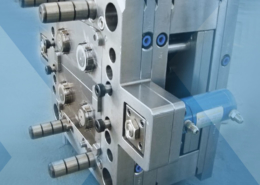
LS Mtron Presses Ahead in North America - plastic injection molding press
Author:gly Date: 2024-09-30
According to Structur3d, the Inj3ctor uses curated material cartridges to mix and inject 2-component flexible materials into any customizable shape, enabling turnkey, small-batch manufacturing of rubber materials.
About Prophecy Market Insights:Prophecy Market Insights is specialized market research, analytics, marketing/business strategy, and solutions that offers strategic and tactical support to clients for making well-informed business decisions and to identify and achieve high-value opportunities in the target business area. We also help our clients to address business challenges and provide the best possible solutions to overcome them and transform their business.
Finkel said product developers can “design a hyper-detailed mold using standard CAD software and 3D print the part with standard, durable or dissolvable plastic. Then users can choose from tens of thousands of liquid rubber materials, customizing it based on desired durability, flexibility, and cure time. After programming the mixing ratio and injection volume, the Inj3ctor fills in the mold, creating a fully customized, flexible product.”
There are several factors that are driving the growth of the plastic injection molding for medical device market, including:
Some potential challenges for the plastic injection molding for medical device market in the future include increasing competition, regulatory changes, and the need for more sustainable and eco-friendly materials. Opportunities include advancements in technology and materials science, increased demand for medical devices due to aging populations and the prevalence of chronic diseases, and growing healthcare infrastructure in emerging markets.
Analyst View:Increasing technological advancements in plastic injection molding techniques to make sure medical products are free from contamination and safer is additionally expected to drive the expansion of the respective market. Rising healthcare expenditure and spending in both developing and developed economies are among the crucial factors anticipated to bolster the worldwide plastic injection molding for the medical device market. Moreover, the growing global geriatric population, including the prevalence of chronic diseases, is another factor expected to fuel market growth.
The Global Plastic Injection Molding for Medical Device Market accounted for US$ 82.7 million in 2020 and is estimated to be US$ 148.88 million by 2030 and is anticipated to register a CAGR of 6.1%. The global plastic injection molding for medical device market report segments the market on the basis of type, end-user, and region.
Developed for the purpose of replacing short run or manual processes that currently exist in industrial injection molding, the Inj3ctor from Structur3d is reportedly the first additive manufacturing system to combine the principles of injection molding with 3D printing.
There are various applications of plastic injection molding in the medical device industry, such as manufacturing of diagnostic equipment, drug delivery systems, surgical instruments, disposable devices like syringes, IV tubing, and catheters, orthopedic implants, and dental instruments. Plastic injection molding is also used for producing housings, covers, and enclosures for medical devices.
The market provides detailed information regarding the industrial base, productivity, strengths, manufacturers, and recent trends which will help companies enlarge the businesses and promote financial growth. Furthermore, the report exhibits dynamic factors including segments, sub-segments, regional marketplaces, competition, dominant key players, and market forecasts. In addition, the market includes recent collaborations, mergers, acquisitions, and partnerships along with regulatory frameworks across different regions impacting the market trajectory. Recent technological advances and innovations influencing the global market are included in the report.
Zhong added that he sees Structur3d advancing prototyping by “opening up the arsenal we have available to tackle rubber components that are both easy to use, turnkey, and can produce a real, usable geometry prototype with the actual material you tend to use in production.”
Covina, March 16, 2023 (GLOBE NEWSWIRE) -- The Plastic Injection Molding for Medical Device Market accounted for US$ 82.7 million in 2020 and is estimated to be US$ 148.88 million by 2030 and is anticipated to register a CAGR of 6.1%. The medical plastic injection molding process is cost-efficient, and ideal for top volume production runs and applications requiring consistency and tight tolerances. This molding process is additionally used for medical device prototype development for the FDA approval process and to be used in laboratory testing. Since inception, the utilization of plastics within modern medicine has steadily increased. Medical devices that are manufactured from injection molded plastic have contributed to a discount in medical costs, communicable disease and pain management. High tech polymers are used within medical device prototype development and are commonly wont to create improved artificial limbs and devices that reduce the danger of infection. Medical plastic injection molding directly results in increased patient safety and therefore the ability to save lots of more lives. Since medical device plastics provide increased versatility and may be combined with metal to make enhanced medical product attributes, medical grade plastics became the well-liked material for varied sorts of electronic medical devices.
Some key challenges faced by manufacturers of plastic injection molding for medical devices include meeting regulatory requirements, ensuring product consistency and quality, managing costs, and keeping up with advancements in technology and materials.
GETTING A QUOTE WITH LK-MOULD IS FREE AND SIMPLE.
FIND MORE OF OUR SERVICES:
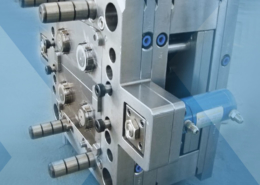
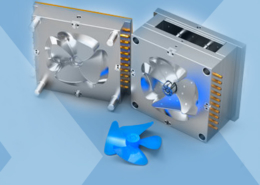
Plastic Molding

Rapid Prototyping
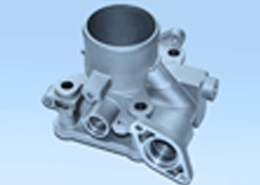
Pressure Die Casting
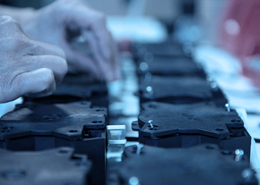
Parts Assembly
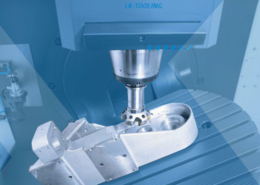