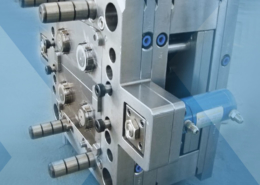
Injection Molding Using A 3D Printer - plastic injection molding part
Author:gly Date: 2024-09-30
MD: Tell me about the resin materials used in two-shot injection molding, and how does the selection of materials impact the overall product design?
Here are capsule summaries of some of the key sessions and speakers at the medical plastics conference track, which takes place on Oct. 16 in room 102F.
Durable medical devices typically are expected to function for up to 10 years or more under a combination of mechanical and/or thermal loads. Designing and analyzing medical devices that incorporate polymeric components, therefore, requires a thorough understanding of the material properties that influence creep and fatigue performance, as well as test and analysis methods for evaluating device performance. In this session, Paul Briant, practice director and principal engineer at Exponent, will review polymer properties that affect creep and fatigue, test methods for evaluating long-term creep and fatigue, and simulation methods of polymer performance under thermal and mechanical loads.
Material science experts will discuss current and emerging applications for medical plastics during a daylong conference track.
To reduce friction in products made from thermoplastic elastomers (TPEs), lubricious coatings can be applied to the devices or the TPEs can be compounded with specialty additives. Shruba Manna , senior development engineer at compounder Foster Corp., will explain the low-friction technolgies available on the market along with the effect of additives on a polymer’s properties and processability.
Plastec Minneapolis is part of the Advanced Manufacturing Minneapolis event, along with co-locates MD&M, ATX, MinnPack, and D&M, at the Minneapolis Convention Center on Oct. 16 and 17, 2024. The event is organized by Informa Markets – Engineering, which also produces PlasticsToday.
JH: With so many variables in design and materials it is very important if you are thinking about designing a part that could potentially be molded as a two-shot part to have your molder in design discussions from the very beginning.
JH: Instead of paying for two separate injection molding processes run sequentially, you pay for two injection molding processes run in parallel. Each time the mold cycles you get a complete part, cutting the manufacturing process time nearly in half saving man and machine hours.
The decision to invest in a 220-ton Nissei two-shot press was a strategic move made by C&J Industries, Meadville, Pa., to expand its capabilities. The selection of this press was a deliberate internal project aimed at gaining experience in this specialized process. By matching the press with its two-shot coaster, the company addressed the growing demand for products that require two-shot capabilities.
JH: It has eliminated secondary assembly and bonding of the parts together, saving costs and improving the overall part quality. It has helped with part consolidation resulting in reduced cost and lead time to market.
Wei Shen, associate professor in the Department of Biomedical Engineering at the University of Minnesota, will present a class of thermoplastic elastomers that exhibit elastomeric properties in both wet and dry environments. The elastomers can be processed via 3D printing, extrusion, and hot-press processing at 60°C. The collective elastomeric, biodegradable, biocompatible, and thermoplastic properties make these materials highly valuable for biomedical applications.
MD: Does the two-shot process enhance the quality and durability of the final product compared to other molding techniques? If so, how?
Going forward we will buy a unit(s) that fits the application we are awarded. There are various options depending on the program whether we buy another two-shot press or buy a side unit that can be used on our existing presses to do two-shot molding. Two-shot molding is very dependent on the part size and shot size required for each material and matching the part to the press size required.
MD: Does the tooling and equipment setup differ for two-shot injection molding compared to conventional molding processes? Please explain.
MD: In what ways does the two-shot injection molding process contribute to cost-efficiency and sustainability in manufacturing?
The compatibility of the two resins had some challenges due to their similar melting temperatures. They bonded well with each other, but the second resin could melt and blend into the first resin, leaving a marbled look which we did not want. Working with the resin manufacturer’s and adjusting the molding process we were able to overcome that. Another issue to keep in mind when matching a part to a two-shot press is considering barrel sizes. The amount of each resin must match the barrel size for each injection unit. This makes it hard to match multiple parts to the same press. This is a reason using a side unit with an existing press is sometimes more economical and gives you more options when trying to utilize your press capacity.
JH: Our press uses parallel injection units and a rotary machine platen. Our design had to consider the part staying on the core and rotating 180 deg. over to the other side. The product design needed to allow gate locations that are on top of each other. The shut-off surfaces between the first-shot part and the second cavity had to be considered. The second cavity must squeeze an area of the first part with enough pressure to prevent the second shot resin from leaking out creating flash. That contact area can leave a visible mark on the part that needed to be considered.
The recently qualified medical device development tool (MDDT) provides an accelerated test methodology to address the performance of new materials at long human implant times. Not only does careful use of accelerated testing reduce dependency on preclinical models, the MDDT increases certainty in predictions of a new material’s bio-durability. Kimberly Chaffin, vice president corporate technologist at Medtronic, will review predictive accelerated testing conducted for a series of commonly implanted medical device polymers, where the accelerated predictions are validated with up to 20 years of real-time human implant data.
MD: What challenges or limitations did you encounter when implementing a two-shot molding approach? How were these overcome?
JH: The tooling and equipment can be much more complex, so the setup takes longer. You are dealing with basically two molds with one side attached to a rotary platen. A robot will come in and pick and place the first shot into the second side. Does the mold have an internal core pull, a shuttle action or maybe a lift and rotate mechanism built in? Do you need air, hydraulics or servos tied into the press controls? The presses have the software built in to integrate the injection units together, so the actual injection set up is the same as a single component mold but with separate screens for each injection unit.
In micromolding, plastics can reach a point where shear thinning behavior is stretched to its limits. In this talk, Patrick Haney, R&D engineer at MTD Micro Molding, will explore the typical flow behavior of plastics and discuss the intriguing phenomena that arise under extreme shear conditions. He will touch on the ramifications of these changes on the final micromolded product, including the effects on final part microstructure as it applies to device application.
MD: Can you explain the key considerations to keep in mind when designing parts for a two-shot injection molding process?
Spielman has more than three decades of experience as a writer and editor for a range of B2B brands, including those that cover machine design; electrical design and manufacturing; interconnection technology; food and beverage manufacturing; process heating and cooling; finishing; and package converting.
Plastics have been instrumental in advancing medical technology for many decades, but, to my mind, a seminal moment happened during WW II, when plastic replaced glass in IV bags on the battlefield and proved its superiority, particularly when it comes to breakage. Since then, polymers have been on a roll in medical technology. From single-use devices that prevent patient infections to resorbable implants that eliminate having to undergo a second surgical procedure to remove the devices, plastics have revolutionized healthcare practices, improving patient outcomes and quality of life.
Secondary assembly operations or separate over-molding or insert molding of the first part can be eliminated. It also reduces handling of parts like you would have with over molding, which increases WIP and potential of part damage or contamination that you avoid with two-shot molding.
JH: The primary advantage is cost savings from producing a completed two-shot or two-component product every machine cycle. You can usually get better quality with better adhesion between the two resins and better matching of the second core or cavity to the first part since it stays in the mold, so the aesthetics are improved. More than one color is possible.
As Machine Design’s technical editor, Sharon Spielman produces content for the brand’s focus audience—design and multidisciplinary engineers. Her beat includes 3D printing/CAD; mechanical and motion systems, with an emphasis on pneumatics and linear motion; automation; robotics; and CNC machining.
Machine Design reached out to John Hanninen, senior engineer of new business development at C&J Industries, to learn about the process, its advantages and its challenges.
JH: The upfront tooling costs for two-shot molding can be significantly more than conventional molding, so an analysis of the return on investment (ROI) would be important. Does the product require a second resin? The part design must fit within one of the several methods used for two-shot molding, so before a design is started you need to know the difference between them. Are the resins compatible? Do you need them to bond together or are you creating an assembly? Depending on the resins you select, some resins chemically bond well together while other resins may require that mechanical bonds are designed in to better hold the two different resins together.
Industry experts from the Society of Plastics Engineers (SPE) Medical Plastics Division will discuss growth drivers and trends in medical polymers, including new resins, advanced molding methods, sustainability, personalized medicine, and regulatory shifts. Rob Klein, senior principal materials engineer at Atricure, and Chris Lyons, managing scientist at Exponent, are scheduled to speak. They will be immediately followed by Arthur Erdman, founding director of the Bakken Medical Devices Center, at 9:30 a.m. Named for Earl Bakken, the founder of Medtronic, the center follows his lead in exploring new avenues for medtech innovation through material development and 3D printing. Erdman will discuss several case studies illustrating the role polymers play in advancing medical technology.
JH: While the final quality of a two-shot part compared to an over-molded part can be similar, the benefit comes from scrap rates and machine capacity. You may run through more parts in the over-molding process to get the same amount of quality parts that you would get with two-shot molding.
John Hanninen: Over the years we have had many instances of having to turn jobs away that required two-shot capabilities. To gain experience, management decided to pursue an internal project and after searching around, it was decided a good used press would be purchased. The Nissei was selected to match up with our two-shot coaster.
JH: The initial resin or first shot is usually a rigid material such as ABS, polypropylene, nylon, etc. The second resin is usually soft resin like a thermoplastic elastomer or silicone-type material. Common items like hand tools with soft grips and even toothbrushes all take advantage of the two-shot process. It can also combine two rigid resins allowing multiple-colored parts like a headlight or taillight with opaque, clear and amber or red variations all in one component.
MD: Can you provide examples of real-world applications or case studies where this process resulted in significant improvements or innovations for your customer(s)?
Machine Design: I understand that two-shot molding is something C&J Industries has recently taken on. Can you tell me about that decision, including how the company went about selecting its 220-ton Nissei two-shot press?
Editor in chief of PlasticsToday since 2015, Norbert Sparrow has more than 30 years of editorial experience in business-to-business media. He studied journalism at the Centre Universitaire d'Etudes du Journalisme in Strasbourg, France, where he earned a master's degree.
A daylong conference track at Plastec Minneapolis is devoted to current and emerging medical plastics technology, bringing together experts from industry and academe to share insights on everything from micromolding to biostability in implants.
Various resin manufacturers have developed materials specifically for two-shot molding to achieve an adhesive or chemical bond between the rigid and soft resins. Working with them would be an important step for a successful design. If two resin are needed that are not meant to chemically bond to each other, then you must design in a mechanical bond feature to be able to mold a successful part.
GETTING A QUOTE WITH LK-MOULD IS FREE AND SIMPLE.
FIND MORE OF OUR SERVICES:
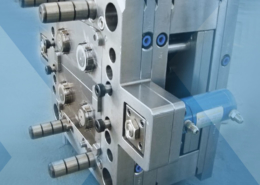
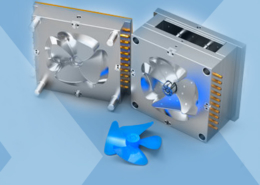
Plastic Molding

Rapid Prototyping
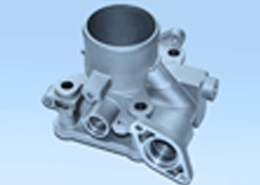
Pressure Die Casting
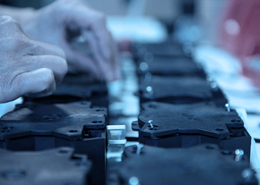
Parts Assembly
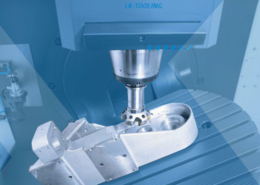