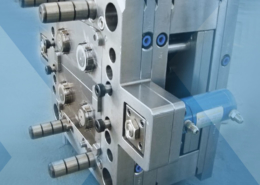
Exploring Plastic Part Molding: Innovation and Efficiency
Author:gly Date: 2024-06-08
Introduction
Plastic part molding stands as a cornerstone in modern manufacturing, revolutionizing the production of a myriad of products we interact with daily. Its importance cannot be overstated, as it not only offers versatility in design but also ensures cost-effectiveness and efficiency in mass production. In this comprehensive exploration, we delve into the intricacies of plastic part molding, unraveling its significance, techniques, and future prospects.
1. Injection Molding
Overview
Injection molding reigns supreme as the most widely used method in plastic part molding. This technique involves injecting molten material into a mold cavity under high pressure, allowing for the precise replication of intricate designs. Its versatility in accommodating various thermoplastics and its rapid production capabilities make it indispensable in industries ranging from automotive to electronics.
Process and Machinery
The injection molding process begins with the feeding of raw materials into the hopper of the injection molding machine. The material is then heated to its melting point and injected into the mold cavity under pressure. Once cooled and solidified, the mold opens, and the finished part is ejected. Advanced machinery, equipped with computerized controls and robotics, ensures precise and consistent results.
Advantages and Limitations
The advantages of injection molding are manifold, including high efficiency, minimal material waste, and the ability to produce complex geometries with tight tolerances. However, challenges such as initial tooling costs and limited flexibility in small-scale production remain noteworthy limitations.
2. Blow Molding
Overview
Blow molding is a specialized technique primarily used for producing hollow plastic parts, such as bottles and containers. It involves inflating a heated plastic parison (hollow tube) within a mold cavity, conforming to its shape. This method is renowned for its scalability and cost-effectiveness in large-scale production.
Process Variants
There are several variants of blow molding, including extrusion blow molding, injection blow molding, and stretch blow molding, each offering unique advantages depending on the desired product specifications. Extrusion blow molding, for instance, is ideal for manufacturing simple hollow shapes, while injection blow molding excels in producing precise neck finishes for bottles.
Applications and Innovations
Blow molding finds extensive applications in the packaging industry, particularly in the production of bottles, containers, and drums. Recent innovations in materials and process optimization have further expanded its usage into sectors like automotive, where lightweight and durable components are in demand.
3. Compression Molding
Overview
Compression molding involves the preheating of a thermosetting material, which is then placed into an open mold cavity. The mold is closed, and pressure is applied, causing the material to spread and conform to the mold's shape. This method is favored for its simplicity and suitability for high-strength composite materials.
Materials and Processing
Compression molding is well-suited for thermosetting polymers like fiberglass, polyester, and phenolic resins. The process typically involves heating the material above its glass transition temperature, allowing for flow and consolidation within the mold cavity. Post-curing may be required to enhance the material's mechanical properties.
Advantages and Challenges
The advantages of compression molding include low tooling costs, minimal material waste, and the ability to produce large and intricate parts. However, cycle times can be relatively long, and achieving consistent part quality may require meticulous process control and mold design.
4. Thermoforming
Overview
Thermoforming is a versatile manufacturing process used to create a wide range of plastic parts, primarily from thin-gauge sheets. It involves heating a thermoplastic sheet to its softening point and then draping it over a mold. Vacuum or pressure is applied to form the sheet into the desired shape, followed by cooling and trimming.
Materials and Applications
Thermoforming accommodates a variety of thermoplastics, including ABS, polycarbonate, and PVC, offering flexibility in material selection based on performance requirements. Its applications span diverse industries, from consumer goods packaging to automotive interior components.
Process Optimization
Advancements in thermoforming technology have led to enhanced process efficiency and part quality. Techniques such as twin-sheet forming and pressure forming enable the production of complex geometries with improved surface finishes. Furthermore, integration with robotics and automation streamlines production workflows, reducing cycle times and labor costs.
Conclusion
In conclusion, plastic part molding represents a cornerstone of modern manufacturing, offering unparalleled versatility, efficiency, and cost-effectiveness. Through techniques such as injection molding, blow molding, compression molding, and thermoforming, manufacturers can realize intricate designs and meet diverse market demands. Continued innovation and integration of advanced technologies promise to further enhance the capabilities and sustainability of plastic part molding, ensuring its enduring relevance in the global manufacturing landscape.
GETTING A QUOTE WITH LK-MOULD IS FREE AND SIMPLE.
FIND MORE OF OUR SERVICES:
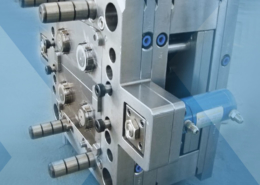
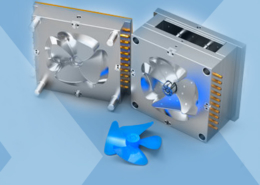
Plastic Molding

Rapid Prototyping
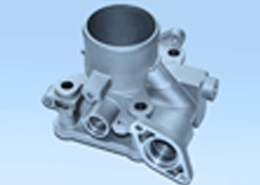
Pressure Die Casting
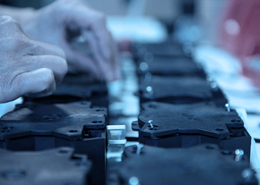
Parts Assembly
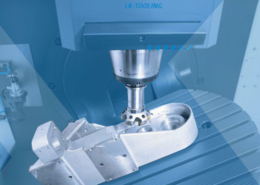