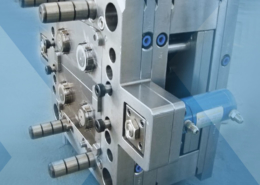
Exploring Precision Injection Molding: Innovations and Applications
Author:gly Date: 2024-06-08
Introduction
Precision injection molding stands at the forefront of modern manufacturing, offering unparalleled precision, efficiency, and versatility in the production of complex plastic components. From automotive parts to medical devices, this advanced manufacturing technique has revolutionized various industries, driving innovation and enabling the realization of intricate designs. In this article, we delve into the world of precision injection molding, unraveling its intricacies, applications, and future prospects.
Understanding Precision Injection Molding
Technological Evolution
The evolution of precision injection molding traces back to the mid-20th century, with the development of thermoplastic and thermosetting polymers. Over the decades, advancements in materials science, machinery, and computer-aided design (CAD) have propelled the technique to new heights of precision and efficiency. Today, precision injection molding encompasses state-of-the-art processes, including micro-molding, multi-shot molding, and insert molding, catering to diverse manufacturing needs.
Process Overview
At its core, precision injection molding involves the injection of molten polymer into a mold cavity under high pressure, followed by cooling and solidification to form the desired component. The process demands meticulous control of temperature, pressure, and injection speed to achieve precise outcomes consistently. With the advent of digital technologies and automation, manufacturers can optimize process parameters and enhance product quality while reducing production costs and lead times.
Quality Assurance
Quality assurance is paramount in precision injection molding, given the stringent requirements of industries such as aerospace, healthcare, and electronics. Advanced metrology techniques, including coordinate measuring machines (CMMs) and optical inspection systems, enable manufacturers to verify dimensional accuracy and detect defects with utmost precision. Moreover, rigorous testing protocols and adherence to industry standards ensure the reliability and safety of molded components in real-world applications.Applications and Impact
Automotive Industry
In the automotive sector, precision injection molding plays a pivotal role in the production of interior and exterior components, ranging from dashboard panels to bumpers. The technique offers advantages such as lightweight construction, design flexibility, and cost-effectiveness, contributing to fuel efficiency, vehicle performance, and aesthetics. With the rise of electric vehicles and autonomous driving technology, the demand for precision-molded components is expected to surge, driving innovation and sustainability in the automotive industry.
Medical Devices
Precision injection molding is indispensable in the manufacturing of medical devices and equipment, where accuracy, biocompatibility, and sterilizability are paramount. From syringe barrels to implantable devices, molded components fulfill critical functions in diagnosis, treatment, and patient care. Furthermore, the scalability and repeatability of injection molding facilitate mass production of medical devices, ensuring accessibility and affordability for healthcare providers and patients worldwide.
Consumer Electronics
The consumer electronics industry relies heavily on precision injection molding to produce compact, lightweight, and durable components for smartphones, tablets, and wearable devices. With shrinking form factors and increasing demand for customization, manufacturers leverage advanced molding techniques to achieve intricate designs and tight tolerances. By integrating functions such as overmolding and micro-molding, electronic devices can offer enhanced functionality, aesthetics, and user experience.Future Directions and Conclusion
As precision injection molding continues to evolve, driven by advancements in materials, technologies, and sustainability initiatives, its impact on manufacturing and society is poised to expand. From micro-scale components to large-scale structures, the technique offers boundless opportunities for innovation, efficiency, and environmental stewardship. By embracing digitalization, automation, and sustainable practices, manufacturers can unlock new frontiers in precision molding, shaping a more resilient and sustainable future for generations to come.
In conclusion, precision injection molding stands as a cornerstone of modern manufacturing, enabling the realization of intricate designs, the optimization of production processes, and the advancement of various industries. As we look ahead, the journey of precision molding is marked by innovation, collaboration, and a steadfast commitment to quality and sustainability. By harnessing the full potential of precision injection molding, we can embark on a path of continuous advancement, driving progress and prosperity in the global manufacturing landscape.
GETTING A QUOTE WITH LK-MOULD IS FREE AND SIMPLE.
FIND MORE OF OUR SERVICES:
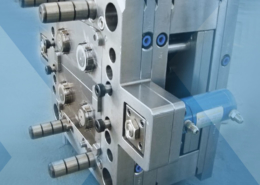
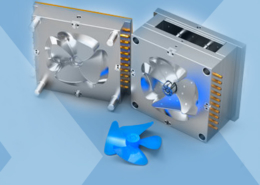
Plastic Molding

Rapid Prototyping
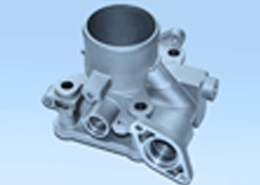
Pressure Die Casting
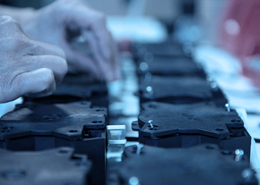
Parts Assembly
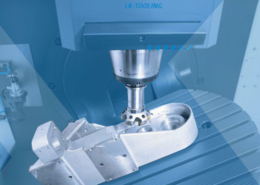