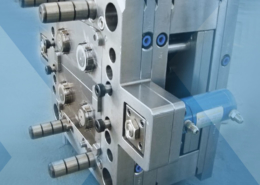
Injection Molding of Thin-Walled rPET Cups Is Now Possible - polypropylene moldi
Author:gly Date: 2024-09-30
The plastic injection molding machines market is experiencing robust growth, driven by the automotive industry's increasing demand for lightweight, high-precision plastic components. Technological advancements, such as electric and hybrid machines, enhance efficiency and sustainability.
Asia-Pacific's Industrial Growth Fuels Dominance in Plastic Injection Molding Machines Market, Contribute Over 43% Revenue
Unstoppable Rise of Hydraulic Plastic Injection Molding Machines Despite High Popularity of Electric Machine, Contribute over 55% Revenue
The growth of horizontal plastic injection molding machines is primarily driven by the increasing demand from key end-use industries such as automotive and packaging. Injection molding has been a well-established manufacturing process for producing plastic, metal, and rubber products across various sectors for many years. This growth is a testament to the dominance of horizontal machines in the plastic injection molding market. As per Astute Analytica, technological advancements have played a crucial role in the growth of horizontal plastic injection molding machines market. Modern machines offer superior precision, speed, and process control compared to older models. Essential elements of molding that were once driven by time and pressure have now evolved to focus on position, peak pressure, and process repeatability. Today, injection molding is considered a highly automated and mature technology, enabling manufacturers to produce ultra-high-quality plastic parts with the highest level of precision and speed.
One of the key advantages of horizontal plastic injection molding machines is their ability to efficiently produce high volumes of parts, making the process highly cost-effective for mass production. Injection molding machines can meet high-volume production requirements once the process is set up, and the high production output rate makes injection molding more cost-effective and efficient compared to other manufacturing methods. Presses can run in size from less than 5 tons to over 4000 tons of clamping pressure, with larger machines capable of producing bigger parts. Larger parts require higher clamping force to keep the mold closed during injection, highlighting the importance of horizontal machines in the production of sizable plastic components.
The main Sumitomo (SHI) Demag stand (Hall B1, Stand 1105) features a fully electric IntElect 180/570-250 injection moulding machine equipped with an LSR package comprising a twin dosing system, robotics, and vacuum and venting peripheral equipment. In a cycle time of just 17 seconds, this IntElect LSR package manufactures 256 individual 0.06-gram single wire seals with absolute precision and stability. Despite this high throughput, the IntElect machine’s energy consumption remains one of the lowest on the market.
To support the high-volume production of individual single wire seals, tooling partner Rico Group reveals its proprietary 256-cavitation LSR mould tool. Combining the direct injection system with double nozzle technology with the IntElect machines optimised clamp force, this LSR package successfully achieves the highest number of cavities in the most compact installation space. The turnkey system coordinates every processing step to efficiently manufacture 256 LSR parts every 15 seconds with minimal flash and material waste. “It’s the definition of high-volume sustainable production,” notes Aliyev.
Contact Us: Astute Analytica Phone: +1-888 429 6757 (US Toll Free); +91-0120- 4483891 (Rest of the World) For Sales Enquiries: sales@astuteanalytica.com Website: https://www.astuteanalytica.com/ LinkedIn | Twitter | YouTube
High initial investments required for the development and installation of plastic injection molding machines can be a significant barrier to plastic injection molding machines market growth. The reliability of some machines can be a challenge, particularly in regions with inconsistent weather patterns. Uncertainty surrounding government policies and regulations can create market instability and slow down growth. The study also suggests that the market is fragmented, with the top players accounting for a marginal share, indicating a competitive environment with room for new entrants and innovation. The demand for machines that offer flexibility and quick changeover capabilities is driven by the growing trend of customization and the need to handle varying production requirements. The trend of reshoring and nearshoring manufacturing operations closer to consumer markets is stimulating demand for injection molding machines in regions experiencing an increase in these activities.
Astute Analytica is a global analytics and advisory company which has built a solid reputation in a short period, thanks to the tangible outcomes we have delivered to our clients. We pride ourselves in generating unparalleled, in depth and uncannily accurate estimates and projections for our very demanding clients spread across different verticals. We have a long list of satisfied and repeat clients from a wide spectrum including technology, healthcare, chemicals, semiconductors, FMCG, and many more. These happy customers come to us from all across the Globe. They are able to make well calibrated decisions and leverage highly lucrative opportunities while surmounting the fierce challenges all because we analyze for them the complex business environment, segment wise existing and emerging possibilities, technology formations, growth estimates, and even the strategic choices available. In short, a complete package. All this is possible because we have a highly qualified, competent, and experienced team of professionals comprising of business analysts, economists, consultants, and technology experts. In our list of priorities, you-our patron-come at the top. You can be sure of best cost-effective, value-added package from us, should you decide to engage with us.
The Asia Pacific region dominates the market, holding 43% of the revenue in 2023, driven by investments in public infrastructure and residential construction. China and India are key contributors, with China accounting for 26.7% of the world's plastic injection molding production in 2023. The automotive segment is a significant driver for the market, with vehicle sales reaching 15,608,386 units in 2023 in the U.S. alone. The healthcare industry's demand for plastic injection molding continues to grow, with applications in drug-delivery systems and blood-glucose test strips. The packaging industry, especially for food & beverage and cosmetic applications, is a major end-use industry, driven by the demand for sustainable, durable, and innovative packaging.
At Fakuma 2023, visitors will get the opportunity to see Sumitomo (SH) Demag’s LSR processing competence in two live demonstrations.
The shift towards more energy-efficient machines, particularly electric machines, is another significant growth driver in the plastic injection molding machines market. Using electric injection molding machines makes the process relatively energy-efficient. The most eco-friendly injection molding companies employ state-of-the-art machinery to assist them in minimizing waste, transportation, and packaging, further emphasizing the importance of energy efficiency in the industry.
On their main stand, the company highlights its multi-cavity LSR processing competence, including OPC-UA interface compatibility, on an all-electric IntElect 180/570-250 injection moulding machine. Visitors to the Reinhardt-Technik booth (Hall A3, Stand 3313) will have the opportunity to view another market where LSR processing is prevalent, the healthcare sector.
“The market for liquid silicone is growing dynamically, both in terms of applications demanding skills in LSR, as well as volume," observes Rustam Aliyev, the company’s LSR expert and business development director of automotive & electronics.
Ensuring the material is exposed to a consistent temperature in all 256 cavities, the Rico tool is designed to run on a cold clamping force. This helps to avoid premature curing of the material before every cavity is filled. As a result, it reduces the risk of component and tooling damage, and consequently expensive machine downtime and costly tool repairs.
Modular by-design, the LSR eTwin Connect allows for quick configuration of programs and instant software upgrades. To support quick drum changes and for ease of maintenance, the system also features a roll in device and automatic drum locks.
The aerospace, food and beverage, construction, and consumer goods industries also contribute to this dominance. The aerospace market is projected to reach $150 billion in 2023, while the food and beverage market is expected to hit $3 trillion. The construction market is projected to reach $5 trillion, and the consumer goods market is anticipated to reach $4 trillion. These sectors' reliance on plastic components for various applications further cements Asia-Pacific’s leading position in the plastic injection molding machines market.
Buy Now Full Report: https://www.astuteanalytica.com/industry-report/plastic-injection-molding-machines-market?buy_now=true&license_type=single
Supporting full connectivity, the OPC UA interface facilitates seamless communication between the IntElect machine control and the eTwin Connect dosing system. During every injection cycle, the intuitive, user-friendly multi-touch 15.6 inch HMI capturing all processing documentation, including material pressure, colouring and additive settings, to ensure high-level transparency and traceability.
The automotive industry continues to dominate the market, driving significant growth and technological advancements. In 2023, the global injection molded plastic market size was estimated at US$ 7.63 billion with expectations to grow at a CAGR of 5.63% from 2024 to 2032. This expansion is largely fueled by the automotive sector's demand for lightweight, high-precision plastic components. In 2023, more than 92 million vehicles were sold around the world, which shows the significant of the automotive industry to the market growth due to the material compatibility, high precision, repeatability, and superior surface finish required for automotive components.
The packaging industry also significantly supports hydraulic IMMs. In the United States, flexible packaging holds around 20% of the market share, necessitating efficient injection molding machines. Technological advancements have enhanced the capabilities of hydraulic IMMs. Hybrid machines, which combine the high clamping force of hydraulic machines with the precision and energy efficiency of electric machines, have propelled the market. Apart from this, cost efficiency and durability make hydraulic IMMs a preferred choice. These machines are priced lower than electric equipment, providing a cost-effective option for manufacturers. Their durability and efficiency make them suitable for large volume and complex component production.
Hydraulic plastic injection molding machines (IMMs) dominate the market due to several compelling factors supported by automotive industry's reliance on plastic components. In 2023, the world witnessed a sale over 92 million vehicles. As a result, the automotive sector, being one of the largest consumers of plastic injection molded parts, significantly contributes to the demand for hydraulic plastic injection molding machines market. The price-conscious nature of the population and the high mileage demand compel auto manufacturers to use plastic parts, driving this demand.
Precision and Performance Demand of Automotive Industry Leaves Positive Impact on the Plastic Injection Molding Machines Market, Contribute Over 28% Revenue
The automotive industry's shift towards lightweight, high-precision plastic components, coupled with increased production capacities and sustainability efforts, underscores its dominance in the market. This sector's influence is expected to drive continued growth and innovation in the coming years.
New Delhi, May 29, 2024 (GLOBE NEWSWIRE) -- The global plastic injection molding machines market is projected to hit the market valuation of US$ 12.28 billion by 2032 from US$ 7.63 billion in 2023 at a CAGR of 5.63% during the forecast period 2024–2032.
Visitors to the Reinhardt-Technik booth (Hall A3, Stand 3313) will have the opportunity to view the healthcare sector where LSR processing is prevalent. Manufacturing surgical dental protection covers demands a combination of the thinnest walls and thicker beaded geometries. To accomplish this level of 3-dimensional LSR moulding precision, specialists in healthcare applications EMDE MouldTec supplies the gated 4-cavity mould tool, which fits into the generous tool space of the IntElect 75/420-65.
The Asia-Pacific region's dominance in the market is intricately linked to its robust growth across various industries, including automotive, electronics, healthcare, packaging, aerospace, food and beverage, construction, and consumer goods. This multifaceted industrial expansion fuels the demand for plastic injection molding machines, making Asia-Pacific a key player in this market. In the automotive industry, Asia-Pacific is expected to grow at a CAGR of 6.5% from 2023 to 2032, with China's automotive sales projected to reach 30% of all automotive sold in the world by 2032. India's automotive industry is set to grow by 10% in the years to come, and EV sales in the region are expected to account for 20% of total automotive sales. This surge in automotive production necessitates extensive use of plastic components, driving the demand for injection molding machines.
The study shows that China is leading consumers when it comes to automotive industry as the country sold over 30.09 million automotives. Out of which, more than 8.1 million were electric vehicles. Apart from this, US automotive is the one of the leading importers of Chinese machines, importing around 15,000-20,000 units annually, with substantial demand from automotive manufacturers in the plastic injection molding machines market. Wherein, electric and hybrid machines are gaining traction in automotive industry, with Arburg introducing the 110-ton Allrounder 470 H hybrid injection molding machine in 2023. The polypropylene segment, holding over 20% of the market in 2023, sees increased consumption in automotive components. Haitian International's new manufacturing facility in Mexico exemplifies efforts to enhance production and expedite deliveries.
Manufacturing four burr-free dental components every 25 seconds, a Sumitomo (SHI) Demag SAM-C5 robot performs the demoulding task. A special end of arm tool uses compressed air to delicately extract and place the dental covers into containers, ensuring hygiene standards are never compromised.
Request a Customized Copy: https://www.astuteanalytica.com/ask-for-customization/plastic-injection-molding-machines-market
The electronics and telecommunication sector in Asia-Pacific is also a major contributor to the regional plastic injection molding machines market. The consumer electronics market is expected to reach $450 billion by 2024, with 5G adoption projected to cover 60% of the population. Increased production of smartphones, laptops, and wearable devices, coupled with a 15% growth in China's semiconductor market, underscores the need for plastic components, further boosting the injection molding machines market. Apart from this, healthcare advancements in the region, with a projected market size of $2.5 trillion in 2023, and a telehealth market expected to grow to $50 billion, highlight the increasing demand for medical devices and biotechnology products. These products often require precision plastic components, thereby driving the market for injection molding machines.
The adoption of injection molded components is increasing across various industries, including automotive, electronics, consumer products, and packaging, due to their material compatibility, high precision, and repeatability. Technological advancements are driving the efficiency and effectiveness of plastic injection molding machines, with continuous innovations in materials, manufacturing processes, and digital technologies. The demand for lightweight and intricately designed plastic components in industries such as automotive and electronics is also fueling market growth. As per Astute Analytica, electric plastic injection molding machines are gaining popularity due to their energy efficiency, using 50% to 75% less energy than hydraulic machines. The market is shifting towards all-electric machines, which save up to 70% of energy compared to hydraulic machines and provide better acceleration performance and repeatability. However, the global plastic injection molding machines market is dominated by hydraulic machines as of 2032.
“Integrating a high precision dosing system with the IntElect machine and the optimal heat balance attained by the Rico dual tip nozzle delivery system ensures unprecedented distribution of the 15 gram shot weight. The result of the high machine dynamics means that part weight accuracy of 0.059 grams is repeatably replicated in the fastest possible cycle time,” explains Aliyev.
Given that each dental article weighs just 0.425 grams, and with an LSR shot weight of just 1.7 grams, the exhibit features Sumitomo (SHI) Demag’s smallest IntElect injection unit. An LSR eTwin Connect from Reinhardt-Technik delivers material to the needle gate nozzle tool. Material is then injected into each of the four cavities twice. Metering data directly connects to the IntElect processing data via OPC-UA, ensuring a fully traceable and stable production process.
LSR tooling specialist RICO supplies the 256-cavity open tool system. The Elastosil LR 3844/50 material from Wacker Chemie is dispensed via a sophisticated yet compact Industry 4.0-ready LSR eTwin Connect dosing system engineered by another LSR expert - Reinhardt-Technik. This metering and static mixing system guarantees the perfect mixing ratio of two additives, ensuring 99.75% of the LSR material is processed.
LSR is regarded as a unique material, in that it remains flexible and elastic down to -50°C, yet also retains its properties up to 200°C. As a result, LSR is used extensively in electronic components, cables etc. where insulation is required, as well as in medical and healthcare products and the consumer goods sector. To support these markets, in the last five years Sumitomo (SHI) Demag has made significant investments developing an all-electric LSR package that inevitably delivers the cleanliness and precise shot control required to handle this low viscosity material. This year’s Fakuma exhibits demonstrate the company’s advanced proficiency in moulding high-specification LSR components, exclaims Aliyev.
The eTwin servo-driven piston pumps save processors up to 80% energy compared to air-driven pumps. While the integrated cooling system and pulsation-free volume flow helps to optimise the filling behaviour and prevent the LSR material from curing too soon. The unit also performs automatic venting, purging air from the material before it is fed into the moulding machine and tool. Combined with the IntElect’s high injection dynamics, the repeatable process ensures the highest component quality is achieved time and time again.
In terms of plastic injection molding machines market leadership, the United States stands out as one of the leaders, with approximately 20,000 plastics processors employing around 1.5 million workers. This dominance is further evidenced by the hybrid injection molding machine's status as the second fastest-growing machine in the market, highlighting the integration of hydraulic systems with advanced technologies. These factors collectively underscore the dominance of hydraulic IMMs in the plastic injection molding market.
GETTING A QUOTE WITH LK-MOULD IS FREE AND SIMPLE.
FIND MORE OF OUR SERVICES:
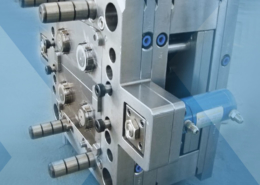
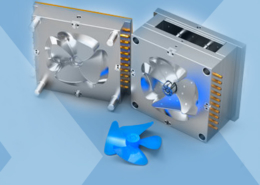
Plastic Molding

Rapid Prototyping
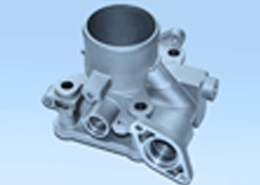
Pressure Die Casting
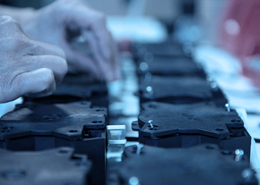
Parts Assembly
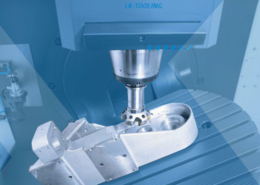