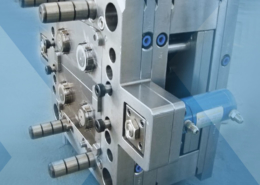
Made Using 100% Waste, These Bricks Cost Just Rs 10 & Are 250% Stronger! - paver
Author:gly Date: 2024-09-30
Discover suppliers of these and more in our advertisers’ index and buyer’s guide, available in the back of PIM International.
The free-to-access PIM International magazine archive offers unparalleled insight into the world of MIM, CIM and sinter-based AM from a commercial and technological perspective through:
The sheer number of small cooling pins in such applications, all packed within a small confined space, maximise the overall surface area and hence optimise thermal efficiency.
Thin thin-wall (<1 mm or 0.04 in.) intricate fibre optic connectors housings are often made from 17-4 PH stainless steel. The parts are used in a parallel optical module for ultra-high-speed transceivers in networking and telecom equipment. In addition to the very thin walls, the MIM housing are able to integrate numerous complex details.
Until she retired in September 2021, Clare Goldsberry reported on the plastics industry for more than 30 years. In addition to the 10,000+ articles she has written, by her own estimation, she is the author of several books, including The Business of Injection Molding: How to succeed as a custom molder and Purchasing Injection Molds: A buyers guide. Goldsberry is a member of the Plastics Pioneers Association. She reflected on her long career in "Time to Say Good-Bye."
Few other technologies can compete with Metal Injection Molding’s combination of high volume capability and tight tolerances. This is just one of many MIM applications that can be found in smartphones and mobile devices produced by a wide range of OEMs.
Metal Injection Molding is used to produce Apple’s Lightning connector, a component that is produced in the tens of millions per week at peak production. Such small, complex, high volume components can be produced in multi-cavity molds to net-shape.
“Over the years, as our customers’ demands grew, we responded by broadening our value-added service offerings,” said Paul Ziegenhorn, President. “In 1995, we put our first molding press on the floor so we could perform our own mold samplings and run small volumes for our customers. We also expanded our inspection capabilities by adding a quality assurance lab and certified our quality systems to ISO 9001 by 1999, one of the first mold shops to do so. At that time, molding production made up a very small portion of our sales, but the momentum had already begun.”
The parts were made from 17-4 PH stainless steel and the MIM process allowed very thin walls, overhanging structures and a complex overall design. The parts also demonstrated the high quality polished finish that can be achieved.
Extensive MIM, CIM industry and sinter-based AM industry news, plus the following exclusive deep-dive articles and reports:
Given the evolution of the company, the decision to move forward with the single corporate identity Matrix Plastic Products is both practical and tactical. “It is the more inclusive name and better represents our broader mix of services today,” said Andy Ziegenhorn, COO. “But we are still moldmakers by trade, so ensuring the integrity of the tools we run in production will always be hard-wired into the way we operate here.”
The ongoing miniaturisation of electronic devices calls for ever smaller parts with better performance at lower cost. This is where Metal Injection Moulding can put forward its strengths.
Reach a truly international audience that includes component manufacturers, end-users, industry suppliers, analysts, researchers and more.
The electronics industry is a major user of Metal Injection Molded parts, resulting in Asia accounting for more than 50% of global MIM parts sales. Smartphone camera housings, buttons, hinges for folding phones, and connectors of complex geometries are now staple MIM products.
Copper coldplates produced by Metal Injection Moulding leverage the full benefits of the MIM process, with shaping capability that gives designers maximum flexibility for innovative design concepts. In this type of pin geometries, which provides optimum thermal performance.
Founded in 1978 by brothers Paul and James Ziegenhorn and their father, William, Matrix Tooling Inc. began with seven employees, “a rich family tradition of moldmaking craftsmanship, and an unwavering focus on customer service,” said Matrix’s news release. In 2000, Matrix secured the trade name Matrix Plastic Products and built a 10,000-square-foot addition dedicated to molding production. An ISO Class 8 cleanroom was installed in 2006 to accommodate the company’s growing emphasis on medical business. ISO 13485 certification followed in 2010.
Today, Matrix Plastic Products operates 15 presses ranging from 5 to 300 tons, and has added assembly and 3D prototyping to further extend its full-service menu. The QA lab has also grown and features four OGP multi-sensor metrology systems to support myriad advanced inspection protocols. A CT scanner is on the soon-to-come list.
The company’s roots are in moldmaking. Today, it incorporates precision moldmaking with injection molding and other value-added services to produce critical components and sub-assemblies for customers in medical manufacturing and other sectors.
Matrix Plastic Products Inc. (formerly known as Matrix Tooling Inc. & Matrix Plastic Products), is celebrating “40 successful years in business” with a new corporate name and website. Matrix Plastic Products (Wood Dale, IL) is a plastic injection molder of critical components that also designs and builds the ultra-precise molds required to produce components for the medical device industry and other high-performance applications.
Don't miss any new issue of PIM International, and stay up to date with the latest industry news. Sign up to our fortnightly newsletter.
“This company has never shied away from technology,” said Gary Johansson, VP of Quality/Regulatory. “We understand that we need to have better equipment than the competition to keep the high-level work coming here.”
Matrix Plastic Products molds critical components and builds the ultra-precise molds required to produce components for the medical device industry.
Four decades and three buildings later, Matrix has evolved from strictly a mold design and fabrication shop into a premier plastics manufacturing facility that incorporates moldmaking with injection molding and other value-added services to produce critical components and sub-assemblies for the medical device industry.
Although from a long discontinued mobile phone, this flip slider and hinge barrel are two parts which mark a milestone in MIM’s adoption in the consumer electronics sector. This mechanism allowed a clamshell style phone cover to slide up and down and flip open in a single movement.
In this report, Dr Paul A Davies, Sandvik Osprey Ltd, provides an overview of the evolution of the region’s MIM industry from a powder producer’s perspective. With selected application examples and data from the recent APMA 2017 conference, the report offers insights into the drivers for growth and how these have stimulated continued investment in capacity.
The thermal performance of the MIM coldplate therefore bring a competitive edge when compared with other manufacturing processes.
The MIM industry in Asia is the world’s largest, whether considered in terms of number of parts produced, sales turnover or production volume. China alone is reported to offer half of the world’s installed MIM capacity, with production predominantly focused on 3C applications.
GETTING A QUOTE WITH LK-MOULD IS FREE AND SIMPLE.
FIND MORE OF OUR SERVICES:
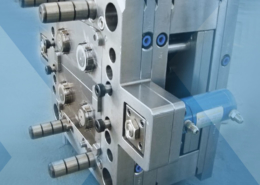
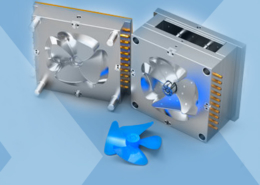
Plastic Molding

Rapid Prototyping
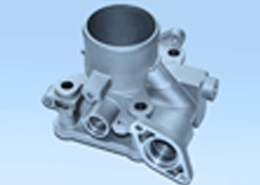
Pressure Die Casting
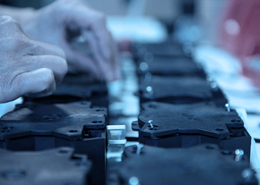
Parts Assembly
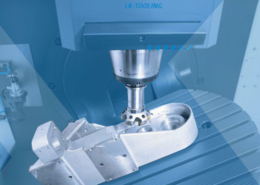