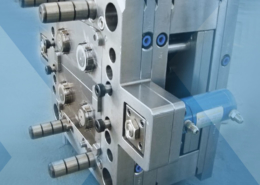
LS Mtron Presses Ahead in North America - plastic mold press
Author:gly Date: 2024-09-30
At the upcoming Fakuma trade show in Friedrichshafen (Germany), Swiss injection molding machine manufacturer Netstal will be presenting what the company says is a “world firstâ€: injection compression molding on a stack mold. Netstal will be demonstrating the new technology at its booth in hall A7 (7303/7304), where a 15oz (425g) margarine tub made from PP and weighing only 10.7 g will be molded on a hybrid Elion injection press equipped with a four-by-four stack mold.The innovative technology is the result of a collaboration between mold manufacturer Plastisud, automation specialist Machines Pagès and Netstal. While the stack mold with 4+4 cavities is impressive enough, turning out standard-sized margarine with IML decoration in a cycle time of five seconds, the truly revolutionary aspect of the whole process is hidden from view, according to Markus Dal Pian, Vice President, Sales & Marketing at Netstal.“The polypropylene packaging is not injection molded but manufactured in an injection compression molding process," he explained. "This combination of injection compression molding and stack mold is a complete novelty in the industrial production of packaging."The cavities are partially filled in only 100 ms with extremely even results and the process is performed at a low pressure to prevent tension in the material. The high quality of the platen parallelism guarantees a synchronicity of 99.98 % between the mold, machine and automation system.The stack mold, especially adapted to the requirements of the new production process, was developed in a few short months by Plastisud. The unique injection compression molding technology guarantees perfectly balanced parting planes with an extremely low dispersion rate."The special design of the stack mold developed by Plastisud plays a key role in this application,†Thomas Iten, PAC Application Engineer at Netstal emphasized. Machines Pagès provided specific know-how in the area of handling systems for in-mold labeling (IML) to ensure that the automation process has been adapted perfectly to the machine and mold.According to Iten, this configuration, in which the injection compression molding process is combined with a specially balanced stack mold, is “a genuine innovative leap." The fundamental benefits of injection compression molding include narrow wall thicknesses and a lighter product resulting in lower unit costs. Furthermore, the end product (lids in particular) shows fewer signs of distortion and has a greater dimensional accuracy due to the lower stresses placed on the material.
"With more than 25 years of experience in the field of medical technology and production in cleanrooms, we are proud to further support our medical technology customers in the safe and effective production of their plastic articles," said Joachim Stiller, general manager of Braunform GmbH.
At the upcoming Fakuma trade show in Friedrichshafen (Germany), Swiss injection molding machine manufacturer Netstal will be presenting what the company says is a “world first”: injection compression molding on a stack mold. Netstal will be demonstrating the new technology at its booth in hall A7 (7303/7304), where a 15oz (425g) margarine tub made from PP and weighing only 10.7 g will be molded on a hybrid Elion injection press equipped with a four-by-four stack mold.
Braunform developed the Med Mold concept to ensure the safe use of injection molds in cleanrooms, based on a quarter century of experience in cleanroom production. Specifically developed for medical and pharmaceutical applications, Med Mold has been part of the company’s standard operations since 2010.
Synchronous lifting of the load-bearing core and stripping of the molded part saves time, mold costs, and installation space.
In the company’s proprietary Lift&Strip² technology, movement is initiated by the machine’s ejector, which lifts and strips the part simultaneously. A movable forced guidance system, the stripping mechanism moves synchronously with the mold opening. Previously, when the mold opened, stripping was actuated by a separate drive. This drive is no longer required and the two processes have been combined into one. This innovation reduces cycle times and increases efficiency, said Braunform.
Medical molding specialist Braunform GmbH will showcase at Fakuma next month how a combination of two technologies developed in-house enabled a mold design and process that optimized the production of insulin pen housings.
Editor in chief of PlasticsToday since 2015, Norbert Sparrow has more than 30 years of editorial experience in business-to-business media. He studied journalism at the Centre Universitaire d'Etudes du Journalisme in Strasbourg, France, where he earned a master's degree.
Braunform initially designed an eight-cavity pilot mold for testing purposes, which ultimately led to a 32-cavity production mold. Synchronized mechanical movements in combination with a horizontal part made it possible to perform direct injection via a valve gate.
German medical molding specialist Braunform combined two technologies developed in-house to reduce cycle times and optimize quality.
Moreover, using a stack mold significantly increase productivity, while the technology reduces material costs by up to 20%, in addition to providing total flexibility in terms of shape, appearance and decoration of the manufactured part.
Braunform will exhibit at booth 5207 in hall A5 at Fakuma. The international trade show for plastics processing returns to Friedrichshafen, Germany, on Oct. 15 to 19, 2024.
Quality is optimized because the horizontal positioning reduces flash formation compared with slider molds. The vertical arrangement also improves gate quality.
Gating options are optimized by enabling a horizontal lengthwise positioning of the parts. Side-gate applications can be avoided and conventional valve gate applications can be implemented.
GETTING A QUOTE WITH LK-MOULD IS FREE AND SIMPLE.
FIND MORE OF OUR SERVICES:
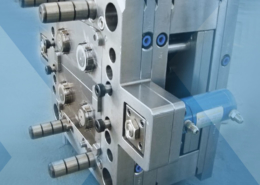
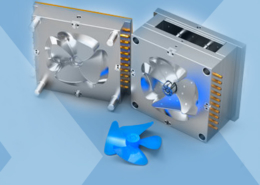
Plastic Molding

Rapid Prototyping
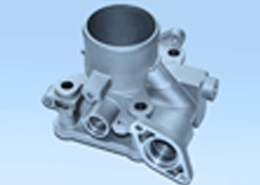
Pressure Die Casting
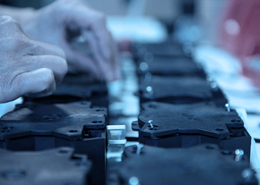
Parts Assembly
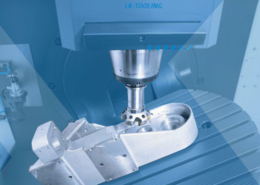