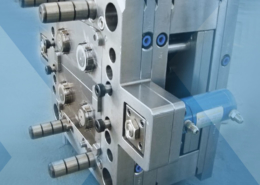
Global Automotive Supplier Adds New Materials and Processes to Win Big with
Author:gly Date: 2024-09-30
Hanwha Advanced Materials also outlined its vision of next-generation car seats in a presentation at JEC Asia last year in Seoul, Korea. “The seat of tomorrow will be a place for working, taking a nap or even postural analysis in a wellness seat,” according to the company. Hanwha Advanced Materials expects to see the emergence of low-center-of-gravity designs that will contribute to an overall lower center of gravity in the vehicle and thereby contribute to overall vehicle safety.
Our expert buyer's guide provides all you need to know about the best entry-level, professional, and industrial metal 3D printers, plus specs, prices, and a metal 3D printing technology primer.
Stephen has been with PlasticsToday and its preceding publications Modern Plastics and Injection Molding since 1992, throughout this time based in the Asia Pacific region, including stints in Japan, Australia, and his current location Singapore. His current beat focuses on automotive. Stephen is an avid folding bicycle rider, often taking his bike on overseas business trips, and is a proud dachshund owner.
Scheduled for serial production in the near future, a seat frame compression-molded from a glass-mat-reinforced thermoplastic polypropylene (PP) composite delivers several advantages over incumbent conventional steel frames, according to its developer Hanwha Advanced Materials of South Korea. Besides an around 15–20% weight reduction versus steel (9.3 kg versus 10.98 kg in the current example), the plastic seat frame also enables a 60:40 split design option. This allows for the installation of three, three-point seatbelts. To boot, the GMT-PP composite possesses the necessary mechanical strength to be employed in the seatbelt anchor components.
The future of car interior design is also likely to feature interchangeable/exchangeable car seats incorporating more functionality such as electronic adjustment functions, which will mean more emphasis on engineering out excess weight, potentially through the use of more plastics. The occupants can also look forward to more cabin space; if there are only three passengers, one car seat could be detached and left at home.
Further advantages include 22% fewer components (25 versus 37 for a steel frame), no corrosion issues and lower assembly costs, as there is no need for welding. Using plastics also expands design options such as locations to tether and retain luggage. Forward and rearward movements are also on a par with a steel frame.
GETTING A QUOTE WITH LK-MOULD IS FREE AND SIMPLE.
FIND MORE OF OUR SERVICES:
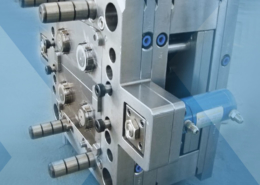
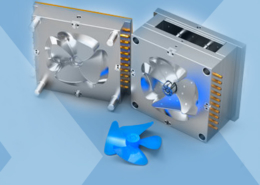
Plastic Molding

Rapid Prototyping
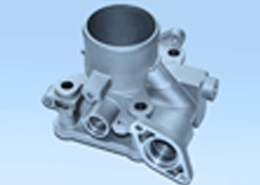
Pressure Die Casting
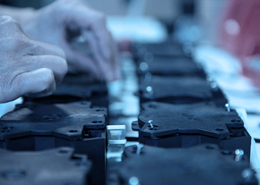
Parts Assembly
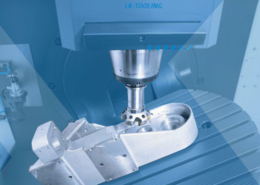