extrusion — including the process of melting and shaping PVC resin into pipe forms Equipment and machinery: detailed explanation of the key equipment involved — such as extruders, dies and cooling systems — and their roles in the extrusion process Process parameters: insight into the critical process parameters like temperature, pressure and cooling rates that influence the quality and consistency of the final PVC pipes Energy efficiency: examination of ways to save material and energy use when extruding PVC pipe products
The Plastics Industry Association (PLASTICS) has released final figures for NPE2024: The Plastics Show (May 6-10; Orlando) that officially make it the largest ever NPE in several key metrics.
The aim of this presentation is to guide you through the factors and the numbers that will help you determine if a robot is a smart investment for your application. Agenda: Why are you considering automation? What problems are you trying to solve? How and why automation can help Crunch the numbers and determine the ROI
When, how, what and why to automate — leading robotics suppliers and forward-thinking moldmakers will share their insights on automating manufacturing at collocated event.
In this collection of content, we provide expert advice on welding from some of the leading authorities in the field, with tips on such matters as controls, as well as insights on how to solve common problems in welding.
This Knowledge Center provides an overview of the considerations needed to understand the purchase, operation, and maintenance of a process cooling system.
After successfully introducing a combined conference for moldmakers and injection molders in 2022, Plastics Technology and MoldMaking Technology are once again joining forces for a tooling/molding two-for-one.
Second quarter started with price hikes in PE and the four volume engineering resins, but relatively stable pricing was largely expected by the quarter’s end.
Each turret has three different grooving tools. Two of those perform roughing operations. The wider of the two is used as often as possible, while the thinner one is used only when space is tight. The third grooving tool is used for finishing, leaving behind a quality, burr-free surface finish while holding dimensional tolerances of less than 0.010-inch on all linear dimensions along a 24-inch-long camshaft.
Introduced by Zeiger and Spark Industries at the PTXPO, the nozzle is designed for maximum heat transfer and uniformity with a continuous taper for self cleaning.
3D printing makes it possible to support custom geometry and tweaks to a product design like a forearm cast, so that each part can be tailored to the user.
Resin supplier Celanese turned to startup Rafinex and its Möbius software to optimize the design for an engine bracket, ultimately reducing weight by 25% while maintaining mechanical performance and function.
Plastics Technology’s Tech Days is back! Every Tuesday in October, a series of five online presentations will be given by industry supplier around the following topics: Injection Molding — New Technologies, Efficiencies Film Extrusion — New Technologies, Efficiencies Upstream/Downstream Operations Injection Molding — Sustainability Extrusion — Compounding Coming out of NPE2024, PT identified a variety of topics, technologies and trends that are driving and shaping the evolution of plastic products manufacturing — from recycling/recyclability and energy optimization to AI-based process control and automation implementation. PT Tech Days is designed to provide a robust, curated, accessible platform through which plastics professionals can explore these trends, have direct access to subject-matter experts and develop strategies for applying solutions in their operations.
Comp Cams’s goal is to be a leading developer of innovative valve train components, Mr. Godbold explains. Machining is viewed as a means to that end. Mr. Godbold says companies with a similar approach are well-served to recognize their manufacturing limitations, especially when considering the addition of a complex lathe like the LT-300MY. It’s best to devote some time to learning the ins and outs of such a machine before depending on it for production, he notes.
Plastics Technology’s Tech Days is back! Every Tuesday in October, a series of five online presentations will be given by industry supplier around the following topics: Injection Molding — New Technologies, Efficiencies Film Extrusion — New Technologies, Efficiencies Upstream/Downstream Operations Injection Molding — Sustainability Extrusion — Compounding Coming out of NPE2024, PT identified a variety of topics, technologies and trends that are driving and shaping the evolution of plastic products manufacturing — from recycling/recyclability and energy optimization to AI-based process control and automation implementation. PT Tech Days is designed to provide a robust, curated, accessible platform through which plastics professionals can explore these trends, have direct access to subject-matter experts and develop strategies for applying solutions in their operations.
Across all process types, sustainability was a big theme at NPE2024. But there was plenty to see in automation and artificial intelligence as well.
Mike Sepe has authored more than 25 ANTEC papers and more than 250 articles illustrating the importance of this interdisciplanary approach. In this collection, we present some of his best work during the years he has been contributing for Plastics Technology Magazine.
Ultradent's entry of its Umbrella cheek retractor took home the awards for Technical Sophistication and Achievement in Economics and Efficiency at PTXPO.
The need for tooling adds automatic lead time to producing a new molded part, but 3D printing can enable a manufacturer to jump straight into production while waiting for that tooling. This means that new products can be launched into the marketplace sooner, and brand owners can get feedback before committing to the expense of a mold. The bridge need not start at the beginning of a product’s life span, either — many companies are now turning to 3D printing to bridge gaps due to supply chain disruptions as well.
While prices moved up for three of the five commodity resins, there was potential for a flat trajectory for the rest of the third quarter.
Comp Cams has refined this process to the point that it can now machine camshaft cores in 35 to 45 minutes. That said, the company had to overcome some initial machining hurdles in order to achieve these faster cycle times.
The Plastics Industry Association (PLASTICS) has released final figures for NPE2024: The Plastics Show (May 6-10; Orlando) that officially make it the largest ever NPE in several key metrics.
Multiple speakers at Molding 2023 will address the ways simulation can impact material substitution decisions, process profitability and simplification of mold design.
Additive technology creates air pockets in film during orientation, cutting down on the amount of resin needed while boosting opacity, mechanical properties and recyclability.
The company uses Exsys/Eppinger Preci-Flex ER32 quick-change adaptors for some of its live-tooling work. Each adaptor can accommodate a drill, tap or mill for use in that single station. During setup, each tool is separately installed in the adaptor and touched off. During a production run, a program stop pauses the machine and prompts the operator to change the tool in the adaptor station to the next tool needed. The operator can change the tool in less than one minute, and touch-off isn’t necessary because the offset for each tool was determined during setup. Mr. Freeman says tools in the adaptor extend out a couple inches farther than normal, but this does not present any clearance issues.
In this collection of content, we provide expert advice on welding from some of the leading authorities in the field, with tips on such matters as controls, as well as insights on how to solve common problems in welding.
Introduced by Zeiger and Spark Industries at the PTXPO, the nozzle is designed for maximum heat transfer and uniformity with a continuous taper for self cleaning.
Join KraussMaffei for an insightful webinar designed for industry professionals, engineers and anyone interested in the manufacturing processes of PVC pipes. This session will provide a comprehensive understanding of the technology behind the production of high-quality PVC pipes: from raw material preparation to final product testing. Agenda: Introduction to PVC extrusion: overview of the basic principles of PVC pipe extrusion — including the process of melting and shaping PVC resin into pipe forms Equipment and machinery: detailed explanation of the key equipment involved — such as extruders, dies and cooling systems — and their roles in the extrusion process Process parameters: insight into the critical process parameters like temperature, pressure and cooling rates that influence the quality and consistency of the final PVC pipes Energy efficiency: examination of ways to save material and energy use when extruding PVC pipe products
Take a deep dive into all of the various aspects of part quoting to ensure you’ve got all the bases—as in costs—covered before preparing your customer’s quote for services.
Affordable desktop 3D printers make it possible to create affordable items for plant use such as inspection fixtures, assembly tools and check gages. CMM nests, for example, can be developed using mold design tools to generate the inverse of the part and arrive at a 3D-printable fixture design. As an added bonus, once fixtures have been developed for 3D printing, they can be saved as digital files. Should one be damaged or go missing, it can be quickly replaced by simply printing another.
Thousands of people visit our Supplier Guide every day to source equipment and materials. Get in front of them with a free company profile.
Once relegated to rapid prototyping, 3D printing technology has now advanced far beyond the design studio. Machines have improved and material options have widened. Today molders, moldmakers and OEMs alike are turning to this layer-by-layer production technology to save time, serve new markets and even fill supply chain gaps.
Sustainability continues to dominate new additives technology, but upping performance is also evident. Most of the new additives have been targeted to commodity resins and particularly polyolefins.
In this three-part collection, veteran molder and moldmaker Jim Fattori brings to bear his 40+ years of on-the-job experience and provides molders his “from the trenches” perspective on on the why, where and how of venting injection molds. Take the trial-and-error out of the molding venting process.
Core Technology Molding turned to Mold-Masters E-Multi auxiliary injection unit to help it win a job and dramatically change its process.
With it acquisition of DuPont’s engineering resins, Celanese’s resin solutions for automotive electrification, e-mobility and consumer electronics are plentiful.
Mr. Godbold believes this approach made all the difference in the world. He humbly says that Comp Cams proves that a shop with only conventional turning and milling experience can successfully integrate a complex multifunction machine without necessarily being outstanding at machining or programming. However, this requires establishing solid relationships with equipment suppliers that are willing to help a shop achieve its goals. Finding trusted people to work with means everything, he says.
While prices moved up for three of the five commodity resins, there was potential for a flat trajectory for the rest of the third quarter.
This Knowledge Center provides an overview of the considerations needed to understand the purchase, operation, and maintenance of a process cooling system.
In this collection, which is part one of a series representing some of John’s finest work, we present you with five articles that we think you will refer to time and again as you look to solve problems, cut cycle times and improve the quality of the parts you mold.
Join Wittmann for an engaging webinar on the transformative impact of manufacturing execution systems (MES) in the plastic injection molding industry. Discover how MES enhances production efficiency, quality control and real-time monitoring while also reducing downtime. It will explore the integration of MES with existing systems, emphasizing compliance and traceability for automotive and medical sectors. Learn about the latest advancements in IoT and AI technologies and how they drive innovation and continuous improvement in MES. Agenda: Overview of MES benefits What is MES? Definition, role and brief history Historical perspective and evolution Longevity and analytics Connectivity: importance, standards and integration Advantages of MES: efficiency, real-time data, traceability and cost savings Emerging technologies: IoT and AI in MES
Gifted with extraordinary technical know how and an authoritative yet plain English writing style, in this collection of articles Fattori offers his insights on a variety of molding-related topics that are bound to make your days on the production floor go a little bit better.
When I first spoke to Billy Godbold, he was at a track watching a professional drag racing team test a custom camshaft. Mr. Godbold is the engineering group leader for Comp Cams, the valve train component manufacturer that supplied the camshaft. One month earlier, Comp Cams’ design group had just started contemplating camshaft materials and geometries for this application. Moving from design to completed billet camshaft so quickly would not have been possible years ago when the company outsourced the machining of its high-end racing camshafts.
Discover how artifical intelligence is revolutionizing plastics processing. Hear from industry experts on the future impact of AI on your operations and envision a fully interconnected plant.
Uniloy is revising its machinery lines across the board and strengthening after-sales services in tooling maintenance, spare parts and tech service.
Discover how artifical intelligence is revolutionizing plastics processing. Hear from industry experts on the future impact of AI on your operations and envision a fully interconnected plant.
The company selected an Okuma LT300-MY. Mr. Godbold says that in many ways, the initial concept and programming execution were greater hurdles than the slight machine modifications that were needed for this application. The primary mechanical change to the machine was increasing the size of the sleeves in the main and subspindles so a 70-mm-journal camshaft could pass through them. The company reasoned that because the machine offered a great deal of rigidity and each of its spindles provided 30 horsepower, the lathe would have no problem machining the tough M4 powder-metal tool steels (rated at 30 HRc) common to its billet racing camshafts.
Despite price increase nominations going into second quarter, it appeared there was potential for generally flat pricing with the exception of a major downward correction for PP.
Wednesday, May 8 | 1:00 – 5:00 PM Orange County Convention Center The 3D Printing Workshop at NPE2024: The Plastics Show, is an immersive, half-day workshop focused on the emerging possibilities for part production via 3D printing and additive manufacturing.
Successfully starting or restarting an injection molding machine is less about ticking boxes on a rote checklist and more about individually assessing each processing scenario and its unique variables.
This month’s resin pricing report includes PT’s quarterly check-in on select engineering resins, including nylon 6 and 66.
Mold maintenance is critical, and with this collection of content we’ve bundled some of the very best advice we’ve published on repairing, maintaining, evaluating and even hanging molds on injection molding machines.
Additive technology creates air pockets in film during orientation, cutting down on the amount of resin needed while boosting opacity, mechanical properties and recyclability.
Join Engel in exploring the future of battery molding technology. Discover advancements in thermoplastic composites for battery housings, innovative automation solutions and the latest in large-tonnage equipment designed for e-mobility — all with a focus on cost-efficient solutions. Agenda: Learn about cutting-edge thermoplastic composites for durable, sustainable and cost-efficient battery housings Explore advanced automation concepts for efficient and scalable production See the latest large-tonnage equipment and technology innovations for e-mobility solutions
GETTING A QUOTE WITH LK-MOULD IS FREE AND SIMPLE.
FIND MORE OF OUR SERVICES:
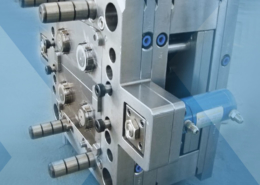
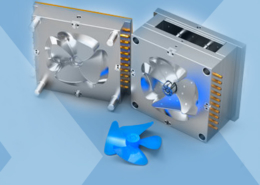
Plastic Molding

Rapid Prototyping
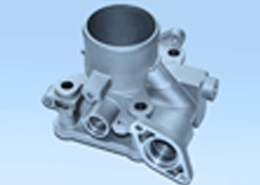
Pressure Die Casting
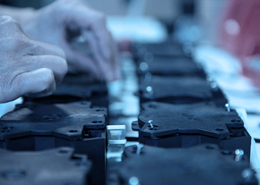
Parts Assembly
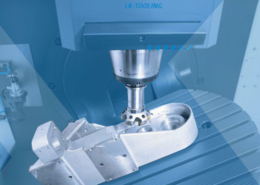