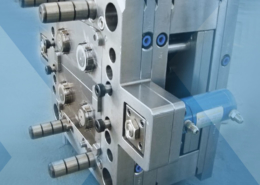
Unlocking Efficiency and Precision: Exploring the Depths of Scientific Molding
Author:gly Date: 2024-06-08
Introduction:
Scientific molding stands at the forefront of modern manufacturing, revolutionizing the production process by integrating cutting-edge technology with meticulous precision. This methodological approach transcends traditional molding practices, harnessing the power of data-driven analysis and systematic optimization to achieve unparalleled levels of efficiency and quality. In this article, we delve into the intricacies of scientific molding, unraveling its key principles, applications, benefits, and future prospects, aiming to enlighten readers on its significance in the realm of contemporary manufacturing.
Key Aspects of Scientific Molding:
1. Process Optimization
Scientific molding embodies a holistic approach to process optimization, where every parameter, from material selection to cooling rates, is meticulously scrutinized and fine-tuned to achieve optimal results. At the core of this optimization lies the utilization of advanced simulation software, such as Moldflow and Sigmasoft, which enable engineers to simulate the entire molding process virtually. By analyzing various factors like flow patterns, temperature distribution, and warpage tendencies, manufacturers can identify potential defects and inefficiencies before they manifest physically.
Furthermore, scientific molding emphasizes the significance of data-driven decision-making. Through the integration of sensors and monitoring systems within molding machines, real-time data on temperature, pressure, and cycle times are continuously collected and analyzed. This wealth of information empowers engineers to make informed adjustments on the fly, ensuring consistent quality and minimizing production variability.
2. Material Science Integration
A fundamental pillar of scientific molding lies in its integration with material science. Beyond traditional thermoplastics, this methodology extends its reach to encompass a diverse array of advanced materials, including thermosets, elastomers, and biodegradables. Each material presents its own set of challenges and opportunities, demanding a nuanced understanding of its rheological behavior, thermal properties, and shrinkage characteristics.
Through collaborative efforts between molders and material suppliers, scientific molding fosters innovation in material development, pushing the boundaries of what is achievable in terms of performance and sustainability. By aligning material selection with specific application requirements and processing conditions, manufacturers can unlock new possibilities for product design and functionality.
3. Tooling Design Excellence
Central to the success of scientific molding is the pursuit of tooling design excellence. Unlike conventional methods, which often rely on trial and error, scientific molding embraces a systematic approach to mold design, guided by empirical data and computational analysis. Advanced CAD/CAM software facilitates the creation of intricate mold geometries, optimized for uniform filling, minimal warpage, and maximum part quality.
Moreover, scientific molding emphasizes the importance of mold maintenance and refurbishment. By implementing proactive maintenance schedules and leveraging predictive analytics, manufacturers can prolong the lifespan of molds, minimize downtime, and mitigate the risk of costly repairs. This proactive approach not only ensures consistent production quality but also enhances the overall efficiency and profitability of molding operations.
4. Continuous Improvement Culture
At its essence, scientific molding fosters a culture of continuous improvement, where innovation and refinement are embraced as integral components of the manufacturing process. Through systematic root cause analysis and performance monitoring, manufacturers can identify areas for enhancement and implement targeted interventions to drive incremental gains in productivity and quality.
Furthermore, scientific molding encourages cross-functional collaboration and knowledge sharing within organizations. By fostering open communication channels between design, engineering, and production teams, manufacturers can harness collective expertise and insights to overcome challenges and seize opportunities for optimization.
Conclusion:
In conclusion, scientific molding represents a paradigm shift in the field of injection molding, offering a systematic approach to achieving unprecedented levels of efficiency, precision, and quality. By leveraging advanced technologies, integrating material science principles, optimizing tooling design, and fostering a culture of continuous improvement, manufacturers can unlock new realms of possibility in product development and production. As we navigate the ever-evolving landscape of manufacturing, embracing the principles of scientific molding will undoubtedly be key to staying ahead of the curve and realizing the full potential of modern manufacturing capabilities.
GETTING A QUOTE WITH LK-MOULD IS FREE AND SIMPLE.
FIND MORE OF OUR SERVICES:
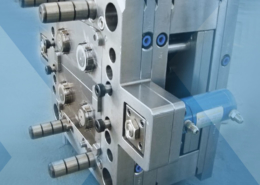
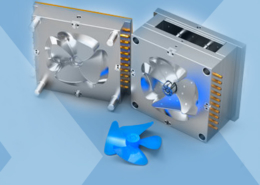
Plastic Molding

Rapid Prototyping
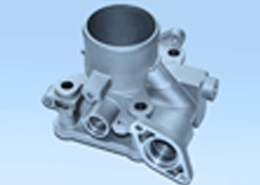
Pressure Die Casting
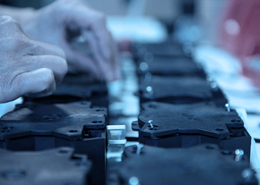
Parts Assembly
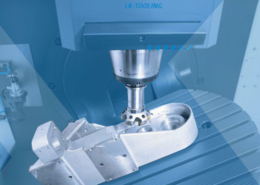