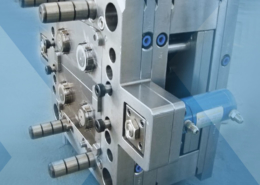
Injection Molding Using A 3D Printer - plastic injection molding part
Author:gly Date: 2024-09-30
Wittmann Battenfeld’s HiQ software can generally be retrofitted even to older injection molding machines equipped with a B8 machine control.
In terms of volume, HDPE is the third-largest commodity plastic material in the world, after polyvinyl chloride and polypropylene.
Comparing AI and machine learning, Glueck said, “AI actually requires a much higher time investment and, correspondingly, a higher financial investment. A large number of parameters must be recorded from a running process and the relevant parameters are determined on the basis of the deviations. These are compared with measurement data of the product.”
AI in manufacturing encompasses an array of technologies that allow machines to perform with intelligence that emulates that of humans. Machine learning and natural language processing help machines approximate the human capacity to learn, make judgments, and solve problems. Data-enhanced efficiency keeps processes moving faster and more cost-effectively.
S&P Global’s Chemical Economics Handbook – Polyethylene Resins, High-Density (HDPE) is the comprehensive and trusted guide for anyone seeking information on this industry. This latest report details global and regional information, including
Geoff Giordano is a tech journalist with more than 30 years’ experience in all facets of publishing. He has reported extensively on the gamut of plastics manufacturing technologies and issues, including 3D printing materials and methods; injection, blow, micro and rotomolding; additives, colorants and nanomodifiers; blown and cast films; packaging; thermoforming; tooling; ancillary equipment; and the circular economy. Contact him at [email protected].
Wittmann co-funded such an assessment program with Austria’s Montanuniversität Leoben university, “but we found that the time needed to make it workable for production had to be questioned because in addition to the long-term investigation of the process, you also need the manpower necessary to handle it.”
Arburg forms flexible — and controllable — production systems by combining machines, automation, and proprietary IT solutions. The company’s Gestica control system, with its intelligent assistant functions, is integral to those systems. “All Kuka six-axis robots, for example, have been equipped with the new Gestica user interface as standard,” Faulhaber noted. “This simplifies programming, as well as the monitoring, storage, and evaluation of process data.”
“One of Arburg's medium-term goals is to develop a system for digital twins of customized injection molding machines. This will open up completely new possibilities for simulating the cycle and making energy predictions. In addition, 3D views and installation plans of the machine — stored in the arburgXworld customer portal and in the control system — support the operator,” said Faulhaber.
Demand in Southeast Asia and mainland China is driven by film and sheet applications, whereas demand in the United States and Western Europe is driven by blow molding applications for HDPE resins.
One application Arburg is working on is the automatic programming of its Multilift linear robotic systems. “The idea is that the operator simply enters the destination, as with a car navigation device, and the system automatically calculates the optimal route. For robotic systems, this means that the operator simply enters the desired start and end positions, and the control system takes care of the rest.”
Construction and other consumer and industrial applications are influenced by business cycles and fluctuate in tandem with the economy because of the exposure of HDPE applications in construction, such as in piping.
World HDPE consumption is driven by mainland Chinese demand, which accounted for more than one-third of world consumption in 2022. Mainland Chinese polyethylene demand represents robust growth, whereas mature markets like the United States, Europe and Japan will either remain flat or grow at a comparatively small rate. The United States is characterized by increased supply in the global environment, whereas mainland China continues to drive Northeast Asian demand for the product.
Thanks to the integrated arburgXworld Control FillAssist, Arburg’s Allrounder "knows" the molded part it is supposed to produce. One issue for the future is to ensure that the machine not only keeps itself stable, but also self-optimizes.
“The technology draws new conclusions from current parameters and, thus, becomes increasingly intelligent as it monitors performance,” said Product Manager Christian Glueck. “We limit it to a methodical determination of parameters. Therefore, the time required to use the technology is minimal, as is the price.”
Arburg uses AI “to develop master models using experience and data collected over the years on process, material, and machinery,” Faulhaber continued. “The customer could then sharpen the provided master model ‘on edge’ and optimize their processes. The in-house development Gestica control system, the Arburg host computer system, and the arburgXworld customer portal give an advantage here.
As AI and machine learning are further leveraged to improve injection molding operations, simply gathering data is not enough to optimize processes, Faulhaber cautioned. “You also need the process expertise and domain knowledge. In the future, the evaluation of many data directly in the control unit will offer further added value.”
Another Wittmann feature, Eco-Vac conserves energy by setting a few parameters on the robot and allowing the robot to turn its vacuum circuits off and on. “The robot monitors the vacuum level of the circuit used for picking the part out of the mold. If the robot senses the vacuum has reduced to a level that it could drop the part before it is told to, the robot will turn the vacuum on until it reaches the safe level again, then shuts back off.” This feature cuts the amount of compressed air each robot uses “and could save customers hundreds of dollars a year per robot.”
By harnessing the reams of data produced in modern plastics processing facilities, artificial intelligence can improve machine performance.
Obtain the data you need to make the most informed decisions by accessing our extensive portfolio of information, analytics, and expertise. Sign in to the product or service center of your choice.
The HDPE industry is in a growth mode, with supply and demand continuing to increase strongly in 2022–2027. Demand will continue to be dominated by Asia, primarily mainland China. Northeast Asia alone is forecast to consume more than one-third of the total global consumption in 2027. Historically, traditional established economies such as North America, Western Europe and Japan produced HDPE. The recent growth of the polyethylene industry has resulted in the shifting of production centers to regions with feedstock advantage (like the Middle East) or those with a prominent domestic demand base (such as mainland China).
Future growth in world HDPE consumption will be driven by the status and progress of regional economies, continued substitution of HDPE for traditional materials (e.g., glass, wood, concrete, paper), and avoidance of obsolescence of HDPE in some traditional applications. This latter factor will be more evident in the developed regions of the world where continued improvements in polyolefin processes and catalyst technologies should allow for the production of very broad ranges of products and grades that will increase HDPE’s utility in the marketplace. HDPE will also experience competition from traditional materials such as other existing thermoplastics as well as from emerging polymers brought into the marketplace via new technologies such as metallocene catalysts.
Blow molding and injection molding are the dominant end uses in Western Europe and North America. Consumption of HDPE in these end uses in Japan is considerably less. As a percentage of total HDPE consumption, film usage in Japan and Other Asia is nearly twice as large as the share of film in either the United States or Western Europe.
The company’s Eco-Mode saves wear and tear on the robot by ensuring it does not run faster than necessary — ultimately saving maintenance and energy costs. Offered standard on many Wittmann robots, Eco-Mode “requires no special programming or interface with the IMM or operator/programmer,” said Jason Long, National Sales Manager for robots and automation for Wittmann USA. “All the end user has to do is tell the robot how many seconds it should get back over the IMM before the mold opens.”
The Industry 4.0 era of manufacturing depends so heavily on data-driven precision that artificial intelligence (AI) is playing an increasing role in harnessing that data to enhance the performance of machines — including injection molders.
S&P Global’s Chemical Economics Handbook – Polyethylene Resins, High-Density (HDPE) has been compiled using primary interviews with key suppliers and organizations, and leading representatives from the industry in combination with S&P Global’s unparalleled access to upstream and downstream market intelligence and expert insights into industry dynamics, trade, and economics.
Wittmann Battenfeld, which has fully embraced Industry 4.0 connectivity across its portfolio of injection molding and auxiliary machines over the past several years, employs AI with its robots to monitor cycle times and control robots’ speeds outside the molding machine.
“AI is becoming increasingly important in mechanical engineering, not least because of the need to automate injection molding processes efficiently and flexibly despite ever smaller batch sizes and shorter product life cycles,” said Werner Faulhaber, Director of Research and Development at Arburg. “Application examples of AI include automatic programming of robotic systems, targeted malfunction remedying, and a spare parts system with ‘intelligent’ image processing. Arburg is working on making injection molding more intelligent, step by step — ensuring that the machine continuously learns, keeps itself stable, and can even optimize itself in the future.”
The company’s machine-learning capabilities — HiQ Flow and CMS technology — will be on display at this year’s K show on Oct. 19 to 26 in Düsseldorf, Germany. The speed of ROI can be as short as a few cycles with HiQ Flow, and the software can often be retrofitted to older injection molding machines equipped with a B8 machine control. A CMS Pro version will be available at a later date.
Based on factors like changes in material, ambient temperature, machine wear, tool wear, and other influences, “AI can determine which machine parameters need to be changed so that the product can be produced within its quality tolerances. This can take months, as errors first must occur in order to learn from them.”
In 2021–2022, the COVID-19 pandemic disrupted demand for HDPE around the world apart from in mainland China, which reported a positive growth rate.
Film and sheet applications lead the demand for HDPE globally, followed by blow molding applications. Blow molding, injection molding and film and sheet together account for more than two-thirds of the world market for HDPE, most of which is for packaging (excluding blow-molded fuel tanks).
GETTING A QUOTE WITH LK-MOULD IS FREE AND SIMPLE.
FIND MORE OF OUR SERVICES:
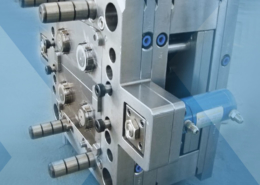
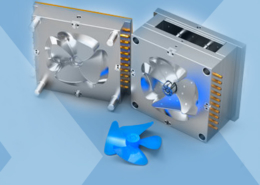
Plastic Molding

Rapid Prototyping
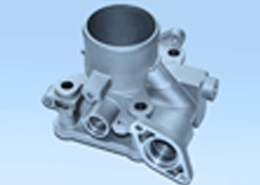
Pressure Die Casting
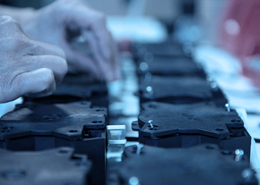
Parts Assembly
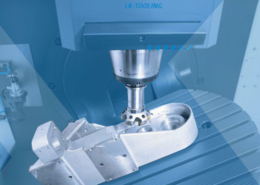