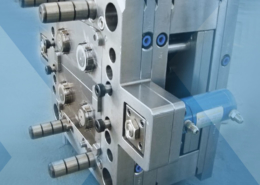
Getting started: Setting up an injection molding plant - two shot moulding
Author:gly Date: 2024-09-30
A subsidiary of Quadrant Engineering Plastic Products, Piper Plastics supplies high-performance polymer materials and precision machined plastic components and assemblies to a range of industries.
Negri Bossi brought a molding machine to the K that is older than the show itself, which is marking its 70th anniversary this year.
The process, which utilizes molding equipment designed and developed by Piper Plastics, allows the company to mold filled or unfilled high-performance thermoplastics with isotropic mechanical properties. “This capability is especially beneficial for large CNC machined parts that were historically limited to extruded or compression molded stock shapes,” explained Dave Wilkinson, Materials Engineering Manager, in a prepared statement. “In comparison to extrusion and compression molding, this new process yields parts that have higher strength—typically 15 to 20% stronger than extruded shapes and 50% stronger than compression molded shapes—with more consistent mechanical properties.”
Stephen has been with PlasticsToday and its preceding publications Modern Plastics and Injection Molding since 1992, throughout this time based in the Asia Pacific region, including stints in Japan, Australia, and his current location Singapore. His current beat focuses on automotive. Stephen is an avid folding bicycle rider, often taking his bike on overseas business trips, and is a proud dachshund owner.
Piper Plastics (Chandler, AZ) reports that it has developed a proprietary high-pressure molding technology that yields near-net-shape polymers up to 2 inches thick without porosity, voids or sinks.
A major reason for developing the new technology was to save costs when machining finished parts from expensive, high-performance materials such as PEEK, PAI or TPI, said the company. “The molds are inexpensive, since we are only molding a near-net shape that will be machined after molding,” said Bruce White, Vice President, Piper Plastics. “Because it’s close to the final part, a near-net shape requires less machining. Less machining means less waste, which is an important consideration for green and sustainable programs.”
The process is suitable for large parts and weights up to 6 pounds per blank, with large and varying wall thicknesses and complex geometries. “Near-net shape is effective for parts that cannot be produced using standard injection molding because the cross sectional area is too thick,” said Wilkinson. “This new technology has opened up exciting opportunities in the semiconductor, oil and gas, medical equipment and aerospace markets.”
The technology also allows Piper to offer small batch runs for mating the right polymer or blend for an application. “Distributors typically only carry about 50 types of engineering plastics, but with this technology we can mold custom blanks from more than 3,000 polymers and compounds, or develop a compound specifically for an application,” said White.
Negri Bossi, for its part, has shipped in a hand-operated unit that was built in 1946 (background in the photo), one year before the company was officially incorporated. The NB28 15-tonne press was the first machine manufactured in Italy and it was sold to a factory near Bergamo for 450,000 lira (€232 in today’s money) to mold buttons from polystyrene.
More recent highlights at the joint Nisse/Negri Bossi booth include an injection molding machine outfitted with an injection blow molding tool from Spanish mold builder Molmasa that employs factory compressed air. The production cell is being demonstrated molding 500-ml biodegradable PLA jars with in-mold PLA labeling.
Nissei and Negri Bossi have brough some of their oldest injection molding machines to the show. The YD-2 in the foreground of the photo dates back to 1960; it was Nissei’s first production model after it was incorporated as an injection machine maker in 1957. With a clamping force of 30 tonnes, the YD-2 on show was used for more than 40 years by a processor molding various resins, including polyacetal, polystyrene, and PVC, before being donated to the Nissei museum.
Both celebrate their 75th anniversary this year, both companies have red in their logo, and both are now under the same roof at K 2022 in Düsseldorf, Germany. Japan’s Nissei Plastic Industrial and Italy’s Negri Bossi are exhibiting jointly for the first time in hall 15, booth B22, after Nissei acquired Negri Bossi in 2020. Also present at the booth is robot maker Sytrama, part of the Negri Bossi group.
GETTING A QUOTE WITH LK-MOULD IS FREE AND SIMPLE.
FIND MORE OF OUR SERVICES:
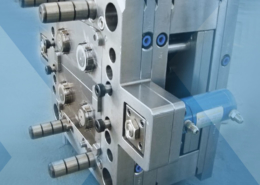
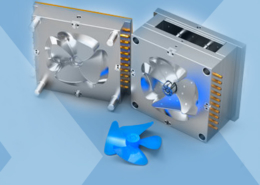
Plastic Molding

Rapid Prototyping
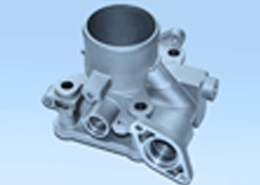
Pressure Die Casting
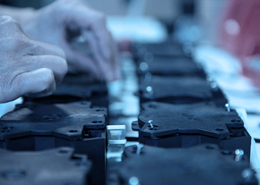
Parts Assembly
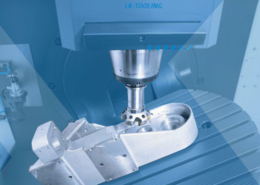