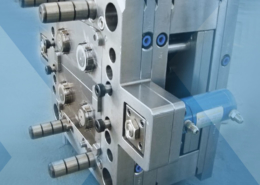
Making Cooling Time Productive With a Shuttle Mold System - injection mold fabri
Author:gly Date: 2024-09-30
Offering a user experience that merges rider intent and independence with the protection and assistance that LUCI’s technology provides also was a priority.
The Boddingtons cleanroom facility has now doubled in size since the factory opening. Boddingtons commercial and technical manager, Chris Philpott notes that “the medical sector requires so much from its suppliers in terms of complete control, traceability, process stability and consistency and all following fully validated manufacturing processes within our Class 7 cleanroom was always the way to go, it is why we invested heavily to support the needs of our customers within the medtech sector.
The plastic housings that contain the radar sensors posed a design challenge, Jered said, because those housings need to be “invisible” to the business card-sized radar sensors, while also being a certain shape, material and thinness to enable the radar devices to do their job of identifying potential hazards.
What they came up with, along with a little manufacturing help from Protolabs, is LUCI, an attachable accessory system that brings smart technology to power wheelchairs for stability, security and connectivity.
The full operation of the Boddingtons Class 7 cleanroom means a failsafe and scrupulous approach to standards, now expressed in the pages of the operation and training manual at the company. No staff at Boddingtons are allowed access to the cleanroom without a minimum of two full days of training. There are no exceptions. Just one incident of non-conformance, not following the stringent procedures just to enter the room itself can close the cleanroom for a deep cleanse. Standards are of the highest level, control and discipline has been trained into every staff member to maintain these high levels.
When the team mentioned their concern about robustly securing the plastic housings to LUCI’S frame, Protolabs suggested using its insert molding service. Insert molding in this case incorporates threaded metal inserts into LUCI’s molded plastic housings to improve their strength when they’re attached to the frame. Insert molding is working so well that LUCI now uses it whenever attaching plastic parts securely to metal.
Boddingtons is a company that operates a facility in Southeast England for the production of injection-moulded components, medical devices and assemblies. All manufacturing is included within the scope of ISO 13485 MDSAP and ISO 14001 accreditations.
The team landed on an ABS plastic that was durable, cost-effective and compatible with the radar sensors. The part would be injection molded at the thinness required, enabling the radar devices to work properly. LUCI iterated rapidly on the housings, cutting test tools, having prototypes made and working on revisions before making new tools for another round of prototyping. The process overall was more cost-effective. If the team went with a traditional injection molder, higher costs and slower turnaround would have meant fewer iterations and more guesswork.
A modular Class 7 cleanroom was established within the new Boddingtons factory straightaway, as the company believes that to succeed in medtech device manufacture, Class 7 cleanroom technology assets are essential and mandatory to make approved Class 1 and Class 2 medical devices. The controls, filtration and essentially the bio-burden must all be monitored regularly and maintained to de-risk products that especially come into patient contact.
To come up with solution, the LUCI engineering team used Protolabs digital quoting platform for design-for-manufacturability (DfM) feedback early on in designing plastic housings for LUCI’s sensors and electronics. Getting the design just right for the housings holding the millimeter-wave radar sensors required iteration and help from Protolabs engineers.
For example, when new injection moulding machines were introduced to the Boddingtons Class 7 cleanroom environment, the material feedstock from outside the facility needed to be expanded – but not so as to interfere with existing production and standards. A second materials link was accordingly created ensuring a dedicated material flow to the new moulding machines while enhancing material control and full traceability.
After years of development, the Dean brothers began selling the LUCI system in early 2021. The system was quick to receive widespread recognition, its accolades including Time’s Best Inventions of 2020, Popular Science’s Best of What’s New, a CES 2021 Health & Wellness Innovation Award and Mobility Management’s “Smart Technology” Product Award.
Protolabs delivered injection-molded parts within three to four weeks, with expedited orders coming in as little as five days. That compares to 16 weeks or longer to order a mold and get first articles from a traditional injection molding service with less flexibility to make rapid iterations to part designs.
As a power wheelchair user steers LUCI with a joystick or other means, onboard sensors map the surroundings to avoid anything in the way, such as curbs, pets or people. The mapping technology includes millimeter-wave radar sensors that detect the range, velocity and angle of objects in the environment.
Sheet metal fabrication service was also used to prototype dozens of parts for the smart frame and brackets that hold LUCI’s sensors. For the dashboard, the team utilized a pad printing process, which transfers a two-dimensional image, like a company logo, to a three-dimensional object. The pad printed symbols are more attractive, durable, and convenient, given that Protolabs was already making LUCI’s dashboard.
Power wheelchair users have the potential to get hurt when their devices, which weigh hundreds of pounds, tip over or run into objects. For brothers Barry and Jered Dean, the danger was one that hit home as Barry’s daughter, Katherine, used a power wheelchair. When a family friend was sent to the hospital after a wheelchair fall, the Dean brothers set out to find a solution that would make his daughter’s chair safer while helping all power chair users avoid potential pitfalls.
Another concern was finding a way to securely attach the plastic housings holding LUCI’s various sensors and electronics to the system’s Smart Frame. The frame is a sheet metal platform that is mounted between the seat and wheels of a new or existing power wheelchair to install the LUCI system.
For the speed and flexibility required, they turned to Protolabs for injection molding of plastic prototypes and production parts, as well as sheet metal fabrication for prototypes of the chair’s platform. The team required quick-turn parts because they were not only developing fast, but also with a lot of unknowns.
In addition to their urgency to create a safer alternative for Katherine and other power wheelchair riders, the Deans’ announcement of their intent to develop such a product generated intense interest from wheelchair manufacturers.
To paraphrase an advert from a leading UK retailer: there’s injection moulding in manufacturing and then there’s medtech injection moulding.
Chris Philpott, commercial and technical manager at Boddingtons, explains the importance of choosing the right injection moulder and the story behind their Class 7 cleanroom.
The design team worked urgently to deliver LUCI to the market, given their personal stake and the high level of interest from potential users. That urgency trickled through to everything, including their choice of manufacturing partner. The goal from the beginning was getting LUCI to the largest number of users possible. For many, it was the difference between someone being able to independently drive themselves and somebody being pushed or not having that freedom in all locations.
One expression of that needed to be through LUCI’s dashboard. The dashboard, located on the wheelchair’s control panel has four indicator lights to track things like Wi-Fi, cellular connection and sensor obstruction. The team wanted each light to have a corresponding symbol that would clearly identify its function while also being attractive and durable.
These high standards need to accommodate and prevail for all new Class 7 cleanroom medtech projects in all circumstances: Any item, person or material entering the cleanroom environment is subject to its stringent protocols.
Philpott points out that “injection moulders should take note that – even after investment and capital outlay - Class 7 cleanroom benefits do not come without ongoing costs – in terms of energy, rigorous maintenance, deep cleaning and an audit process that could see customers or regulatory bodies arriving unannounced at any time – day or night. All of which requires us to properly resource and commit to our cleanroom moulding, not least in terms of our people where a culture of pride resides.”
Now that we are well along the curve of our Class 7 cleanroom expertise, we don’t hesitate to apply manufacturing lessons to other areas of our business; building additional cleanroom resource for specific new projects and applying cleanroom manufacturing disciplines across the whole of our facilities offering flexibility, capability and increased volume manufacturing.”
LUCI’s hardware and software combine to give power wheelchairs a 360-deg. view of the world to avoid collisions and drop-offs, as well as warn of tipping dangers. Cloud-based communications alert loved ones of an accident and securely send user data to family and medical team members. LUCI incorporates stereo-vision cameras and infrared, ultrasonic and radar sensors in a patented, first-of-its-kind system that gets mounted between the seat and wheels of a power wheelchair.
For many clients in the medical sphere, it’s important to find a company that understands and can take primary legal responsibility for all regulatory matters of medical device manufacture, from concept design following design and development processes and procedures, process optimisation & validations, whilst maintaining conformity to international medical standards such as MHRA & FDA including device registrations and working to the Medical Device Regulations (MDR).
Additionally, sheet metal prototypes arrived from Protolabs within a week compared with eight to 12 weeks from a traditional metal shop. LUCI continues to use Protolabs’ on-demand manufacturing to source end-use molded parts and to prototype plastic parts for more models of wheelchairs and new products.
GETTING A QUOTE WITH LK-MOULD IS FREE AND SIMPLE.
FIND MORE OF OUR SERVICES:
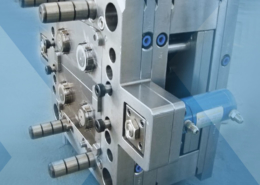
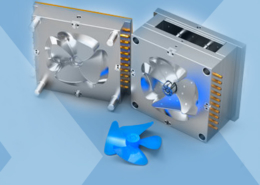
Plastic Molding

Rapid Prototyping
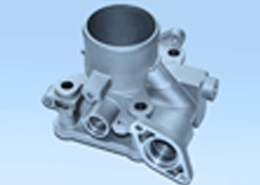
Pressure Die Casting
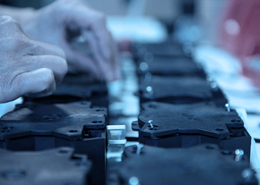
Parts Assembly
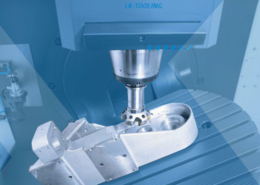