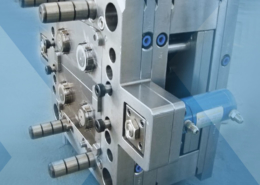
Global Automotive Supplier Adds New Materials and Processes to Win Big with
Author:gly Date: 2024-09-30
Advanced Engineering is the UK’s largest annual gathering of engineering and manufacturing professionals. The event will help you to source new suppliers, network, build connections and learn about the latest industry developments all in one place. Get involved and exhibit alongside 400+ exhibitors offering solutions and products across all industries and sectors to help improve your productivity and inspire creativity. With over 9,000+ of your peers due to attend and ready to network with and inspire you, this is the event you can’t afford to miss!
Why the unusual product name? “In ancient Greek myths, Kyron (also spelled Chiron) was part centaur and part human,” explains Randy White, MCAM chief innovation officer. “Kyron used his unique personal skills to rise above his beastly nature. We likened that to our compounds, which are half carbon fiber and half resin, so as strong as a horse and as smart as a human for ease of processing.”
American Bureau of Shipping (ABS) certifies use of jointly developed CFRP repair technique on FPSO and FSO industrial systems, addressing traditional steel restoration challenges.
CompositesWorld is the source for reliable news and information on what’s happening in fiber-reinforced composites manufacturing. About Us
New aircraft is expected to deliver wind turbine blades from 105 meters up to expand the reach of wind energy and achieve global climate goals.
CompositesWorld’s CW Tech Days: Infrastructure event offers a series of expert presentations on composite materials, processes and applications that should and will be considered for use in the infrastructure and construction markets.
The composite tubes white paper explores some of the considerations for specifying composite tubes, such as mechanical properties, maintenance requirements and more.
Whether you’re exploring new applications or seeking to gain a foothold in emerging markets, Carbon Fiber 2024 is where you’ll discover the insights and connections needed to shape your business strategy. Register now.
Cevotec, a tank manufacturer, Roth Composite Machinery and Cikoni, have undertaken a comprehensive project to explore and demonstrate the impact of dome reinforcements using FPP technology for composite tanks.
An MCAM customer wanted to replace metal injection molded (MIM) magnesium with a composite on a performance mountain bike’s suspension elements with the goals of reducing mass and avoiding processing concerns with the reactive alkaline earth metal. Given the complexity of the part and the production volumes involved, only injection molding could meet the customer’s price point. MCAM formulated a 30% FWF short carbon fiber-reinforced polyphenylene sulfide (PPS) composite (KyronMAX S-8230) that met all mechanical requirements — including challenging fatigue targets — and successfully replaced magnesium in this application. Photo Credit, all images: Mitsubishi Chemical Advanced Materials Inc.
Recoat temperature, part orientation and bead geometry are some key design variables to consider for a successful and reliable large-format additive manufacturing (LFAM) process.
Stephen has been with PlasticsToday and its preceding publications Modern Plastics and Injection Molding since 1992, throughout this time based in the Asia Pacific region, including stints in Japan, Australia, and his current location Singapore. His current beat focuses on automotive. Stephen is an avid folding bicycle rider, often taking his bike on overseas business trips, and is a proud dachshund owner.
“On a datasheet, LFT compounds look stronger, but often they’re unable to fill the kinds of part geometry we can fill with short carbon fiber technology,” explains Alex Wojtysiak, MCAM key accounts manager – composites. “Because our flow is so much higher, we’re better able to fill intricate geometry, so our compounds produce parts that are dramatically stronger.”
Program will focus on sustainable, next-gen wing solutions, including in wing design and manufacturing and advancements in carbon fiber-reinforced composite materials.
Now, with greater production capacity and access to a broader array of polymer and carbon fiber materials, the MCAM team has been busy developing an array of new products — several of them specifically formulated for the automotive market. One of the most interesting is KyronMAX ES 4240, said to be the world’s first short carbon fiber injection molding compound to break the 414 MPa (60,000 psi) tensile strength barrier. That grade, which was introduced at the 2019 SPE Automotive Engineered Plastics Conference (AutoEPCON) in the Detroit suburbs, is a 40% fiber weight fraction (FWF) carbon fiber-reinforced PPA that also offers tensile modulus values of 41.2 GPa, flexural modulus values of 34.5 GPa and flexural strength values of 552 MPa. PPA is a specialized form of polyamide with better thermal and broader chemical resistance and far lower tendency toward hydrolysis than conventional PA6 and PA6/6.
An overview of ASTM Standard Guide D8509, and its coupon-level mechanical testing of design properties for analyzing composite bolted joints.
Herone, Spiral RTC, Teijin Carbon Europe and Collins Aerospace Almere recycle A350 thermoplastic composite clips/cleats waste into rods for the all-thermoplastic composite Multifunctional Fuselage Demonstrator’s crown.
Additionally, stitch-bonded non-crimp fabrics (NCFs) provide manufacturers and asset owners even more ways to gain a competitive advantage with products built specifically for the environments and loading conditions in which they will be utilized. Join Vectorply Corporation and Creative Composites Group (CCG) for this in-depth webinar detailing the process of engineering NCFs to build composite parts that will stand the test of time. Unlike steel, concrete and wood, composite NCFs can be optimized utilizing various fiber types, architectures and substrates to achieve the specific goals of their application efficiently. High corrosion resistance, strength and stiffness, and longevity can all be accomplished with custom-designed laminates for these heavily abused applications. Vectorply Vice President of Engineering Trevor Gundberg and Creative Composites Group Chief Sales Officer Dustin Troutman will share their industry-leading expertise on the process of laminate design and part production. Attendees can expect to learn when to use composite NCFs in their production process and the wide range of fiber-reinforced plastic (FRP) composites that Creative Composites Group produces for the industrial and infrastructure markets. Whether you want to learn more about utilizing NCFs in your production process or why CCG’s extensive product line may be the choice for your project, this webinar is the place learn the process and how to take the next steps. Agenda: Distinct advantages of non-crimp fabrics versus alternative materials How to design laminates for specific processes such as pultrusion and infusion Real-world success spotlights of NCFs in industrial applications
Analyzing structural resonance of the aircraft under various loads becomes a critical step in obtaining flight certification.
During this CW Tech Days event, sponsored by Composites One, experts will offer presentations to review and evaluate the composite materials, processes and applications that should and will be considered for use in the infrastructure and construction markets.
Reliable news and information on where and how fiber-reinforced composites are being applied — that’s just the start of what you get from our team here at CompositesWorld.
Circa 2012, Piper was a midsize custom injection molder serving a customer base in aerospace and sporting goods/recreational equipment. Company leadership wanted to grow its parts-making business but had two challenges. First, it was having trouble sourcing the kinds of compounds the team felt would enable the company to compete in higher performance market segments. Second, the company wanted to enter the automotive market, but didn’t have enough available molding capacity to compete on major programs.
The composites-intensive VTOL platform is next expected to undergo a series of test flights in various conditions to validate its performance, safety and reliability, leading up to eventual certification.
Over the last 8 months, Archer Aviation has completed a total of 402 test flights with its composites-intensive aircraft, adding to key milestones.
Thousands of people visit our Supplier Guide every day to source equipment and materials. Get in front of them with a free company profile.
In these sessions, experts will discuss the emerging hydrogen economy and the opportunities for composites in this lucrative space.
The materials are formulated and sold by Mitsubishi Chemical Advanced Materials Inc. (MCAM, Tokyo, Japan). MCAM combines several previously separate businesses acquired by the parent company over the last decade. These include the former Quadrant AG (Lenzburg, Switzerland), a producer of glass mat thermoplastic (GMT) and organosheet composites as well as thermoplastic engineered shapes, and what had been Piper Plastics Inc. (Chandler, Ariz., U.S.), which started life as an injection molder and producer of precision machined parts, and later expanded into custom CFRTP compounding — first for its own use and later for other molders.
Stephen Heinz, vice president of R&I for Syensqo delivered an inspirational keynote at SAMPE 2024, highlighting the significant role of composite materials in emerging technologies and encouraging broader collaboration within the manufacturing community.
Increasingly, prototype and production-ready smart devices featuring thermoplastic composite cases and other components provide lightweight, optimized sustainable alternatives to metal.
Whether you’re exploring new applications or seeking to gain a foothold in emerging markets, Carbon Fiber 2024 is where you’ll discover the insights and connections needed to shape your business strategy. Register now.
Explore the cutting-edge composites industry, as experts delve into the materials, tooling, and manufacturing hurdles of meeting the demands of the promising advanced air mobility (AAM) market. Join us at CW Tech Days to unlock the future of efficient composites fabrication operations.
Celebrating National Composites Week 2024, CW looks at how composites are being used to provide the next generation of energy.
As its product line has expanded, so too have the markets in which these materials are used. In addition to long-desired automotive business, the company now serves medical device (both durable and disposable), small appliance and consumer electronics (metal replacement cases/covers). Aviation/aerospace is still important, as is the sporting goods industry, which has grown to include applications on racing bikes, mountain bikes, golf clubs, firearms, compound bows and other archery parts. With several products offering coefficient of linear thermal expansion (CLTE) values similar to those of metal injection molded (MIM) aluminum and magnesium — albeit with better toughness, lighter weight and lower cost — the team finds itself replacing metals in an increasing array of applications.
Milacron India’s Ahmedabad facility completed its most recent expansion in 2016. The expansion allowed Milacron to increase its annual output of 1,500 injection and blow molding machines to 2,100 machines per annum, a 40% increase.
In the Automated Composites Knowledge Center, CGTech brings you vital information about all things automated composites.
Knowing the fundamentals for reading drawings — including master ply tables, ply definition diagrams and more — lays a foundation for proper composite design evaluation.
The Marservis PROeco is a mass transportation marine vessel using Bcomp natural fiber for interior parts in place of standard materials.
The DOMMINIO project combines AFP with 3D printed gyroid cores, embedded SHM sensors and smart materials for induction-driven disassembly of parts at end of life.
On March 22nd, Milacron’s India manufacturing team presented its 12,501st India manufactured machine. The Milacron Magna Toggle 450 ton 2K machine was handed over to Vagish Dixit – Managing Director, Alpla India Company, a manufacturer of caps and closures and affiliate of Austria’s Alpla Werke Alwin Lehner GmbH & Co KG.
Established in 1995, the Indian plant offers a full range of injection moulding machines from 50-ton to 3200-ton clamping force, with capacity to manufacture 2000 machines per annum.
This collection features detail the current state of the industry and recent success stories across aerospace, automotive and rail applications.
The composites industry plays a crucial role in developing lightweight and durable materials for a range of applications, including those critical to national defense. One key focus area is the development of advanced structural materials and manufacturing technologies that support next-generation space, missile and aircraft systems for the U.S. Department of Defense (DOD). ARC Technologies LLC (ARC), a division of Hexcel Corporation, based in Amesbury, Massachusetts, is a provider of advanced composites structures, specialty materials and other unique products that provide the U.S. Department of Defense with advanced capabilities to protect service members while in harm’s way. This team’s specialty is to understand a specific need from a program office, PEO, platform manufacturer or other offices within the DOD. With that understanding, the team can design a solution, develop a prototype for test and evaluation, perform extensive in-house testing — including electromagnetic, environmental and structural testing — and then partner with the customer through platform evaluation. The Hexcel Amesbury division has a team of engineers on staff, including mechanical, chemical, electrical and research and development specialists that can provide design, testing and manufacturing capabilities to service customer requirements from concept through production. This presentation will illustrate capabilities in advanced composites and other specialty materials structures, focusing on the Hexcel Amesbury team's niche in electromagnetic signature reduction and other unique capabilities.
CompPair and Composite Recycling introduce a roof scoop made of recycled fibers to an eco-efficient rally buggy, which channels airflow to the engine for optimal, sustainable performance.
Kennametal will cover the influence of different composite materials characteristics on drilling performance and how to optimize the process. Agenda: Who is Kennametal? Hole making challenges in composite materials Innovations for hole making applications Upcoming events and academic partnerships
Foundational research discusses the current carbon fiber recycling landscape in Utah, and evaluates potential strategies and policies that could enhance this sustainable practice in the region.
While the world continues to wait for new single-aisle program announcements from Airbus and Boeing, it’s clear composites will play a role in their fabrication. But in what ways, and what capacity?
The first problem was solved by applying a focused R&D effort on various base resins and fiber sizing technologies, which led to the development of a family of high-performance, injection moldable CFRTP compounds called KyronMAX. These materials feature matrices such as polyamide 6/6 (PA6/6), polyphthalamide (PPA), polyetherimide (PEI), polyphenylene sulfide (PPS), polyetheretherketone (PEEK) and polyaryletherketone (PAEK) reinforced with short chopped carbon fiber. The compounds — most of which offer high thermal performance, broad chemical resistance, good mechanicals and low flame/smoke/toxicity (FST) values — were formulated not only to replace short glass fiber-reinforced and mineral-filled injection molding grades, but also LFT compounds (with average starting fiber length of 13 millimeters) and even metals.
CW Tech Days are virtual events dedicated to the topics impacting the composites industry today. Access past event recordings and register for upcoming Tech Days.
EU project will develop bio-based, repairable and recyclable vitrimer composites and advanced sensors for highly reliable, sustainable wind blades.
A family of short carbon fiber-reinforced thermoplastic (CFRTP) compounds specifically formulated for injection molding is being used to extend the capabilities of thermoplastic composites in a variety of part sizes and complexities. Interestingly, these materials have been shown to outperform long fiber thermoplastic (LFT) composites (in fiberglass or carbon fiber) as well as metals in a growing range of applications — from sporting goods and car parts to medical devices and aerospace components.
Closed mold processes have many advantages over open molding. In this knowledge center, learn the basics and vital tools needed to produce parts accurately.
Initial demonstration in furniture shows properties two to nine times higher than plywood, OOA molding for uniquely shaped components.
This collection details the basics, challenges, and future of thermoplastic composites technology, with particular emphasis on their use for commercial aerospace primary structures.
With fiber weight fractions of up to 50% and an array of thermoplastic matrices available, injection molding compounds are expanding composites’ capabilities.
During this webinar, the audience will be introduced to a variety of fiber composite technologies — as well as the machines and equipment — from short fibers to continuous fibers, from thermoset to thermoplastic, as well as the according process technology, including a special focus on long-fiber injection (LFI) and structural composite spray (SCS). Focus markets include automotive, aviation and AAM, transportation, and construction. This webinar will provide a detailed overview of according application examples. Agenda: Long fiber injection (LFI) Structural composite spray (SCS) Resin transfer molding (RTM), wet compression molding, etc. Pultrusion FiberForm
In other news, Milacron’s Mold-Masters product brand recently celebrated its 10th anniversary. Mold-Masters started its Indian operations in 2007 as an engineering center along with a dedicated sales and service team to provide better support to domestic market. The India hot runner operations expanded in 2010 adding a manufacturing plant to become the first global hot runner brand to do so in India. In recent years the Coimbatore, India facility has undergone a number of expansions to better serve the rapidly growing market demands in India and grown over 350 employees. The anniversary was celebrated with a special customer event.
Keyland Polymer's R&D chemist will demonstrate the UV powder coating application process followed by UV curing on a carbon fiber water bottle holder. (Sponsored)
Validation of 80-100% tensile strength and comparability to injection molding via Voxelfill extrusion process was achieved through plastic and fiber-filled test series.
Collaboration aims to deliver the next generation of thinner, lighter, stronger and more sustainable composite materials used in consumer electronics and automotive industries.
The first project is underway to recover carbon fiber used in an A330-200 aircraft, which will then be regenerated for other end uses by HRC.
Within MCAM itself, another technology that’s nearing commercialization is a new family of textile (nonwoven, woven and unidirectional)-reinforced dry prepregs with thermoplastic matrices called KyronTEX. These products are currently being strategically sampled.
Continuous fiber-reinforced thermoplastic composite targets full circularity in aircraft interior applications, with FST, impact resistance and toughness features.
Six U.S. companies have proven their recycling technologies for composites and rare earth elements, and will be supported for relevant scale demonstration and validation.
A report on the demand for hydrogen as an energy source and the role composites might play in the transport and storage of hydrogen.
A combination of Airtech’s 3D printing materials and Ascent’s production capabilities aim to support increased use of composite additive tooling in spaces like defense and aerospace.
Wheel brand Parcours reveals composite bike wheels using Hypetex colored carbon fiber to achieve aesthetic, lightweight and performance goals.
Among the new injection moldable CFRTP compounds specifically developed for automotive use is KyronMAX ES 4240, a 40 FWF short carbon fiber-reinforced PPA said to be the first to break the 414-MPa (60,000 psi) tensile strength barrier.
Formnext Chicago is an industrial additive manufacturing expo taking place April 8-10, 2025 at McCormick Place in Chicago, Illinois. Formnext Chicago is the second in a series of Formnext events in the U.S. being produced by Mesago Messe Frankfurt, AMT – The Association For Manufacturing Technology, and Gardner Business Media (our publisher).
Base Materials introduces a high-performance, toughened epoxy tooling board designed for thermoforming and vacuum forming processes, direct-to-part applications and more.
This session is designed to demonstrate the benefits of ultra polymers for aerospace applications with real case examples of Syensqo's polymer portfolio. Agenda: Introduction to ultra polymers (PAEK, PEKK, PEEK, PAI) key features Application of ultra polymers in aerospace: concrete examples Benefits of ultra polymers: enhanced performance, durability and cost-efficiency
To demonstrate the performance capabilities of KyronMAX composites to aerospace customers, MCAM designed and produced a generic quarter-turn retaining latch for use in aircraft galleys. The parts are currently produced in aluminum owing to high load requirements. A 30% FWF short carbon fiber/PEI grade (KyronMAX S 6230) was selected both for its mechanical performance as well as its flame/smoke/toxicity (FST) listing. The composite parts meet the performance requirements of aluminum at half the weight and are currently being evaluated by several customers. They also permit painting to match aircraft interiors.
Other automotive grades introduced at the 2019 SPE AutoEPCON include a high-temperature carbon fiber-reinforced PPA grade specifically developed for underhood applications. That grade is said to have a glass transition temperature (Tg) and continuous-use temperature (CUT) rivaling that of PEEK, but is easier to mold. Given the cost sensitivity of high-volume industries like automotive and small appliances, it comes as no surprise to learn that the team also is working on a polypropylene (PP)-based KyronMAX product.
Finally, last summer MCAM acquired carbonNXT GmbH and sister company CFK Valley State Recycling GmbH and Co. KG (both Wischhafen, Germany), bringing a complete line of carbon fiber recycling technology into the group’s product offering. The MCAM team is said to be testing multiple formulas using recycled carbon fiber ahead of qualifying commercial products.
The ITHEC 2024 will take place from the 9 to 10 October 2024 in Bremen, Germany. At the 7th International Conference, more than 300 participants from around the world will be presenting and discussing newest scientific results, meet leading international specialists, share their expertise and start business co-operations in the field of thermoplastic composite technologies. The international exhibition will feature 40+ exhibitors showcasing all steps of the supply-chain. Be it materials, machines, testing, processes, or solutions. By combining the exhibition and the conference ITHEC is further fostering the inter-connectivity between science and industry.
CompositesWorld's Carbon Fiber conference offers you cutting-edge information and access to industry experts in streamlining manufacturing costs, market outlooks and forecasting, and more. You will make invaluable contacts as you meet and network with the industry's most innovative and influential leaders at Carbon Fiber. __PRESENT
CompositesWorld’s Tech Days: Design, Simulation and Testing Technologies for Next-Gen Composite Structures is designed to provide a multi-perspective view of the state of the art in design, simulation, failure analysis, digital twins, virtual testing and virtual inspection.
How the predictive tool “CZone” is applied to simulate the axial crushing response of composites, providing valuable insights into their use for motorsport applications.
Arris presents mechanical testing results of an Arris-designed natural fiber thermoplastic composite in comparison to similarly produced glass and carbon fiber-based materials.
How the predictive tool “CZone” is applied to simulate the axial crushing response of composites, providing valuable insights into their use for motorsport applications.
Prepreg co-molding compound by IDI Composites International and A&P Technology enables new geometries and levels of strength and resiliency for automotive, mobility.
This sidebar to CW’s August 2024 feature article reviews this technology for more efficient composites manufacturing and why it aligns with Koridion active core molding.
CW’s editors are tracking the latest trends and developments in tooling, from the basics to new developments. This collection, presented by Composites One, features four recent CW stories that detail a range of tooling technologies, processes and materials.
Prepreg co-molding compound by IDI Composites International and A&P Technology enables new geometries and levels of strength and resiliency for automotive, mobility.
Unsurprisingly, because these compounds were initially formulated by a molder for a molder, they were designed to provide properties that made them easy to process and to consistently yield higher quality, better performing parts. “We formulated our KyronMAX product line to provide higher flow and fiber interaction, lower internal stresses, less anisotropy, stronger weld lines, fewer sink marks, less tendency for warpage and greater dimensional accuracy — regardless of whether wall sections were thick or thin,” notes Dave Wilkinson, MCAM R&D director. “In addition to our formulation work and unique sizing technology, we also made our own press modifications to run these materials more efficiently.”
Explore the technologies, materials and strategies used by composites manufacturers working in the evolving space market.
Recoat temperature, part orientation and bead geometry are some key design variables to consider for a successful and reliable large-format additive manufacturing (LFAM) process.
Low-melt polyaryletherketone (LMPAEK) unidirectional tapes provide outstanding thermal and fire protection, demonstrating their effectiveness through rigorous testing. These tapes are fire, smoke and toxicity compliant with FAR25.853 and meet OSU Heat Release Rate standards. The tapes were tested under ISO 2685/AC 20-135 Change 1, meeting the fireproof criteria. Additionally, they met UL 2596 requirements for battery thermal runaway tests. These tapes are crucial for high-temperature applications showcasing their resilience and safety in both aerospace and automotive applications. Part of a broader range that includes films and compounds, Victrex LMPAEK materials are valued for their excellent processability and weldability. They offer versatile solutions for complex needs beyond traditional structural parts, such as: thermal runaway and lightning strike protection, heat sinking, and intricate bracketry. Victrex LMPAEK materials facilitate automation and high-rate production while addressing performance and sustainability challenges. With reduced environmental impact, lower weight and cost-efficiency, they meet the evolving demands of the transportation industry and support innovative design solutions. Agenda: Introduction to LMPAEK ecosystem, highlighting unidirectional tapes Thermal and fire protection performance: applications and benefits Material forms and processability Sustainability and efficiency Conclusion and future innovations
“It’s not so much that we set out to create a broad range of CFRTP compounds but that each one was developed to meet the specific needs of a particular customer,” adds Clint Newell, MCAM global composites technology manager. “As our formulation capabilities grew, we entered new markets, met with new customers, asked what they needed and set about creating a perfect compound to meet those needs.”
During the celebration at the Ahmedabad facility, Vagish Dixit stated, “Milacron is a progressive organization with innovation in engineering design and manufacturing. We’re extremely pleased with our partnership with Milacron in India.” Dixit added, “Milacron has fostered our relationship over the last 17 years, when we bought our first injection molding machine. The enthusiasm towards their work and commitment towards customers are the key strengths behind the consistent success of Milacron. The technologies Milacron provides us increase our productivity and the competitiveness of our products.”
During the celebration, Milacron India’s Managing Director, Shirish Divigi, thanked Alpla India for their business and loyalty over the almost two-decade partnership. “As India’s plastics industry continues to grow, Milacron’s Indian operations will continue to excel and offer the industry’s most complete plastics offering.” Divigi added, “The entire Milacron organization is focused on a customer first mentality. We continue to add new value added products and services to better serve our customers in India and across the world. Our customers feel fully supported and connected with our team.”
Milacron Holdings Corp. marked a milestone recently with the shipment of the 12,501st injection molding machine from its Ahmedabad, India manufacturing facility.
Milacron CEO Tom Goeke stated, “India is a vital market for Milacron and it continues to impress. Milacron places great importance in the Indian market and we’re uniquely positioned to serve it in ways our competition simply cannot with our ability to deliver the entire spectrum of services to the plastics industry.”
As formulation expertise grew, the company came to the attention of Mitsubishi Chemical Holdings Group (MCHC, Tokyo, Japan), which acquired Piper in 2016. MCHC immediately made a substantial multi-million dollar investment to increase the size of the compounding line in Arizona, automate operations and bring in its own carbon fiber sizing and chopping technologies to enable KyronMAX compounds to be produced faster and with greater consistency and efficiency. Subsequently, a second compounding line was set up in Michigan and a third in Japan. This expanded capacity meant that KyronMAX grades could compete for automotive business in North America and in Asia. Other markets have followed.
The JEC Forum DACH is a business meetings event organised by JEC The JEC Forum DACH is organised on October 22 and 23, 2024 by JEC, in partnership with the AVK, gathering the composite materials community from the DACH Region (Germany, Austria and Switzerland).
In 2018, Teijin broke ground on a facility that is reportedly the largest capacity carbon fiber line currently in existence. The line has been fully functional for nearly two years and has plenty of room for expansion.
Aerospace manufacturer joins forces with composite materials company to achieve sustainable manufacturing practices that overcome traditional composite layup tooling.
Performing regular maintenance of the layup tool for successful sealing and release is required to reduce the risk of part adherence.
Thermoplastics for Large Structures, experts explored the materials and processing technologies that are enabling the transition to large-part manufacturing.
What’s next? With access to the broader Mitsubishi organization globally, the MCAM team can access technology representing a broader composites portfolio that spans thermoplastic as well as thermoset chemistries, with a range of reinforcement types and lengths. For example, another Mitsubishi group produces split and chopped tow carbon fiber-reinforced forged molding compound (FMC), an advanced form of sheet molding compound (SMC) that helps bridge the performance and processing gap between short glass or carbon fiber-reinforced SMC and continuous carbon fiber-reinforced prepreg. Still another group produces woven and nonwoven carbon fiber reinforced prepreg and rapid-cure prepreg compression molding (PCM) materials.
An on-demand mapping tool for anisotropic materials and polymer material fracture prediction model, i-Lupe, aims to help predict impact, crash behaviors.
Prepreg co-molding compound by IDI Composites International and A&P Technology enables new geometries and levels of strength and resiliency for automotive, mobility.
This idler wheel that is part of a performance compound archery bow was originally produced in machined aluminum. The customer wanted to convert to composites, so initially tried 50% FWF long glass PA6/6. However, that material had challenges filling the complex geometry, which led to premature failure of the part. MCAM formulated a 20% FWF short carbon fiber-reinforced PA6/6 composite (KyronMAX S 2220) for the application. Not only was the new composite able to be molded in the same tool as the LFT grade without modification, but failures were eliminated and weight was reduced 21% versus the LFT material and 50% versus the original aluminum.
Further, at Plastivision 2017 in January Milacron Extrusion launched the TC Conical Twin Screw extrusion system in the Indian market. The TC’s customized screw designs are matched specifically to the customer process requirements for optimal performance. The TC uses advanced materials of construction, including tungsten coated screws and tungsten clad barrels for maximum wear protection and the lowest possible life cycle costs. Milacron’s breadth of extrusion offerings is all encompassing, from extruders, to new and rebuilt extrusion barrels and screws, to pipe heads, dies and downstream equipment, providing powerful, reliable solutions that meet customers’ unique needs. Milacron’s extrusion solutions are highly customizable and increase productivity, output and accuracy, while reducing costs.
The composites industry is increasingly recognizing the imperative of sustainability in its operations. As demand for lightweight and durable materials rises across various sectors, such as automotive, aerospace, and construction, there is a growing awareness of the environmental impact associated with traditional composite manufacturing processes.
Jetcam’s latest white paper explores the critical aspects of nesting in composites manufacturing, and strategies to balance material efficiency and kitting speed.
Ohio-based Canvus Inc. upcycles fiberglass wind blades, car tires and post-consumer plastics to create outdoor furniture that amplifies sustainability messages in community spaces.
GETTING A QUOTE WITH LK-MOULD IS FREE AND SIMPLE.
FIND MORE OF OUR SERVICES:
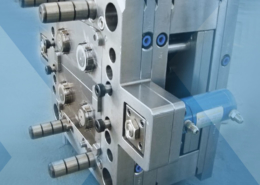
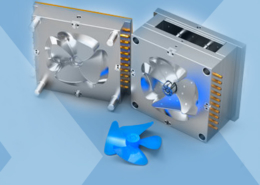
Plastic Molding

Rapid Prototyping
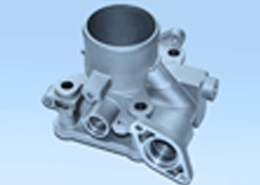
Pressure Die Casting
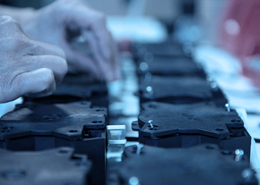
Parts Assembly
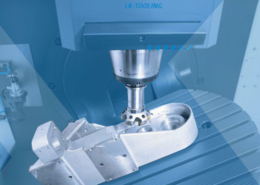