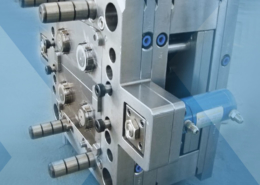
Made Using 100% Waste, These Bricks Cost Just Rs 10 & Are 250% Stronger! - paver
Author:gly Date: 2024-09-30
“The decision was strategic but also a timely investment. It led to many more doors opening and helped improve the company’s performance and competitiveness, while at the same time increasing our customer base for design and manufacture of dies and moulds. This is after all the core focus of the business,” continued Anthony.
For any plastics manufacturer, zero defects remain the target. In the medical industry, for example, there’s no wiggle room. You can’t shift the parameters to suit. If you’re producing a medical device or a sterile implant, nothing less than 100 percent quality is acceptable.
“We had been growing at 40% per annum and when you grow at such a rate, productivity is always a critical concern for any and every manufacturer or machine shop. We had already started on a route to invest in the latest advanced manufacturing technologies so it was an easy decision to invest in a DMG Mori Milltap 700, the first joint development from DMG and Mori Seiki. The Milltap 700 is a compact machining centre with tool changes in 0.9 seconds and chip-to-chip times of less than 1.5 seconds, rapid traverses of 60 m/min, a 24 000 rpm spindle, and it is equipped with a Siemens 840D control,” explained Jarrad.
Although not a prerequisite for the automotive and packaging sector, validation can be good business practice for a large number of mass manufacturers of injection-moulded components. Think of it as a long-term investment. Essentially, it’s a risk assessment which, when executed professionally, can deliver efficiency gains and save your business time, money and resources by ensuring product integrity and reducing scrap volumes.
When Anthony’s son Jarrad joined him in 2010 they decided to expand and get back into the manufacture of tools, moulds and dies.
The final validation phase - Continued Process Verification - focuses on demonstrating that your process is consistently stable. It involves simulating different production runs using the same production equipment and the processes that you will be routinely using, ensuring repeatability of the set-up conditions throughout the machine’s full lifecycle.
At the Process Design stage you are looking to see if you have the proper sized machine - shot size and tonnage - and that the equipment is properly calibrated.
Success comes to shops that are attentive to the changing needs of their customers. Such shops are generally willing to make fundamental manufacturing changes and process additions, when appropriate, to best meet those demands. In a growing number of cases, a shop’s customer wants to receive more than just a component that has been accurately machined.
When it comes to product quality in injection moulding, machine and tool validation is fundamental to creating a stable manufacturing process and de-risking the project. Yet, it’s often bureaucracy rather than methodology that drives companies to validate. James Hines, Process and Training Engineer at Sumitomo (SHI) Demag goes back to the basics of why we validate and why this complex process shouldn’t be just regarded as a tick-box exercise to get the FDA or other regulatory bodies off your back.
“I started out primarily as a design studio specialising in plastic product design and development, coupled with mould design. At that stage the manufacture of the tooling was outsourced. During my career as a toolmaker I learnt how to use and take advantage of the CAD/CAM design software available. In fact I believe that I was one of the first in South Africa to use the Vero Visi CAD/CAM software supplied by Software Development in South Africa, and I have remained loyal to the brand ever since. That was over 27 years ago,” said Anthony.
The validation process requires a step-by-step approach, working with each customer to break down each element of each injection moulding cycle and documenting every stage. Conducted by an engineer, the actual validation usually takes longer than actually building the tool itself. For this reason, the validation is often partially completed at the toolmakers’ facility by a senior engineer from the company as this allows issues to be addressed there and then on site, rather than shipping the tool back and forth. Ultimately, the final phases of the validation will be completed in-house on the specified equipment.
During the Process Qualification phase, you will move on to establish the range of process parameters. This involves conducting a selection of statistical and dimensional studies, enabling you to identify and investigate any deviations in the process. A process is not considered as validated if the variations have negatively impacted the finished product in any way.
“We could have invested in two different machines but the Milltap 700, which was supplied by Retecon Machine Tools, allows us to machine-to-completion precision parts in fewer set-ups and reduced cycle times.”
“We were then able to offer a total project management service. After the design phase, this service includes having development components machined or grown samples made, to manufacturing of the moulds,” continued Jarrad.
New home, new machines With the increase in business the company moved to a bigger factory in the same industrial park, which is located in Spartan, Gauteng, in February 2014. The move afforded the company the opportunity to increase its machining capacity to help take the pressure off the company’s existing equipment.
Gantec Tool and Die owner Anthony Barnes has always been conscious of this fact since he established the company in 2008.
Like before, there are three key phases to process validation, only now the FDA categorises them as Process Design, Process Qualification, and Continued Process Verification. These reflect the focus on the manufacturing lifecycle and the need to provide scientifically sound data to verify that your injection moulding processes start and continue to remain stable.
Before you start validating, it is vital to be clear on your expectations. If it’s to provide a documented source of evidence to satisfy a regulatory body, you need to do it. But that shouldn’t be your sole motivation. Validation is not purely about procedures and scrambling to put the correct documentation in place. The objective of having an efficient process and repeatable high product quality should never be overlooked, as this is ultimately how you can avoid costly product recalls and cosmetic product defects.
The company’s services now include component design, development and liaising with client to mould design and mould manufacture. We design and manufacture high-tech moulds for intricate components, including high-speed automatic unscrewing moulds, and incorporation of hot runnerless injection systems.
The DMG MORI Milltap 700, which was supplied by Retecon Machine Tools, allows Gantec Tool and Die to machine-to-completion precision parts in fewer set-ups and reduced cycle times. The Milltap 700 is a compact machining centre with tool changes in 0.9 seconds, and chip-to-chip times of less than 1.5 seconds, rapid traverses of 60 m/min, a 24 000 rpm spindle, and it is equipped with a Siemens 840D control
“We also made a substantial investment in the CAD/CAM design software, which includes full 3D solid and surface modeling, presentation shading, drafting and dimensioning, intricate split line generation and mould build libraries,” added Jarrad.
In accordance with ISO 13485 standards, ongoing documentation of the injection moulding process needs to be maintained. This is a continuous process, which is a significant change under the new directive. From time to time, machine settings may have to be adjusted to compensate for changes in the environment or to address moulding issues, such as pulling, distortion, or aesthetic defects. The key areas that might impact a stable process include changes in pressure, temperature, flow rate and cooling rates, any of which may trigger a re-validation exercise.
At the same time the company introduced another CNC lathe, a spark eroder and an injection moulding machine so that they could run trials with the moulds they were manufacturing.
“This is why we looked at the relatively new process of laser welding, and purchased a German manufactured OR Laser 3300 which was supplied by Retecon Machine Tools in 2012” said Anthony.
The company’s commitment to continuous improvement and its progressive attitude to investing in the future have seen Gantec Tool and Die branch out and provide moulds for other industries, including closures and packaging. In addition to investing in its equipment, manufacturing processes and systems they have also invested in their people. They recently hired two apprentices.
Laser welding, maintenance and repairs “We also offered a service to maintain the moulds. Because of the extreme use of moulds in the plastic industry you are always going to have the necessity of repairs. But we felt that the industry standard repairs were not a good enough end result for our clients,” explained Anthony.
Going back to the basics of why validation exists, it’s to ensure that injection moulders have a stable and dimensionally centred process that consistently produces high quality products. Validation is basically providing the scientific evidence that the machine and tool is repeatedly doing everything you expect it to do, every minute of every day.
From a business perspective, validation will also address profit-driven challenges and design out production weaknesses. Functional tests can help operatives better understand what drives the machine, how fast it goes and the consequences if manufacturing procedures are not correctly followed. In some instances, ramping up to a faster cycle time won’t always be the most optimised process.
Major repairs, changes, or improvements to the mould tool may require changes in the set up, and this would mean re-validating the process. This is also true of the moulding machines. Significant repairs or machine exchanges if not carefully managed and controlled may trigger a full validation of the process, which takes time and costs the moulder more money.
“Our customers were demanding that we take control of their projects from beginning to end. So we purchased the necessary toolroom machinery including a brand new Leadwell V-40 CNC vertical machining centre.”
Last year the European Commission issued its first update since 2001, causing more confusion. The new version of Annex 15 now requires manufacturers to ensure that “critical aspects” of their operation are validated throughout the product lifecycle. This includes any changes that could impact a product’s quality. Effective 1st October 2015, the amendment to EurdraLex Volume 4, Annex 15: Qualification and Validation closely mirror the FDA’s (U.S. Food and Drug Administration) lifecycle approach. There’s also a greater emphasis on risk management to reflect today’s manufacturing and regulatory environment. So, how do these changes impact manufacturers?
GETTING A QUOTE WITH LK-MOULD IS FREE AND SIMPLE.
FIND MORE OF OUR SERVICES:
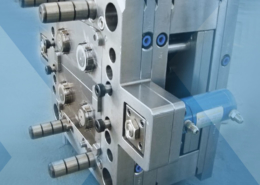
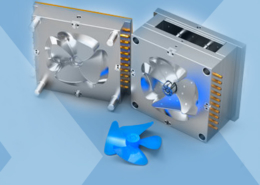
Plastic Molding

Rapid Prototyping
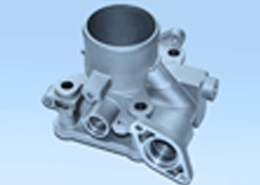
Pressure Die Casting
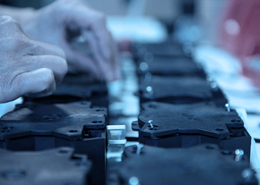
Parts Assembly
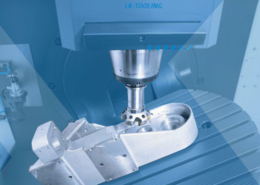