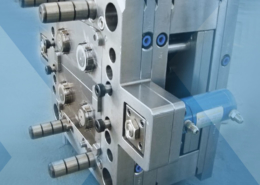
Scientific Injection Molding: Revolutionizing Plastic Manufacturing
Author:gly Date: 2024-06-08
In today's rapidly evolving industrial landscape, precision, efficiency, and quality are paramount in plastic manufacturing. Scientific Injection Molding (SIM) emerges as a groundbreaking approach that integrates the principles of polymer science, engineering, and data analytics to optimize the injection molding process. This article delves into the intricacies of SIM, elucidating its principles, applications, benefits, and future prospects.
Understanding Scientific Injection Molding
Scientific Injection Molding, also known as Design of Experiments (DOE) for Injection Molding, represents a departure from traditional molding methods by employing a systematic, data-driven approach. At its core, SIM utilizes statistical techniques to analyze and control various parameters of the injection molding process, such as temperature, pressure, and cooling rate. By comprehensively understanding the interactions between these variables and their impact on the final product, manufacturers can optimize production processes, enhance product quality, and reduce costs.
Key Components of SIM
The implementation of SIM entails several key components:
Material Characterization
: Thorough characterization of the polymer material properties is fundamental to SIM. This includes analyzing viscosity, thermal behavior, and shrinkage, among other factors, to ascertain the material's behavior during the molding process.
Process Optimization
: SIM emphasizes the optimization of process parameters through rigorous experimentation and analysis. Design of Experiments (DOE) techniques enables manufacturers to identify the optimal settings for variables such as temperature, pressure, injection speed, and cooling time.
Mold Design and Simulation
: Advanced mold design and simulation software facilitate the creation of molds tailored to specific geometries and materials. By simulating the molding process, manufacturers can anticipate potential issues and refine designs before production, thereby minimizing defects and optimizing cycle times.
Advantages of SIM
The adoption of Scientific Injection Molding offers several compelling advantages:
Enhanced Quality and Consistency
: By systematically controlling process parameters, SIM minimizes variability and ensures consistent part quality, reducing the incidence of defects and rework.
Cost Reduction
: Optimizing the injection molding process leads to increased efficiency, reduced material waste, and shorter cycle times, ultimately lowering production costs.
Shortened Time-to-Market
: Through iterative experimentation and simulation, SIM accelerates the product development cycle, allowing manufacturers to bring new products to market faster and gain a competitive edge.
Applications of Scientific Injection Molding
Scientific Injection Molding finds applications across various industries, including automotive, electronics, medical devices, and consumer goods. Some notable applications include:
Automotive Components
: SIM is utilized in the production of intricate automotive components such as interior trim, dashboards, and exterior body panels, where precision and durability are critical.
Medical Devices
: In the medical sector, where stringent quality standards and regulatory compliance are paramount, SIM ensures the production of precise, sterile components for devices such as syringes, IV catheters, and surgical instruments.
Electronics Enclosures
: SIM enables the fabrication of complex electronic enclosures with tight tolerances, shielding sensitive components from environmental factors while maintaining structural integrity.
Challenges and Future Directions
Despite its numerous benefits, the widespread adoption of Scientific Injection Molding is not without challenges. These include the initial investment in equipment and training, as well as the need for expertise in statistical analysis and process optimization. However, advancements in automation, artificial intelligence, and machine learning hold promise for overcoming these obstacles and further optimizing the injection molding process.
In the future, research efforts should focus on enhancing the integration of simulation technologies, improving material characterization techniques, and developing advanced control systems for real-time monitoring and adjustment of process parameters. By addressing these challenges and embracing innovation, the plastic manufacturing industry can unlock the full potential of Scientific Injection Molding and usher in a new era of efficiency, quality, and sustainability.
Conclusion
In conclusion, Scientific Injection Molding represents a paradigm shift in plastic manufacturing, offering a systematic, data-driven approach to process optimization and quality assurance. By leveraging the principles of polymer science and engineering, SIM enables manufacturers to achieve unprecedented levels of precision, consistency, and efficiency. As industries continue to evolve and demand for high-quality, cost-effective products grows, the adoption of Scientific Injection Molding is poised to accelerate, driving innovation and reshaping the future of manufacturing.
GETTING A QUOTE WITH LK-MOULD IS FREE AND SIMPLE.
FIND MORE OF OUR SERVICES:
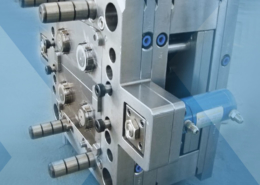
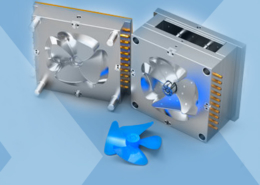
Plastic Molding

Rapid Prototyping
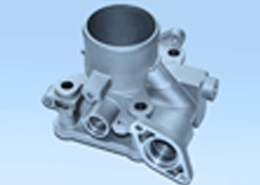
Pressure Die Casting
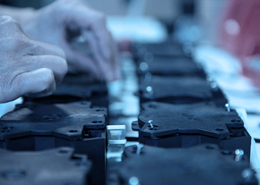
Parts Assembly
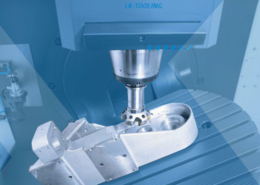