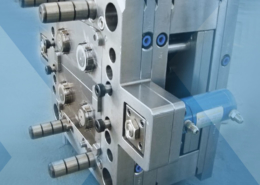
High transparency PP resin clears way for extrusion blow molding - pp injection
Author:gly Date: 2024-09-30
Solvay has been appointed the primary composite material supplier to Beta Technologies, an electric aircraft company based in Vermont. Solvay will provide Beta with qualification support and advanced materials for the production of its Alia CTOL fixed-wing electric aircraft and Alia VTOL electric vertical takeoff and landing (VTOL) aircraft, developed for a variety of applications, including medical, cargo, and passenger transportation. Solvay is a leading supplier of carbon-fiber-reinforced materials as well as thermoset and thermoplastic composites.
Anticipating EU-mandated reduction of CO2 emissions by manufacturers, the Wittmann Group has created a simple calculator to determine the product carbon footprint (PCF) throughout a product’s lifecycle.
The IMAGOxt software creates a dynamic picture of energy use and lets users create custom key performance indicators to monitor usage, according to a Wittmann data sheet. The system integrates all industrial communication instruments, including previously existing equipment, and allows data access via the cloud.
Wittmann’s calculator software will be available with the company’s TEMI+ manufacturing execution system (MES). By clicking a production cell on the TEMI+ extended dashboard, a processor receives data for each production cycle, including CO2 emissions for single- or multi-cavity molds expressed in grams per cycle.
The PCF calculation determines emissions from raw material production to recycling. The calculation is based on energy consumption of an injection molding cell and the amount of raw material processed per cycle (shot weight).
“For Germany, for example, with the current electricity mix, the factor is 0.354 g CO2 per Wh (watt hour),” the company said in a press release. “This value is stored in the MES or shared from the customer’s ERP so that the system can automatically calculate the CO2 footprint of the production cell. The CO2 footprint of the raw material is also a predefined value . . . provided by the material manufacturer and entered into the MES.”
Solvay and Beta are collaborating to select and qualify a tailored suite of materials from Solvay’s broad portfolio to meet the rigorous performance demands of the Advanced Air Mobility (AAM) market. Composites and specialty polymers will be used for primary and secondary structures, as well as non-structural parts, combining multifunctional integration with high strength and low weight as well as electromagnetic interference and lightning protection.
“Solvay is proud to be the advanced material supplier of choice for Beta Technologies as it brings its new aircraft to market,” said Marc Doyle, executive vice president of composite materials at Solvay. “These vehicles represent a new dawn in safe and efficient electric aviation. Solvay's unrivaled portfolio of composite, adhesive, and specialty polymer solutions will help ensure the development of lightweight and certifiable aircrafts. Our technical team is supporting Beta and its partners both remotely and on site across material qualification, certification, and industrialization. We are excited to be involved in this pioneering program.”
The product carbon footprint calculator measures cradle-to-grave emissions based on energy consumption of injection molding cell and amount of raw material processed per cycle.
Stephen has been with PlasticsToday and its preceding publications Modern Plastics and Injection Molding since 1992, throughout this time based in the Asia Pacific region, including stints in Japan, Australia, and his current location Singapore. His current beat focuses on automotive. Stephen is an avid folding bicycle rider, often taking his bike on overseas business trips, and is a proud dachshund owner.
“We’re focused on building the safest, most reliable, technically proficient, and scalable electric aircraft, and that means starting from the strongest foundation possible, right down to the materials and systems we use," said Beta Technologies founder and CEO Kyle Clark. "We are proud to be collaborating with Solvay and benefit from their broad knowledge and experience of aerospace materials qualifications and unmatched technical support.”
Geoff Giordano is a tech journalist with more than 30 years’ experience in all facets of publishing. He has reported extensively on the gamut of plastics manufacturing technologies and issues, including 3D printing materials and methods; injection, blow, micro and rotomolding; additives, colorants and nanomodifiers; blown and cast films; packaging; thermoforming; tooling; ancillary equipment; and the circular economy. Contact him at [email protected].
Energy usage is measured every cycle, either by the MES or Wittmann’s IMAGOxt software. This energy management software (EMS) was designed to help Wittmann customers implement the EU Green Deal, a plan to make the continent climate-neutral by 2050. IMAGOxt can use data gathered from sensors on all points of energy consumption to indicate energy costs per machine or injection molded part.
GETTING A QUOTE WITH LK-MOULD IS FREE AND SIMPLE.
FIND MORE OF OUR SERVICES:
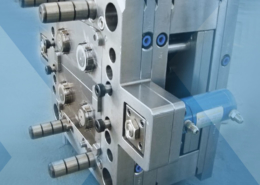
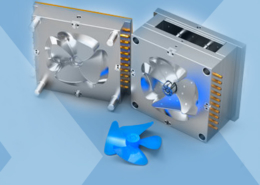
Plastic Molding

Rapid Prototyping
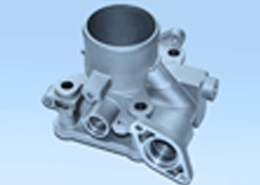
Pressure Die Casting
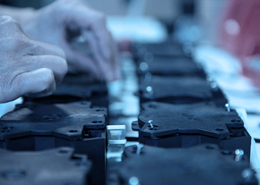
Parts Assembly
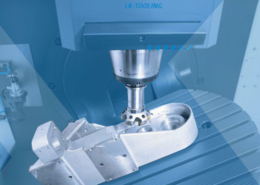