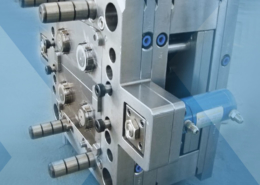
Exploring Precision Plastic Injection Moulding: Innovation and Impact
Author:gly Date: 2024-06-08
Introduction
Precision plastic injection moulding stands as a cornerstone of modern manufacturing, offering unparalleled precision, efficiency, and versatility in the production of intricate plastic components. This article delves into the world of precision plastic injection moulding, unraveling its intricacies, applications, and impact on various industries. From automotive to medical sectors, precision moulding has redefined manufacturing processes, driving innovation and enabling the realization of complex designs.
Understanding Precision Plastic Injection Moulding
Process Overview
Precision plastic injection moulding involves the injection of molten thermoplastic material into a carefully crafted mould cavity under high pressure, followed by rapid cooling and solidification to form the desired component. The process demands meticulous control of temperature, pressure, and cycle time to achieve consistent and high-quality results. Advanced machinery, robotics, and automation further enhance precision and efficiency, minimizing defects and optimizing production throughput.
Material Selection
Material selection plays a pivotal role in precision plastic injection moulding, with a wide range of thermoplastics available to meet diverse application requirements. From commodity plastics like polypropylene and polyethylene to engineering polymers such as ABS and nylon, each material offers unique properties in terms of strength, flexibility, and thermal stability. Moreover, the advent of bio-based and recycled plastics opens new avenues for sustainable manufacturing practices, aligning with environmental objectives.
Tooling and Design
The design and fabrication of precision moulds are critical factors in the success of plastic injection moulding. Utilizing advanced CAD/CAM software and machining techniques, toolmakers can create intricate moulds with tight tolerances and complex geometries. Moreover, innovations such as conformal cooling channels and rapid tooling technologies enhance thermal management and cycle times, optimizing production efficiency and part quality.Applications and Impact
Automotive Industry
In the automotive sector, precision plastic injection moulding is ubiquitous in the production of interior and exterior components, ranging from dashboards and door panels to engine components and lighting systems. The technique offers advantages such as lightweight construction, design flexibility, and cost-effectiveness, contributing to fuel efficiency, vehicle performance, and aesthetics. Furthermore, the integration of advanced materials and manufacturing processes enhances safety, durability, and sustainability in automotive applications.
Medical Devices
Precision plastic injection moulding plays a vital role in the manufacturing of medical devices and equipment, where accuracy, biocompatibility, and sterilizability are paramount. From syringes and surgical instruments to implantable devices and diagnostic equipment, molded components fulfill critical functions in healthcare delivery and patient care. Furthermore, the scalability and repeatability of injection moulding facilitate mass production of medical devices, ensuring accessibility and affordability for healthcare providers and patients worldwide.
Consumer Electronics
The consumer electronics industry relies heavily on precision plastic injection moulding to produce compact, lightweight, and durable components for smartphones, tablets, wearables, and home appliances. With shrinking form factors and increasing demand for customization, manufacturers leverage advanced moulding techniques to achieve intricate designs and tight tolerances. By integrating functions such as overmoulding and insert moulding, electronic devices can offer enhanced functionality, aesthetics, and user experience.Future Directions and Conclusion
In conclusion, precision plastic injection moulding serves as a catalyst for innovation, efficiency, and sustainability in modern manufacturing. As technology continues to advance, driven by digitalization, automation, and materials science, the potential of precision moulding to revolutionize diverse industries is boundless. By embracing the principles of precision engineering, design optimization, and sustainable practices, manufacturers can unlock new frontiers in plastic injection moulding, shaping a more resilient and sustainable future for generations to come.
As we look ahead, research and development efforts in areas such as material science, process optimization, and circular economy initiatives hold the key to unlocking the full potential of precision plastic injection moulding. By fostering collaboration, innovation, and knowledge-sharing, we can address global challenges and drive positive change in manufacturing practices, contributing to a more prosperous and sustainable world.
GETTING A QUOTE WITH LK-MOULD IS FREE AND SIMPLE.
FIND MORE OF OUR SERVICES:
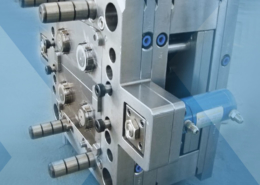
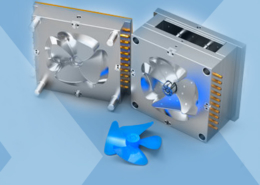
Plastic Molding

Rapid Prototyping
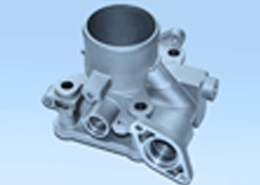
Pressure Die Casting
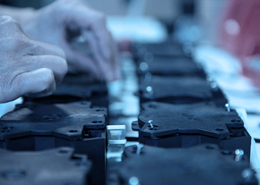
Parts Assembly
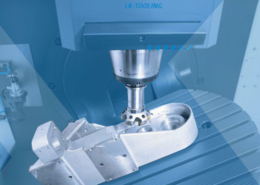