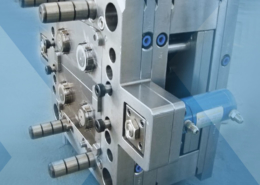
Plastic Prototype Manufacturing: Shaping the Future
Author:gly Date: 2024-06-08
Introduction
Plastic prototype manufacturing serves as a cornerstone of innovation, offering a gateway to transform conceptual designs into tangible realities. As industries embrace rapid product development cycles and customization demands, the role of plastic prototypes becomes increasingly indispensable. This article delves into the realm of plastic prototype manufacturing, elucidating its significance, methodologies, applications, and future trends.
The Significance of Plastic Prototypes
Plastic prototypes serve as invaluable tools in the product development process, enabling designers and engineers to visualize concepts, validate designs, and iterate rapidly. By bridging the gap between ideation and production, plastic prototypes facilitate informed decision-making, mitigating risks and optimizing product performance, functionality, and aesthetics.
Moreover, plastic prototypes serve as effective communication tools, facilitating stakeholder engagement and feedback early in the design process. By eliciting user input and preferences, prototypes ensure alignment with market needs and enhance product-market fit, ultimately driving innovation and competitive advantage.
Methodologies in Plastic Prototype Manufacturing
Plastic prototype manufacturing encompasses a diverse array of methodologies, each tailored to specific design requirements, materials, and production volumes. Rapid prototyping techniques such as stereolithography (SLA), selective laser sintering (SLS), and fused deposition modeling (FDM) offer expedited turnaround times and cost-effective solutions for low-volume prototyping.
Conversely, traditional manufacturing processes like CNC machining and injection molding excel in producing high-precision prototypes with superior surface finish and mechanical properties. Hybrid approaches, combining additive and subtractive techniques, further enhance versatility and efficiency in plastic prototype manufacturing, catering to a spectrum of design complexities and production scales.
Applications Across Industries
Plastic prototypes find applications across diverse industries, ranging from aerospace and automotive to consumer electronics and healthcare. In aerospace and automotive sectors, prototypes facilitate aerodynamic testing, ergonomic evaluation, and functional validation, enabling manufacturers to optimize performance, safety, and fuel efficiency.
In consumer electronics, prototypes serve as platforms for user interface testing, form factor validation, and aesthetic refinement, ensuring seamless integration with user lifestyles and preferences. Similarly, in healthcare, prototypes enable surgeons to rehearse complex procedures, medical device manufacturers to conduct clinical trials, and prosthetics designers to customize patient-specific solutions, ultimately improving patient outcomes and quality of life.
Future Trends and Emerging Technologies
Looking ahead, the landscape of plastic prototype manufacturing is poised for continued innovation and disruption. Advancements in materials science, such as bio-based polymers and nanocomposites, offer new possibilities for sustainable and high-performance prototypes with enhanced biocompatibility and environmental compatibility.
Furthermore, the integration of artificial intelligence (AI) and machine learning (ML) algorithms streamlines design optimization, material selection, and process simulation, accelerating the prototyping process and minimizing development costs. Additive manufacturing technologies, including multi-material printing and continuous liquid interface production (CLIP), unlock new frontiers in geometric complexity, material versatility, and production scalability, heralding a future where plastic prototypes transcend traditional boundaries and catalyze transformative innovation across industries.
Conclusion
In conclusion, plastic prototype manufacturing embodies the intersection of creativity, technology, and practicality, offering a dynamic platform for innovation and experimentation. The evolution of methodologies, applications, and emerging technologies underscores the enduring relevance and potential of plastic prototypes in driving product development, market competitiveness, and societal progress. Moving forward, continued investment in research, collaboration, and technological adoption is essential to unlock new frontiers in plastic prototype manufacturing and realize the full spectrum of possibilities in product innovation and design.
GETTING A QUOTE WITH LK-MOULD IS FREE AND SIMPLE.
FIND MORE OF OUR SERVICES:
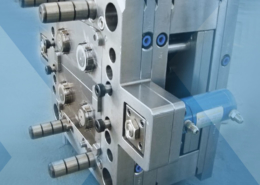
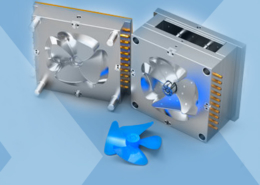
Plastic Molding

Rapid Prototyping
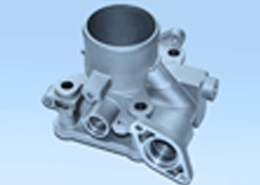
Pressure Die Casting
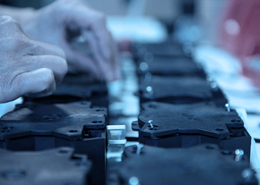
Parts Assembly
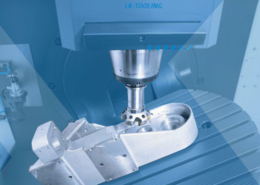