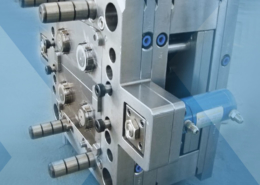
Injection Molding of Thin-Walled rPET Cups Is Now Possible - injection molding f
Author:gly Date: 2024-09-30
With the delivery of the e-mac 100, ENGEL is making a contribution to education and research in the field of plastics technology at Darmstadt University of Applied Sciences. Students benefit from modern technology and practical teaching methods that optimally prepare them for their future roles in the industry. At the same time, the machine opens up new possibilities in research to develop innovative solutions and applications.
As plastic injection molding methods continue to advance and evolve, allowing for enhanced flexibility and more sophisticated customization options, molding companies must be able to stay ahead of the curve in order to offer clients the latest technologies and highest-quality end products that suit their needs in the changing market. At The Rodon Group, we’ve always been dedicated to constant innovation and improvement, and we’re proud to announce a facility expansion and acquisition of a new, large size, 720-ton hybrid plastic injection molding machine for large parts. The expansion includes an additional 125,000 square feet of space at a secondary location in Hatfield, PA. The area will allow Rodon to grow with its diverse customer base and allow for improved process flow and future advancements of our injection molding capabilities. The new 720-ton injection molding machine enhances the capacities of our existing 118 molding presses to now offer a range of fractional to 107 ounces, and clamping force of 46 to 720 tons. With a much higher tonnage capability than those of our existing machines, the new press allows us to offer greater production flexibility for large part injection molding and improves our capabilities for customers that are looking to manufacturer these types of parts. Since 1956, our core competencies have centered on small (index card size or smaller), high volume custom plastic components. With these new capabilities and expansion, we look forward to continuing to serve our existing customers as well as new customers that are looking to source globally competitive, innovative manufacturing solutions for larger plastic parts. The Rodon Group is proud to be at the forefront of the many exciting advancements and trends in plastic injection molding, and our recent equipment acquisition and expansion are just two aspects of our commitment to continuous improvement. Contact us today if we can help answer any questions.
Technical details of the e-mac 100: The ENGEL e-mac 100 is a compact, all-electric injection moulding machine known for its precision and energy efficiency. With a clamping force of 1000 kN, it provides the necessary performance for a wide range of applications. The machine is equipped with the ENGEL CC300 control unit, which allows intuitive operation and precise control of the injection moulding process. Additionally, the iQ assistance systems - iQ weight control for continuous compensation of fluctuations in plastic viscosity, and iQ clamp control for automatic optimisation of the clamping force - are integrated. These systems enable real-time automatic adjustment of process parameters, resulting in consistent part quality, reduced scrap, and lower energy consumption. Furthermore, the machine features the iQ process observer, which monitors all four phases of the injection moulding process: plasticising, injecting, cooling, and demoulding. Finally, the ENGEL EDGE Device ensures secure connectivity for remote maintenance and other digital services from ENGEL.
Hatfield, PA – The Rodon Group has partnered with ICF Solutions, a division of Indian Creek Foundation on a facility-based work program. Since 1975, the Foundation’s mission is to “provide opportunities for people with intellectual and developmental disabilities; to live in and enrich the community throughout their lives.” The work program includes onsite training for various jobs that are subcontracted from local businesses, such as Rodon. Types of work include bulk mail processing, product assembly, packaging and sorting. More than 60 local businesses rely on ICF Solutions for these services. The Rodon Group has been working with ICF Solutions since 2012 and is currently utilizing their team to assemble multiple plastic parts for a variety of their customers. The trained workers average 300,000 units per month for Rodon. One or two staff members oversee the workers at each table and tables are set up by job skill, background and overall capabilities. ICF Solutions also partners with Thomas Jefferson University occupational therapists who intern to help the workers with various needs and independence goals. As of June, there were approximately 86 individuals involved in the program. According to Kevin McGrath, vice president of sales and marketing at Rodon “The collaboration with ICF has been invaluable. The assembly services they’ve provided have given us the ability to pursue additional opportunities and markets that we would not have been able to pursue otherwise. We are very thankful to have a local community resource like ICF. “ To learn more about Indian Creek Foundation and ICF Solutions, visit their website at www.indcreek.org/icf-solutions/ About The Rodon Group The Rodon Group is an ISO 9001:2008 certified landfill-free, plastic injection molder. In business since 1956, The Rodon Group makes billions of parts each year in its 125,000 square foot facility. With over 105 injection molding presses, Rodon is one of the largest family-owned and operated plastic injection molders in the United States and serves a diverse group of industries including consumer products, medical, construction, pharmaceutical and toys. Since 1992, Rodon has manufactured over 30 billion parts for the K'NEX building toy system, and is a subsidiary of K'NEX Brands, L.P.
In the Bachelor's programme in Plastics Technology, the new injection moulding machine will be used in practical training. Here, students will learn how to determine setting parameters, optimise the process for part quality, and use statistical experimental designs (DOE) to analyse the influencing factors on part characteristics. This practical application is crucial for translating theoretical knowledge into hands-on skills and preparing students for their future roles in the industry.
See how we've remained a manufacturing leader since 1956. This video highlights our factory, employees and our three primary capabilities as a high-volume, custom plastic injection molder: mold design, mold building, and parts manufacturing. In business since 1956, The Rodon Group makes billions of parts each year in our 125,000-square-foot facility. With over 117 injection molding presses, we are one of the largest family-owned and operated injection molders in the United States.
Fluid trap tip for superior collection and accurate results. An excellent choice for laboratories, hospitals, testing centers, medical schools and clinics.
This machine, equipped with ENGEL's digital assistance systems, the iQ products, will be used in both education and research. The e-mac 100 aims to provide students and researchers with new opportunities to practically experience and apply digitalisation and energy efficiency in the field of plastics technology.
ENGEL has delivered an all-electric injection moulding machine, the e-mac 100, to the Institute for Plastics Technology (ikd) at Darmstadt University of Applied Sciences.
The Rodon Group, one of the largest family-owned and operated plastic injection molders in the U.S., has added a Baxter robot to their factory floor in Hatfield, PA. See how employees work alongside Baxter, their robotic manufacturing assistant and co-worker.
Our line of universal plugs is designed to maximize manufacturing efficiency by speeding production and lowering inventory costs. Its unique annular fin design provides a positive fit for a wide range of tubing wall thicknesses with a single component. Within its 14-23 gauge range, the Universal Plug greatly reduces the number of plug I.D.'s needed in inventory. One plug per tube O.D. does the job, often with improved fit. Round, square or rectangular, Universal Plugs can make a substantial difference in efficiency and production costs.Standard plugs include a wide range of plastic plugs, flat head plugs, rectangular plugs, square plugs, forked plugs, ball plugs, specialty plugs, split stem & stem bumpers, beveled edge hole plugs and flat top hole plugs. In-house design services for specific custom plastic plugs are available. To see for yourself, contact us for samples today.
Specializing in high-volume, custom manufacturing solutions for a range of industries, The Rodon Group recently announced that their 720-ton hybrid plastic injection molding machine is now being used to manufacture a new, large-scale component for a customer in the food and beverage sector. Click the headline above to read the full article. https://thomasnet.com/insights/u-s-plastic-injection-molder-uses-720-ton-hybrid-machine-to-manufacture-new-large-scale-component
In 1956, The Rodon Group was founded with just four presses, 5,000 square feet of space, and a big vision. Today, as we celebrate our 65th anniversary, we do so as one of the largest family-owned and operated plastic injection molders in the country. With 128 presses, we serve clients in a wide range of industries with innovative manufacturing solutions, and we look forward to doing so for many years to come. The Rodon Group’s History The Rodon Group was founded by Irving Glickman in 1956 while he was still working with ELGO Rubber. This small, part-time company grew steadily with Glickman's strategic investments in equipment and other additions. He was passionate about cost-effective manufacturing materials and methods, and that thoughtful planning helped get the company off the ground and growing as ELGO Rubber eventually closed. Today, The Rodon Group is one of the largest family-owned and operated plastic injection molding companies in the United States, with 250,000 square feet of manufacturing space and a robot at every press. We're ISO 9001:2015 certified with a 99.92% quality parts rating, and we guarantee our molds for the life of your project. From design to toolmaking to materials selection, we're here to take your project from start to finish. What Sets Rodon Apart Our years of plastic injection molding experience is just the beginning. Irving Glickman's knowledge and foresight laid the foundation for success, which has been driven by the key values that were established in the earliest days and continue to serve as our guiding principles: We Treat Our Employees Well: Having third-generation employees on our team is no accident. We value our team members and know they're the backbone of the company. As a result, we have high employee retention and a team that's deeply invested in our clients and the work we do. We Offer Fair Prices for Our Customers: Part of our mission is to make sure you have the cost-effective solutions you need to run your business. We take pride in customizing a solution that helps you save time and money. We Re-Invest Our Profits in Talent and Equipment: Staying at the top of the industry means staying on top of the latest innovations and ensuring we attract the best professionals to work with us. Our company grows because we're willing to invest in our people, their education, and the equipment they use every day. We Focus on Being a Solution for the Customer--Never a Problem: We're your partner for your projects. We listen to your goals and develop a plan that suits you, managing any challenges as they arise to ensure the process is seamless for you. It's our job to make your business simpler, not more challenging. Over the decades, we've worked with a variety of industries and applications, including medical, food and beverage, window and door components, and construction with SillDry, a patented window protection line co-invented by our own Joel Glickman. As a proud U.S. manufacturer, we've always promoted domestic manufacturing, and we're active members of both American Made Matters and the Made in America Movement to help educate people about the benefits of buying American-made products. The future of U.S. manufacturing is bright, and we're excited to be a part of it. Our long history and extensive experience has prepared us for the next 65 years and beyond. Our turnkey manufacturing solutions are backed by our commitment to quality and excellent customer service, and we look forward to helping you with your high-volume production project as we celebrate our 65th anniversary. Contact us to learn more or request a quote for your project.
The Rodon Group is an ISO 9001:2015 certified landfill-free, high volume, plastic injection molder. In business since 1956, the Rodon Group makes billions of parts each year in its 125,000 square foot facility. We offer a turnkey and innovative manufacturing solution including mold design, mold building, and high-volume parts manufacturing. With over 125 plastic injection molding presses, Rodon is one of the largest family-owned and operated injection molders in the United States. The Rodon Group serves a diverse group of industries including food and beverage, window and door, medical and pharmaceutical, consumer products, construction and more. The Rodon Group has earned a reputation for being one of the best in the industry, offering high-quality, low-cost solutions. With our globally competitive pricing, we offer you the opportunity for leveraging the benefits associated with using a domestic manufacturer while avoiding the risks of offshore sourcing. Specializing in close-tolerance injection molding of small plastic parts, we provide a total concept solution from design and tooling to production, fulfillment, and packaging. The combined effort of our designers and toolmakers results in molds that ensure quality, precision tolerances, and optimized cycle times. We have the capacity to mold parts with complex geometries and variations in wall thickness. Our maximum part size is 10 inches square, although our major concentration revolves around parts with smaller dimensions. We have material specialists on staff to make recommendations from more than 100 commodity, engineering, and specialty plastics, including FDA, RoHS, REACH, and NSF certified resins and HACCP-compliant materials. Our 125 fully automated presses are the heart of our operation. Ranging in size from 46 to 720 tons, they feature capacities from fractional to 107 ounces. Hydraulic, hybrid, and all-electric technologies allow us to adapt production to the individual requirements of every application. Microprocessor-controls, self-diagnostics, and full-servo robotics allow us to operate 24 hours a day, 7 days a week for maximum efficiency. Using a combination of online vision inspection systems, SPC charting, as well as in-lab test, measurement, and inspection equipment, we ensure tolerances, color, physical appearance, and mechanical characteristics match your specifications. We offer custom packaging, 3D printed prototypes, safety stocking programs, just-in-time delivery, and a number of other additional support services.
An inefficient injection mold setup can result in increased machine downtime and ultimately have a negative impact on your profit margins. Click the headline above to read the full article. https://www.thomasnet.com/insights/improve-production-with-this-injection-mold-setup-checklist/
The Thomas Verified Supplier badge indicates that Thomas has confirmed the company operates in North America, provides accurate business information on the Thomasnet.com supplier discovery platform, has undergone a complete review and validation of all products and services currently offered, and are open to quoting new opportunities.
The Rodon Group is committed to environmental sustainability. The company's green initiatives make it a leader in the plastics industry. Its manufacturing process minimizes packaging, transportation costs, waste, water consumption and energy. Consider this example: in manufacturing just one of the more than 600 unique K'NEX parts, the Rodon Group recycles enough cardboard to save 300 cubic yards of landfill space, the equivalent of three football fields!
Our Standard Fasteners include a wide range of fasteners, two piece plastic fasteners, finned fasteners, removable fasteners, push fasteners, tufting button set, and two piece removable rivets. Custom designed plastic fasteners are available.
The new injection moulding machine from ENGEL will also offer numerous applications in research. Thanks to its comprehensive digital equipment, data on tool wear and predictive maintenance can be easily collected and analysed. This enables preventive measures and extends the lifespan of the tools, saving costs and increasing efficiency.
Rodon takes a solid relationship with toy giant K’NEX and applies its business model to other manufacturers—taking domestic manufacturing to the next level.
Our Additional Standard Products include caster sockets for beds, snap tie cones, plastic spacers, bushings , hose washers, O rings, eyeglass clips and inserts, dowel pins and hose grips.
“[Our patients were] swabbed twice, first with the one Fox Chase had been using and then with the new test swab,” said Dr. Eric M. Horwitz, Chair of Radiation Oncology at Fox Chase. “It turned out that the one [The Rodon Group] designed actually worked even better than the one we had.” Click the headline above to read the full article. https://www.thomasnet.com/insights/plastic-injection-molder-invents-innovative-american-made-fda-registered-covid-19-testing-swab/
Hatfield, PA – The Rodon Group participated in the Walmart sponsored U.S. Manufacturing Summit in Denver, CO. Walmart executives, industry experts, suppliers, and component manufacturers gathered for two days to discuss Walmart’s commitment to spending an additional $50 billion on investment of American-made products. Rodon exhibited at the Summit’s trade show event, where over 85 other contract manufacturers, material suppliers and service providers were on hand to meet with companies looking to manufacturer their products in the U.S. According to Michael Araten, President and CEO of K’NEX Brands and The Rodon Group, “Since 1992, our subsidiary The Rodon Group has helped K’NEX Brands make this a reality, manufacturing more than 32 billion bricks, rods and connectors at our plastic injection molding facility in Hatfield, Pennsylvania. We sell many of these toys at Walmart. So when the company (Walmart) announced its U.S. manufacturing commitment, we were thrilled – because we were aligned with a retailer that’s acting on a cause we’re passionate about.” Mr. Araten was personally invited by Walmart to speak at the Summit along with Jim Steven, CEO of Weber Grills. Walmart created a live webcast of the event which can be seen at http://news.walmart.com/events/2014-us-manufacturing-summit Walmart’s blog features an article by Mr. Araten, appropriately titled “Constructing the Future of U.S. Manufacturing”. In the post he states “While the case for manufacturing in America has been presented by many, some businesses remain skeptical that there are advantages. And we know firsthand the journey isn’t always easy. “At The Rodon Group, we not only make toys – we also make about 5 billion parts a year for industries from home construction to food and beverage. So we’ll be sharing those details with companies who are interested, and we’ll also be seeking our own partners, too.” Rodon has been on the forefront of American Manufacturing from the beginning, offering their “Cheaper than China" pricing policy and reshoring billions of manufactured parts back to the United States. According to Lowell Allen, executive vice president of manufacturing, recent expansion of their facility underscores Rodon’s commitment to re-shoring parts for other companies. “We have invested a great deal to increase our manufacturing capacity, strengthening our position as a premier U.S. plastics manufacturer.” About The Rodon Group The Rodon Group is an ISO 9001:2008 certified landfill-free, plastic injection molder. In business since 1956, The Rodon Group makes billions of parts each year in its 125,000 square foot facility. With over 105 injection molding presses, Rodon is one of the largest family-owned and operated plastic injection molders in the United States and serves a diverse group of industries including consumer products, medical, construction, pharmaceutical and toys. Since 1992, Rodon has manufactured over 32 billion parts for the K'NEX building toy system, and is a subsidiary of K'NEX Brands, L.P.
Full service manufacturers incorporate a complete line of production capabilities to facilitate fast, cost-efficient manufacturing of complex products without the need for multiple contractors.
The Rodon Group is proud to announce the launch of our newly redesigned website https://www.rodongroup.com/. Based on both customer and employee feedback, we’ve streamlined and enhanced our site using the latest technology to provide the best possible user experience for our customers and fellow industry professionals. With new user-friendly, intuitive design and various new educational resources, we’ve made it easier than ever to get started on your next high-volume project. What’s New? Let’s take a look at some of the new features our new website has to offer: Responsive Mobile Site In addition to redesigning our website for desktop and laptop, we’ve also accounted for the fact that people are now using technology everywhere - in the office, at home, while traveling. Our new website is responsive and reliable on mobile phone and tablet, so you can navigate our website with ease, whether at your desk or on the production floor. Resource and Media Libraries Our new Resource Library offers free informative guides, catalogs, and helpful industry information available for download. Our eBook titles include: “An Introduction to Plastic Injection Molding” “How to Manufacture a Perfect Plastic Part” and “10 Must-Ask Questions when Choosing a Plastic Injection Molder,” all of which provide valuable industry insights and answers to frequently asked questions customers about the plastic injection molding process. We also provide a comprehensive Media Library - a complete video and photo library that outlines our capabilities and turnkey manufacturing process. In the photo section, users can browse through photos of our engineers hard at work as well as images showcasing the interior and exterior of our cutting-edge facility. Custom Molding Case Studies As a leading authority on plastic injection molding, we’re proud of our innovative problemsolving solutions, offering our high volume customers custom solutions catered to their specific application and needs. Showcasing our diverse capabilities in our new Case Study section, we’ve compiled some examples of our previous work and product offerings, such as: Residential window hardware Custom beverage cap for the food and beverage industry Point-of-purchase (POP) display components Polystyrene diagnostic kit for the medical industry Solutions and Capabilities As a full-service turnkey manufacturer, The Rodon Group works with customers from concept to completion, providing all the necessary resources to promptly and accurately complete your project. On our new website, we break down the three main stages of this turnkey process - design, toolmaking, and manufacturing - allowing potential customers to easily assess our capabilities and further understand our production and quality control processes. Learn More Providing high-volume, custom plastic injection molding solutions since 1956, The Rodon Group offers innovative manufacturing solutions for customers who have an annual volume of 1 million or more parts per year. To learn more about The Rodon Group and how we can help with your next project, visit our new website https://www.rodongroup.com/ today.
As plastic injection molding methods continue to advance and evolve, allowing for enhanced flexibility and more sophisticated customization options, molding companies must be able to stay ahead of the curve in order to offer clients the latest technologies and highest-quality end products. At The Rodon Group, we’ve always been dedicated to constant innovation and improvement, and we’re proud to announce our recent acquisition of several new plastic injection molding machines. Nissei Plastic Injection Molding Machinery Amongst the new equipment are six new hybrid molding machines from Nissei’s FNX-III series - four FNX-180 III hybrid molding machines and two FNX-360 III hybrid molding machines. Incorporating aspects of both electrically and hydraulically powered molding machines, these models are powered by Nissei’s proprietary X-Pump. Besides allowing for energy-use reductions of up to 47% compared to fully hydraulic plastic injection molding machinery, X-Pump-equipped FNX-180 III and FNX-360 III machines offer a wide range of benefits, including: Fast injection response Wide-ranging injection speed Stability in ultra-low velocity range Long-sustained, high injection holding pressure Minimal maintenance and recalibration requirements Affordability, low maintenance, and running costs High-rigidity straight-hydraulic clamping unit Superior precision With greater tonnage capabilities than those of our existing machines, the new FNX-III series plastic injection molding equipment allows Rodon to offer greater production flexibility. We’ve operated this new equipment with several new production programs and have successfully run each machine in conjunction with a Star Automation Servo Robot, which we’ll discuss in greater detail below. Star Automation Servo Robot An industry-leading automated unloader manufacturer, Star Automation specializes in unloaders specifically designed for the injection molding industry; their Servo Robots series of unloaders are among the most reliable, high-performing models available on the market. Rodon’s new Servo robots allow for efficient automatic unloading and stacking of completed, ejected molded parts. Improving our production rates while ensuring the same level of quality clients have come to expect from Rodon, these sophisticated robots feature part present sensors, part and sprue grip circuits, custom step programming, active vibration control, and defective product drop. Learn More The Rodon Group is proud to be at the forefront of the many exciting advancements and trends in plastic injection molding, and our recent equipment acquisition is just one aspect of our commitment to continuous improvement. To learn more about working with a turnkey manufacturer and saving time and money, download our newest free guide today https://info.rodongroup.com/lp-download-the-benefits-of-working-with-a-turnkey-manufacturer. Or, for more information on our products and services, check out our comprehensive product catalog today https://info.rodongroup.com/lp-the-rodon-group-catalog.
We developed this eBook with designers, engineers and purchasing specialists in mind. It is written to provide a basic understanding of plastic injection molding presses, processes and costs. Our goal is to make our customers more knowledgeable about what goes into making a plastic part.
Thomas uses cookies to ensure that we give you the best experience on our website. By using this site, you agree to our Privacy Statement and our Terms of Use.
Robbins will be Vice President, Legal Affairs and General Counsel for K’NEX Brands Hatfield, PA, – K’NEX, the only U.S. construction toy company focused on Building Worlds Kids Love®, is pleased to announce the promotion of Rachel Robbins to Vice President, Legal Affairs and General Counsel. Hired in 2013, Ms. Robbins previously served as Associate General Counsel for K’NEX Brands. Prior to joining K’NEX, Ms. Robbins was a Partner in the Commercial Litigation group of the law firm Cozen O’Connor, where she successfully represented a broad spectrum of clients in the life safety, pharmaceutical, entertainment, internet, telecommunications and sports management industries in complex commercial disputes, including antitrust, securities, trademark infringement, and product liability actions. Ms. Robbins earned her Juris Doctor from the Dickinson School of Law of Pennsylvania State University, and served as Comments Editor for the Dickinson Law Review. She earned her undergraduate degree from Binghamton University, where she majored in business management, and minored in marketing. In her new position, Ms. Robbins will provide legal counsel to company management and business teams as to commercial relationships, as well as all general corporate matters, including contracts, employment, regulatory, and intellectual property matters. About K’NEX Brands Founded in 1992, K’NEX Brands, the world’s most innovative construction toy company, was established to make and sell what has become one of the world’s leading integrated construction systems for children, and is America’s STEM building solution. Winner of over 250 international awards and recognitions, K’NEX, America’s Building Toy® company, is focused on Building Worlds Kids Love® and encourages youngsters to “imagine, build and play.” From the living room to the classroom, K’NEX has building toys specially designed for every age group and skill level. The K’NEX family of brands includes K’NEX Building Sets, K’NEX Thrill Rides, K’NEX Education™, Lincoln Logs®, Tinkertoy®, NASCAR®, Angry Birds™, Mario Kart Wii™, Mario Kart 7™, Super Mario™, PacMan™, Titanfall™, Family Guy™, Plants vs. Zombies™, and more. Since 1992, The Rodon Group®, a subsidiary of K'NEX Brands, L.P., has manufactured over 31 billion parts for the K'NEX building toy system. Join us as we help build the leaders of tomorrow. For more information, please visit www.knex.com or www.rodongroup.com. Contact: Kate Loffio K’NEX Brands 215.996.4209 kloffio@knex.com
Prof. Dr.-Ing. Thomas Schröder, head of the institute, commented on the significance of the new machine: "The main advantage of the all-electric injection moulding machine is its complete readiness and equipment for digitalisation. We can send over 32,000 parameters from the injection moulding machine via interfaces like OPCUA to a cloud, where they can be analysed using AI and correlated with the quality features of the produced products. Additionally, an all-electric injection moulding machine can demonstrate how energy-efficient these plastic parts can be manufactured."
In the Master's programme in Plastics Technology, the machine is supplemented by the ENGEL tool sim link. Sim link allows Cadmould simulations to be directly integrated into the injection moulding process, making the production start more efficient. Machine and tool parameters are analysed by students using artificial intelligence and linked to part characteristics. By using this technology, students and researchers can trace and optimise the entire process from simulation to production, leading to a well-founded optimisation of the injection moulding process regarding production time, sustainability, and energy efficiency.
Injection molding services for hardware, appliances, doors, and windows. Works with acetal, nylon, acrylonitrile butadiene styrene (ABS), high impact polystyrene (HIPS), low and high density polyethylene, polyamide, polycarbonate (PC), and polypropylene (PP) materials. Cleanroom services are provided. Caps, fasteners, plugs, swabs, sockets, spacers, bushings, and washers are also offered. Prototypes and high volume production runs are available. Designing, engineering, tooling, and inventory management are offered as secondary services. Serves construction, medical, pharmaceutical, telecommunication, transportation, food, and beverage industries.
Our Standard Caps include a wide range of plastic caps, tubing caps, ball caps, square caps, rectangular caps, bar caps, vinyl shower rod caps, heavy caps, angle iron caps, concrete form bullet caps, heavy vinyl tips, reducing silencers, wire tips, concrete form end tips and self tapping thread protectors.
GETTING A QUOTE WITH LK-MOULD IS FREE AND SIMPLE.
FIND MORE OF OUR SERVICES:
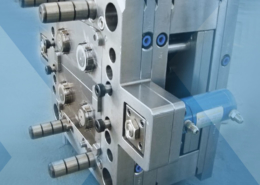
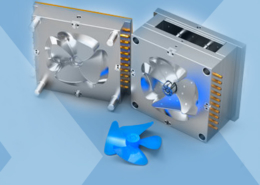
Plastic Molding

Rapid Prototyping
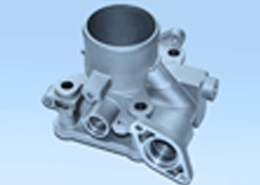
Pressure Die Casting
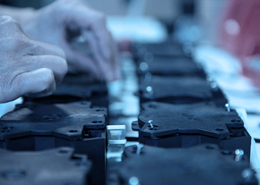
Parts Assembly
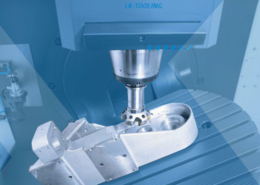